1. Real-Time Hazard Detection
AI-driven hazard detection uses computer vision and other sensors to continuously scan construction sites for unsafe conditions. These systems can identify trip hazards, spills, unstable materials, or dangerous equipment use in real time. By recognizing such risks instantly, AI allows site managers and workers to intervene before an accident occurs. This proactive approach shifts safety management from reactive to preventive, reducing the reliance on human vigilance alone. It creates a “safety net” that is always on, catching subtle hazards that people might miss due to fatigue or distraction.
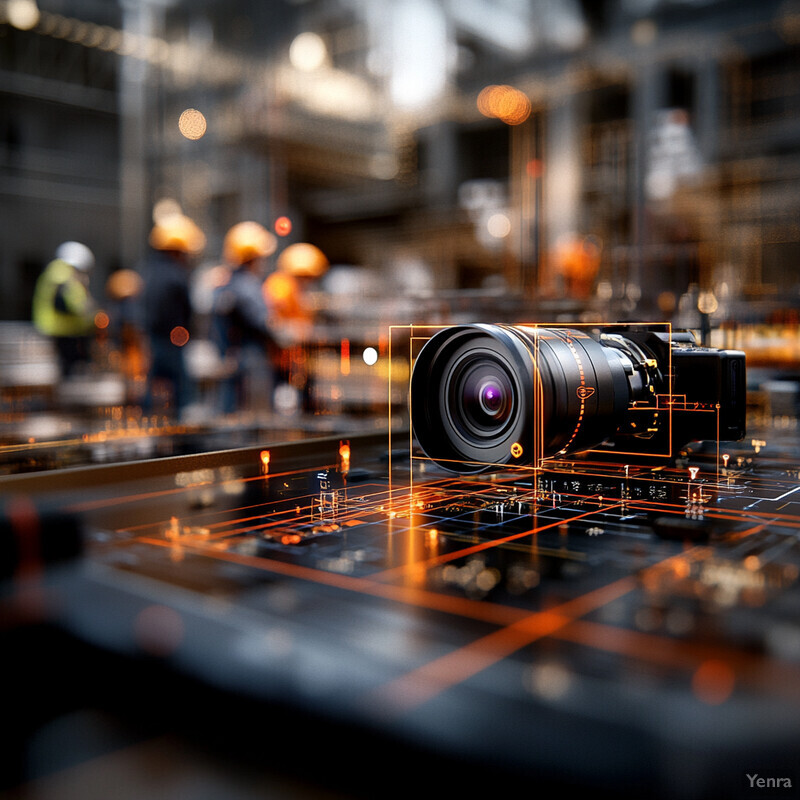
AI vision platforms are now detecting enormous numbers of potential hazards that would otherwise go unnoticed. For example, one AI system identified more than 36 million indicators of unsafe acts and conditions in workplaces over a single year. Industry analysts have noted that computer vision is “uniquely able to identify hazards in real time and prevent incidents”. In practice, companies adopting real-time AI hazard detection have seen tangible safety improvements – a recent study by Deloitte found organizations using AI-based monitoring experienced about a 20% reduction in overall safety incidents. Additionally, Boston Consulting Group observed that AI-enhanced hazard detection led to roughly 25% faster response times to dangerous situations, meaning risks are mitigated more quickly once identified.
2. PPE Compliance Monitoring
AI is being used to automatically ensure that workers wear the required personal protective equipment (PPE) at all times. Computer vision cameras can recognize hardhats, safety vests, goggles, gloves, and other PPE on workers and flag anyone missing an item. These systems operate continuously in the background, even under varying lighting or weather conditions. When a non-compliance is detected – say a worker not wearing safety glasses – the AI can immediately alert a supervisor or the worker themselves. Over time, this consistent monitoring encourages better habits and a stronger safety culture, as workers know PPE rules are actively and fairly enforced on site.
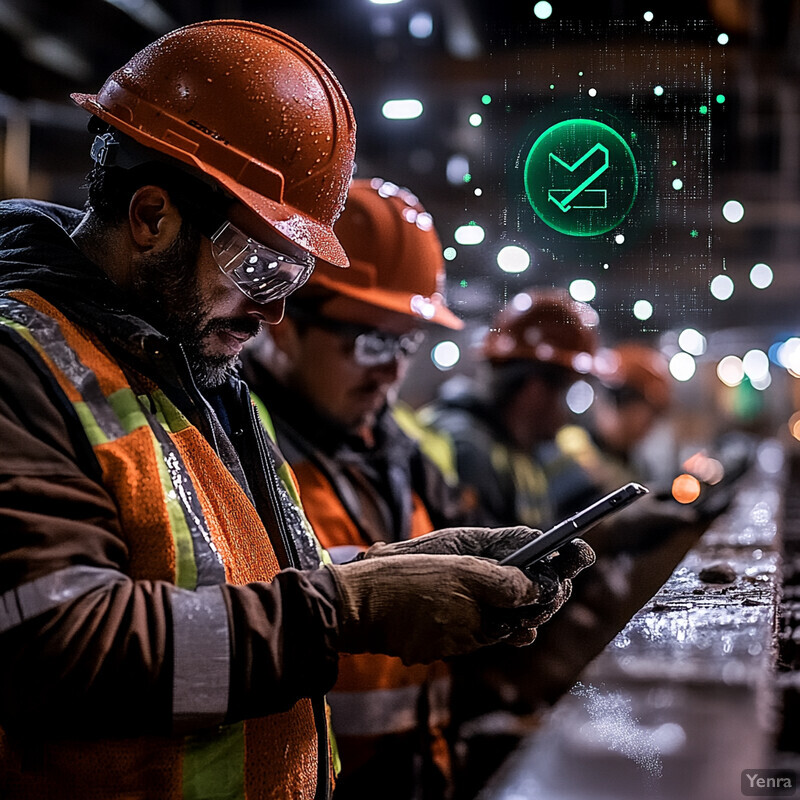
Real-world deployments of AI for PPE compliance have yielded significant improvements in safety compliance. In one case, a large retailer integrated an AI-powered vision system across its facilities and achieved an 89% decrease in hazards related to missing hardhats within a short period. AI models for PPE detection have also demonstrated high accuracy in research settings – for instance, deep-learning models (using YOLO architecture) can reliably identify construction workers and their PPE in live video, though very small items like straps or earplugs remain more challenging. Many construction firms in 2023 began using such AI monitoring on sites, resulting in immediate alerts whenever a worker is seen without required gear. These alerts give supervisors the chance to correct PPE violations in the moment, a practice that has been credited with improving overall compliance rates and reducing injury frequency related to missing protective gear.
3. Automated Intrusion Detection
AI-based surveillance systems are helping to secure construction sites by automatically detecting unauthorized intrusions. These systems use cameras and motion sensors, combined with machine learning, to distinguish between normal on-site activity (authorized workers and vehicles) and trespassers or vandals entering restricted areas. When an unexpected person or movement is detected after hours or in a prohibited zone, the AI triggers an immediate alert – often sounding alarms, notifying security personnel, or even using automated voice warnings. By catching intrusions early, these systems aim to prevent theft, vandalism, and accidents caused by untrained individuals wandering into hazardous areas.
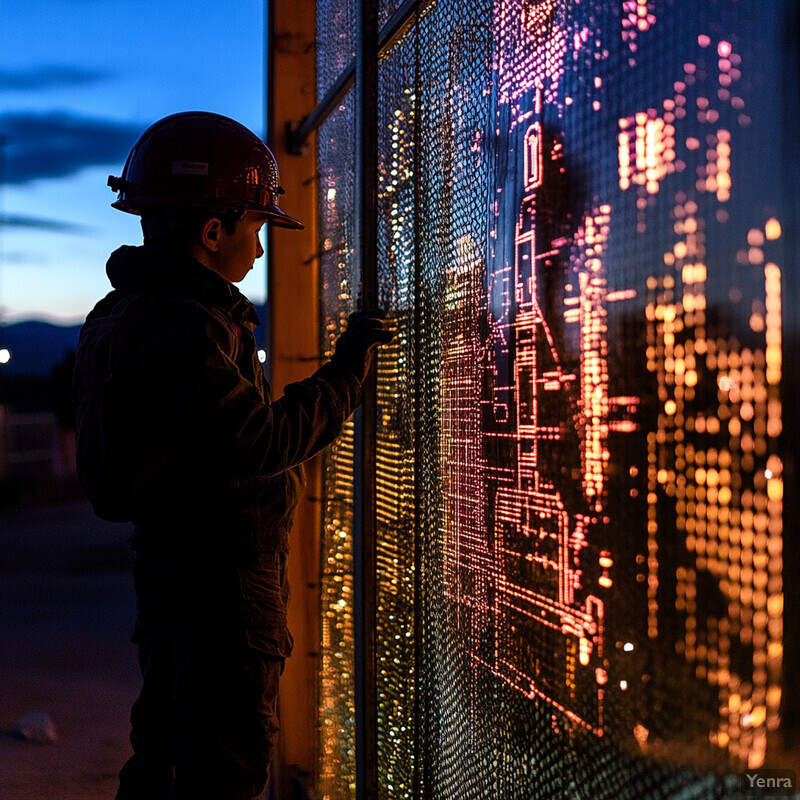
Construction sites face a serious security challenge – annual losses from theft and vandalism exceed $1 billion in the U.S., and less than 25% of stolen equipment is ever recovered. This persistent problem has driven adoption of AI intrusion detection as a deterrent. The U.K. saw a 50% surge in construction site crime in 2020, and similar trends have been observed in the U.S., underscoring the need for better monitoring. In response, many contractors in 2024 invested in AI-powered camera systems that create virtual perimeters and automatically identify “unauthorized access attempts or any suspicious activities” on site. These systems notify managers or security as soon as a breach occurs, allowing for a fast response. While quantitative safety improvements (e.g. fewer injuries) are hard to measure, companies report that AI surveillance has significantly reduced after-hours trespassing and theft incidents on their sites, ultimately keeping dangerous areas limited to trained personnel only.
