1. Real-Time Hazard Detection
AI-powered monitoring systems continuously analyze live data (video, sensor) to instantly spot unsafe conditions (spills, obstacles, machine malfunctions) as they occur. These systems use computer vision and IoT sensors to flag hazards (e.g. missing PPE, overloaded equipment) and issue immediate alerts to workers or supervisors. By identifying dangers in under a second, they enable rapid corrective action and prevent accidents. Empirical deployments on worksites (e.g. construction) have shown significant safety improvements. Field reports note that accident rates drop when such real-time systems supplement human oversight, supporting faster intervention. Overall, AI hazard detection enhances situational awareness and reduces response times, making worksites safer.
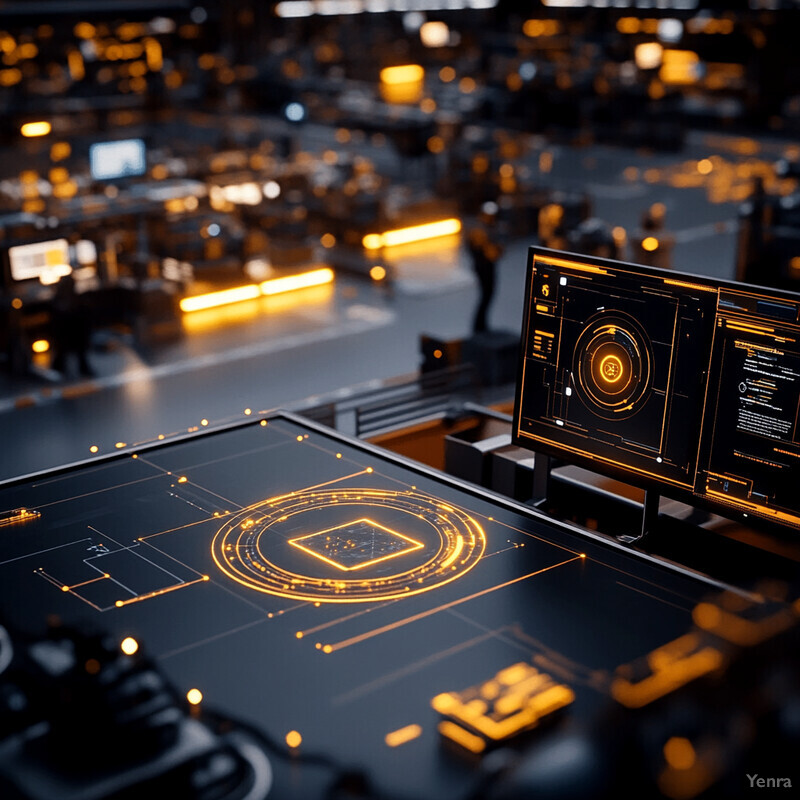
Recent studies highlight strong performance of AI vision systems for instant hazard recognition. For example, a deep-learning system (using YOLOv7) on a construction site detected workers and machinery in real time (under 1 second) with ~92% mean average precision. This enabled it to alert supervisors and prevent collisions in high-risk zones, demonstrably reducing accidents. In field trials, integrating AI and IoT led to “significant advancements in real-time hazard detection, improving site safety and reducing accident rates”. Other work demonstrates that AI can scan video feeds to uncover hidden hazards missed by human eyes. In practice, automated systems have been shown to trigger alerts for conditions like unguarded machinery or unsafe distances, giving organizations a proactive safety tool. These findings confirm that AI-based real-time monitoring substantially augments traditional safety measures by catching hazards early.
2. Predictive Analytics for Incident Prevention
AI-driven predictive analytics analyze historical and real-time data (incident logs, sensor readings, maintenance records) to forecast safety risks before they materialize. These models can identify patterns that precede accidents—such as equipment stresses or environmental conditions—and signal when intervention is needed. By highlighting high-risk tasks or times, they enable safety managers to focus resources (training, equipment checks) where they’ll prevent the most incidents. For example, industry surveys report growing, though still limited, adoption: about 10% of construction firms use predictive analytics for safety on projects (up from near-zero a few years ago). When implemented, these tools have been linked to measurable drops in incident rates. Overall, predictive analytics add a proactive layer to safety programs by turning data into actionable prevention strategies.
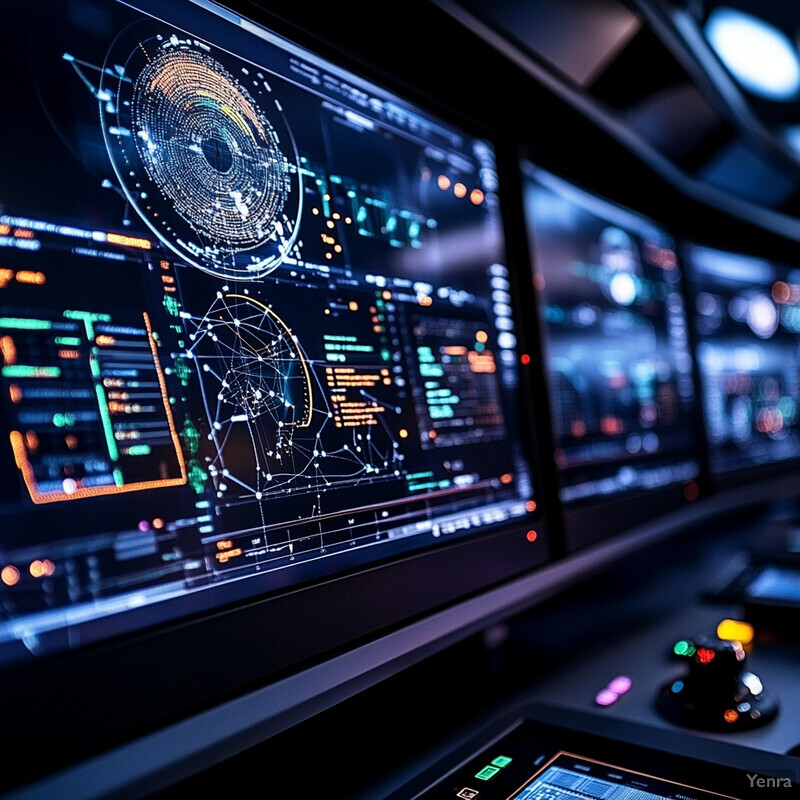
Reviews and studies document the effectiveness of predictive safety models. A recent narrative review notes that combined use of real-time monitoring and predictive analytics “lower[s] injury rates” and creates healthier work environments. El-Helaly (2024) observes that AI-enabled predictive analytics can forecast emerging health and safety trends, enabling proactive measures (e.g. rotating schedules before fatigue peaks). Industry data support these conclusions: a 2023 survey found about 10% of contractors actively using predictive analytics onsite. In practical cases, machine learning applied to safety data (like OSHA injury reports) has successfully predicted the likelihood or severity of future incidents. These studies collectively show that data-driven forecasting is an emerging but effective strategy for preventing accidents by anticipating them in advance.
