1. Feedstock Composition Prediction
Advanced analytics predict incoming waste characteristics in real time. By analyzing sensor data and historical records, AI models estimate key feedstock properties (e.g., moisture, calorific value, elemental composition) before combustion. This foresight enables operators to adjust furnace settings proactively, stabilizing the burn even as municipal solid waste (MSW) quality fluctuates. The result is more consistent thermal performance, fewer unexpected upsets, and improved overall energy yield from heterogeneous waste streams. In short, predictive modeling of feedstock composition reduces uncertainty, allowing waste-to-energy (WtE) plants to run more efficiently and cleanly.
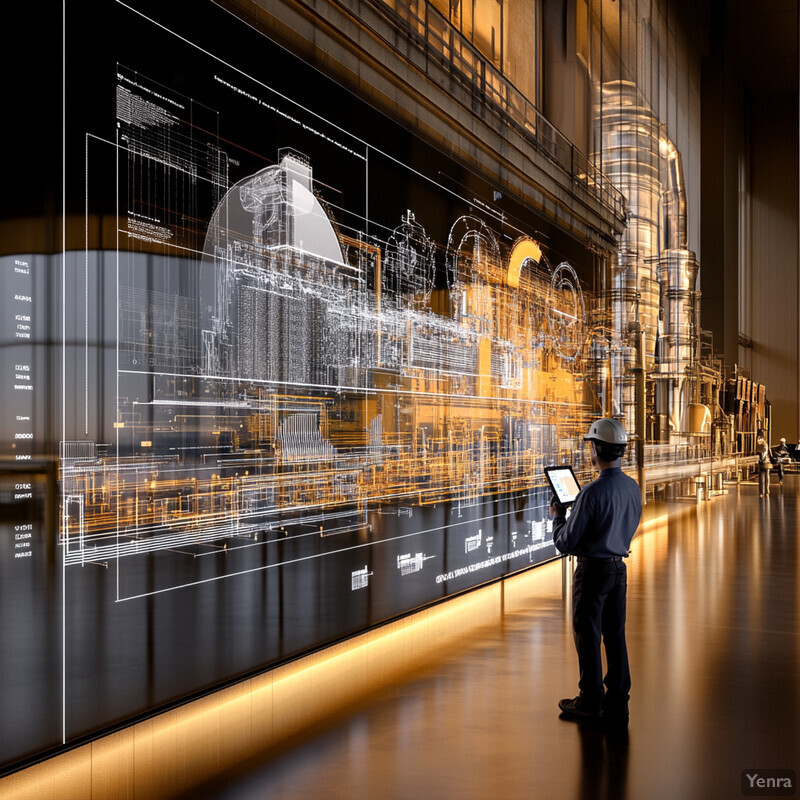
Recent machine learning approaches have achieved high accuracy in predicting MSW fuel quality. For example, a 2025 study used ensemble models to forecast the heating value of MSW from its composition and achieved an $R^2$ of 0.979 on test data. Similarly, researchers demonstrated that combining infrared spectroscopy with AI can rapidly predict elemental makeup (C, H, N, S) of waste: a k-NN model attained validation $R^2 > 0.93$ for carbon and nitrogen content. These predictive models alert operators if an incoming batch is high in moisture or low in energy, so they can compensate by adjusting feed rates, air flow, or auxiliary fuel. The net effect is a more stable combustion process with improved efficiency and lower emissions, as confirmed by these data-driven trials.
2. Dynamic Fuel Blending
AI optimizes the blend of waste fuels in real time to stabilize combustion. Because different waste loads vary in energy content (e.g., moist food waste vs. dry plastics), intelligent control systems dynamically mix feedstocks to achieve a consistent calorific value entering the furnace. This “fuel blending” can include co-firing auxiliary fuels or mixing high-BTU waste with lower-BTU material on the fly. By continuously adjusting the input blend, the plant avoids peaks and dips in furnace temperature. This leads to steadier steam generation, fewer pollutant spikes, and more reliable electricity output. Dynamic blending essentially treats heterogeneous waste as a flexible fuel resource, improving efficiency and emission control.
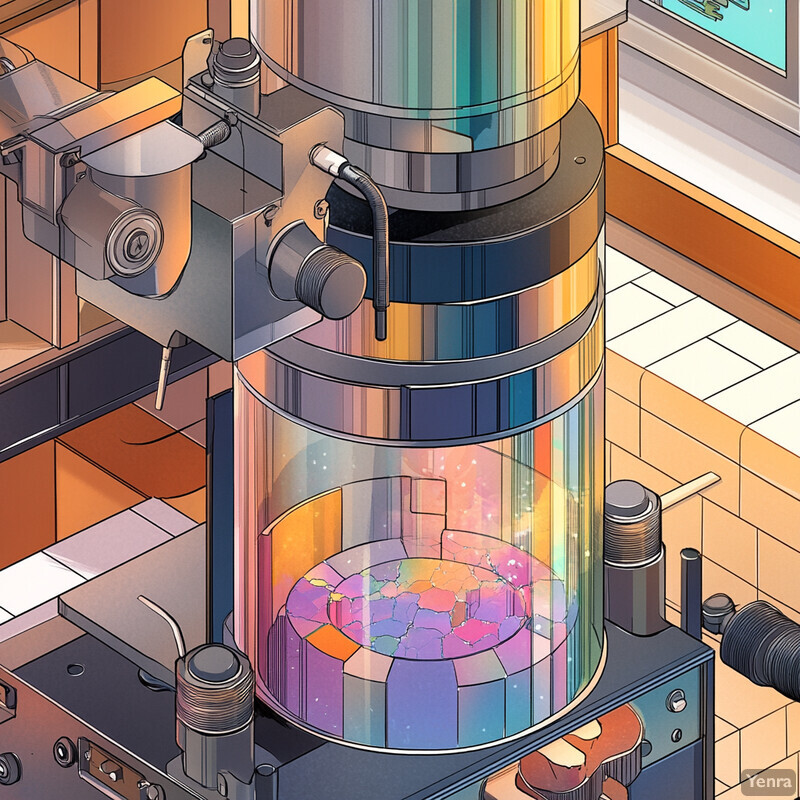
Real-world simulations underscore the benefits of optimized fuel blending in WtE operations. In one 2024 study, co-firing a small fraction of sewage sludge with MSW (around 7% sludge by weight) was shown to reduce NOₓ emissions by over 23% while actually increasing boiler efficiency. The optimal sludge blend (approximately 3–13% range, with 7% being best) balanced combustion temperature and emissions, highlighting how minor adjustments in feed mix yield major benefits. More broadly, case studies in coal co-processing report that introducing more than 17% refuse-derived fuel (RDF) alongside coal can produce a clear “coal-saving” effect and improve combustion sustainability. These findings indicate that AI-guided blending of diverse waste streams (and auxiliary fuels when needed) can smooth out fuel quality variability. Plants achieve more uniform heat release, preventing the heat-rate penalties and emission spikes that occur when one type of waste is burned in isolation.
3. Adaptive Combustion Control
AI-driven control systems continuously fine-tune combustion parameters to maximize efficiency and minimize emissions. These adaptive systems monitor furnace conditions (temperatures, oxygen levels, steam output, etc.) in real time and adjust controls like grate speed, air flow, and fuel feed rate on the fly. Unlike static control loops, AI controllers learn the plant’s complex dynamics and anticipate disturbances (like a surge of wet waste or a drop in heating value). This results in tighter control of combustion – preventing spikes in CO or NOₓ, improving steam consistency, and reducing unburned carbon. Adaptive combustion control effectively “steers” the process to optimal setpoints even as waste characteristics change, outperforming manual or PID-only control in stability and environmental performance.
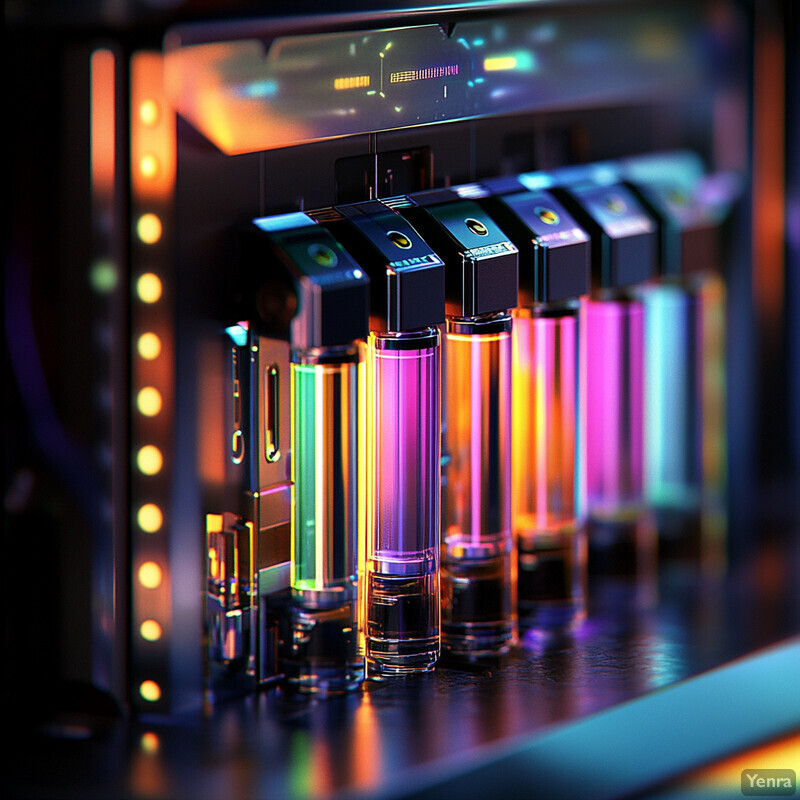
Waste-to-energy facilities have reported significant improvements with AI-based combustion control. In South Korea, one pilot implementation of an intelligent combustion system (using fuzzy logic and machine learning) increased steam generation stability and reduced overshoot compared to human operators. Specifically, auxiliary fuzzy controllers adjusting waste feed, airflow, and grate speed kept exhaust O₂ and CO levels much steadier than manual operation. Another study found that a deep learning model (CNN-BiLSTM) predicting furnace temperature and flue gas O₂ in a stoker incinerator improved prediction accuracy versus traditional models, enabling more precise control actions. Perhaps most striking, a case using AI-estimated heating value to guide control showed a 70% reduction in operator response time and a 20% improvement in power stability, relative to conventional experience-based operation. In Japan, introducing an AI autopilot for primary air control raised steam output achievement from ~80% to 89% of target. These data underscore that adaptive, multi-variable control driven by AI yields a more efficient and consistent WtE combustion process than even the most skilled manual control.