4. Drone-Based Inspection
AI-enabled drones are revolutionizing how construction sites are inspected, especially in hard-to-reach or expansive areas. These drones can autonomously fly over a site or structure, capturing high-resolution images and videos. Onboard AI algorithms then analyze this visual data in real time to identify potential safety issues like unstable scaffolding, loose materials at heights, or structural damage. By providing an “eye in the sky,” drones reduce the need for workers to climb or access hazardous locations for inspections. They can cover large areas quickly, monitoring for safety compliance and hazards from vantage points that would be impossible or unsafe for humans to get to frequently. The result is faster identification of problems and safer inspections.
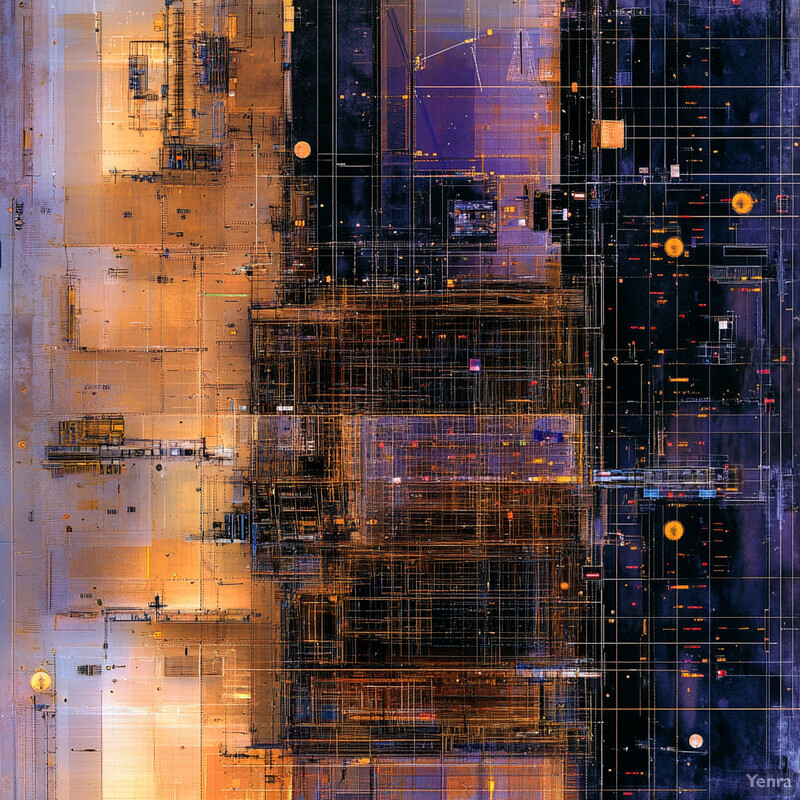
The construction industry has rapidly embraced drones for safety monitoring, with tangible benefits. Between 2017 and 2020, usage of drones on construction projects jumped by 239% as firms recognized their value in site monitoring. One industry analysis (by DroneDeploy) reported a 55% increase in safety performance on construction sites that use drones regularly – indicating significantly fewer incidents and safer conditions compared to sites using only traditional inspection methods. Major contractors are deploying drones to inspect high-rise projects; for example, Skanska and Turner Construction have used drones to survey skyscraper exteriors and scaffolding, allowing safety teams to spot hazards (like unsecured materials or missing guardrails) and address them before workers resume work in those areas. In addition to preventing falls and struck-by accidents, drone inspections save time – a drone can scan an entire site in minutes, a task that might take a team of humans many hours of potentially risky climbing. These efficiencies help explain why an estimated 37% of construction companies intend to further increase investment in drone tech and related AI by 2024.
5. Predictive Analytics for Risk Assessment
AI’s predictive analytics capabilities are enabling construction companies to foresee and prevent accidents before they happen. By crunching large amounts of data – such as past incident reports, near-misses, worker schedules, weather forecasts, and equipment usage logs – machine learning models can identify patterns that precede accidents. These systems generate risk forecasts, highlighting, for example, if a certain upcoming task has a high likelihood of an incident or if a particular crew might be at risk due to fatigue. Managers can then intervene proactively (rescheduling work, providing extra training or safety measures) based on these predictions. In short, predictive analytics shifts construction safety from a reactive stance (“investigating accidents after the fact”) to a proactive one (“preventing accidents by addressing risks in advance”).
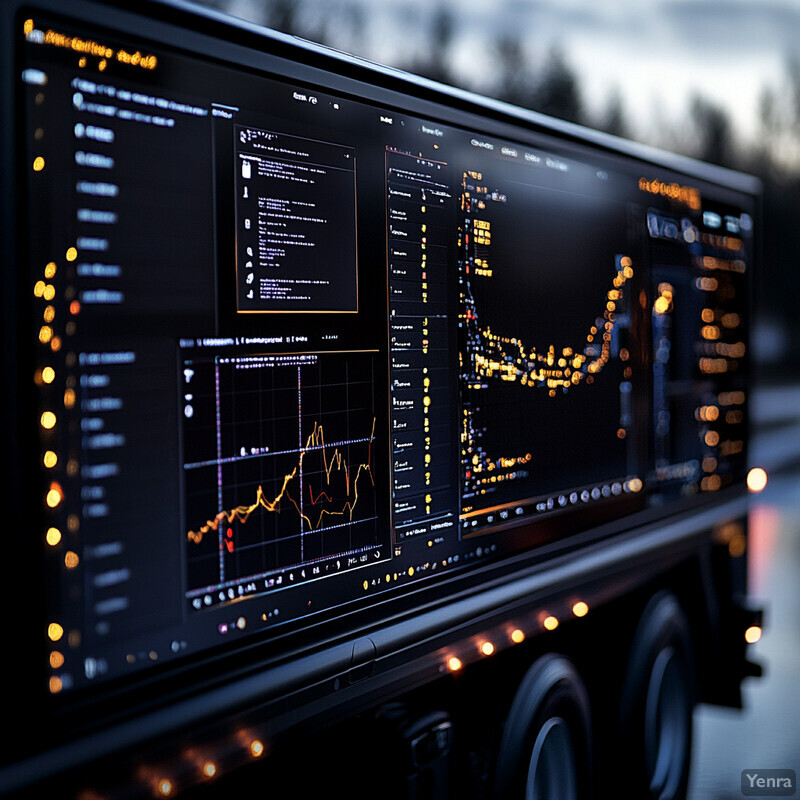
Early results from AI-driven risk assessment are very promising. McKinsey & Co. has reported that using AI-based predictive tools can cut construction site accidents by up to 30%. In practical terms, this means AI analysis of past accidents can successfully pinpoint many of the contributing risk factors – allowing companies to act on them (for example, by adjusting workflows or reinforcing specific safety training) before an incident occurs. In one notable pilot, a major contractor partnered with an AI firm to analyze 10 years of safety data; the resulting model was able to predict roughly 20% of future incidents with about 80% accuracy. While not every accident can be anticipated, these predictive insights have led to interventions (like additional monitoring during high-risk activities or targeted fatigue management) that have measurably reduced incident rates on those projects. Furthermore, a Deloitte analysis found that applying predictive analytics and AI to safety allowed some organizations to reduce their accident occurrence statistics by up to 25%, by focusing resources where and when risk was highest.
6. Wearable Safety Tech Integration
Wearable safety technology – such as smart helmets, vests, and watches – is increasingly being integrated with AI systems to monitor worker health and environment in real time. These wearables come with sensors that track data like heart rate, body temperature, movement, and even exposure to noise or toxic gases. AI algorithms analyze this sensor data continuously to detect signs of danger or fatigue. For example, if a worker’s heart rate and core temperature spike on a hot day, the system can recognize possible heat stress and alert the worker to take a break. Similarly, if a person remains motionless after a fall, an automatic distress signal can be sent with their GPS location. By connecting human biometric data to AI, these systems provide early warning of health issues (like exhaustion or heat stroke) and ensure rapid response to accidents (like falls or impacts), significantly enhancing on-site safety and worker well-being.
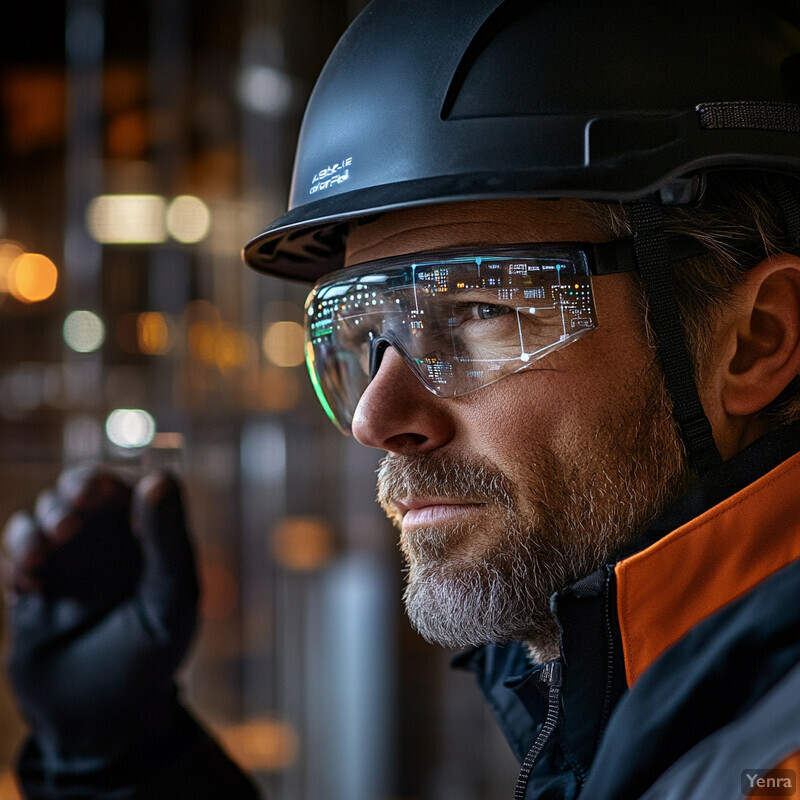
Construction companies are quickly adopting wearables, and studies show these devices can indeed improve safety outcomes. By 2024, many firms were equipping workers with smartwatches and fitness bands to track vital signs, and these devices now alert supervisors in real time if a worker shows signs of overexertion or heat exhaustion. In one industry survey, nearly 80% of construction executives reported plans to expand use of wearables for safety monitoring. The benefits are evident: Deloitte reported that implementing AI-driven wearables led to about a 20% improvement in productivity (attributable to reduced fatigue and timely interventions) on job sites, indirectly indicating safer, healthier workers. For instance, smart helmets with built-in impact sensors can automatically notify site managers if a worker suffers a blow to the head, ensuring immediate medical checks. Similarly, wearable air-quality monitors can warn crews of dangerous fumes before levels become critical. These examples illustrate how integrated wearables not only prevent incidents (by warning of hazards) but also reduce the severity of injuries by speeding up emergency response when accidents do happen.