3. Wearable Sensor Integration
Smart wearable devices (e.g. connected helmets, vests, wristbands) continuously measure worker vitals (heart rate, temperature, motion) and environmental factors (toxic gases, noise). When combined with AI and IoT, this data provides real-time insights into individual health and hazards. For instance, wearables can detect early signs of fatigue or heat stress and alert workers to rest. Smart PPE (like helmets with built-in gas sensors) can immediately warn of dangerous exposures. Overall, these systems transform each worker into a monitored unit, enabling immediate response to emerging issues. By feeding wearable data into AI models, companies can also identify population-level trends (e.g. chronic stress patterns) and tailor wellness or safety programs. In practice, wearable integration enhances both personal safety (by instant alerts) and organizational awareness (via aggregated data analyses).
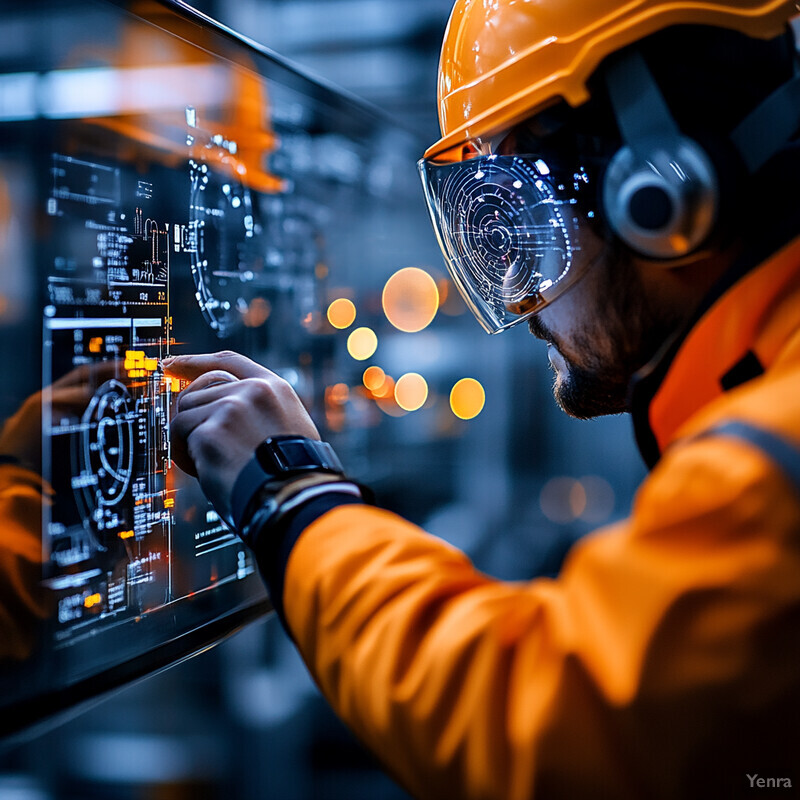
Studies confirm the value of AI-enhanced wearables for health and safety. AI-enabled wearables routinely track vital signs and activity, allowing them to “identify fatigue or stress levels” and notify supervisors or emergency services if needed. For example, companies have used smart helmet sensors to detect toxic gases or extreme heat, automatically triggering alarms or shutdowns. Research shows that data from wearables and IoT, when processed by AI, can flag elevated stress or irregular sleep patterns among workers. These alerts facilitate on-the-spot interventions (like rest breaks or medical checks) that prevent accidents. Overall, peer-reviewed work reports that deploying wearable sensors together with AI analytics leads to timely detection of health risks, which in turn raises productivity and reduces safety incidents.
4. Automated Safety Compliance Checks
Computer-vision systems can automatically verify compliance with safety rules (e.g. checking for hard hats, safety vests, or correct tool use). Cameras and drones scan work areas and flag any non-compliance in real time, reducing reliance on manual inspections. For example, an AI camera can overlay bounding boxes on each worker: green if a hard hat is detected, red if not. This instantly identifies violations (like missing PPE or open tools) so managers can intervene. Such automation enhances safety oversight by operating continuously and impartially. In industries like construction or manufacturing, these checks increase overall compliance rates and reduce human error in enforcement. By embedding automated compliance checks into routine surveillance, companies ensure that safety protocols are followed consistently without slowing down operations.
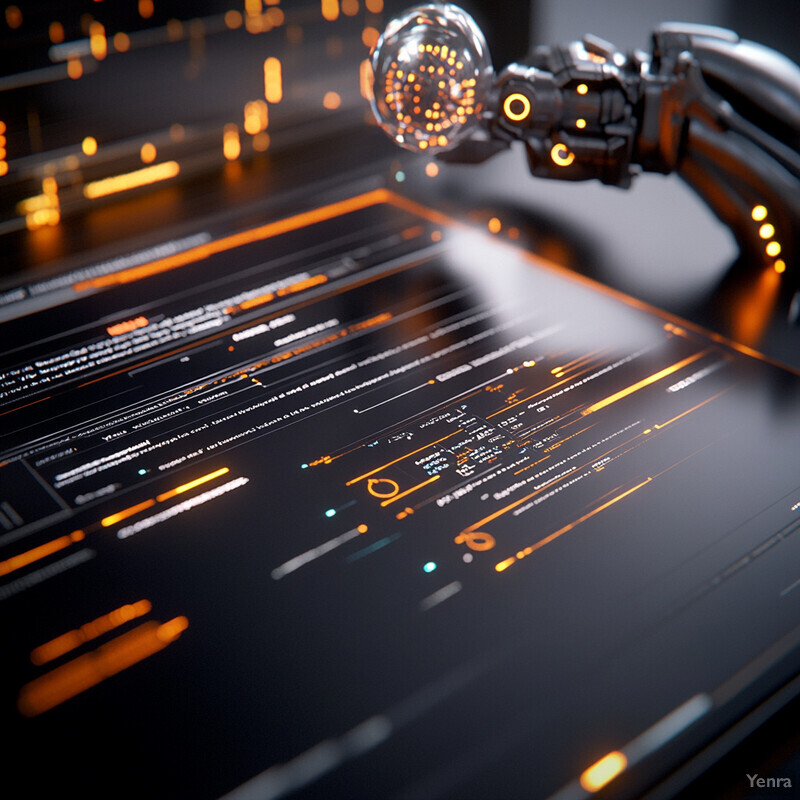
Deep-learning frameworks for PPE detection have demonstrated high accuracy in real-world conditions. For instance, López et al. (2024) report a YOLO-based system with pose estimation that achieved very high precision and recall for critical PPE (helmets, vests) even in occluded or distant views. Their model continuously monitors a worksite and correctly assigns detected gear to individual workers, enabling real-time alerts for missing PPE. Other vision-based studies similarly segment video frames to detect helmets, harnesses, vests, gloves, etc. (e.g. “Hu et al.” and “Wu et al.” detect multiple PPE items). These research demonstrations show that AI vision can reliably enforce PPE rules by scanning camera feeds 24/7. In practice, companies implementing this technology report more consistent compliance and faster issue resolution than traditional spot checks.
