1. Optimization of Print Parameters
AI algorithms intelligently tune 3D printing settings to achieve optimal results with less trial-and-error. Machine learning can analyze how factors like temperature, speed, and layer thickness affect print outcomes, then suggest the best combination for a given material or design. In industrial settings, this means higher consistency and reduced waste—printers automatically adjust to maintain quality across different machines and environments. For hobbyists and small businesses, AI-driven calibration takes the guesswork out of settings, making printers more user-friendly and reliable. Overall, AI-based optimization leads to faster print setup times and improved part performance without needing extensive manual experimentation.
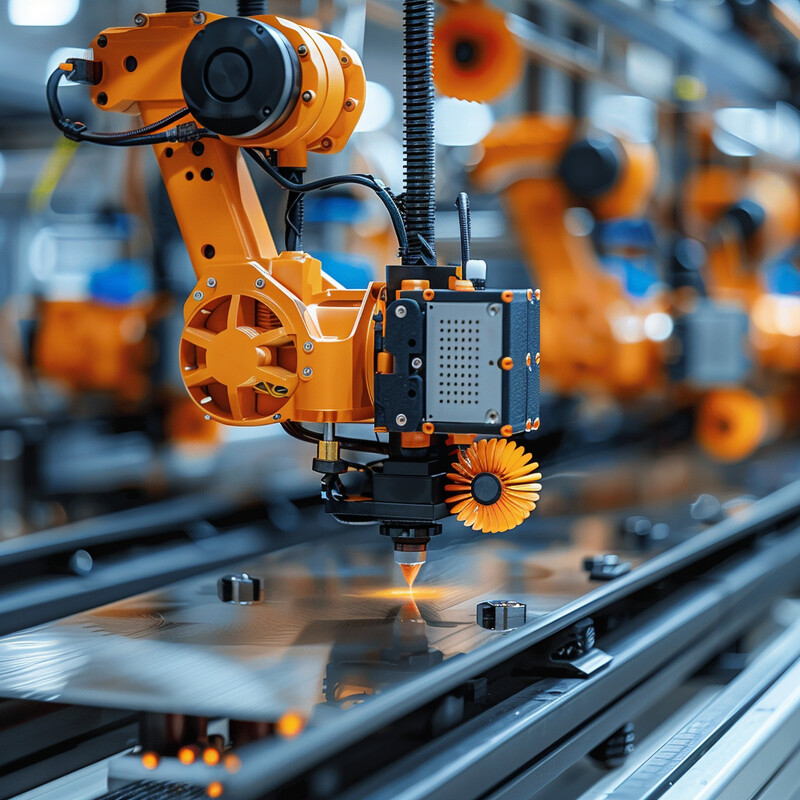
In a 2024 study, researchers found that using advanced machine learning to optimize printing parameters sped up the calculation of optimal settings by about 50% compared to a conventional neural network approach, while maintaining equal or better print quality. The AI-driven method even identified new parameter sets that traditional trial-and-error methods had missed (Szczupak et al., 2024). This demonstrates how AI can significantly streamline the planning of 3D print jobs by rapidly homing in on the best settings for material and quality targets. By reducing human guesswork, such AI tools save time and ensure parts are printed right the first time.
2. Predictive Maintenance
AI-powered predictive maintenance keeps 3D printers running smoothly by anticipating problems before they cause breakdowns. Sensors on printers feed data (e.g. motor currents, temperatures, vibration) into machine learning models that learn normal operating patterns. If the AI detects signs of wear or abnormal behavior, it can alert operators to service the machine or replace a part before a failure happens. In large-scale industrial print farms, this minimizes unplanned downtime—printers get maintenance exactly when needed, instead of waiting until something breaks. Even for small businesses or avid makers, predictive maintenance can mean fewer failed prints due to equipment issues (like clogged nozzles or misaligned optics) because the system proactively flags maintenance needs. The result is higher printer uptime, longer equipment life, and more reliable production schedules.