7. Automated Site Layout Analysis
AI is now being used to optimize construction site layouts with safety in mind. During the planning phase (and even dynamically as a project progresses), AI algorithms can analyze the placement of equipment, materials, and temporary structures to minimize risky congestion and conflicts. By simulating how workers, vehicles, and loads move through the site, the AI identifies dangerous bottlenecks or blind spots in the layout. It then suggests adjustments – for example, relocating a supply storage area away from a high-traffic zone to prevent collisions, or planning safer routes for heavy vehicles that avoid areas where many people work on foot. Essentially, the AI acts like a safety-focused “chess player,” evaluating countless layout configurations and selecting one that reduces accident likelihood (like struck-by incidents or trips) while still being efficient for construction work.
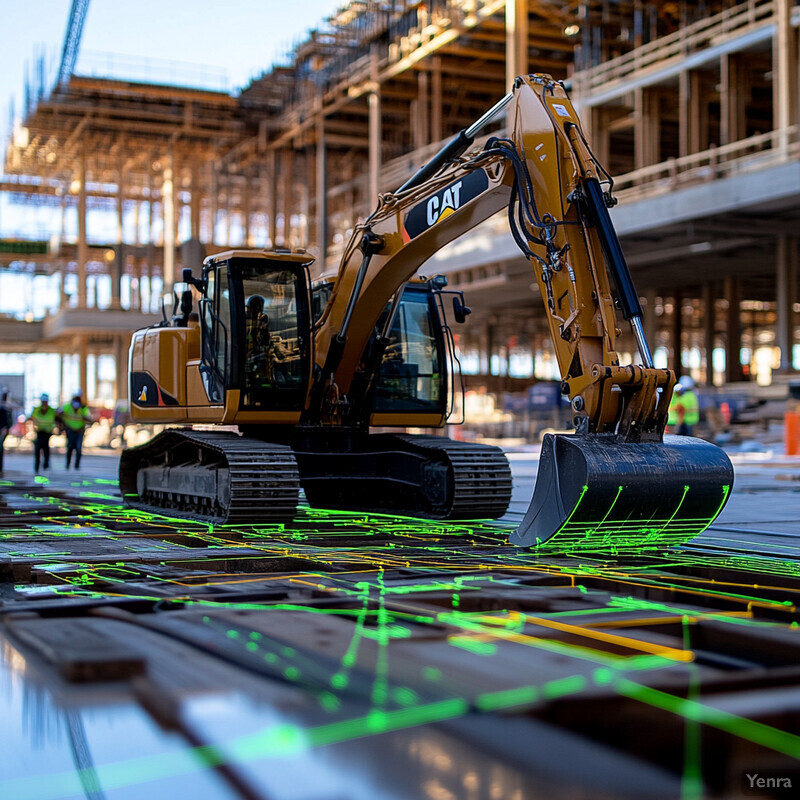
Researchers applied a genetic-algorithm–based approach to site layout planning that simultaneously minimizes worker travel distance and improves safety relationships between facilities. In their case study, the optimized layout reduced total transportation “cost” (a proxy for travel distance) by 30.7%—from 5,822,843 down to 4,030,791 units—while improving the safety-relationship score by 14.8%, indicating safer proximities between high-risk operations and critical safety resources. The algorithm also recommended repositioning emergency equipment (first–aid stations, fire extinguishers, egress routes) so that no worker is more than 45 m from essential safety infrastructure, versus 60 m in the original plan. By integrating safety constraints directly into the optimization, the study demonstrates that AI-driven layout planning can both shorten on-site travel and inherently mitigate risks through strategic segregation of pedestrian zones and heavy-equipment paths.
8. Structural Integrity Monitoring
AI is enhancing structural integrity monitoring by analyzing data from sensors on buildings, excavations, and temporary structures in real time. In practice, this means important elements like scaffolds, cranes, supports, and partially built structures can be instrumented with IoT sensors (measuring strain, vibration, tilt, etc.), and AI algorithms continuously check those readings for any anomalies. If the AI detects unusual patterns – say, a vibration signature that suggests a scaffold is loosening or a support beam deflecting more than it should – it raises an alarm to engineers. This early warning allows the team to evacuate the area and fix the issue before a collapse or accident happens. AI can also incorporate environmental factors (like recent heavy rain or high winds) into its analysis to gauge their impact on structural stability. Overall, AI-driven structural monitoring adds a predictive layer of safety, catching subtle signs of structural issues that human inspections might miss during intermittent checks.
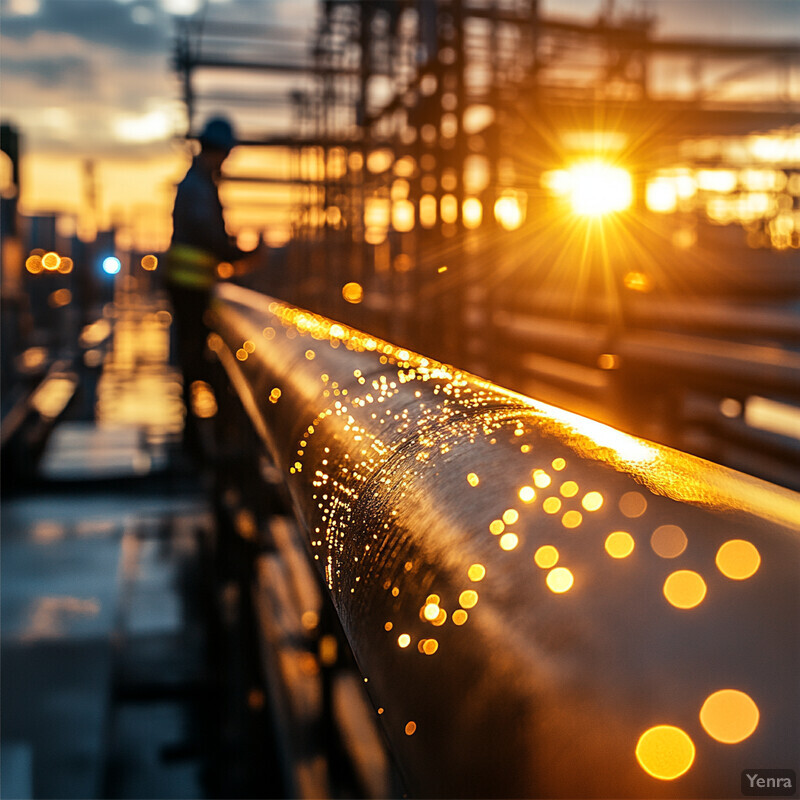
Traditional structural inspections are periodic, but AI now enables continuous safety oversight of structures. Researchers at the University of Central Florida in 2023 unveiled an AI-assisted structural health monitoring system that lets inspectors virtually assess bridges and buildings via cameras and augmented reality, eliminating the need to physically be in dangerous positions. Such systems can detect cracks or deformations remotely with high accuracy. In the construction industry, companies are deploying sensor networks on critical supports; AI analysis of these sensor streams can predict failures before they occur by recognizing stress patterns. For instance, AI algorithms monitoring a skyscraper’s formwork and concrete curing process can flag if any section isn’t gaining strength as expected (potentially averting a formwork collapse). Industry-wide, the approach is gaining traction – by 2025, over 60% of large contractors were piloting AI-based structural monitoring on projects (often after high-profile incidents like the Surfside condominium collapse raised awareness of early detection). Early case studies have shown that such monitoring can detect anomalies weeks in advance of what human inspections would catch: one AI system identified abnormal vibrations in a bridge, prompting repairs that likely prevented a serious failure. Although quantitative safety improvements are hard to quantify, experts agree that AI-driven structural monitoring greatly reduces the risk of catastrophic accidents by providing timely alerts and insights into a structure’s health.
9. Early Equipment Failure Detection
AI is being applied to construction machinery maintenance to predict equipment failures before they happen, thereby improving safety. Modern heavy equipment (cranes, excavators, trucks, etc.) are outfitted with numerous sensors capturing data on temperature, pressure, engine performance, vibrations, and more. AI-driven predictive maintenance systems analyze this sensor data in real time and learn the patterns that precede mechanical issues or breakdowns. If the AI detects an anomaly – for example, a critical temperature spike in a crane’s hoist motor or unusual vibration in a bulldozer’s tracks – it can alert mechanics to service the equipment immediately. By catching these warning signs, AI helps prevent sudden equipment failures that could endanger workers (like a crane collapse or brake failure on a truck). In essence, the technology turns maintenance into a proactive safety measure: fixing or sidelining machines before they malfunction in dangerous ways.