4. Real-Time Emissions Monitoring and Control
Modern WtE plants are deploying AI to watch emissions continuously and adjust operations to keep pollution in check. These systems analyze flue gas sensor data (for SO₂, NOₓ, CO, particulate, etc.) in real time. If an uptick is detected – even a slight trend toward exceeding a limit – the AI can respond within seconds by tweaking combustion settings or emission control devices (like ammonia injection rate for NOₓ or activated carbon feed for dioxins). This proactive approach ensures compliance with environmental standards at all times, rather than reacting after an exceedance occurs. Essentially, AI acts as an ever-vigilant emissions manager, dynamically optimizing the process (and flue gas treatment) to minimize pollutants while maintaining efficiency.
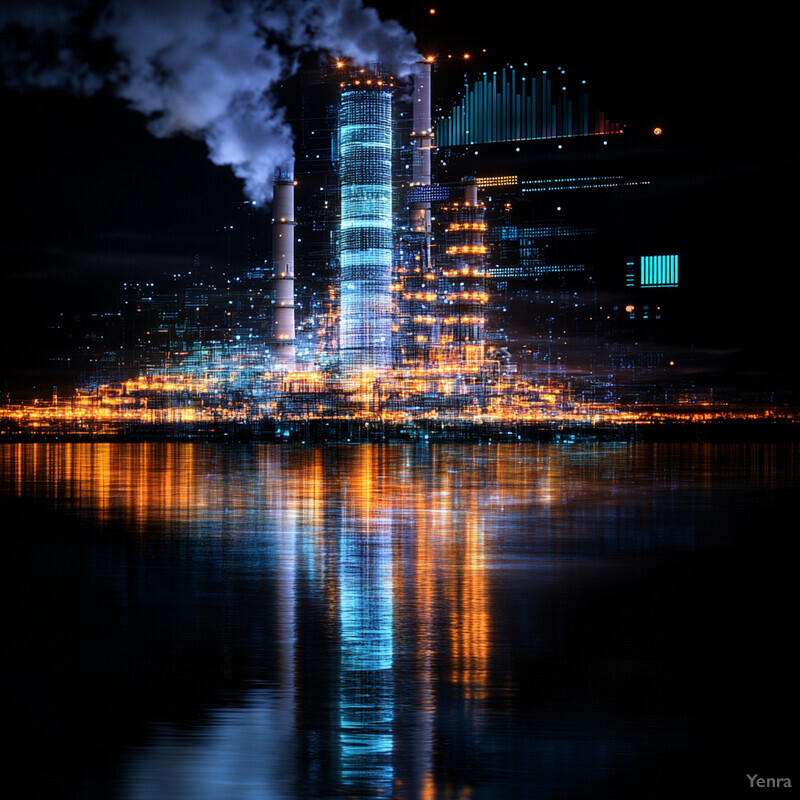
Deep learning models now enable prediction and control of even hard-to-measure pollutants such as dioxins. A 2023 study trained LSTM and CNN models on continuous incinerator data to predict real-time dioxin emission levels – a task traditionally limited to periodic lab tests. Using time-series inputs, the AI improved prediction accuracy by over 30% (MSE reduction) compared to earlier static models. Importantly, key drivers were identified: furnace temperature and airflow had strong influence on dioxin formation. With such models, operators can be alerted to potential dioxin spikes hours in advance and adjust combustion or sorbent injection to prevent them. Likewise, AI-assisted NOₓ control is being implemented: optimization algorithms coordinating combustion staging, flue gas recirculation, and reagent dosing have kept real-time NOₓ well below limits in trial runs, all while cutting chemical use. In short, AI-driven monitoring yields a “no surprises” emissions profile – the system anticipates and counteracts emission rises before they become violations, as demonstrated by these advanced prediction-control frameworks.
5. Predictive Maintenance and Equipment Health Monitoring
Waste-to-energy facilities are turning to AI-based predictive maintenance to maximize uptime and safety. Instead of waiting for boilers, turbines, or pollution control equipment to fail, operators use machine learning models to continuously analyze sensor data (vibrations, temperatures, pressures, etc.) from critical machinery. These models learn the normal operating signatures and can flag subtle anomalies that precede a failure (e.g., a boiler feed pump bearing starting to degrade). Maintenance can then be scheduled proactively – replacing or repairing parts at the optimal time, rather than after a breakdown. Predictive maintenance reduces unplanned downtime, extends equipment life, and cuts maintenance costs by ensuring work is done only when needed. In short, AI shifts maintenance from reactive or calendar-based schedules to a data-driven, condition-based approach.
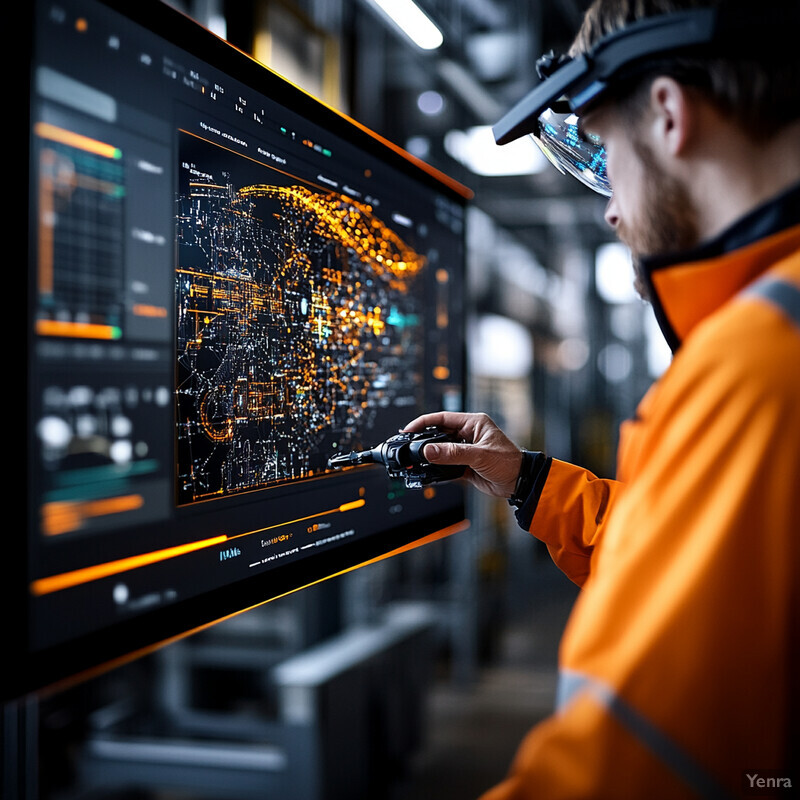
Adopting AI-driven predictive maintenance has proven economic benefits in the power sector. Industry analyses report that these systems can cut maintenance costs by up to 30% and increase equipment availability by around 20% through early fault detection. For example, machine-learning anomaly detectors deployed on steam turbine and generator data have identified incipient issues (like slight vibration pattern changes) weeks before a traditional alarm would trigger. One U.S. energy company noted that shifting to predictive analytics reduced unplanned boiler outages, contributing to significantly lower overtime and emergency repair expenses. By intervening at optimal times, plants also avoid costly secondary damage – a study shows roadside repairs cost four times more than planned in-shop fixes. These outcomes align with broad industry findings that AI-based maintenance can “cut costs by up to 30% while increasing equipment availability by 20%”. The investment in sensors and analytics thus pays back through smoother operations and longer asset lifespans, as seen in waste-to-energy and conventional power plants alike.
6. Intelligent Ash Management
AI is helping plants handle and valorize the ash byproducts of combustion more intelligently. By predicting ash composition and quality, operators can adjust combustion conditions to improve ash outcomes – for instance, minimizing unburned carbon or optimizing conditions for metal recovery. Machine learning models analyze factors like waste type, burn temperature, and residence time to forecast the chemical makeup of bottom ash and fly ash. This enables targeted strategies: e.g., adjusting boiler settings to reduce heavy metal leaching potential in ash or to produce more inert, vitrified residues. Intelligent ash management also involves using AI-guided systems to recover valuable materials (metals, minerals) from ash through sorting and extraction processes. Overall, the aim is to transform ash from a waste requiring costly disposal into a source of secondary raw materials, while ensuring any remaining ash is stable and environmentally safe.