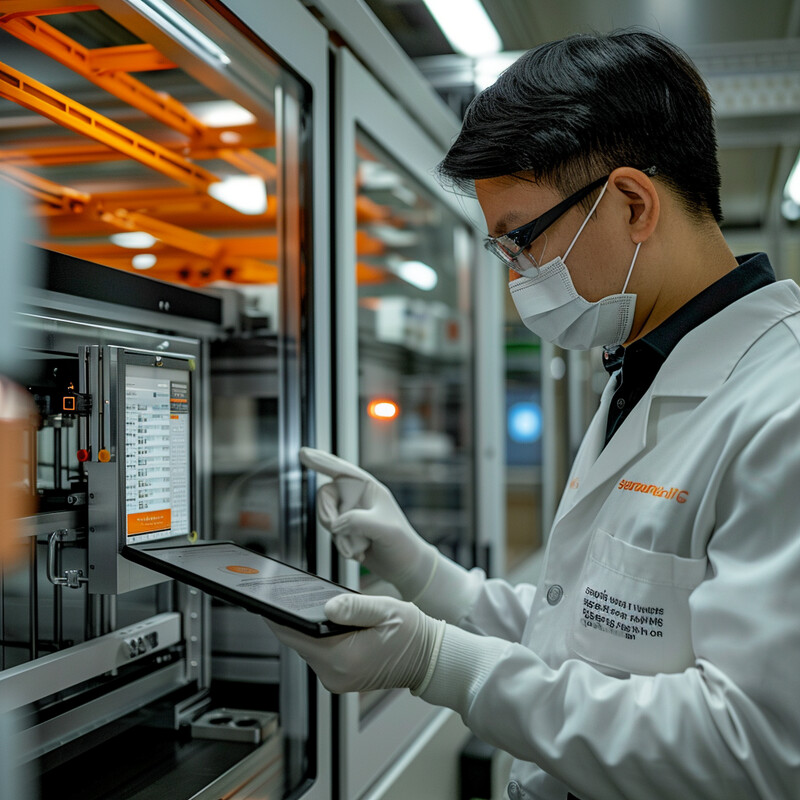
Predictive maintenance has been shown to substantially cut downtime and upkeep costs in manufacturing. For example, an industry analysis in 2025 reported that AI-based maintenance forecasting can reduce machine downtime by up to 15%, and lower maintenance expenses by around 10% compared to traditional scheduled or reactive maintenance (Advances in Preventive Maintenance, 2025). By catching issues early, an AI-driven approach prevents costly, unexpected printer failures and avoids unnecessary routine service when it isn’t needed. These improvements translate into both financial savings and smoother operations for companies using fleets of 3D printers.
3. Quality Control
AI is elevating quality control in 3D printing by automatically detecting defects and ensuring each part meets specifications. During printing, computer vision systems—often powered by neural networks—monitor each layer with cameras or lasers and spot anomalies like blobs, gaps, or warping. The AI can either adjust printing parameters on the fly to correct the issue or mark the part for rejection if it’s beyond salvage. This real-time oversight is especially valuable in industrial contexts (aerospace, medical) where internal defects could be critical; AI can catch microscopic flaws that human inspectors might miss. For finished parts, AI-driven inspection tools can compare 3D-scanned models of the print against the original CAD design to identify any deviations. On the consumer side, similar technology (like smartphone apps or cloud services) helps hobbyists detect print failures (such as the dreaded “spaghetti” error) early and stop the printer, saving time and filament. Overall, AI-based quality control leads to higher yield of good parts and greater confidence in 3D-printed products.
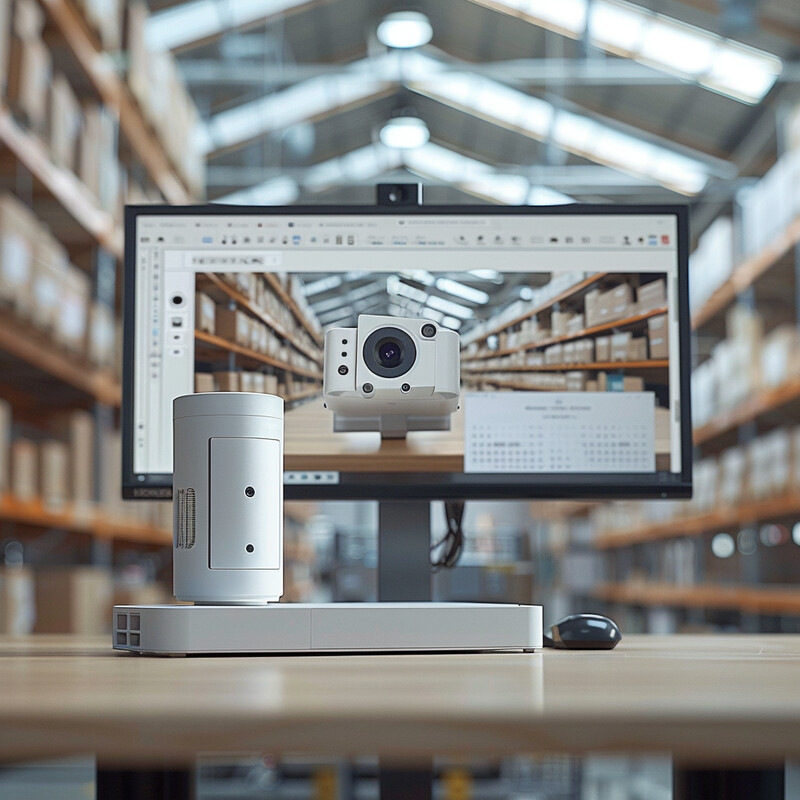
AI techniques have achieved remarkable accuracy in finding tiny defects during the print process. In one 2024 experiment focused on metal 3D printing, researchers used a machine learning system with simple sensors (like microphones and photodiodes) to monitor the build and detect the formation of microscopic “keyhole” pores in real time. The AI model accurately caught over 90% of these hidden defects, with a reaction time of just 0.1 milliseconds (Ren et al., 2024). This high level of precision and speed means the system can potentially halt or adjust a print the moment a flaw starts to form. Such AI-driven inspection not only improves part quality but also reduces waste, as printers can terminate faulty builds early instead of completing a defective part.