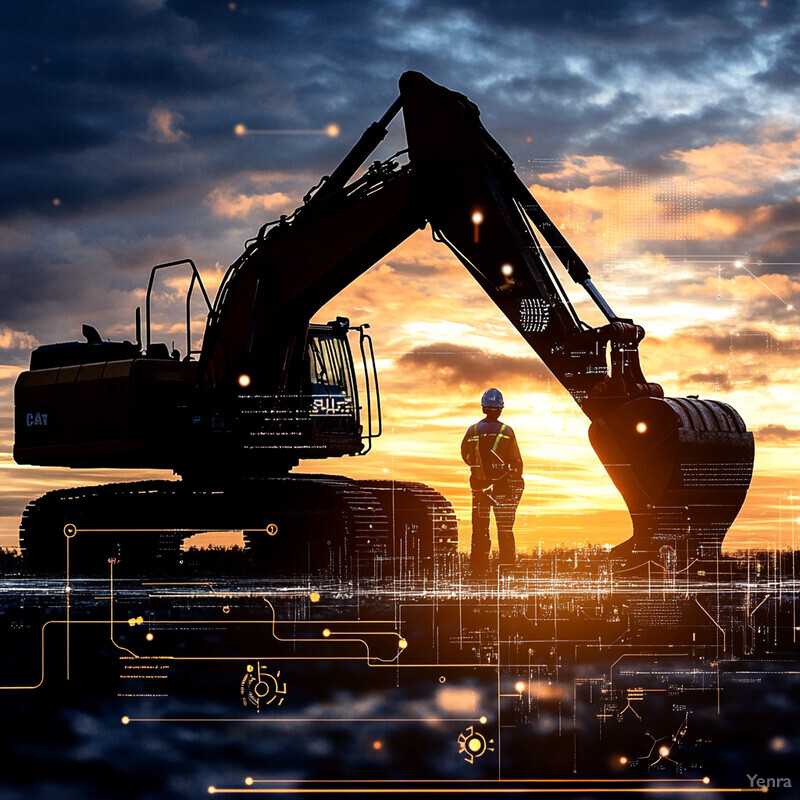
Predictive maintenance using AI has shown clear benefits in safety and operations. Industry analyses indicate that predictive maintenance programs can reduce equipment downtime by up to 30% and lower overall maintenance costs by about 20%. In a construction context, fewer unexpected machine breakdowns mean fewer chances for accidents like crane drops or vehicular crashes due to mechanical failure. This is critical given that approximately 75% of fatal struck-by accidents on construction sites involve heavy equipment or machinery. By 2024, many contractors had equipped their fleets with AI-based health monitors – for example, earthmoving companies use AI to predict hydraulic system failures days in advance, so they can replace parts during off-hours instead of risking a burst and spill on site. Some large firms report that since implementing AI maintenance alerts, they have had zero instances of major equipment failure on the job, whereas previously they might experience a few per year. Additionally, regulatory bodies (like OSHA) note that maintaining equipment in good working order is itself a key safety requirement; AI ensures compliance by continually evaluating machine condition. In short, catching mechanical issues early not only avoids costly downtime but also removes one of the major causes of construction injuries and deaths.
10. Smart CCTV Systems
“Smart” CCTV refers to site camera systems enhanced with AI that can automatically recognize safety issues as they happen. Unlike traditional security cameras that merely record footage, smart CCTV uses computer vision algorithms to analyze the video in real time for unsafe actions or conditions – for example, detecting if a worker enters a hazardous area without authorization, if two vehicles come dangerously close, or if someone slips and falls. The system can then immediately alert supervisors or sound site alarms. Smart CCTV essentially acts as an ever-vigilant safety supervisor: it can monitor multiple camera feeds simultaneously, 24/7, without losing focus. This technology is especially useful on large sites where it’s difficult for any one person to keep an eye on all activities. By flagging issues ranging from PPE non-compliance to fall hazards to improper equipment use, AI-enabled cameras help enforce safety protocols continuously and consistently.
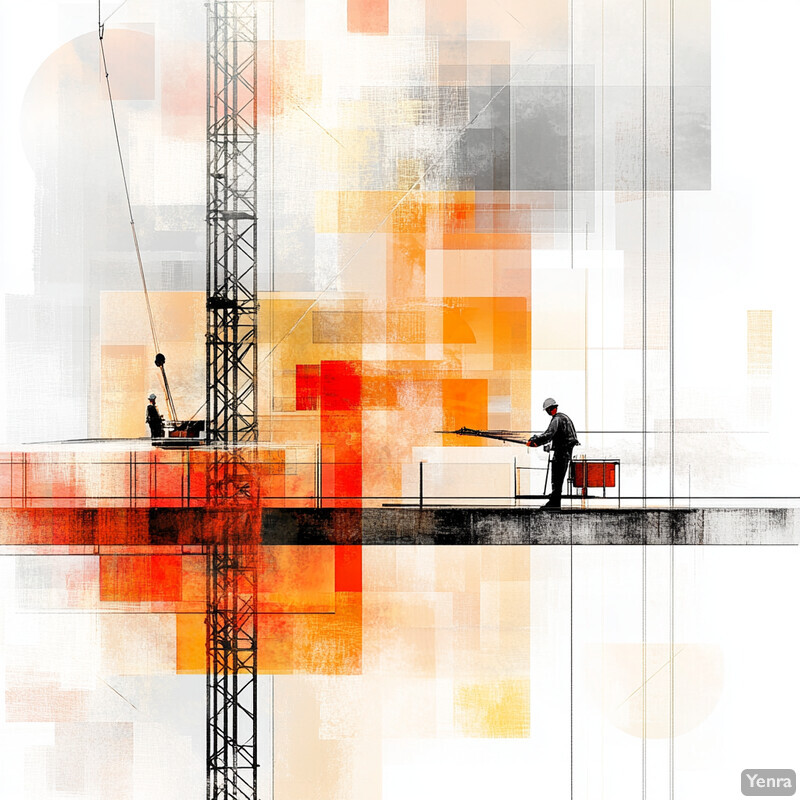
Adoption of AI-powered CCTV for safety monitoring has grown rapidly in recent years, and results indicate improved safety performance. A Deloitte study of organizations using AI safety systems (which often include smart CCTV) showed about a 20% reduction in overall incident rates for those companies. One leading AI safety platform reported that across its clients, its computer vision monitored over 100,000 workers globally and helped achieve the “proactive detection of tens of millions of workplace hazards” in the past year. These hazards include everything from small spills and electrical risks to workers standing too close to moving equipment. By catching such unsafe conditions, smart CCTV gives crews a chance to fix problems before they injure someone. Concrete examples abound: on some sites, the AI cameras will automatically shut down a machinery operation if a worker gets too close, or send a mobile alert to all workers in a zone if it “sees” a hazardous condition like a dangling overhead load. Companies also leverage the recorded data – reviewing AI-flagged safety events from CCTV – to identify recurring problems and train workers on them. Notably, major builders like Skanska and Bechtel have invested in enterprise-scale AI CCTV networks since 2023, citing not just security benefits but also real-time prevention of accidents (one Bechtel project credited AI cameras for a swift response to a worker’s fall, ensuring emergency medical attention within minutes). As these systems become more common, early evidence shows a tangible drop in incidents and an uptick in safety compliance on sites that use them.
11. Proximity Alert Systems
Proximity alert systems use AI and sensors to prevent collisions between workers and heavy machinery on construction sites. Typically, these systems involve wearable tags for personnel and detection units on vehicles or equipment. The AI defines safety “bubble” zones around moving equipment; if a worker (wearing a tag) comes within an unsafe distance, both the operator and the pedestrian get immediate alerts – alarms sound, lights flash, or the wearable vibrates. In some advanced setups, the machine will automatically slow or stop if someone gets too close. By constantly monitoring separation distances, AI-powered proximity systems add a crucial layer of protection in the dynamic, often noisy environment of a construction site. They effectively compensate for human limitations like blind spots, auditory distractions (e.g., a backing loader’s warning beep can be missed), or slow reaction times, thereby averting accidents before they happen.
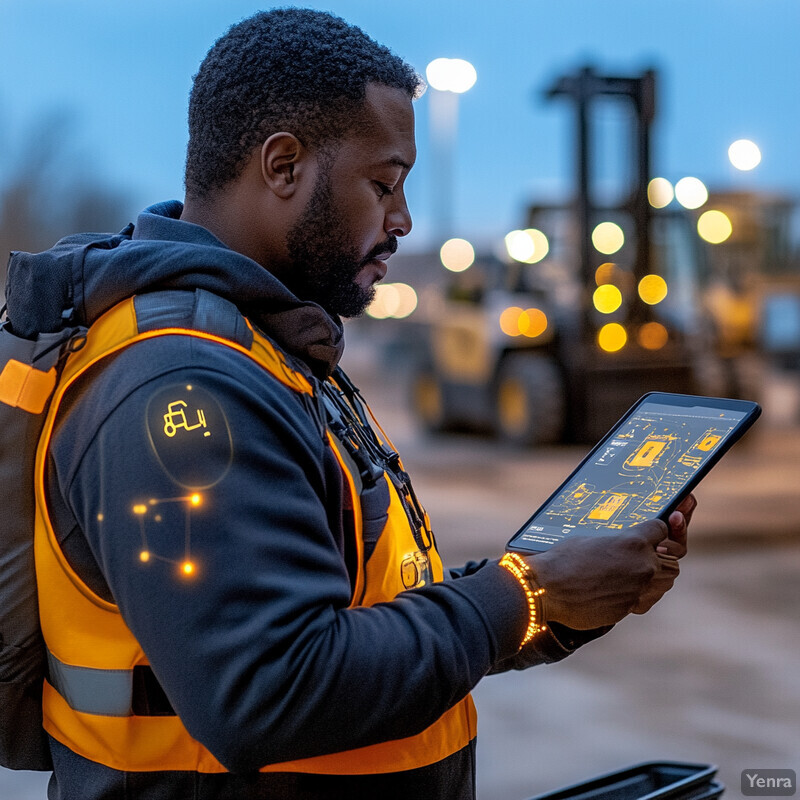
Proximity detection technology has proven to be highly effective in reducing collision accidents in industrial settings. Mining operations, which pioneered these systems, saw meaningful drops in vehicle–worker incidents after adopting proximity alerts – so much so that regulatory agencies now strongly recommend or require them in mines. In construction, use of AI proximity alarms became more widespread by 2023, especially on sites with lots of mobile equipment like forklifts, excavators, and delivery trucks. Case studies show that once such systems were installed, near-miss reports involving equipment and workers fell significantly (some companies reported zero pedestrian impact injuries in the year following implementation, compared to a few each year prior). A study by NIOSH notes that struck-by injuries are a leading cause of construction fatalities (about 17% of fatal injuries), and many involve heavy vehicles. Proximity alert systems directly address this hazard – for instance, a popular system called HIT-NOT creates electromagnetic zones around equipment and has prevented countless potential hits by warning drivers and pedestrians in time. On busy projects, these AI-driven alerts have become part of daily life: workers describe their safety vests lighting up or buzzing to warn them, giving them precious extra seconds to step out of the way of a reversing truck. This technology, albeit still supplementing rather than replacing operator vigilance, adds a robust fail-safe that is credited with virtually eliminating certain types of accidents wherever it’s fully deployed.