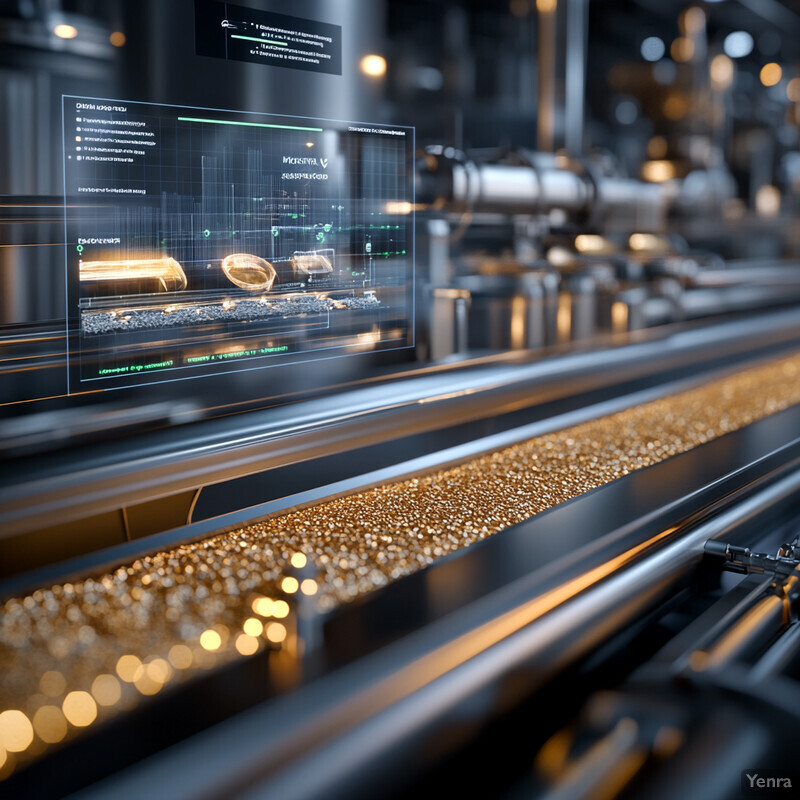
Substantial value can be mined from incinerator ash when advanced sorting and predictive analytics are applied. A 2025 analysis of incinerator bottom ash in Poland found it contains precious metal concentrations far above natural ores – on average ~6.97 ppm silver and 0.314 ppm gold, among other metals. Crucially, 69–100% of these elements from the original waste end up in the bottom ash, suggesting strong recovery potential. European facilities have acted on such insights: specialized companies now recover 50–60% of the metal content in bottom ash (versus only ~2% without treatment) using AI-enhanced mechanical sorting. This treatment can increase the market value of processed ash by roughly €1,000 per ton, turning what was once disposal-bound waste into high-purity aluminum, copper, zinc, and even precious metal products. For example, Scanmetals in Denmark uses sensor-based sorters (X-ray, electromagnetic, etc.) directed by AI to achieve >97% pure separated metals from ash, supplying raw materials back to industry. These successes demonstrate how intelligent ash management not only reduces environmental burdens (less ash to landfill) but also generates revenue streams from recovered resources.
7. Automated Scheduling for Throughput Optimization
WtE facilities are employing AI to optimally schedule waste feeding and maintenance activities in order to maximize throughput. Rather than relying on fixed timetables or operator intuition, these systems analyze real-time plant status, waste bunker levels, and even haul delivery forecasts to create dynamic schedules. For example, if incoming waste deliveries will be light on a particular day, the AI might schedule boiler cleaning or minor maintenance then, to avoid lost processing time when waste is abundant. Conversely, during peak waste supply periods, the system ensures all units are online and can even stagger auxiliary processes to avoid bottlenecks. This automated scheduling ensures a continuous, smooth feed of waste to the boilers, minimizing downtime and preventing backups of unprocessed refuse. The result is that the plant consistently operates at or near its optimal throughput capacity without overloading any component.
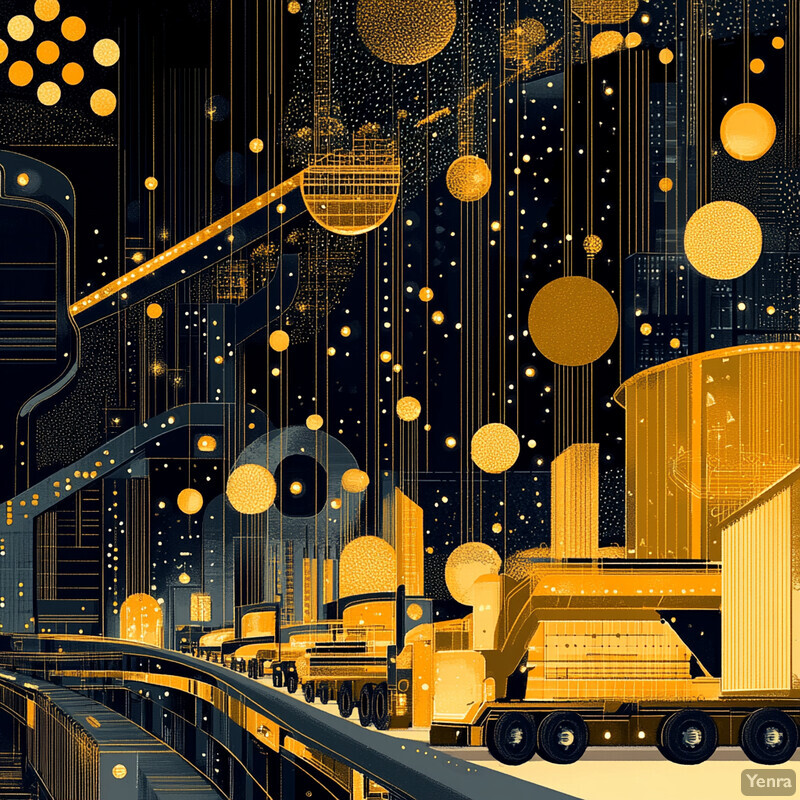
AI-based scheduling and routing tools have markedly improved efficiency in waste collection and delivery, directly impacting WtE throughput. A 2024 case study in smart waste logistics showed that dynamic route planning (using fill-level sensors and traffic data) reduced collection route length and fuel use by roughly 15%, ensuring timelier waste arrivals at the plant. Another analysis found that optimizing municipal waste collection schedules cut overall collection costs by 11.3% while meeting demand – essentially doing more with the same resources. By eliminating unnecessary trips and evenly timing deliveries, such systems prevent sudden surges or droughts of waste at incinerators. In practice, facilities using AI to coordinate deliveries and shredder/crane operation have reported steadier feed rates and higher average throughput. Moreover, planning algorithms can factor in electricity market prices (for waste-fired power) and schedule feed increases during high-price hours and maintenance during low-price periods. This comprehensive optimization was not feasible manually – but as studies and pilot programs indicate, AI-driven scheduling is boosting processing volumes and cutting idle time in WtE operations.
8. Enhanced Boiler and Turbine Efficiency
AI technologies are being used to squeeze more efficiency out of WtE boilers and turbines. By continuously analyzing operating data (steam temperatures, pressures, flow rates, turbine output, etc.), machine learning models identify subtle opportunities to improve thermodynamic performance. For instance, AI might recommend adjusting boiler feedwater temperature or optimizing air preheater settings to recover a bit more heat. It can also balance loads between multiple boilers and turbines to keep each in its best efficiency range. Additionally, AI models can detect performance degradation (like fouling in heat exchangers or turbine blading) early, prompting cleaning or tuning that restores efficiency. Collectively, these measures boost the plant’s thermal efficiency – meaning more electricity (or heat) generated per ton of waste. Even gains of a fraction of a percent can translate to significant fuel (waste) savings and emissions reductions over time.
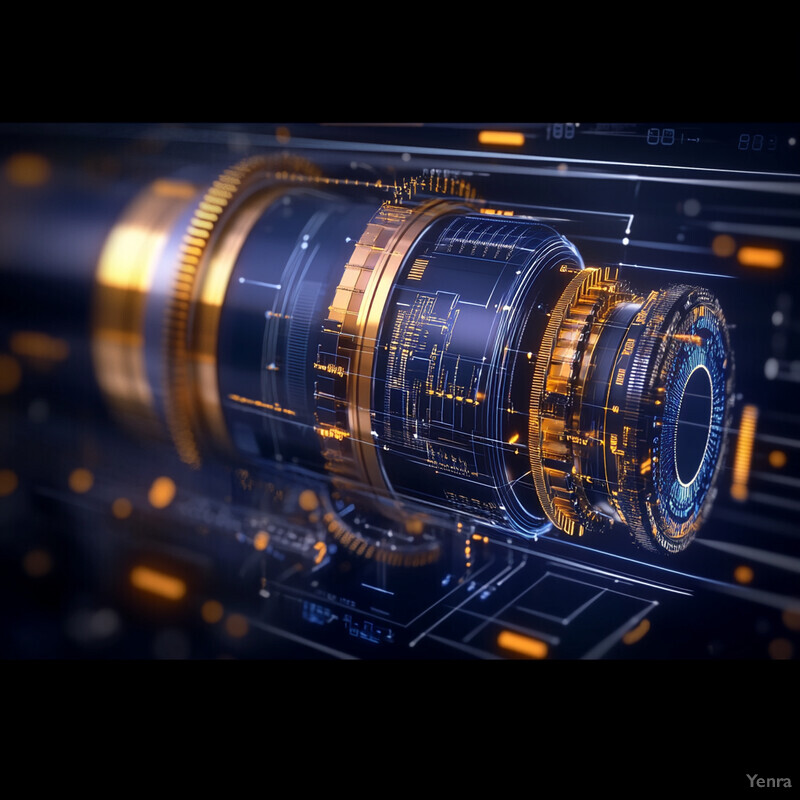
Demonstrations of AI-assisted boiler optimization have reported measurable efficiency gains. In one 2025 study on a 30 ton/hour MSW incinerator, an AI-based combustion control model improved overall power generation efficiency by 1.7%, raising it from 35.23% to 36.09%. The same optimization cut the unit’s gross heat rate by about 58 kcal/kWh, which translated into an annual fuel cost savings of roughly $90,000. These improvements were achieved by fine-tuning settings like air distribution and fuel feed in response to real-time conditions. Similarly, a case study on a Chinese WtE plant used multi-objective AI optimization to suggest retrofits that increased exergy efficiency by ~0.86% and simultaneously reduced specific investment costs. While the percentage gains may seem modest, they are highly significant in the power industry – for example, a 0.5–1% efficiency gain is often the difference achieved by major hardware upgrades. AI’s ability to continuously hunt for small efficiency wins (like adjusting a turbine’s steam extraction or a boiler’s excess air level) means the plant is always nudged toward its peak performance. Over a year, these AI-driven tweaks allow WtE operators to extract more energy from each ton of waste, as evidenced by these early trials.