4. Generative Design
AI-driven generative design is transforming how we create objects for 3D printing by autonomously evolving optimized shapes that a human might not conceive. Engineers can input goals (like “minimize weight but withstand these forces” or “use least material while staying rigid”) and the generative design software—often using algorithms inspired by evolutionary processes or neural networks—produces a multitude of design alternatives. Many of these AI-generated shapes are highly efficient organic forms that look unconventional but perform exceptionally well when 3D printed. In industrial use, this leads to lighter, stronger components (crucial in aerospace and automotive for fuel efficiency) and consolidation of many parts into one complex printed piece. Small businesses and makers benefit too: generative design tools allow them to rapidly iterate product designs and tailor structures for specific needs (like custom ergonomic furniture or equipment) without needing an expert designer for each variant. Essentially, AI acts as a creative partner, exploring the design space far faster than a person, resulting in innovative geometries ready for additive manufacturing.
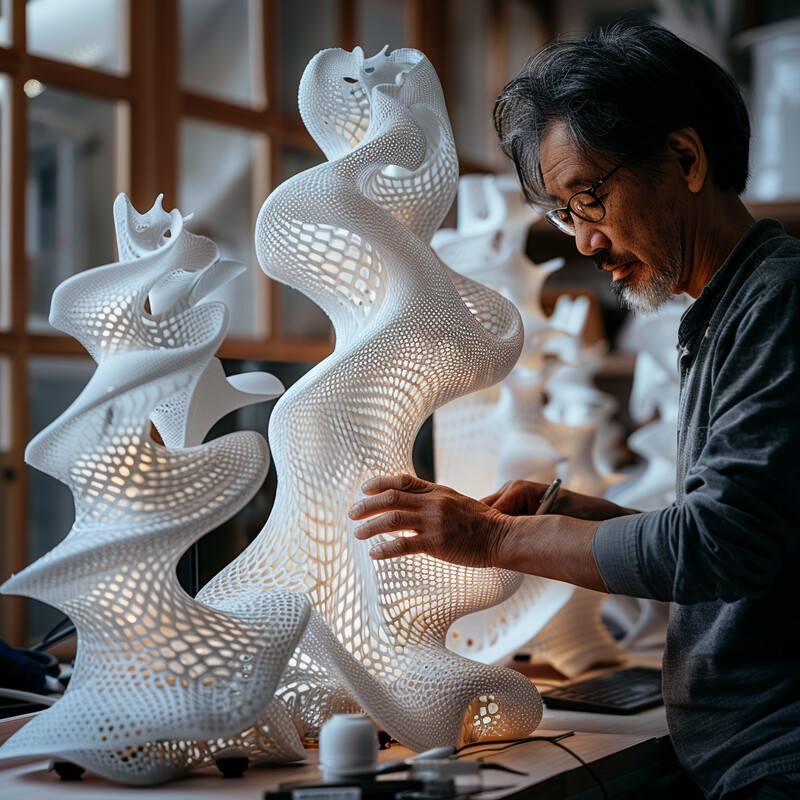
A notable example of generative design’s impact is General Motors’ development of a seat belt bracket using AI design and additive manufacturing. In this proof-of-concept project, the AI software explored over a hundred design options and came up with an intricate geometry that would be impossible to produce via traditional methods. The final 3D-printed bracket was 40% lighter and 20% stronger than the original, conventionally designed part it replaced (Danon, 2018). This dramatic weight reduction without sacrificing strength illustrates how AI-generated designs can outperform human designs. In practice, such weight savings can translate to better fuel efficiency in vehicles and lower material costs, while the strength gains ensure safety and durability. Generative design enabled GM to combine eight separate pieces into a single 3D-printed part, streamlining assembly and maintenance. This real-world result has encouraged wider adoption of AI-driven design in automotive and other industries for creating next-generation, high-performance components.