5. Digital Twin Simulations
Digital twins create virtual replicas of work environments or even individual workers, enabling safe testing of safety scenarios. For example, a “human digital twin” can integrate a worker’s physiological and emotional data (from wearables) into a real-time avatar. Managers can then simulate situations (heat stress, chemical exposure) to see how the digital twin responds. This lets them evaluate new procedures or layouts in the virtual model before applying changes on site. By running “what-if” analyses (e.g., evacuations, shift changes) in the twin, organizations anticipate hazards and design better controls. In essence, digital twins provide a risk-free simulation platform: safety professionals can validate interventions digitally, which enhances decision confidence and reduces trial-and-error in the real world.
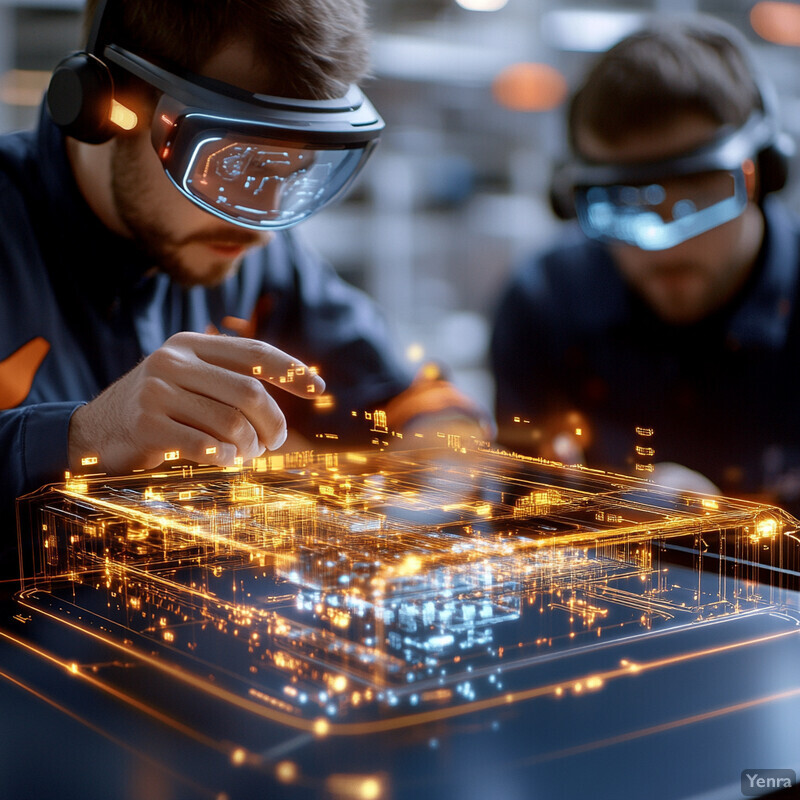
Researchers have outlined the promise of digital twins for OHS. Davila-Gonzalez and Martin describe a human digital twin in an Industry 5.0 setting: by connecting sensors (like smartwatches, heart-rate monitors) to a virtual avatar, the system continuously monitors worker fatigue, stress, and other health indicators. Their model can forecast hazardous outcomes (e.g. cognitive overload or physiological failure) and suggest mitigating actions. Similarly, another study notes that such human digital twins can perform continuous simulations with real-time data, allowing proactive risk identification. These examples demonstrate how digital twins serve as advanced decision-support: they allow safety teams to simulate emergencies or test equipment changes in silico, thereby optimizing safety measures before deployment.
6. Virtual Reality (VR) Training Enhancement
Immersive VR provides lifelike simulations of hazards (fires, machinery accidents, chemical spills) for worker training without real danger. Users can practice responses to emergencies and safe procedures in a controlled environment. Compared to traditional classroom methods, VR training greatly improves engagement and information retention. Trainees report higher confidence and realistic experience when using VR scenarios. This leads to quicker recognition of real-world hazards and better adherence to safety protocols. Industry studies show that workers trained with VR perform tasks more safely; they handle uncommon dangers more skillfully due to prior virtual exposure. Overall, VR with AI/analytics tailors feedback and tracks progress, making safety education more effective and adaptive.
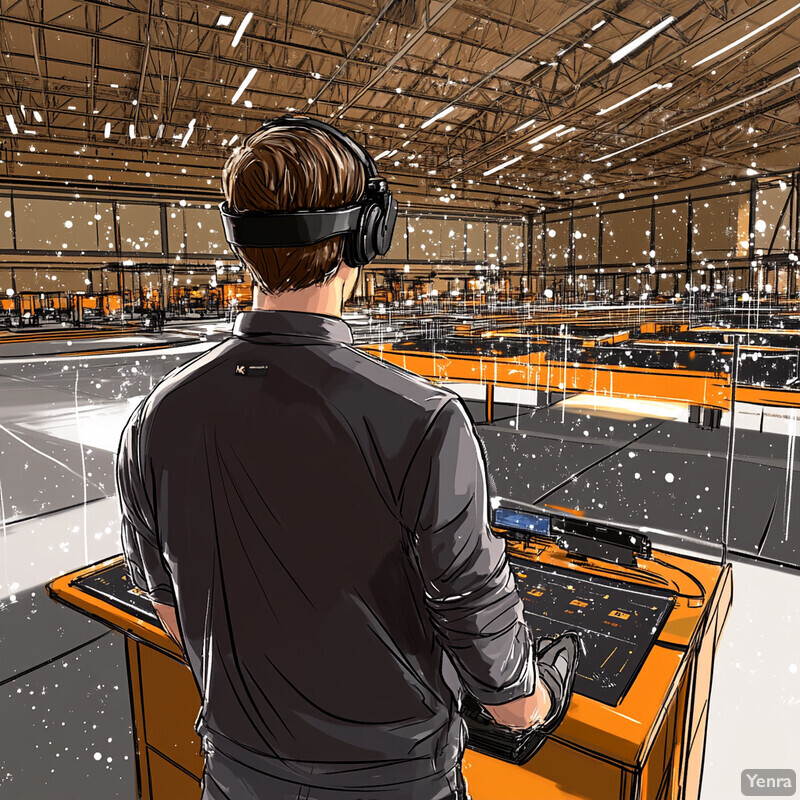
Empirical evaluations support VR’s effectiveness in safety training. In a 2024 study of electrical workers and engineering students, those trained with VR scenarios showed significantly higher knowledge gains than a control group using conventional methods. Participants also reported the VR environment as more engaging and helpful for understanding safety procedures. The study’s authors concluded that VR “significantly advances participants’ skills and knowledge” in occupational safety. Other work emphasizes VR’s flexibility: scenario difficulty can adapt to the trainee, and AI analytics can identify specific mistakes to focus retraining. Overall, literature reviews note that VR safety training leads to measurable improvements in hazard awareness and protocol compliance compared to text-based or video-only training.