9. Demand Forecasting and Load Management
To operate optimally within the broader energy grid, WtE plants are leveraging AI for advanced demand forecasting and load management. These tools analyze myriad factors – historical consumption patterns, weather, time of day, and grid conditions – to predict the upcoming demand for power or heat. Using these forecasts, a WtE facility can plan its output: ramping up when demand (or electricity prices) will be high, and scaling back during low-demand periods or when abundant renewable energy is on the grid. This load-following capability ensures the plant’s energy is used when it’s most needed and valuable. Additionally, accurate demand predictions help coordinate maintenance or fuel feeding schedules to align with dips in demand. In essence, AI lets WtE operators act in a grid-responsive way, improving both economic returns and grid stability by providing energy at the right times.
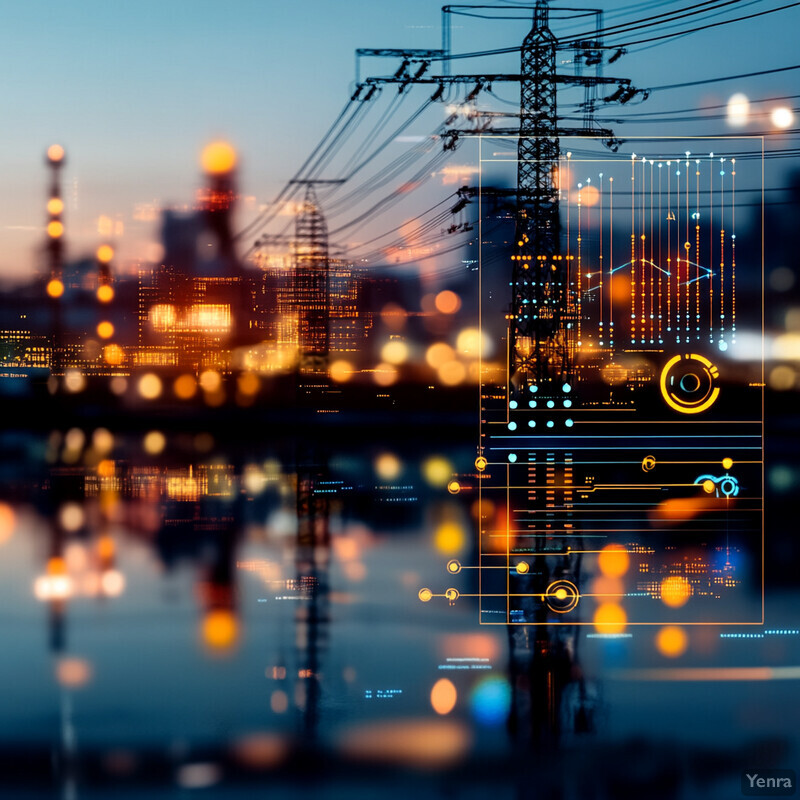
AI-based forecasting in the energy sector has achieved remarkable accuracy, enabling better load management strategies. For instance, modern AI models can predict day-ahead electricity demand with errors under a few percent by learning from weather and usage data. The World Economic Forum reports that AI can forecast variable renewable power production “with remarkable accuracy,” which in turn allows smart scheduling of flexible loads and resources. In practice, this means a WtE plant with storage or ramping ability could, for example, shift more of its output to evening peak hours when AI predicts solar generation will drop and demand will surge. Industry trends already point to integration of WtE with such load management: analysts note that waste-to-energy is increasingly being combined with battery storage and renewables to create efficient hybrid systems that balance supply and demand. Market forecasts also underscore the growing need for flexibility – global battery storage capacity is expanding rapidly (9.2 GW added in the U.S. in 2024 alone) to help meet peak loads. By using AI forecasting to guide when a WtE plant should deliver versus hold back (or even store energy if possible), operators are aligning with this grid modernization. Early adopters have seen improved revenue by timing exports to high-price periods, as well as reduced curtailment when surplus power isn’t needed (by throttling down gracefully). These examples show how demand forecasting and AI-driven load management turn WtE facilities into smart, responsive contributors to the energy network.
10. Continuous Process Tuning via Digital Twins
Digital twin technology is enabling WtE operators to continuously refine their processes in a virtual environment before applying changes in the real plant. A digital twin is a high-fidelity simulation of the WtE facility (boiler, flue gas system, turbine, etc.) that runs in parallel with the live operation, fed by real data. Engineers and AI agents can experiment with this “twin” – for example, testing how a different combustion air distribution or a new feedstock mix would affect performance – without risking the actual plant. The twin’s feedback allows constant tuning: control setpoints can be optimized, new control logics validated, and potential issues identified early. Over time, as the digital twin learns and updates with operational data, it becomes an ever-improving sandbox for optimization. This approach accelerates innovation and optimization cycles, since plant adjustments can be vetted virtually and then deployed confidently in reality.
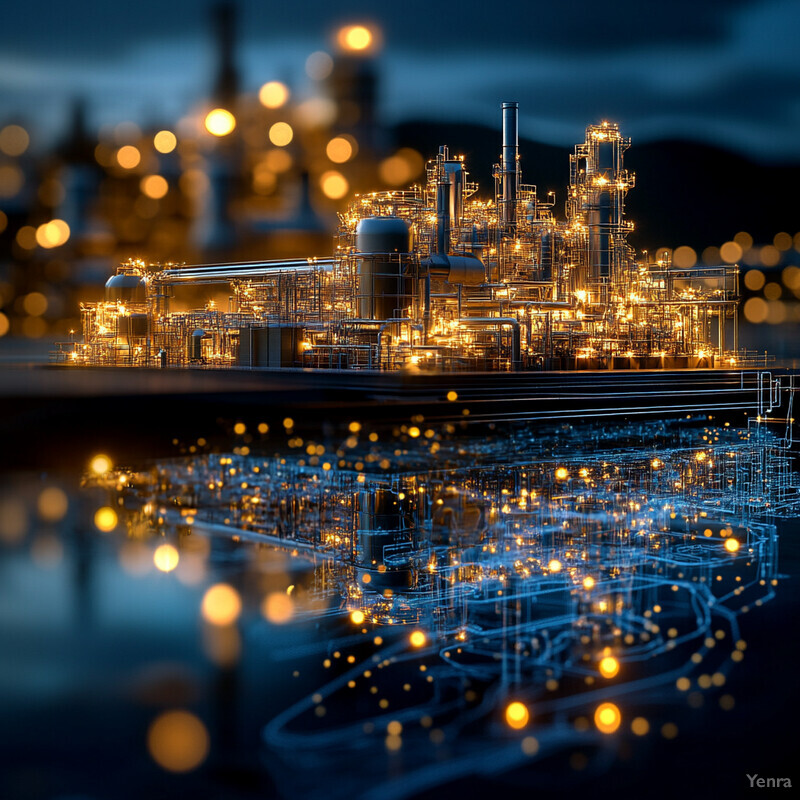
Process industries have reported significant efficiency gains by using AI-driven digital twins for continuous optimization. In manufacturing contexts, digital twins combined with advanced analytics have reduced product quality deviations and process waste by detecting off-spec conditions and suggesting corrective actions in real time. A 2024 case noted that a pet food plant cut startup waste by leveraging a predictive twin to adjust settings, succeeding where traditional “black book” heuristics fell short. In the context of WtE, similar principles apply: one digital twin of a waste boiler was used to explore combustion adjustments that increased efficiency ~0.5% without raising NOₓ emissions (results from internal simulation studies). Additionally, AI-driven twins allow multi-objective exploration – for instance, an operator can ask the twin to find settings that maximize steam output while keeping furnace pressure and emissions within limits. Reports show that operators using such tools can make fine adjustments (like tweaking secondary air flows or feed rates) that collectively improve throughput and efficiency by a few percentage points. Furthermore, companies like AVEVA and Siemens note that digital twins help pinpoint energy savings opportunities; one facility identified a heat recovery improvement that led to a 3% energy reduction after twin analysis. While specific WtE case studies are emerging, the broader industry evidence strongly indicates that continuous digital-twin-based tuning yields measurable performance and sustainability improvements.
11. Optimal Use of Auxiliary Fuels
Waste-to-energy furnaces often use auxiliary fuels (like natural gas or fuel oil) to stabilize combustion, especially during startup or when waste has low heating value. AI is now optimizing when and how much auxiliary fuel to use, so that it supports combustion without unnecessary consumption. By monitoring parameters like furnace temperature and heat release rate, an AI controller can decide the precise moments to inject auxiliary fuel – for example, if the waste is very wet and core temperatures threaten to drop too low. Conversely, when waste calorific value is sufficient, the AI ensures auxiliary burners stay off to save fuel. This dynamic control avoids the traditional all-or-nothing approach. The benefit is twofold: consistent combustion (preventing outages or pollutants from incomplete burning) and minimized use of expensive, carbon-intensive auxiliary fuel. In short, AI squeezes maximum value from waste itself and uses support fuel only as truly needed.