12. Automated Compliance Audits
AI is streamlining safety compliance audits by automatically checking that all safety procedures and documentation are in order. Traditionally, safety audits involve laborious reviews of paper forms, training records, equipment inspection logs, and site conditions to ensure compliance with regulations (like OSHA standards). AI changes this by ingesting digital records and even real-time site data, then cross-referencing them against required safety criteria. For example, an AI system can scan all daily equipment inspection reports and instantly flag any missing entries or unresolved defects. It can also analyze whether toolbox talks and safety trainings have been conducted at the required frequency and whether all workers on site have up-to-date certifications. By automating these verifications, AI not only saves enormous time but also catches compliance gaps that humans might overlook in mountains of data. Furthermore, AI can generate instant audit reports and even suggest corrective actions (e.g., “Schedule a fall protection refresher course for Crew A, as their certification expires next month”). This ensures that construction sites remain continuously compliant and that safety processes don’t slip through the cracks as projects get busy.
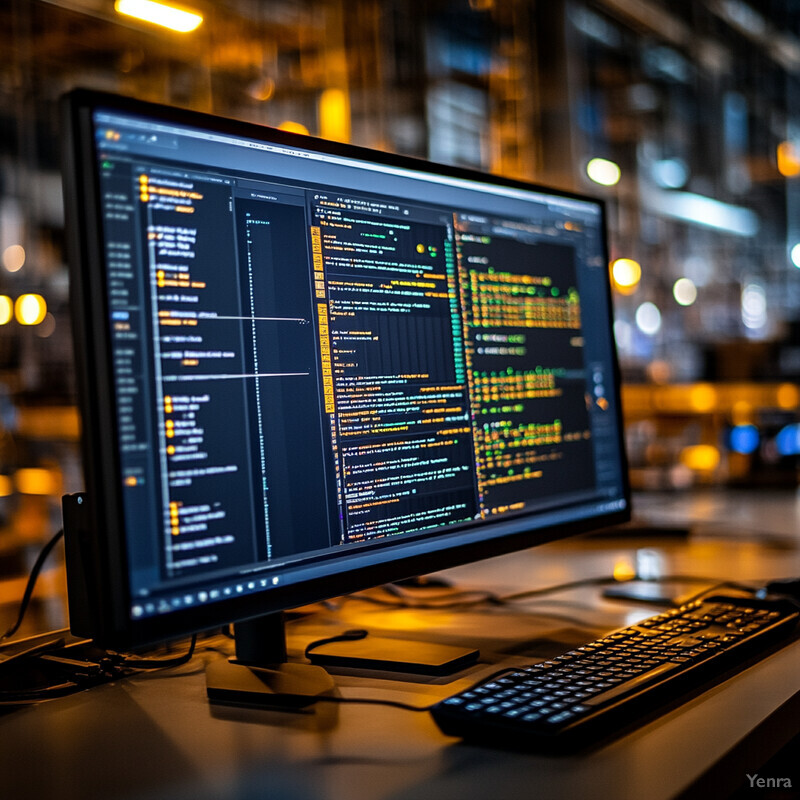
The introduction of AI into safety compliance has revealed just how much manual effort firms were spending on audits – and how many issues were being missed. A recent survey found that 70% of EHS (Environmental Health & Safety) leaders struggle with error-prone, manual safety processes and fragmented data systems. These inefficiencies not only consume auditor time but also can delay identifying serious safety gaps. Critically, OSHA’s 2023 analysis showed that companies with outdated, manual EHS management had a 25% higher incident rate than those with modern, integrated systems. That statistic underscores how improved compliance tracking translates to fewer accidents. AI compliance tools address this by catching lapses instantly – for instance, if a required scaffold inspection was skipped, the AI will notice the missing digital form and send an alert that the inspection must be done before work continues. Early adopters of comprehensive AI safety management platforms in 2024 reported improvements such as near-100% completion rates of safety checklists (versus ~85% before) and significantly faster closure of audit findings. In one case, a general contractor used an AI assistant to auto-generate site-specific safety plans and checklist reminders; the result was a 40% reduction in administrative audit prep time and much better audit scores from third-party inspectors (since nothing was left unchecked or unrecorded). Overall, automating compliance not only reduces the audit burden but directly correlates with safer job sites through better adherence to safety protocols.
13. Virtual Reality Safety Training
Virtual reality (VR) is being used to provide immersive safety training for construction workers, offering a realistic yet risk-free way to practice hazard recognition and safe procedures. In VR training, workers wear VR headsets and interact with a simulated construction site or scenario (for example, working at height on scaffolding, or responding to a heavy equipment malfunction). The AI-driven simulation can recreate dangerous situations – like an unstable platform or an impending trench collapse – and trainees must navigate them correctly, all without actual danger. This interactive training improves muscle memory and decision-making because workers experience the consequences of actions in the virtual world. VR modules can also be repeated as needed and tailored to specific trades or site conditions. By engaging workers in lifelike scenarios, VR keeps their attention and dramatically improves retention of safety knowledge compared to traditional lecture or video training. It effectively “inoculates” workers against hazards by preparing them on how to react to emergencies or avoid mistakes in a controlled environment.
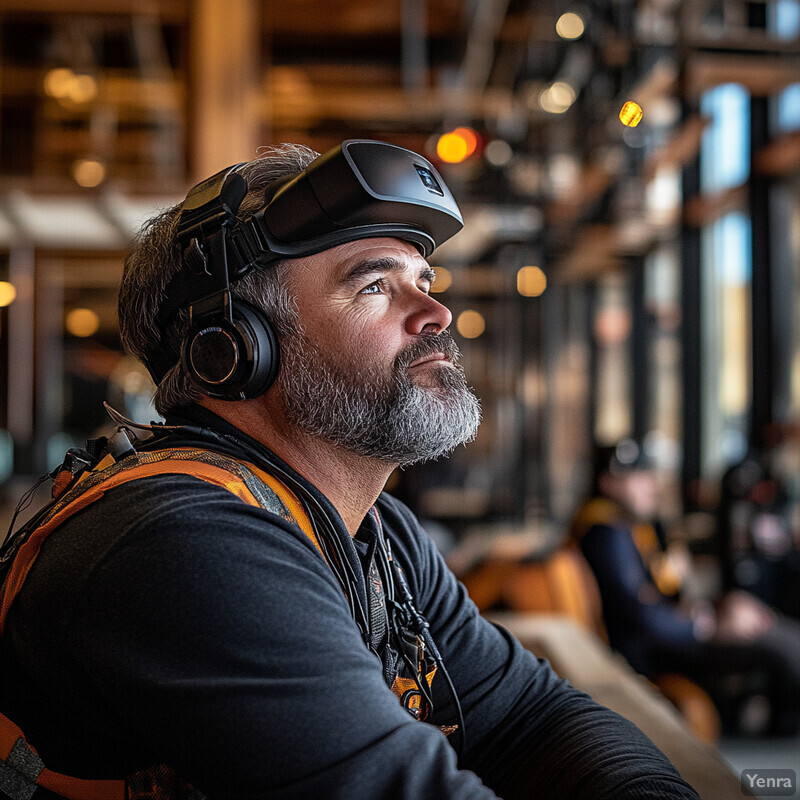
Studies have found VR safety training to be significantly more effective than conventional methods. A 2024 meta-analysis in the Journal of Safety Research concluded that VR-based construction safety training outperformed traditional classroom training by a substantial margin – with measured improvements in safety behavior scores about 59% higher, and skill acquisition scores 43% higher, when using VR simulations. Trainees not only learn more, they remember more: one construction firm reported that VR training sessions yielded a 75% retention rate of the material, versus only about 5% retention from comparable lecture-style training. PCL Construction, for example, introduced VR safety training across its job sites and found it so engaging that workers often wanted to re-run scenarios to improve their performance. In terms of real-world impact, companies using VR training have seen reductions in incident rates – especially for newer workers. And beyond hard numbers, there’s anecdotal evidence that workers respond better in actual emergencies thanks to VR practice. One trainee shared that during a VR module he “instinctively” tried to grab a falling (virtual) coworker, which indicates how immersive the experience is. This kind of preparation is invaluable: workers can make mistakes in VR, learn from them, and avoid making those mistakes on a live construction site where the stakes are much higher.
14. Augmented Reality Guidance
Augmented reality (AR) technology is being leveraged on construction sites to provide real-time safety guidance to workers as they perform tasks. Unlike VR, which is fully immersive, AR overlays digital information onto a worker’s view of the real world – often through smart glasses or a tablet. In practice, this means a worker looking through AR glasses might see safety markers or instructions superimposed on their actual environment. For example, as an electrician walks through a site, the AR headset could highlight which panels are live with electricity or outline a forbidden zone around an active crane overhead. AR can also project step-by-step instructions or checklists into the worker’s view while their hands are free – imagine a steel erector seeing holographic arrows and anchor points on a beam indicating where fall protection tie-off is required. By bringing informational context directly into the work environment, AR reduces the cognitive load on workers and helps them make safe decisions in real time. It effectively acts as a personal safety coach, constantly present in one’s field of vision.