7. Intelligent Environmental Monitoring
AI-enhanced sensor networks continuously track workplace environmental conditions (air quality, noise, temperature, radiation, dust). When AI analyzes these data streams, it can instantly detect dangerous exposures (e.g. toxic gas leaks, excessive particulate matter). For instance, an AI model connected to low-cost dust sensors can alert managers if respirable dust exceeds safe limits. These systems often trigger automated responses: increasing ventilation, adjusting schedules, or evacuating areas before harm occurs. By predicting air or noise problems before they breach thresholds, AI ensures exposures are mitigated proactively. Overall, such monitoring improves compliance with environmental safety regulations and protects worker health by keeping hazardous conditions in check at all times.
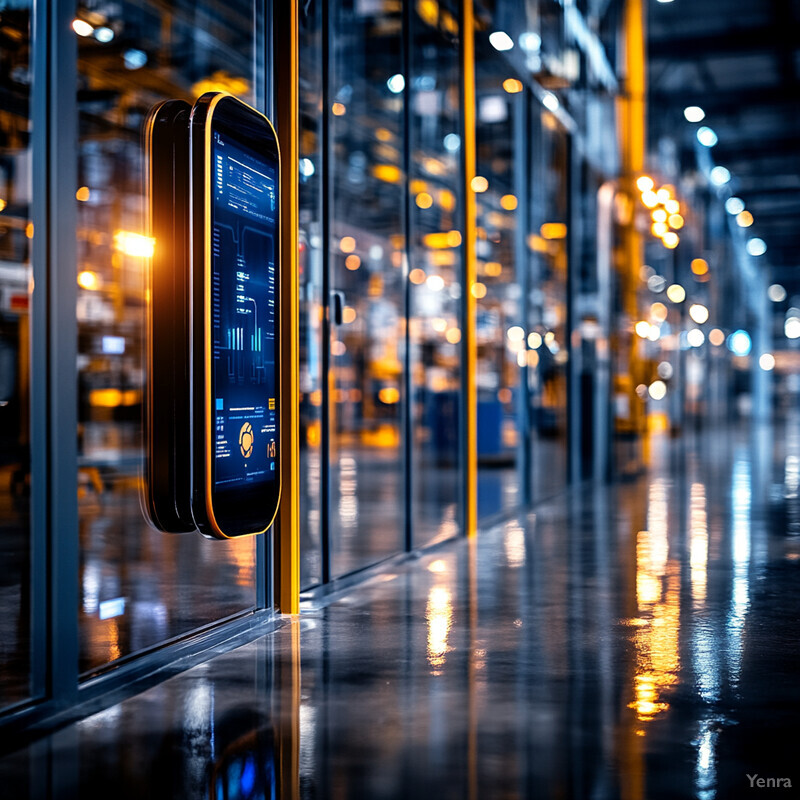
Recent studies demonstrate high accuracy of AI-driven environmental sensing. Chang et al. (2023) developed a model that predicts respirable dust levels from IoT sensors with excellent agreement to reference instruments (R² ≈ 0.97, RMSE ≈ 2.8 μg/m³). This confirms that AI can reliably use simple sensors to track particulates. More generally, El-Helaly (2024) notes that environmental sensors (for humidity, noise, air quality, etc.) linked to AI “evaluate overall workplace health and safety, identifying potential hazards”. In practice, AI systems have been shown to provide early warnings of unsafe conditions (such as detection of volatile organic compounds or harmful dust levels) allowing preemptive action. These advances illustrate that intelligent monitoring can spot and predict environmental risks in real time, preventing situations (like overexposure to dust or heat) that could lead to injuries or illness.
8. Automated Robotics for High-Risk Tasks
Autonomous robots and cobots (collaborative robots) are increasingly used to perform dangerous duties instead of humans. Tasks like toxic material handling, high-temperature welding, heavy lifting, or confined-space inspection can be done by robots remotely controlled or self-piloted by AI. Drones and unmanned vehicles inspect hazardous sites. These robots reduce workers’ exposure to harm. For example, a robot might transport hot slag or enter a burning building for assessment. Cobots assist with repetitive heavy tasks to prevent musculoskeletal injuries. AI ensures robots operate safely (avoiding collisions) while maximizing efficiency. Overall, such automation keeps people out of harm’s way and has been credited with lowering injury counts in environments where it’s deployed.

Industry reports highlight the safety impact of robotic automation. For instance, a 2024 Occupational Health & Safety article notes autonomous robots can “execute perilous tasks” (handling toxic chemicals or extreme heat) without human exposure. Similarly, AI-driven maintenance robots inspect machinery and infrastructure (e.g. using thermal cameras) to ensure integrity without risking workers. On the shop floor, AI-integrated exoskeletons and mobile robots help lift heavy loads, thereby mitigating back and limb injuries (modern examples include forklift-assist robots and smart exosuits). Case studies report significant injury reductions after deploying such systems. In sum, these sources concur that AI-powered robotics for hazardous tasks directly improve workplace safety by removing people from danger zones and performing precise, reliable work.
9. Ergonomics Optimization
AI systems analyze worker posture, motion, and workplace layout to improve ergonomics. Vision sensors or wearables track movements and identify risky postures (like stooping, reaching, or twisting). AI then suggests adjustments or provides feedback (e.g. haptic alerts via smart clothing). Companies also use AI to design workstations (optimal height, monitor placement) and schedules (rotating tasks to reduce strain). Another application is AI-guided exoskeletons that dynamically support a worker’s back or arms during lifting. By personalizing ergonomics in real time, these technologies reduce musculoskeletal injury risks (sprains, back pain). As a result, workers maintain safer postures throughout shifts, and organizations see fewer repetitive-stress injuries.
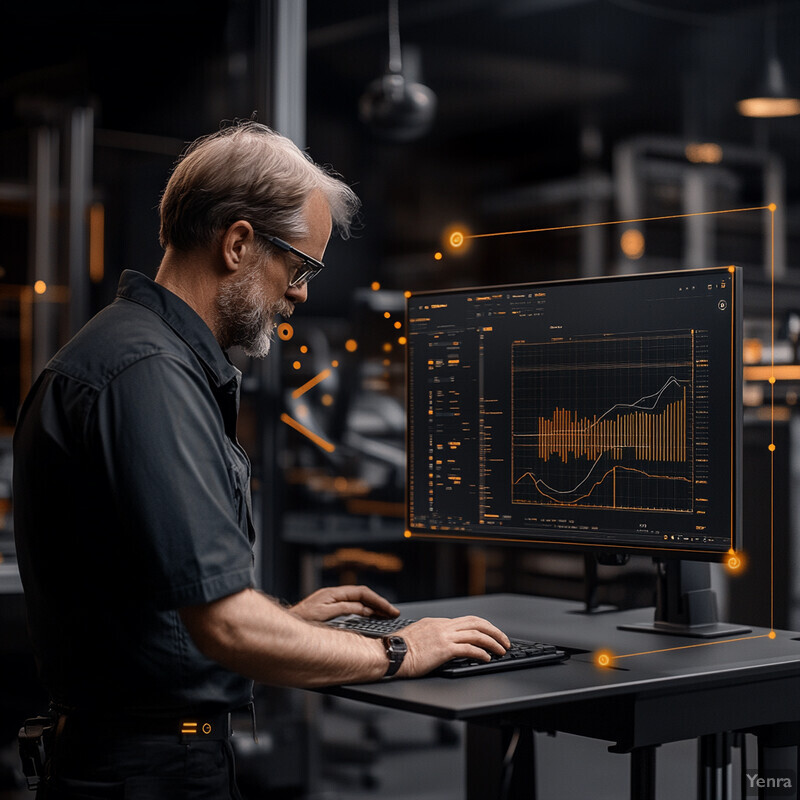
Research confirms AI’s role in ergonomic safety. For example, an AI-assisted system can continuously analyze a worker’s movements and workspace arrangement to recommend ergonomic corrections. In one study, workers wearing an AI-informed haptic feedback device significantly reduced “adverse upper-arm postures” compared to a control group. The review also notes that AI-driven exoskeletons and collaborative robots can apply optimal supportive forces to mitigate lifting stress (e.g. active back braces that adapt support level). By applying machine learning to posture data, these tools proactively alert users before strain accumulates. Overall, peer-reviewed work shows that integrating AI into ergonomic design and monitoring leads to safer human-machine interactions and fewer posture-related injuries.