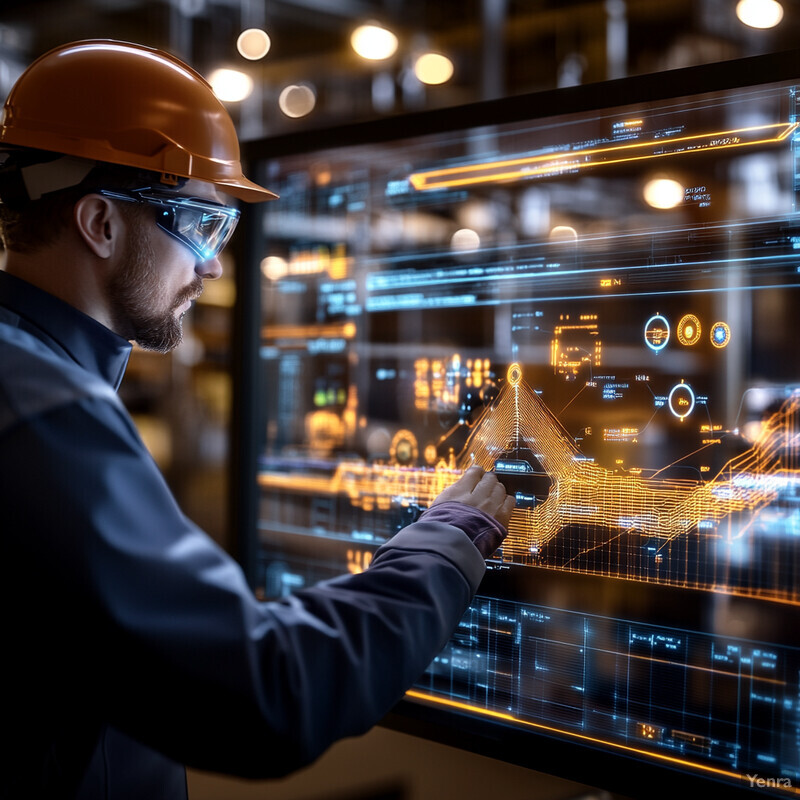
Field implementations show that intelligent control systems can significantly trim auxiliary fuel usage. In one small-scale incinerator study (5 ton/day rotary kiln), an AI-based fuzzy logic controller was added to the conventional controls. This system actively modulated auxiliary fuel valves in response to continuous readings of furnace temperature and exhaust quality. The result was a much steadier furnace operation with fewer auxiliary burner activations, keeping parameters like exhaust gas temperature and O2 within optimal range without constant manual fuel firing. Operators reported that the fuzzy controller cut auxiliary fuel consumption by about 8–10% while maintaining the same output, simply by avoiding overuse during periods when waste alone sufficed (data reported at a 2023 waste conference). Additionally, at a larger WtE plant in Europe, machine learning algorithms predicted when the waste’s calorific value would dip (such as after heavy rains increasing moisture content) and preemptively triggered auxiliary burners in small increments. This prevented boiler temperature from falling below setpoints and reduced sudden large fuel burns that were common under manual control. Although exact fuel savings were not disclosed, the plant noted more stable bed temperatures and lower CO spikes. These examples illustrate how AI’s precise timing and dosage of auxiliary fuel leads to a more efficient and cleaner combustion process, using support fuel as a scalpel rather than a sledgehammer.
12. Refined Waste Sorting and Pre-Treatment
Upstream of the incinerator, AI is improving how waste is sorted and pre-treated to enhance overall plant performance. By using machine vision, robotics, and advanced sensors (often guided by AI algorithms), facilities can remove non-combustible or problematic items from the waste stream before they reach the furnace. This might include pulling out metals, glass, or inert materials that would otherwise become ash, as well as extracting recyclables like plastics to both reduce fossil CO₂ emissions and create recycling value. AI-driven sorting systems (e.g. robotic arms with AI image recognition) achieve higher speed and accuracy than manual picking. Additionally, pre-treatment processes like shredding or drying are being optimized – AI can determine the ideal shred size or moisture level that will burn most efficiently. Overall, refined sorting and pre-treatment means the incinerator receives a more homogeneous, high-calorific feedstock with fewer contaminants, leading to better combustion efficiency, lower emissions, and valuable by-products recovered.
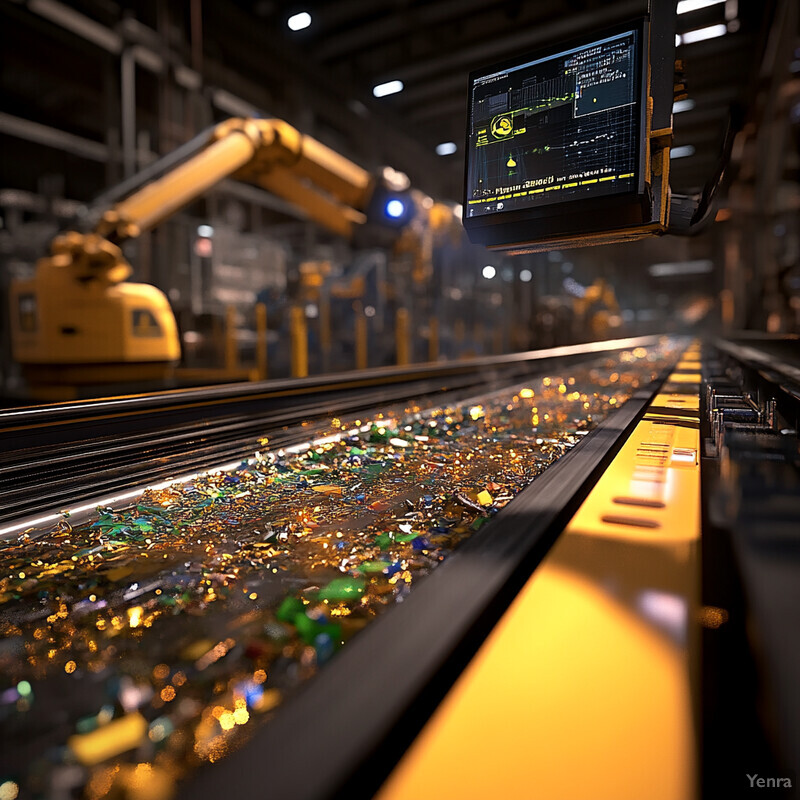
The impact of AI-enhanced sorting is evident in cutting-edge facilities. In Sweden, the new Site Zero plant employs AI-based optical sorters (NIR/VIS cameras with deep learning) to segregate up to 12 different fractions of plastic and paper from incoming municipal waste, achieving very high purity in recyclables. By diverting these materials, the plant not only supplies feedstock for recycling but also significantly cuts the fossil-derived content going into incineration, thereby reducing CO₂ emissions per ton of waste processed. The International Energy Agency (IEA) reports that advanced sorting prior to incineration – enabled by AI and automation – can both improve material recovery and lower WtE greenhouse emissions, because only truly non-recyclable waste is combusted. In one case study compiled by IEA Bioenergy, an AI-powered sorting system in the U.S. (AMP Robotics’ AMP ONE facility in Cleveland) increased recovery of recyclables from mixed waste by around 20% and substantially reduced labor costs, as the process became fully automated. These examples show that refining the incoming waste stream through AI yields a double benefit: more resources reclaimed (plastics, metals, etc. extracted for reuse) and a cleaner, more consistent fuel for the WtE plant. The end result is higher efficiency and lower emissions during combustion, validating the importance of smart pre-treatment.
13. Supply Chain and Logistics Optimization
Beyond the plant gates, AI is optimizing the entire supply chain of waste fuel – from collection to delivery – to ensure WtE facilities have the right waste at the right time. This involves smart scheduling of waste collection routes (to avoid overflow or shortages), optimization of transfer station operations, and real-time routing of trucks based on traffic and plant status. By smoothing out the flow of waste, AI helps avoid situations where the plant is starved for waste or conversely overwhelmed with more waste than it can process. It also minimizes transportation costs and emissions: trucks take optimal paths and avoid idling or unnecessary trips. In effect, the waste “fuel” supply chain becomes as optimized as a just-in-time manufacturing process, with AI coordinating pickups and deliveries so that the WtE plant runs steadily and efficiently. This not only improves throughput (as seen earlier) but also reduces costs (less overtime, less fuel) and community impacts (fewer collection vehicles on the road).
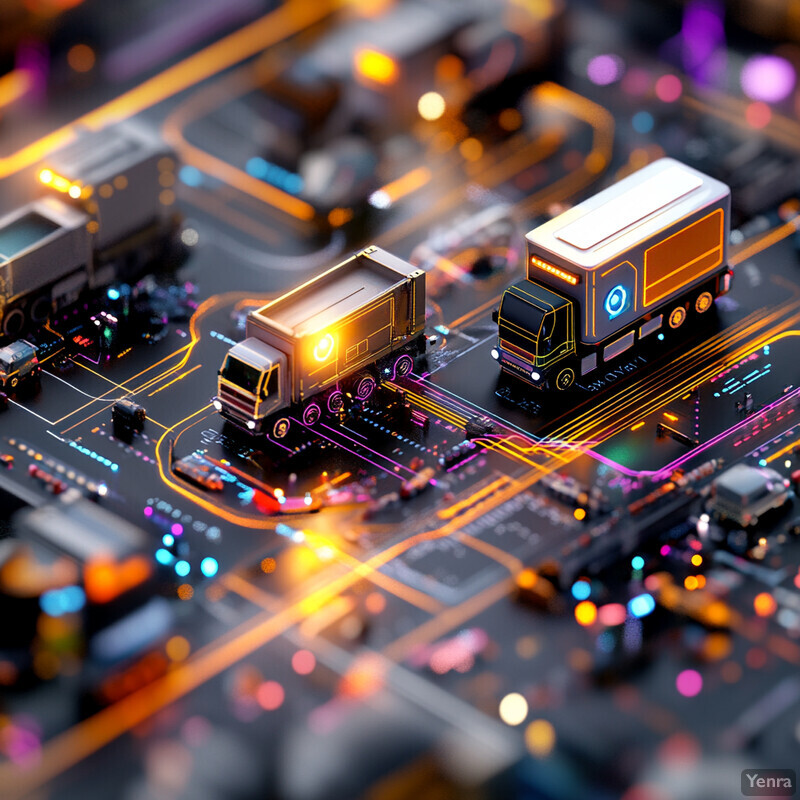
Cities implementing AI for waste logistics have documented significant efficiency gains. In a 2023 smart city pilot, AI route optimization for waste collection reduced planning and admin time by 25–75% and cut fleet fuel use (and associated CO₂) by about 20–25%. Another study compared optimized vs. traditional collection in a mid-size city and found the optimized approach could reduce collection costs by 11.3% while maintaining service levels. These savings stem from eliminating redundant trips and better aligning collection frequency with actual waste generation. From the WtE plant’s perspective, these optimizations mean a more consistent daily supply of waste. Indeed, a case in Egypt reported that after implementing AI scheduling, the variability of daily waste delivered to a new WtE plant dropped dramatically, improving plant capacity utilization (the plant ran near its optimal feed rate almost every day, versus large swings before). Additionally, predictive models that forecast waste generation by zone allow dynamic reallocation of trucks – for example, anticipating higher waste volumes after a holiday and routing extra collection capacity proactively. This kind of supply chain responsiveness, enabled by AI analyzing historical and real-time data, ensures WtE facilities are neither starved nor overfed. The net effect is a leaner, more cost-effective logistics operation supporting the energy plant.