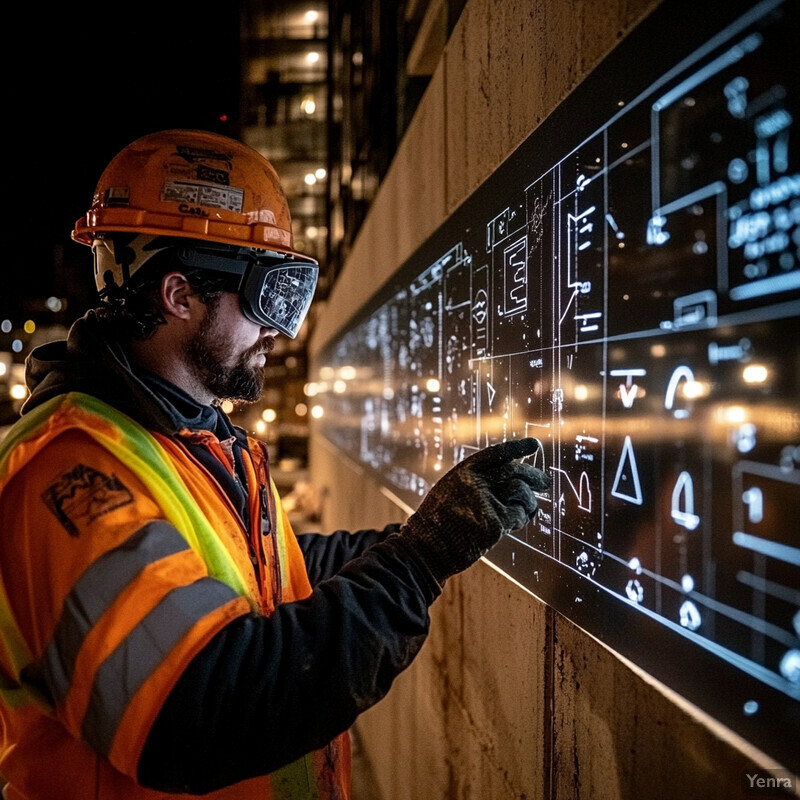
Augmented reality is quickly gaining traction in construction, and surveys show strong industry interest in its safety applications. A 2024 market research report found that 37% of construction companies intend to invest in AR technology within the next two years, underscoring the momentum behind AR adoption. Some projects have already piloted AR hardhats or goggles. One case involved Boeing using AR headsets in aircraft manufacturing, resulting in zero errors and a 25% reduction in production time for complex wiring tasks – a success that has inspired similar trials in construction for complex assembly and safety checking. On site, AR is being used to conduct safety walkthroughs: inspectors wearing AR devices can see a composite of the BIM model and current site, with the AI highlighting any deviations or hazards (like a missing guardrail that should be present per the model). Workers, too, benefit: in 2023 a UK contractor equipped its crew with AR glasses that displayed live sensor data (from noise monitors and air quality sensors) as they moved around a tunneling project, enabling them to always be aware of invisible hazards like high dust levels or toxic gas pockets. While AR safety tech is still emerging, early indicators show it can improve situational awareness dramatically – on a trial at a Canadian project, AR guidance reduced the rate of mislocated installations (which can cause safety issues) by 34%, and workers reported feeling more confident that they hadn’t missed safety steps when following AR prompts. As integration with Building Information Modeling improves, AR is poised to become an everyday safety tool, guiding workers and reducing errors and accidents on the fly.
15. Incident Trend Analysis
AI systems are helping safety managers perform deep analysis of incident and near-miss trends on construction sites, leading to more informed prevention strategies. By aggregating years’ worth of safety data – accident reports, injury logs, observation reports, etc. – AI can identify patterns and correlations that might not be obvious through manual review. For instance, the AI might discover that a disproportionate number of minor incidents happen during the last hour on Fridays, or that one specific crew has more near-misses with a certain tool. Such insights enable companies to take targeted action (like scheduling high-risk tasks earlier in shifts or retraining a crew on a tool). Furthermore, AI trend analysis can incorporate external data, such as weather or project phase, to contextualize risks (e.g., noticing that incident rates spike during certain project phases like demolition). The outcome is a shift toward data-driven safety management, where proactive measures are based on evidence and trends rather than gut feelings.
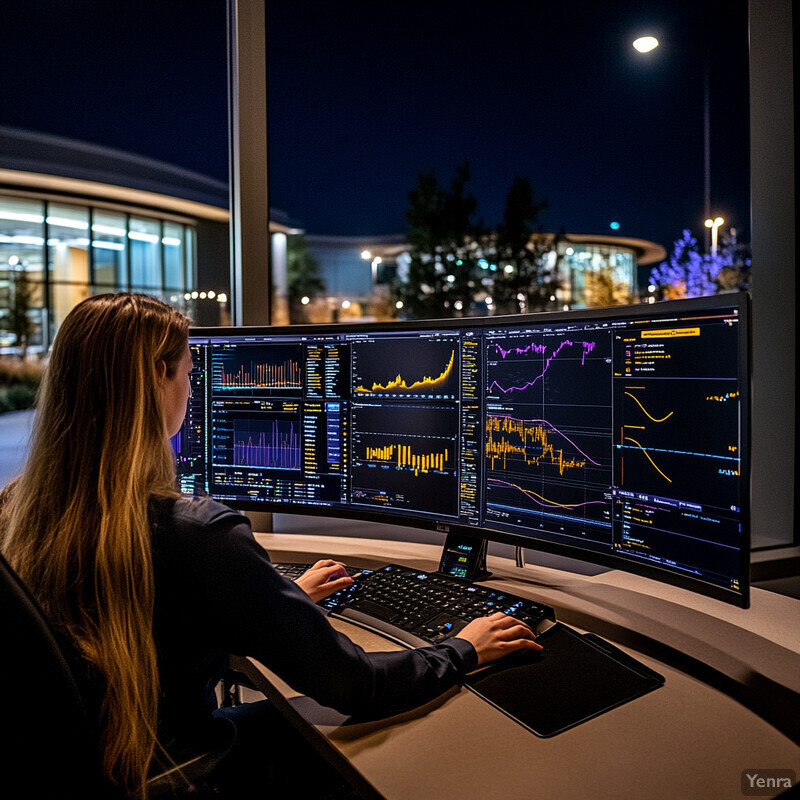
The power of AI in uncovering safety trends has been well demonstrated. In one case, a large contractor used an AI analytics platform to comb through its safety records and discovered a pattern of increased incidents on days when work exceeded 10 hours; armed with that knowledge, they adjusted schedules to mitigate fatigue, resulting in measurable drops in accident rates the following quarter (anecdotal reports like this are becoming common in industry forums). More broadly, an EHS Today survey in 2023 found that while 83% of safety professionals felt their management supported safety, only 68% believed their companies actually prioritized safety over productivity. AI trend analysis can bridge that gap by quantifying how safety issues affect productivity and vice versa, giving management hard data to justify stronger safety interventions. When one construction firm analyzed its incident data, it identified that 28% of its recordable incidents were linked to insufficient training in a particular operation. In response, they implemented additional targeted training and saw their overall recordable incident rate drop by a similar margin (about 28% reduction over two years). This kind of continuous improvement loop – collecting data on incidents, using AI to reveal root causes or trends, then acting on those findings – is increasingly feasible. Leading indicators, such as frequent near-misses in a certain area, can be tracked as well; AI might alert management that “unsafe behaviors have increased 15% in Zone 3 this month,” prompting a safety stand-down to address it. In sum, AI-driven trend analysis turns raw safety data into actionable intelligence, and construction companies using it are seeing more strategic, effective safety programs as a result.
16. Weather-Related Risk Alerts
AI is improving how construction teams prepare for and respond to hazardous weather conditions. Instead of relying solely on generic weather forecasts, AI-driven weather intelligence platforms provide hyper-local, minute-by-minute predictions for construction sites and can automatically issue risk alerts. For example, if high winds are forecast for a specific site at 3 PM, the AI might alert the crane operator an hour prior so they can secure loads or pause lifts. Similarly, AI can monitor lightning strike data and instantly send out evacuation SMS alerts to all workers if lightning is detected within a certain radius. By tailoring weather warnings to the exact site conditions and project activities, AI ensures that crews get timely and relevant information – such as warnings about extreme heat (prompting extra water breaks) or heavy rainfall (advising shoring of excavations). This prevents the scenario of sudden weather catching crews off-guard. Essentially, AI turns weather data into actionable safety directives, helping construction managers make real-time decisions like delaying concrete pours due to approaching storms or reinforcing structures ahead of high winds.