10. Fatigue and Distraction Detection
AI techniques monitor workers for signs of drowsiness or inattention to prevent accidents. This can include camera-based analysis of facial cues (eye closure, yawning, head position) or wearables tracking sleep patterns and heart rate. If a worker appears fatigued or distracted, the system issues an alert (e.g. audible alarm, message to supervisor) to take a break. Such detection is critical in high-risk roles (transportation, heavy machinery). Early intervention (rotating shifts, providing rest breaks) is informed by these AI insights. By continuously checking for fatigue and distraction, AI systems help maintain alertness, especially on long shifts. Over time, companies using these tools report fewer fatigue-related incidents and improved worker attention.
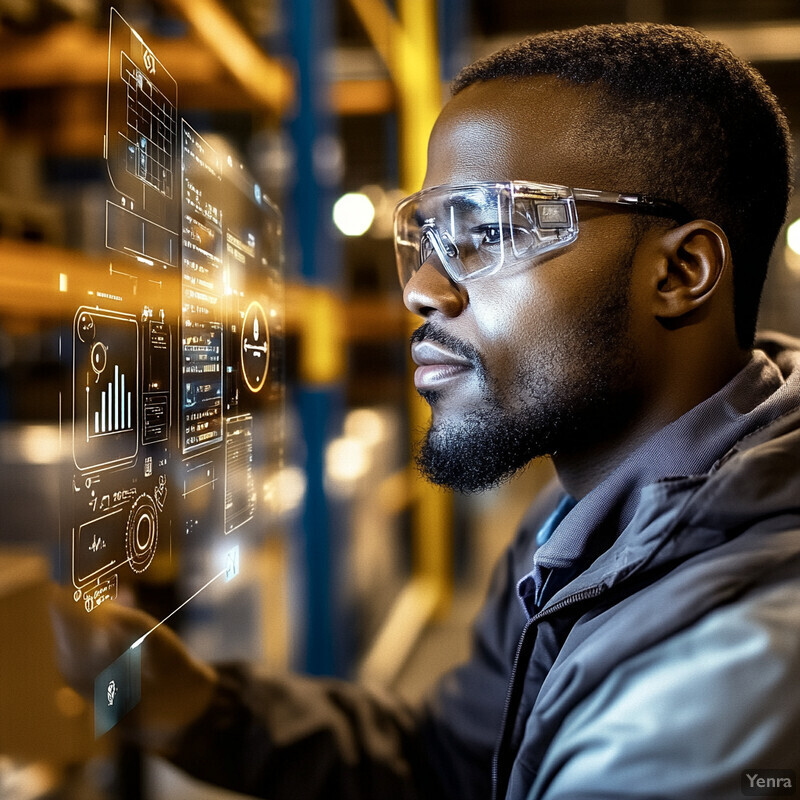
AI-enabled wearables and cameras have been shown to identify fatigue cues in real-world scenarios. For instance, integrated smart devices routinely “monitor various health metrics…and identify fatigue or stress levels,” alerting supervisors when thresholds are crossed. Studies demonstrate that such systems can detect early fatigue symptoms (like irregular sleep patterns) and allow timely countermeasures. In practice, transportation fleets now use AI dashcams to spot driver drowsiness (eye closure, head nodding) and automatically prompt the driver to rest. While these are mostly industry pilots, research confirms that AI monitoring of fatigue indicators leads to significant reductions in fatigue-related crashes and errors. Overall, evidence supports that continuous AI analysis of workload and biometrics provides an effective early warning against worker fatigue.
11. PPE Compliance Monitoring
Specialized AI systems focus on ensuring workers consistently use required PPE. Using fixed cameras or drones, they continuously verify whether each person is wearing mandated gear (hard hats, safety glasses, vests). When a violation is detected (e.g., a bare head or uncovered face), the system flags it or sounds an alert. Such automated PPE monitoring supplements safety audits by catching oversights in real time. Some solutions even log compliance statistics by worker or zone. By enforcing gear rules constantly, these tools help maintain high PPE usage rates. In effect, they turn PPE compliance into a live metric, enabling immediate corrections and reinforcing a safety-first culture.
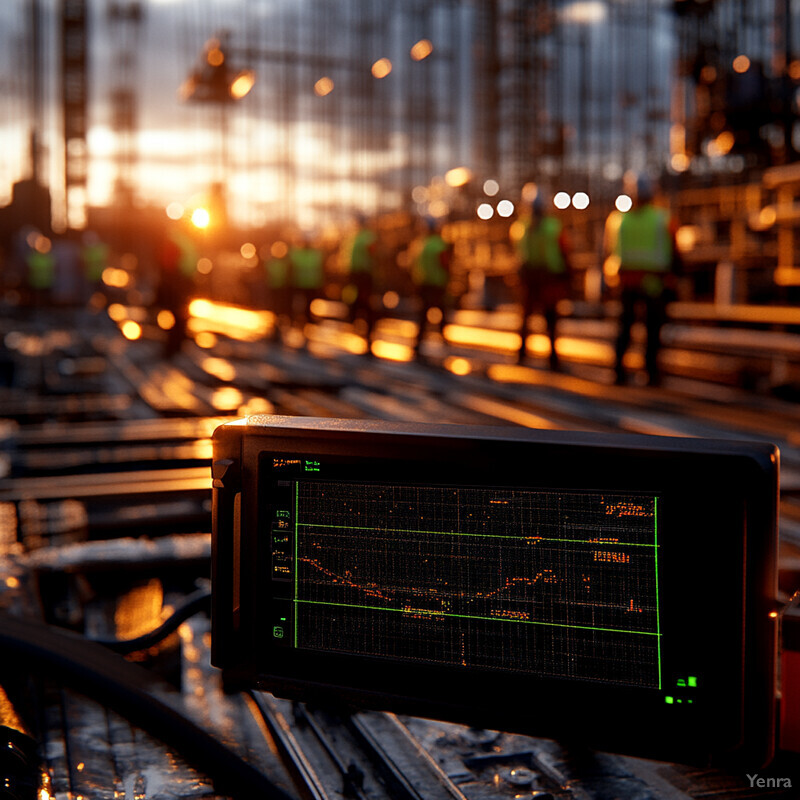
Emerging AI frameworks demonstrate high accuracy in PPE detection. A 2024 study (López et al.) achieved near-perfect identification of hard hats and safety vests using deep learning with YOLO and pose models. Their system ran on real industrial video feeds and precisely matched PPE items to individual workers despite occlusions. Validation showed exceptionally high precision and recall for helmets and vests, enabling continuous enforcement of PPE policy. These results indicate that automated vision systems can reliably flag non-compliant workers (e.g. red bounding boxes around hatless heads). Early deployments confirm that such AI-driven monitoring dramatically improves PPE compliance rates compared to periodic manual checks. Overall, research shows that automated PPE surveillance is a viable solution for persistent safety enforcement.