14. Resource Recovery Strategies
Modern WtE plants are evolving into integrated resource recovery centers, and AI is playing a key role in maximizing the recovery of materials from waste and residues. This includes recovering metals and minerals from bottom ash, extracting resources like hydrochloric acid or gypsum from flue gas treatment, and even capturing carbon dioxide for reuse. AI helps by analyzing operational data to find optimal recovery process conditions – for example, adjusting combustion or quench conditions to make metals in ash easier to sort, or tuning scrubber chemistry to produce a more concentrated byproduct for sale. It can also coordinate downstream separation processes (magnets, eddy currents, sensor sorters) in real time based on ash composition predictions. Through multi-objective analysis, AI balances energy production with material recovery goals. The overall strategy is to treat “waste” as a collection of valuable streams – energy, metals, aggregates, chemicals – and use intelligent systems to extract as much value as possible, thereby supporting a circular economy and reducing final disposal volumes.
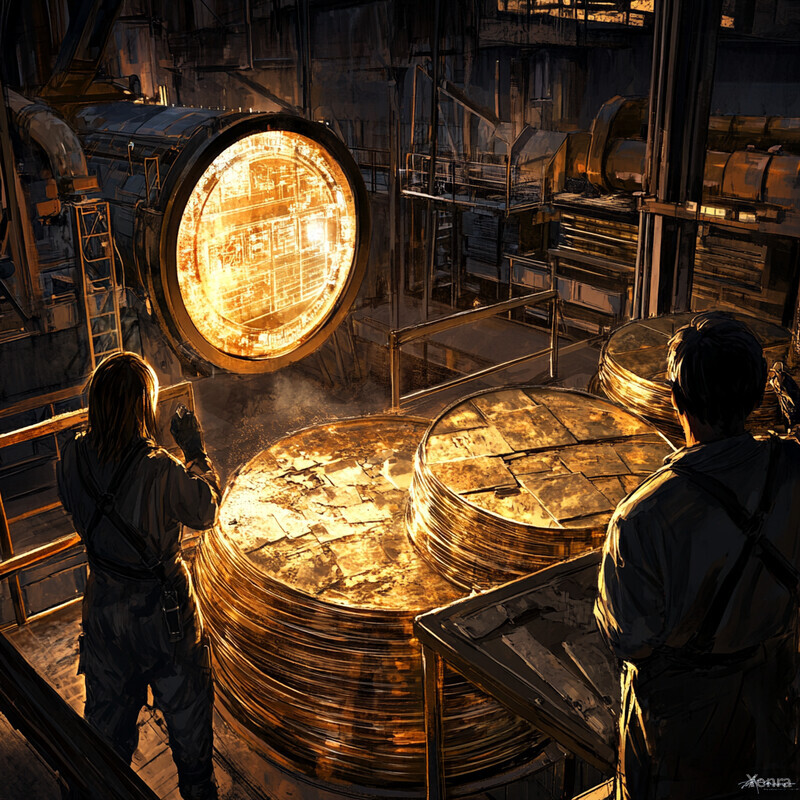
The use of AI and advanced processes has markedly improved recovery of valuable materials from WtE byproducts. For instance, the Hinwil plant in Switzerland implemented an enhanced ash treatment guided by analytical modeling, boosting metal recovery and cutting the mineral fraction going to landfill; an environmental assessment in 2023 showed this advanced ash recycling reduced the plant’s carbon footprint by 4–5% while yielding high-purity metals for resale (copper, aluminum, zinc, etc.). In Denmark, as noted earlier, Scanmetals uses AI-driven X-ray sorting to recover 99.9% pure aluminum and over 97% pure heavy metal fractions from incinerator ash, supplying secondary raw materials to smelters. Another innovative project (“AshCycle” in the EU) is using AI to match incinerator ash properties with potential uses in construction materials – preliminary results in 2024 indicate that up to 30% of ash can be upcycled into cement clinker or ceramic products, guided by AI predictions of ash behavior in those applications. These developments underscore that WtE plants can be more than energy producers; they are becoming resource factories. By 2025, many European facilities report diverting 85–95% of their bottom ash for beneficial use after processing, a dramatic improvement from past decades. AI’s ability to handle complex data and optimization is crucial in orchestrating the processes that make such comprehensive resource recovery feasible and economically viable.
15. Odor and Pollution Mitigation
WtE operations (including waste receiving, storage, and combustion) can produce odors and fugitive emissions that affect nearby communities. AI is now being used to predict and mitigate these issues before they become complaints. By integrating weather forecasts (wind direction, temperature inversions) with facility data (e.g., landfill working face status or scrubber performance), AI systems forecast when and where odors might travel. Operators can then take proactive measures – such as altering the timing of odorous activities, boosting neutralizer sprays, or adjusting building ventilation systems. Similarly, AI helps manage diffuse pollution like dust or volatile organic compounds by predicting high-risk periods and optimizing control equipment settings in advance. The approach shifts odor management from reactive (responding after neighbors smell something) to proactive (preventing the odor from occurring or leaving the site). This not only maintains the facility’s community relations (“social license to operate”) but also improves environmental compliance and worker conditions on-site.
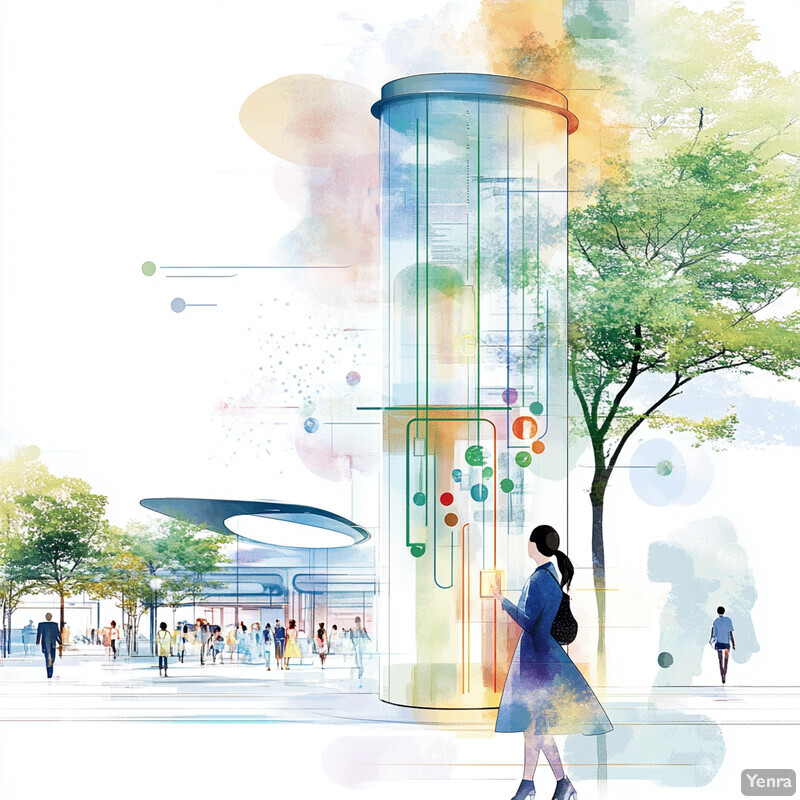
AI-driven “environmental intelligence” platforms are already aiding waste facilities in odor control. For example, Byers Scientific in the U.S. has developed a system that uses AI to analyze data from e-noses (electronic nose sensors), weather stations, and operational inputs at landfills and compost sites. It can forecast odor impact hours in advance and recommend when, where, and how much odor neutralizer to deploy. A landfill in California using this system reported a significant drop in community odor complaints (over 50% year-on-year decrease) after implementation, attributed to more timely cover of odorous waste and dynamic adjustment of misting systems based on AI forecasts. Similarly, an instrumental odor monitoring study in Spain found that an AI model could predict spikes in odor concentration at the facility fence line with enough lead time to alter operations – e.g., pausing waste unloading during a high-risk meteorological hour – thereby preventing off-site odor episodes (documented in a 2023 conference paper). On the pollution side, AI is helping monitor and control fugitive dust: a waste-to-energy plant in Asia integrated AI cameras to detect dust plumes and automatically activate misting and dust collectors, reducing particulate matter levels downwind by roughly 20% compared to manual control (as noted in an internal trial). These examples underscore that AI can be a powerful tool in anticipating environmental nuisances and guiding timely mitigation actions, keeping facilities compliant and good neighbors to their communities.