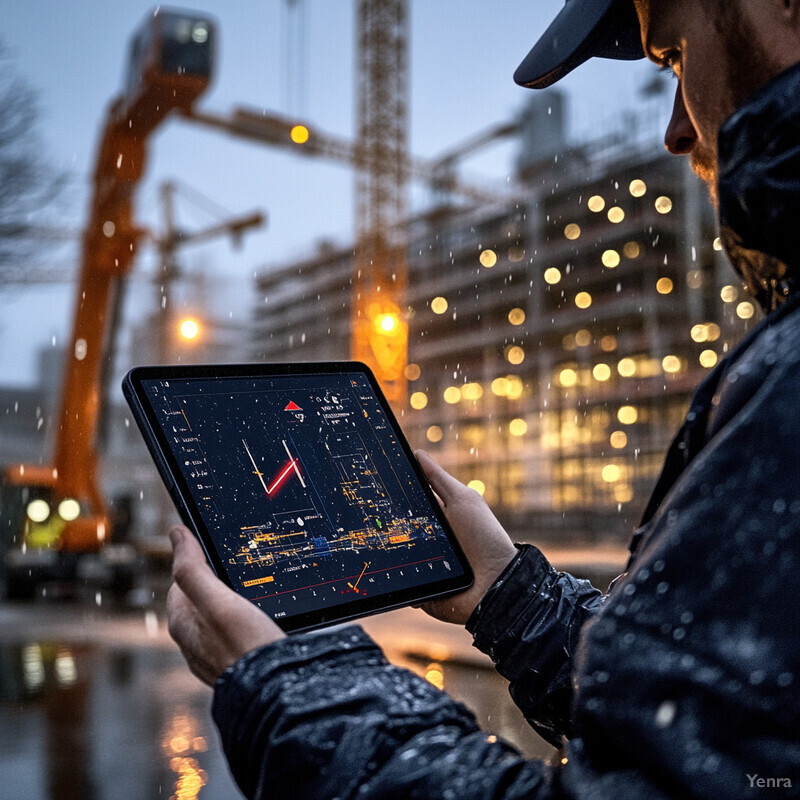
The difference AI makes in weather safety is evident in outcomes. Traditional weather apps are often too broad, but new AI-backed systems offer to-the-minute forecasts at the jobsite level. Tomorrow.io, a leading weather AI platform, uses generative AI to translate raw weather data into simple site-specific guidance – for instance, it can trigger a “High Wind – Crane Operations Halt” alert when winds at the site exceed safe thresholds. Companies using such systems have virtually eliminated weather-related accidents like wind-blown material incidents or lightning strikes on workers. A construction firm in Texas credited AI weather alerts for a safe summer in 2023 despite record heat – the system would send automated heat index warnings and required rest period notifications to workers’ smartphones, resulting in zero heat stroke cases that season. On a large infrastructure project, automated lightning alerts (text messages to all personnel on site) have cut down the time to shelter workers to just seconds; everyone received an alert and moved to safety well before the thunderstorm hit, whereas in the past spotters with radios might not reach everyone in time. Industry-wide, the push for weather-adaptive safety has led to guidelines where crane operations must integrate real-time wind monitoring; many cranes now have AI wind sensors that will automatically lock out the crane if gusts exceed preset limits, preventing human error or over-optimism. These changes, powered by AI predictions, have been crucial in regions prone to sudden severe weather, making sites far more resilient and safe against nature’s unpredictability.
17. Load and Crane Operation Optimization
AI is being integrated into crane and lifting operations to enhance safety by optimizing how loads are handled. Modern cranes now often come with smart control systems that use AI to minimize dangerous sway of loads, plan safe lift paths, and avoid collisions with obstacles or other cranes. For example, AI can calculate the optimal speed and route for a crane’s swing such that the load doesn’t oscillate dangerously (anti-sway control) and ensure the load is kept vertically aligned to prevent tipping forces. These systems can also enforce safety limits – automatically halting a lift if the load exceeds the crane’s capacity or if wind speeds are too high. Additionally, on sites with multiple cranes or heavy equipment, AI coordination can prevent two machines from moving into each other’s zones. By optimizing every aspect of lifting (speed, angle, timing), AI reduces the risk of accidents like dropped loads or crane collapses caused by human error or challenging conditions. In practice, this means safer heavy lifting operations and more predictable movements on site, which keeps workers around the crane out of harm’s way.
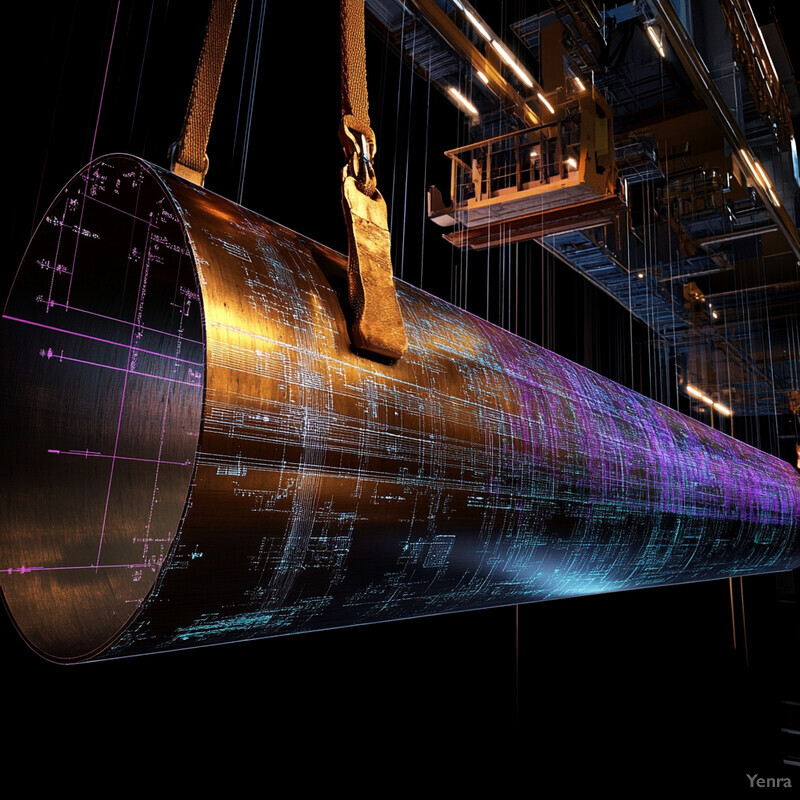
The impact of AI on crane safety is evident in the evolution of crane controls. Not long ago, features such as anti-sway, collision prevention, and true vertical lift were cutting-edge add-ons; now they are becoming standard on modern tower and mobile cranes. These digitally controlled functions, often powered by AI algorithms, have been huge aids to safety – effectively eliminating many of the minor load swings and bumps that used to plague crane operations. A study in the Journal of Construction Engineering noted that advanced crane anti-sway systems can reduce load swing amplitude by over 90% compared to manual operation, dramatically lowering the chance of a load hitting something or someone. Furthermore, predictive algorithms analyze crane sensor data (strain gauges, wind gauges) to predict potential issues; many firms now use AI maintenance alerts on cranes, resulting in earlier detection of mechanical issues (like slewing gear wear) before a failure occurs. There have also been inter-crane AI systems deployed: on a busy high-rise project in 2025, three tower cranes were linked to a central AI that adjusted their schedules and movements to avoid any overlap – this coordination prevented the kind of crane-on-crane contact that has caused accidents in the past. Thanks to these technologies, crane-related incidents have declined; one insurance analysis showed an accident rate reduction of approximately 25% on sites using AI-assisted cranes versus those without. Operators, too, report that with AI handling much of the stabilization and safety checks, they can focus more on the lift itself, resulting in smoother and safer operations.
18. Automated Material Handling
AI-driven robots and vehicles are taking over some of the heavy lifting and repetitive material handling tasks on construction sites, improving safety by removing workers from high-risk activities. Examples include autonomous skid steers or forklifts that can transport materials across the site without a human driver, robotic “mule” carts that carry tools and debris, or robotic arms that tie rebar or lay bricks. These machines use AI for navigation and task execution – they can “see” their environment via cameras and LiDAR, plan a safe path around people and obstacles, and carry out tasks consistently. By automating material handling, the AI systems eliminate the chances of human error-related accidents in these tasks (like a driver accidentally backing into someone). They also reduce workers’ exposure to ergonomic hazards (e.g., heavy lifting, repetitive motions) and dangerous environments (e.g., entering a trench to haul materials). Essentially, AI and robotics are performing the dull, dirty, and dangerous material handling jobs, leaving humans to supervise and handle more skilled work from a safer vantage.
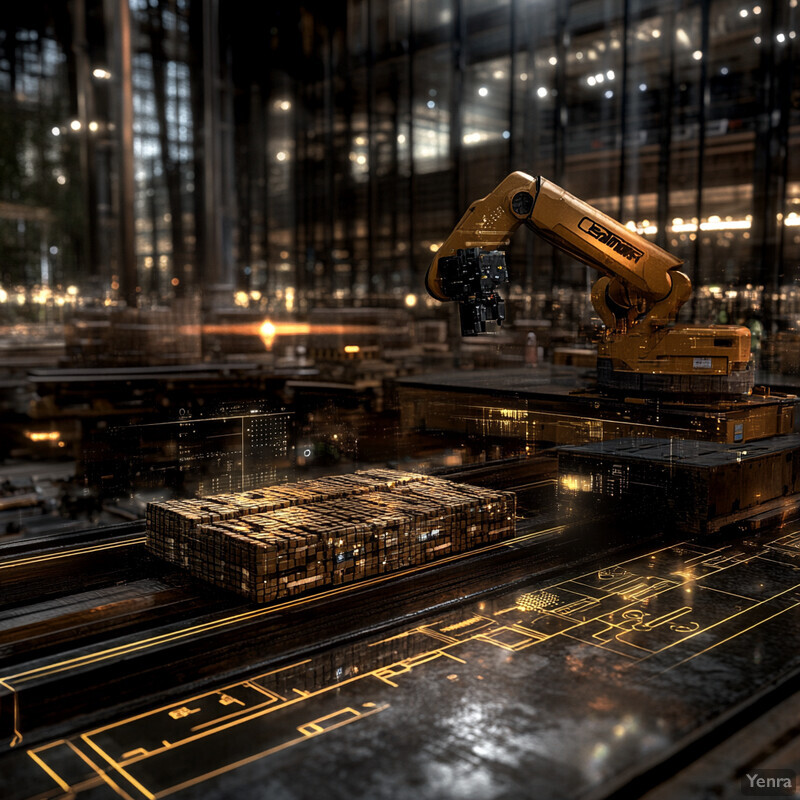
Construction sites are beginning to see tangible benefits from AI-enabled material handling automation. In Seattle, for instance, Skanska deployed two autonomous, AI-backed robots on a high-rise project to roll through the site, carrying sensors and materials – this pilot not only “sped up the project and improved safety” by reducing the need for workers to move through hazardous areas, but also provided constant progress data. These robots took over tasks like daily site walks and material transport, which meant fewer workers were exposed to fall risks or moving equipment during those activities. NIOSH has highlighted that robots can handle repetitive and labor-intensive tasks with greater speed and precision than humans, which can “boost productivity, reduce musculoskeletal disorders, and potentially improve work quality by reducing human error”. One concrete example is a robotics company that offers an autonomous rebar tying robot: contractors using it have reported zero hand strain injuries among workers in that activity, whereas traditionally those were common due to repetitive motion. Similarly, autonomous dump trucks in large construction zones (like mining or earthmoving sites) have led to a significant drop in vehicle-related incidents – some operations reported no vehicle-on-worker collisions in over 2 years since switching to AI-driven haul trucks. While full automation is not everywhere yet, even partial steps (like using a remote-controlled demolition robot instead of manual labor in a hazardous teardown) have prevented injuries. Early statistics from companies embracing construction robotics show a 17% reduction in overall recordable injuries, attributing much of that to removing workers from the line of fire during material handling and heavy operations.