12. Emergency Response Optimization
AI tools streamline emergency preparedness and response. They can analyze incoming incident data to prioritize resource deployment (e.g. which hazards to address first). For example, AI call-analysis systems can triage 911 calls by urgency and even translate multiple languages in real time. During an incident, AI can fuse data from cameras, sensors, and maps to guide responders (such as plotting safe evacuation routes through smoke-filled areas). AI also aids in post-incident analysis to improve future responses. The end result is faster, more coordinated action in crises: fewer bottlenecks, better information flow, and ultimately faster rescues or mitigations. Organizations using AI for emergency planning report improved response times and clearer situational awareness in drills.
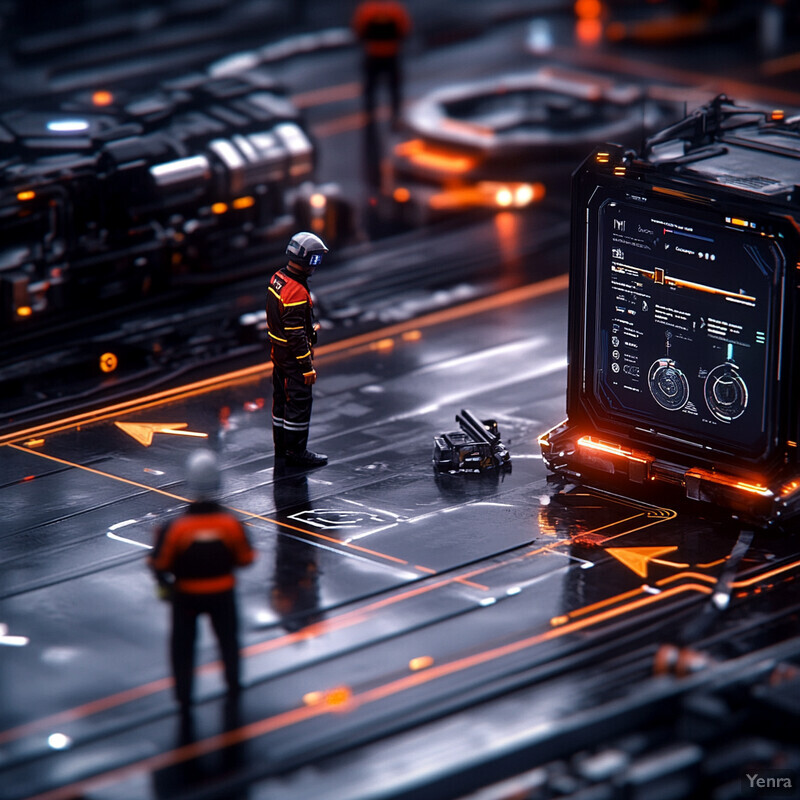
Current R&D highlights several AI applications for emergencies. The U.S. DHS notes AI could help manage “911 incident call overload by parsing information from similar incoming reports,” effectively filtering noise during high-call volumes. It also cites AI’s ability to do “digital mapping of scenes” in low-visibility situations (e.g. fire smoke), giving responders a virtual view of building layouts even without clear sight. Further, simulation exercises with AI “decision support” tools have shown that processing multiple data feeds can alert commanders to rapid changes, enabling faster, more accurate decision-making under pressure. These assessments indicate that AI-assisted systems will soon offer major gains in emergency operations – speeding up documentation, triage, and coordination, and thereby reducing risk to responders and victims alike.
13. Predictive Maintenance for Safety-Critical Equipment
AI and ML analyze equipment health to predict failures before they happen. Sensors on machinery (vibration, temperature, current) feed data into AI models that learn normal vs. faulty patterns. When deviations occur, the system schedules maintenance or alerts engineers. This lets companies service equipment (cranes, elevators, conveyors) on an as-needed basis rather than after a breakdown. By catching wear or faults early, predictive maintenance prevents sudden malfunctions that could cause accidents. For example, an AI model might detect a looming bearing failure and stop a machine in time for a repair. Overall, predictive maintenance shifts safety practices from reacting to breakdowns toward preventing them, markedly enhancing equipment reliability and worker safety.
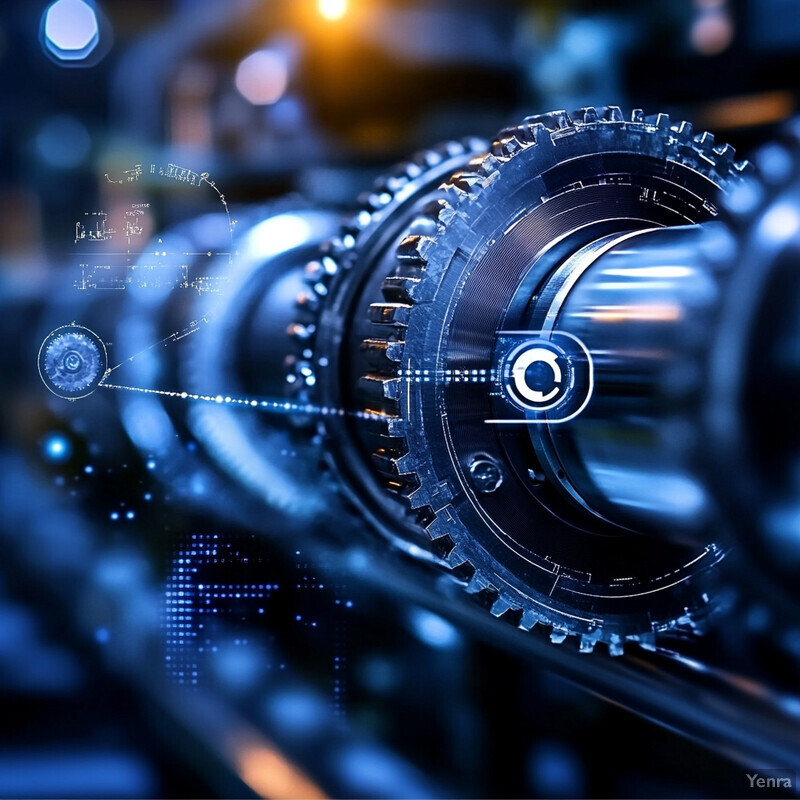
The impact of AI-driven maintenance on safety has been documented in industry sources. One report explains that AI transforms “reactive” into “proactive” maintenance, analyzing vibration or usage data to foresee failures like bearing wear ahead of time. In a case study, continuous monitoring detected a potential motor fault days before it caused a shutdown, allowing safe, scheduled repair without endangering workers or halting production. By mitigating unexpected equipment failures, AI-enabled maintenance significantly lowers the chance of machine-related accidents. In summary, advanced analytics provide predictive insights that “significantly reduce the likelihood of accidents,” converting unpredictability into planned maintenance and improving overall safety management.