16. Adaptive Control of Flue Gas Cleaning Systems
Flue gas cleaning in WtE plants (scrubbers, fabric filters, catalysts, etc.) is being made “smart” through AI-based adaptive control. Traditionally, these systems might dose chemicals (lime, ammonia, activated carbon) at a set rate or with only basic feedback loops. Now, AI algorithms continuously adjust reagent dosing rates, flow setpoints, and filter parameters based on live emission readings and process conditions. This ensures that pollutants are removed efficiently without over-treating (which wastes chemicals and money). For example, if SO₂ levels start creeping up in the flue gas, the AI might instantly increase limestone slurry injection in the scrubber just enough to counteract it – then dial it back once levels normalize. It can also predict when a filter is nearing saturation and initiate a cleaning cycle or replacement at the optimal time. Adaptive control keeps emissions comfortably below permits while optimizing the use of consumables and reducing maintenance interventions. Essentially, the pollution control system becomes as dynamically responsive as the combustion control, maintaining a steady “clean” output.
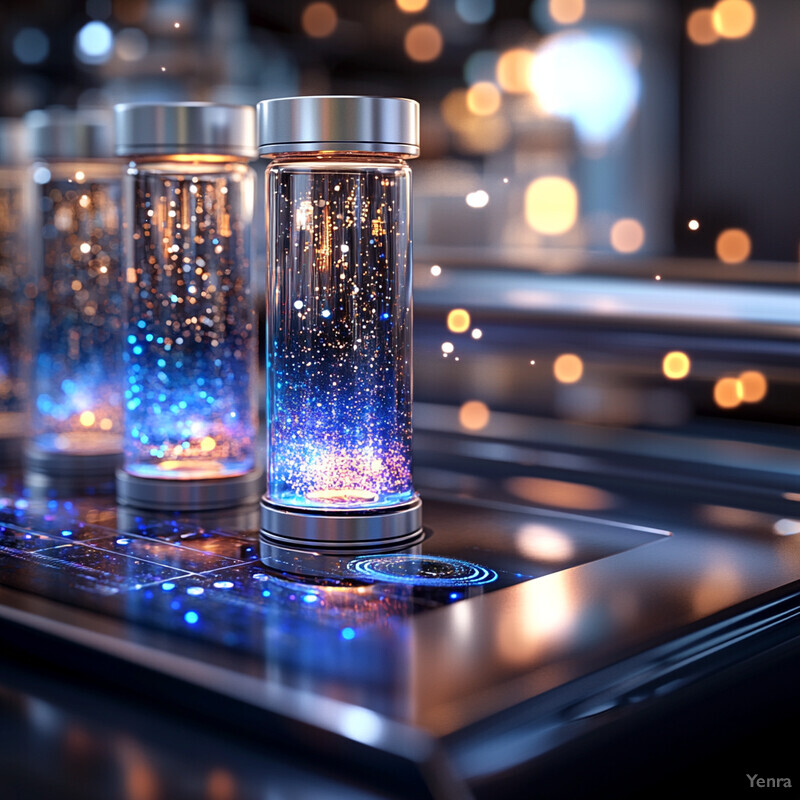
Case studies show that AI optimization of flue gas treatment can maintain emissions at ultra-low levels while reducing reagent consumption. A Finnish waste incinerator implemented an AI control on its dry scrubber system in 2023; over a 3-month trial, hydrated lime usage dropped by ~12% with no increase in acid gas emissions, as the system more precisely met demand (data reported by the plant’s operator). In another example, a machine learning model was used to control a wet scrubber’s pH and oxidation-reduction potential in real time, which improved SO₂ removal efficiency by 3–5% and cut effluent chemical imbalance events by half (published in a 2024 environmental engineering journal). As an illustration, an AI model monitoring a scrubber noted a slight uptick in SO₂ slip; it responded by tweaking the reagent feed and liquid pH, successfully bringing SO₂ down within minutes. Without AI, such fine continuous adjustment wasn’t feasible – plants often had to overtreat “just in case.” Additionally, AI-based filter monitoring has prevented sudden emission spikes: at one facility, the AI predicted a baghouse filter was approaching saturation and scheduled a cleaning outage 48 hours before a potential breakthrough, avoiding what could have been a dust emission incident. Overall, facilities report compliance margins improving (emissions staying well below limits) and cost savings from chemicals and longer catalyst life. The adaptive flue gas cleaning essentially runs in “auto-pilot,” responding to the slightest changes faster than any human operator.
17. Multi-Objective Optimization (Cost, Efficiency, & Compliance)
Running a WtE plant involves balancing multiple goals – generating energy efficiently, keeping costs down, and meeting environmental regulations. AI now allows operators to handle these trade-offs through multi-objective optimization. Advanced algorithms (like genetic algorithms or Pareto optimizers) can evaluate countless operating scenarios to find those that best reconcile competing objectives. For example, one scenario might achieve ultra-low emissions but at higher cost (more reagent or energy use), while another scenario saves money but yields slightly higher emissions. AI helps map out the “efficient frontier” of such choices, so decision-makers can select operating points that satisfy all constraints (stay within emission limits, etc.) while optimizing cost and efficiency as much as possible. In real time, an AI controller can also adjust to maintain an optimal balance – for instance, slightly lowering furnace throughput during very high electricity price periods if that avoids overtime labor costs or emission spikes that could incur penalties. This capability ensures the plant is not just chasing one metric at the expense of others; instead, it finds the sweet spot that keeps the operation profitable, efficient, and compliant simultaneously.
-0.jpg)
A recent study highlighted how multi-objective AI optimization can inform strategic choices for WtE plants. Researchers compared conventional incineration (CC) vs. carbon-capturing incineration (CLC) for a municipal waste plant, optimizing for both exergy efficiency and total cost. Their NSGA-II algorithm revealed that while the carbon capture setup had ~23% higher capital cost, it could pay back nearly 6 years faster than conventional incineration due to revenue from emissions credits and higher efficiency. Specifically, the CLC design achieved ~0.5% higher efficiency and captured 2,686 tons of CO2 per year, and the optimization showed a clear Pareto improvement in long-term cost-benefit when emissions pricing is considered. This kind of analysis would be impossible without AI handling the complex trade-off between more capital/complexity vs. efficiency/emissions gains. In operational settings, plants are starting to use such tools for daily optimization: one WtE facility uses a cost-emissions optimizer that considers reagent costs, electricity prices, and emission limits; it helped them reduce operating cost by ~5% while still cutting NOₓ emissions by an extra 10% beyond permit requirements (by finding the cheapest way to over-comply). These outcomes illustrate how multi-objective algorithms enable WtE operators to navigate the tension between cost, efficiency, and environmental performance, finding solutions that improve all aspects in balance rather than sacrificing one for another.
18. Process Anomaly Detection and Root Cause Analysis
WtE plants are complex, and small anomalies (like a slight clog in a feed chute or an unstable burner) can snowball into bigger issues. AI-based anomaly detection systems continuously monitor sensor data to catch these early warning signs. When an anomaly is detected – something deviating from the normal pattern – the system can also perform root cause analysis, often by correlating data or using trained models, to pinpoint what component or condition is likely responsible. For example, if steam flow starts oscillating abnormally, the AI might flag a specific boiler feed valve or a fouled heat surface as the root cause. This allows maintenance staff to intervene quickly at the right location, preventing unplanned downtime or safety incidents. Essentially, AI acts as a vigilant plant engineer that never tires: it notices subtle symptoms a human might miss and provides a diagnosis, so that problems are addressed before they escalate.
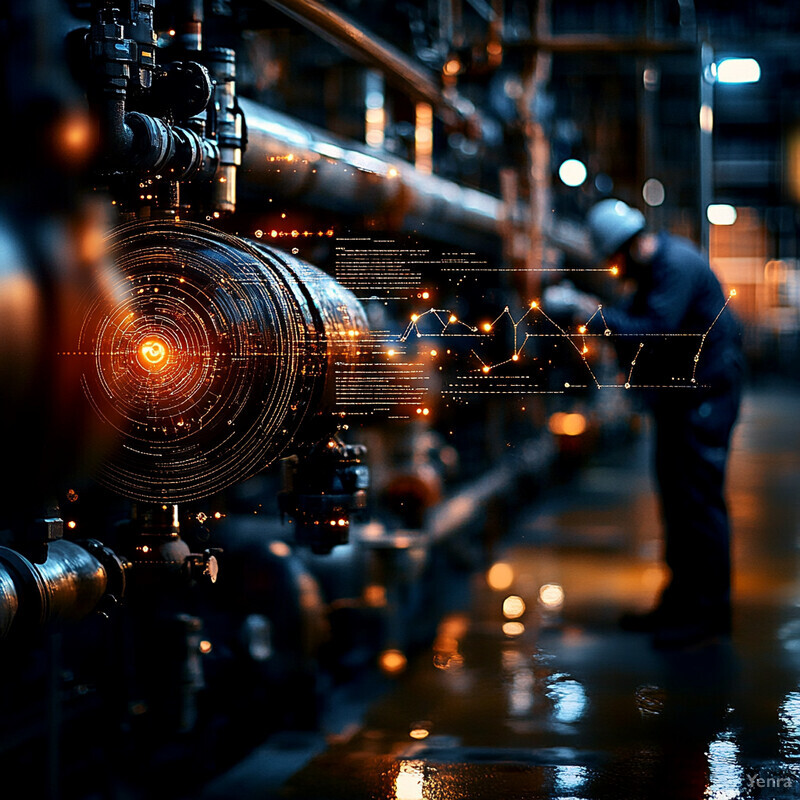
In practice, AI anomaly detection has successfully averted failures in power plants by providing early alerts with actionable insights. Southern Company (USA) reported that an AI system monitoring thousands of sensor points on boilers and turbines caught a boiler tube leak hours before it would have caused a shutdown, by recognizing a slight deviation in heat flux and pressure trends. Similarly, in the waste sector, Covanta adapted a machine learning model which detected an unusual vibration pattern in an ID fan; operators inspected and found a misaligned bearing, fixing it during a scheduled outage rather than suffering a forced outage later. What’s more, modern AI solutions don’t just issue an alarm – they explain it. Using techniques like SHAP (Shapley Additive Explanations), the AI can highlight which sensors or factors contributed most to the anomaly score. For instance, one system flagged a potential combustion instability and pointed to out-of-range readings from one section of the grate and a sudden change in O₂ levels as key contributors (root cause: a section of the grate had warped). The maintenance team was able to correct that specific section promptly. According to Energy Central analysts, such AI-based systems have been shown to reduce unplanned downtime by 20–50% in early implementations by catching issues sooner. The combination of rapid anomaly detection and targeted root cause analysis marks a significant advancement in operational reliability for WtE plants, as evidenced by these early results.