19. Real-Time Communication Systems
AI-enhanced real-time communication systems ensure that crucial safety information and alerts are shared instantly with everyone on the construction site. These systems often integrate with mobile apps, radios, wearables, and alarm devices. If a hazard is detected by any of the AI monitoring tools (be it an approaching storm, a gas leak, an unauthorized entry, etc.), the communication platform uses AI rules to immediately broadcast the appropriate warning to relevant personnel. This could mean sending a mass text or push notification to all workers’ phones, triggering audible sirens in specific zones, or even delivering spoken warnings through smart hardhat speakers in multiple languages (AI can translate messages for a diverse workforce on the fly). Real-time communication also works in the other direction – workers can report hazards via voice or an app, and AI can prioritize and route those reports to the right supervisors instantly. The overall effect is that the moment a safety issue arises, everyone who needs to know will know, no matter where they are on site or what language they speak, drastically reducing reaction times in emergencies.
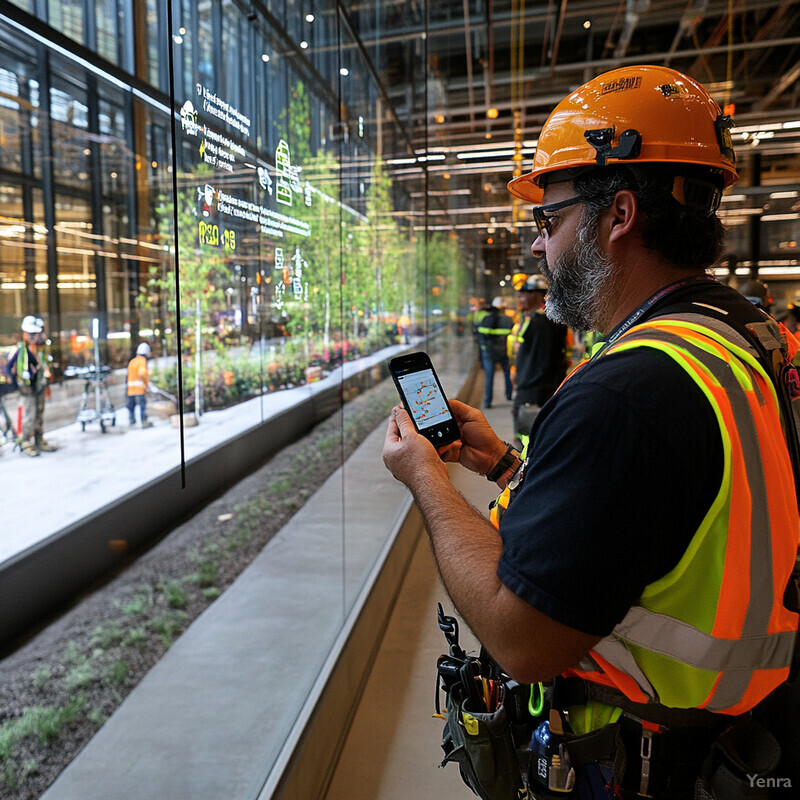
Speed and clarity of communication during safety incidents can be life-saving, and AI systems are proving their worth here. For example, modern lightning detection networks connected to construction sites will automatically send SMS alerts to all crew members when lightning is within a predefined distance, often giving workers a critical several-minute head start to seek shelter before a storm hits. In the realm of hazardous gas detection, AI-linked personal monitors now not only alarm locally but also immediately notify the whole site and management via cloud networks if one unit detects a spike – in one tunnel project, when a sensor picked up carbon monoxide beyond threshold, an evacuation alert was auto-triggered through every worker’s headset and the PA system, clearing dozens of people from danger in under a minute (an event that, in the past, might have taken much longer to coordinate). A study published by the National Safety Council highlighted that nearly 40% of surveyed workers would even reject a job offer if they perceived poor safety communication culture on site. AI is helping bridge such gaps: tools like chatbots and digital assistants (think of them as “safety Siri”) let workers query safety procedures or report issues hands-free, and get immediate answers or confirmation. On multi-lingual sites, AI translation ensures a Spanish-speaking laborer and an English-speaking foreman get the same message at the same time in their preferred languages. The technology has effectively eliminated the delay between hazard detection and workforce notification. Early adopters report scenarios where fall-detection AIs automatically called rescue teams within 10 seconds of a fall and notified nearby first-aid-trained staff – a dramatic improvement over hoping someone witnesses the incident and makes a call. These real-time, AI-coordinated communications are becoming the nervous system of site safety, enabling rapid, organized responses that have been credited with reducing the severity of injuries and preventing small problems from snowballing into major crises.
20. Continuous Improvement Through Feedback Loops
One of AI’s most powerful contributions to construction safety is enabling continuous improvement via feedback loops. Every incident, near-miss, or hazard detection provides data that the AI can learn from, refining its models and rules. For example, if an AI system notices that it issued many slip hazard alerts in a particular area, it can prompt a review of why that area is problematic and “learn” to watch for contributing factors (like water accumulation) earlier. At the same time, safety managers feed their on-the-ground lessons back into the AI – if a false alarm occurs, they correct it, making the system smarter over time. This cyclical process means the safety monitoring gets better and more accurate as the project progresses (and even carries over improvements to future projects). Moreover, AI can automatically compile safety performance metrics (leading indicators like number of near-misses, lagging indicators like injury rates) and highlight trends to management on dashboards. Teams then use those insights in regular safety meetings to adjust training, update site rules, or install new controls. In short, AI creates a dynamic safety environment that is always learning from itself – fostering a culture of continuous feedback and enhancement rather than static compliance.
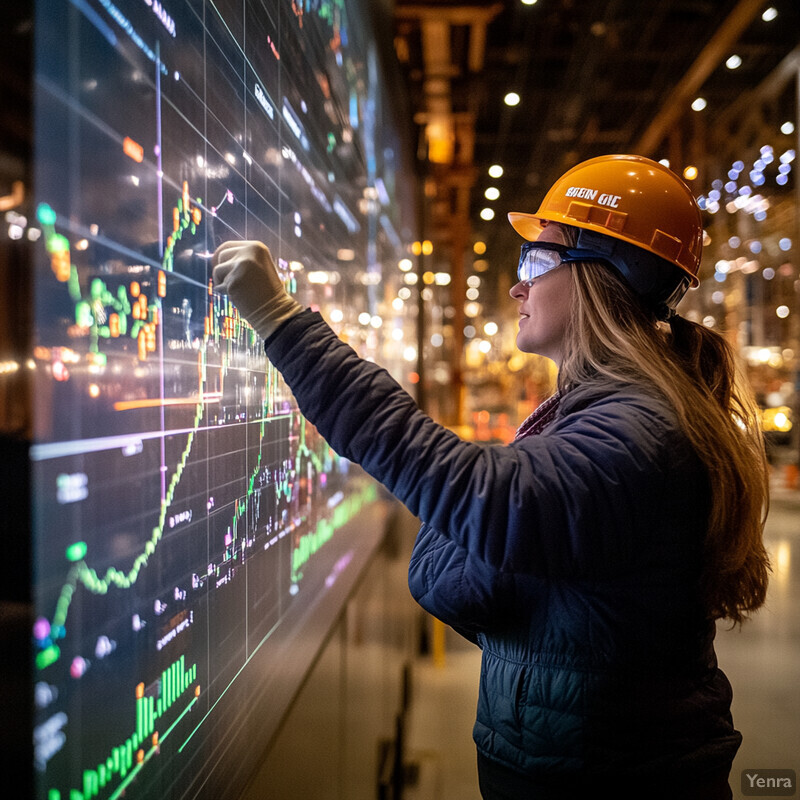
The implementation of AI-driven feedback loops has led to tangible improvements in safety metrics over time. For instance, one international contractor reported that in the first six months of using an AI safety platform, the system’s false positive rate for PPE alerts dropped from 15% to under 5% due to continuous model retraining on their site-specific data (each time the AI mistakenly flagged something, the correction was used to improve its accuracy). This kind of self-improvement is built in: sensor data analysis identifies trends, inefficiencies, and bottlenecks for process optimization, which the AI then uses to suggest or implement changes. In practice, construction firms using these systems have seen steady declines in their incident rates year-on-year – not just from one-off interventions, but from incremental adjustments guided by AI insights. A 2025 industry report noted that companies leveraging AI analytics for safety experienced on average a $4 return for every $1 invested in terms of reduced injury costs and improved productivity, attributable largely to the continuous fine-tuning of safety processes. Qualitatively, safety managers say they now have an ongoing “conversation” with their safety AI: the AI surfaces patterns (like frequent short-cuts taken by workers) and the managers respond with countermeasures, then the AI evaluates the effect of those actions. This feedback loop has led to proactive initiatives such as modifying site layouts or schedules mid-project when AI data showed an unexpected hazard trend. Ultimately, AI has turned safety management into a living process of constant learning – aligning perfectly with the principle of kaizen (continuous improvement) that many construction firms strive for. The result is a virtuous cycle: more data -> better insights -> safer practices -> fewer incidents -> new data confirming improvement, and so on.