14. Adaptive Learning Platforms for Safety Training
AI-powered learning platforms tailor safety education to each employee. These LMS systems adjust content based on the learner’s role, skill level, and performance. For instance, if a worker struggles with a hazard module, the AI will provide additional practice or explanations. The result is a personalized learning path that ensures everyone masters critical safety topics. Such platforms also track completion of compliance requirements automatically. By using AI and AR/VR technologies, training becomes more interactive and efficient. Companies using adaptive platforms report higher engagement and better retention of safety protocols. Ultimately, these tools help embed a stronger safety culture by making training more relevant and easier for each worker.
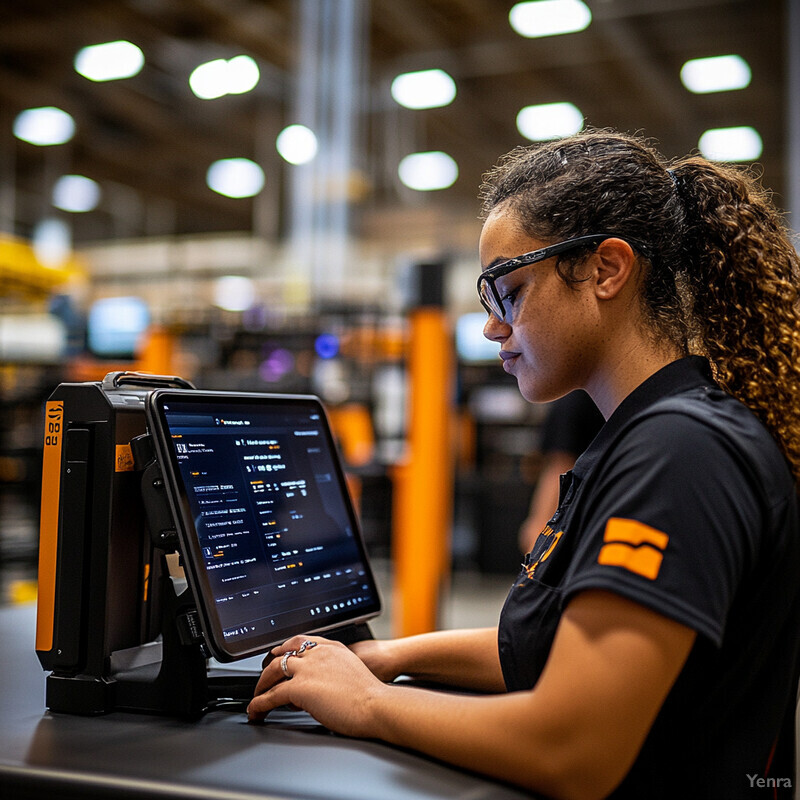
Industry reviews note that modern learning management systems increasingly incorporate adaptive learning and compliance tracking features. For example, an OHS Online article observes: “some LMS systems…integrate adaptive learning tools…assist with individual learning and reporting on OSHA requirements”. These adaptive LMS tailor lessons to an employee’s knowledge gaps, and automatically log OSHA-mandated training tasks. The article predicts that as AI, AR, and LMS converge, specialized training tailored to employer and employee needs will become widespread. Although peer-reviewed studies on AI tutoring for safety are still emerging, available evidence suggests these systems can fine-tune training content in real time, leading to measurable gains in learner comprehension and compliance adherence.
15. Decision Support for OHS Managers
AI-driven decision-support tools help safety managers interpret complex data and choose optimal safety strategies. These systems combine inputs (incident rates, compliance records, sensor alerts) to generate risk scores or recommendations (e.g., which area needs attention this week). For instance, an AI dashboard might highlight that a certain task has an elevated accident probability, prompting preemptive training. By quantifying risks and simulating outcomes, AI aids in allocating resources (training budget, inspections) where they can prevent the most harm. These tools also produce visualizations and predictive trends for easier planning. In short, AI augments managerial judgment with data-driven forecasts, enabling smarter, evidence-based safety decisions.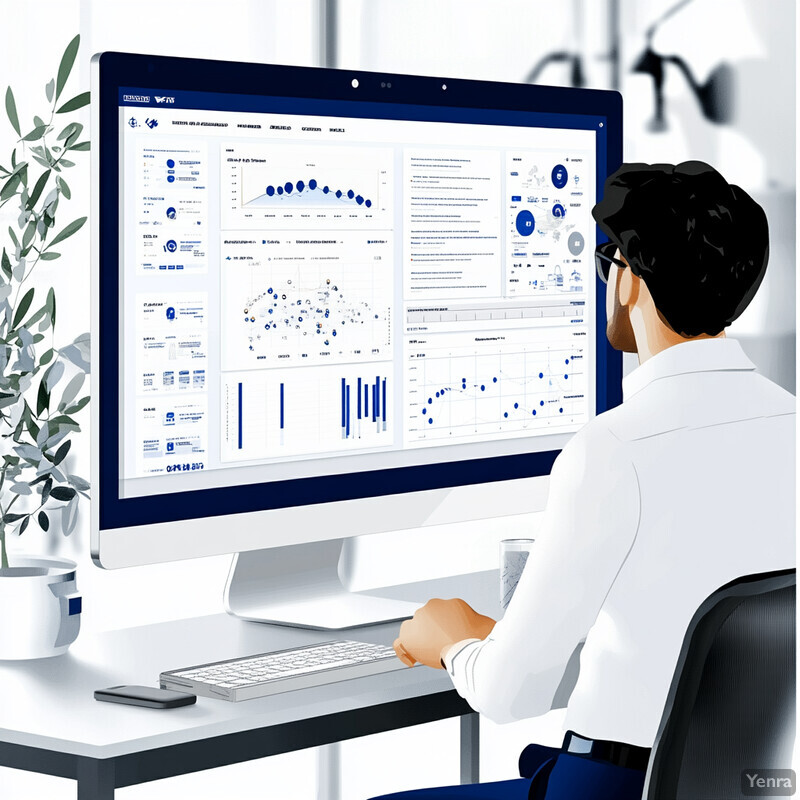
Reviews emphasize that AI can significantly support OHS decision-making. One narrative review states that AI’s proactive risk identification “supports OHS professionals in optimizing resources and tailoring safety measures”. In practice, this means the AI highlights high-risk tasks or locations so that managers can focus their limited safety resources effectively. While large-scale studies in workplace safety management are still developing, related fields (like emergency operations centers) have already begun using AI to process multiple data feeds and suggest action plans. Overall, available evidence indicates AI-based decision tools can streamline safety planning and improve outcomes by ensuring that interventions target the riskiest situations.