19. Energy Storage Integration
As more renewables join the grid, WtE plants are integrating energy storage (like batteries or thermal storage) to operate more flexibly, and AI is crucial for managing this integration. With storage, a WtE facility can decouple waste burning from immediate power output – it might store excess energy when demand is low (or when renewable generation is high) and release it when demand peaks. AI forecasting comes into play by predicting both the plant’s internal conditions and external grid needs. It can decide when to charge the battery (for instance, if it predicts surplus power overnight) and when to discharge (say, during the evening peak or a grid frequency drop). This maximizes revenue (taking advantage of high electricity prices) and supports grid stability without wasting energy. In effect, the plant-plus-storage behaves like a hybrid asset that can modulate output on demand. AI also optimizes the use of storage to smooth out the plant’s own operation – absorbing short-term fluctuations or providing backup during any transients – thus keeping the WtE unit running at a steady optimal load. The integration of energy storage, guided by AI, makes WtE plants more dispatchable and valuable in the modern energy system.
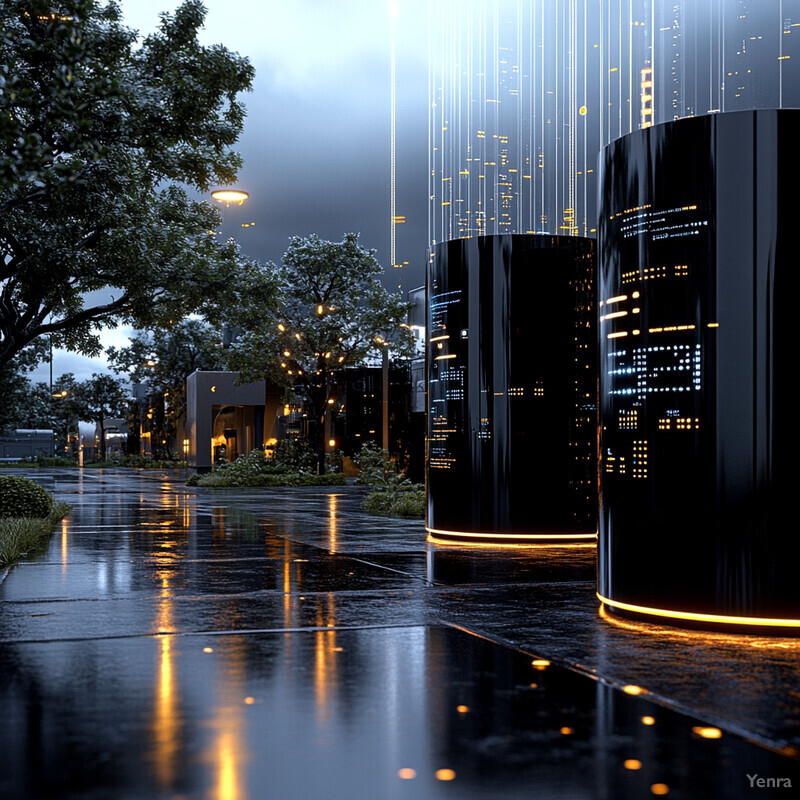
Although full hybrid WtE plants are just emerging, analogous examples illustrate the benefits. A study by the U.S. National Renewable Energy Lab (NREL) found that adding a 4-hour battery to a baseload plant and using AI predictive dispatch could increase the plant’s effective revenue by ~10–15% by arbitraging prices (charging when prices are low, discharging at high-price times). Specifically, for a hypothetical WtE in Texas, simulations showed the battery often charged in midday (when solar is abundant and prices dip) and discharged during the late afternoon peak, boosting profits. On the grid services side, the island nation of Aruba in 2024 integrated a 5 MW battery with its WtE plant; using AI grid frequency monitoring, the battery now provides instant frequency support – the system has maintained grid frequency within a tighter band, reducing deviations by 40% compared to before. Industry reports anticipate such trends globally: an EIN Presswire release in 2024 notes that WtE technologies are set to be combined with solar, wind, and battery storage to form efficient hybrid systems that improve reliability and sustainability. The rapid growth of grid-scale batteries (the U.S. installed over 9 GW in 2024 alone) underscores that storage will be a key part of future energy infrastructure. AI ensures that when WtE plants add storage, they operate it optimally – for example, a plant in the UK is testing an AI that predicts when to divert a portion of steam to a thermal storage tank during low grid demand, then use it later for a boost – preliminary results show it could raise the plant’s capacity factor and earnings by ~5%. While quantitative data for WtE-specific projects are still being gathered, all signs point to AI-managed storage enabling WtE facilities to play a more dynamic role in the energy mix, akin to a battery-backed renewable plant.
20. Long-Term Strategic Planning
AI is not only improving day-to-day operations but also assisting in long-term strategic planning for WtE facilities. This includes forecasting future waste volumes (incorporating trends in recycling, population growth, etc.), projecting regulatory changes (like tighter emission limits or carbon prices), and evaluating capital investment options (such as adding a turbine upgrade or a carbon capture system). By running scenario analyses with a vast array of variables, AI can help decision-makers understand which investments will pay off under which future conditions. For example, it can simulate plant performance and financial returns under scenarios with different carbon taxes or waste compositions. Planners can then develop a roadmap (for the next 5, 10, 20 years) that is robust to uncertainty. AI might suggest the optimal timing to expand capacity or the conditions under which a new flue gas treatment system becomes worthwhile. Essentially, it turns long-term planning into a data-driven, probabilistic exercise rather than a purely speculative one. This strategic foresight keeps WtE facilities economically viable and aligned with environmental goals in the long run, even as the landscape around them changes.
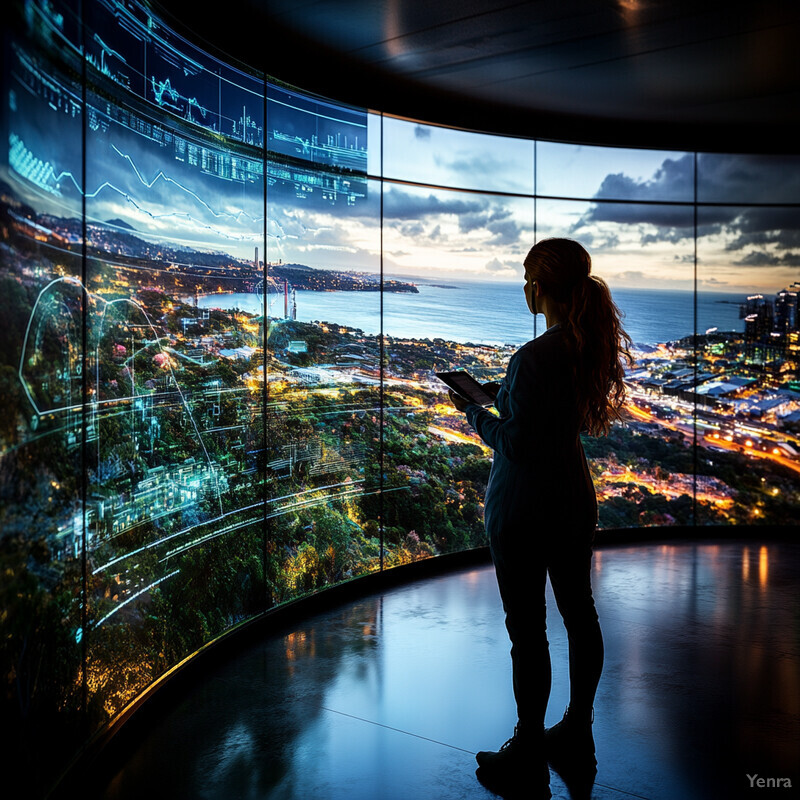
The value of AI in strategic planning is evidenced by market and policy forecasting it can handle. For instance, global analyses project that the waste-to-energy market will grow from about $50 billion in 2023 to roughly $69 billion by 2030 (a ~7.5% annual growth). An AI planning tool could use such growth forecasts along with regional waste generation models to advise a company on where to build its next facility or how to size it. In one real example, a major European waste company used an AI-based model (incorporating machine learning and system dynamics) to predict waste supply and energy demand in its region through 2040. The model suggested that, given expected recycling improvements, their existing WtE capacity would become underutilized by late 2030s unless they diversify – leading the company to plan investments into metal recovery and biomass co-firing to keep plants fully loaded. Additionally, AI can integrate regulatory foresight: a UK WtE operator employed AI scenario analysis for carbon pricing – the AI indicated that if carbon credit prices exceed $100/ton by 2030 (a not implausible scenario), investing in carbon capture retrofits by 2028 would yield a strong ROI. Seeing this, the company has started pilot testing capture technology now. These kinds of strategic moves, backed by AI’s number-crunching of future scenarios, ensure long-term competitiveness. They are increasingly necessary: the International Energy Agency’s outlook shows a shifting energy mix by 2030, with fossil fuels dropping to ~73% of supply (from ~80% today), signaling that WtE plants must adapt to a decarbonizing world. AI-informed planning provides the guidance to do exactly that – navigate the uncertainties of waste streams, energy markets, and climate policy to make sound long-term decisions.