16. Smart Personal Protective Equipment
“Smart” PPE integrates sensors and connectivity into traditional safety gear. Examples include helmets with gas detectors or heart-rate monitors, vests with location trackers, and gloves with force sensors. These devices feed real-time data into AI systems. For instance, a helmet might detect a toxic gas spike and immediately warn the wearer and trigger an evacuation alarm. Smart boots might monitor posture to prevent slips. AI can also adapt the PPE’s function (e.g. automatically tighten harness straps). By turning passive PPE into active safety systems, workers get continuous protection and alerts. This transforms PPE from a barrier into a connected safety platform, offering higher protection especially in isolated or hazardous roles.
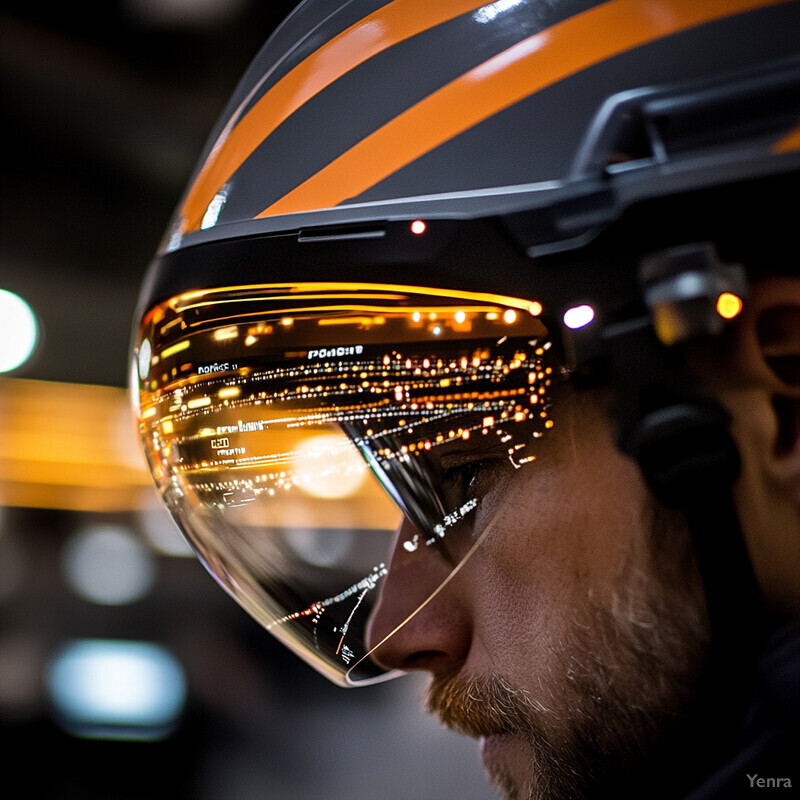
Research shows that AI-enhanced PPE provides significant safety benefits. Smart helmets with embedded AI sensors can continuously monitor for hazards (toxic gases, excessive heat) and worker status (like head impact detection) and promptly trigger alerts. Another review notes that such AI-driven gear can dynamically adapt to conditions – for example, adjusting cooling vents if a worker’s heat stress is detected. These smart PPE systems have proven to reduce response time to on-site dangers and have improved compliance by actively monitoring usage. While much of this work is in prototype stages, field tests of intelligent PPE consistently find that on-demand alerts (e.g. fall detection alarms) help prevent severe injuries by enabling rapid intervention.
17. Remote Inspection via Drones and AI
Drones combined with AI are increasingly used to inspect hard-to-reach or hazardous areas (towers, pipelines, tunnels) without endangering workers. Equipped with cameras and sensors, AI-enabled drones autonomously scan structures for cracks, leaks, or anomalies. For example, a drone can fly inside a smoke-filled building to identify hotspots, or navigate a tunnel to photograph ceiling cracks. After collecting data, AI vision algorithms immediately highlight defects. This approach replaces hazardous manual inspections (ladders, scaffolds) and often detects issues more thoroughly. Companies report that using drones speeds up inspections and improves accuracy, since AI can systematically check every component and flag even minor defects. In sum, drones + AI make safety inspections faster, safer, and more reliable.
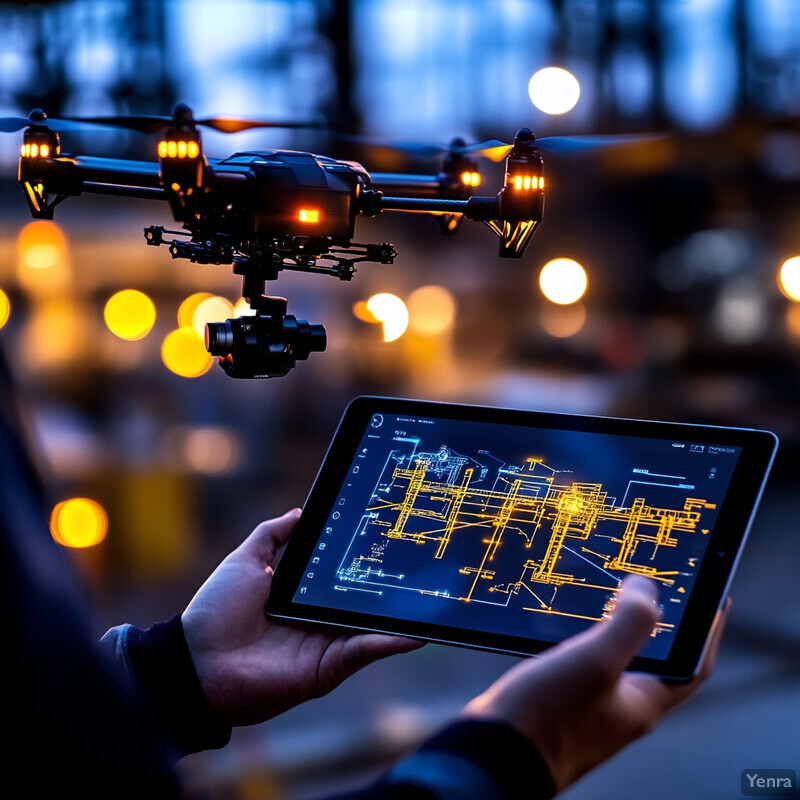
Studies and reports confirm the safety impact of AI-driven drones. One industry article highlights that drone inspections “eliminate the need for human presence in high-risk environments”. It notes that drones provide detailed surveillance and allow inspections (even in challenging terrain) without exposing workers. In research, a Korean team developed a generative-AI-powered drone for aging tunnel inspections: it autonomously navigates, captures images of concrete damage, and identifies cracks, all without any human worker in the tunnel. Field tests showed it effectively replaced manual ceiling inspections, greatly reducing worker exposure to hazards. These examples illustrate that remote AI-driven inspection tools are proven to enhance safety by keeping people out of harm’s way during critical checks.