5. Material Science Advancements
AI is accelerating advancements in the materials used for 3D printing, helping scientists develop stronger, lighter, and more sustainable materials faster than ever before. By training machine learning models on materials databases and experimental results, researchers can predict how changing a material’s composition or processing will affect properties like strength, flexibility, or heat resistance. This means new alloys or polymer formulas optimized for 3D printing can be discovered with far fewer lab experiments—AI narrows down the most promising candidates. AI also assists in tweaking existing materials for better performance in printing (for example, adjusting a resin’s recipe so it cures with less shrinkage). In both industrial and maker communities, these AI-guided material improvements lead to printed parts with better mechanical properties and reliability. Additionally, AI is enabling more effective use of recycled or biodegradable materials by finding the right process settings or additives to make them print as well as virgin materials, which supports sustainability in 3D printing.
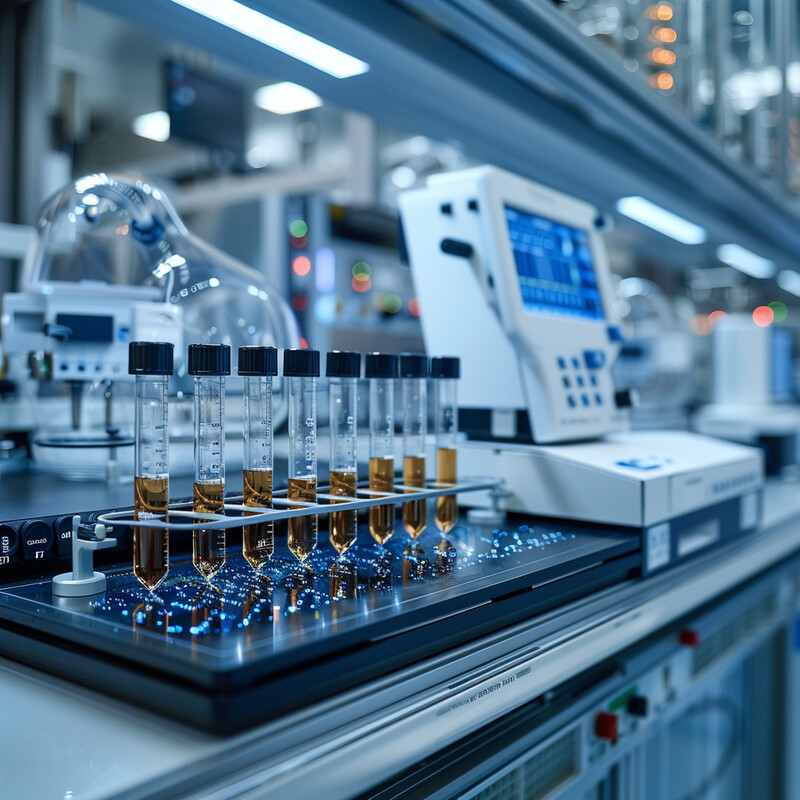
One concrete benefit of AI optimization is more efficient material usage and less waste in the printing process. A 2025 review noted that AI-based process controls can identify and eliminate inefficiencies in how material is laid down. This can save enough filament or powder that for roughly every 6–7 prints, one extra print is essentially “free” in terms of material that would have been wasted without optimization (Rojek et al., 2025). In other words, smarter printing strategies driven by AI yield about a 15% material savings, directly reducing costs. Such savings are significant for both small-scale users (who get more prints out of each spool of filament) and large manufacturers (who spend less on raw material and generate less scrap). Beyond cost, these optimizations mean less plastic and metal waste, aligning with environmental goals. AI’s ability to fine-tune parameters for each material also has enabled improvements like boosting the tensile strength of recycled 3D-printing plastics by over 7% through optimal print settings, making recycled options more viable as a replacement for new material.
6. Automation of Post-Processing
AI is streamlining the often labor-intensive post-processing stage of 3D printing, which includes tasks like removing support structures, surface finishing, and part inspection after a print is completed. Traditionally, these steps can require significant manual work—technicians might spend hours cutting off supports with tools, sanding surfaces, or tending machines like tumblers or furnaces. Now, AI-driven robotics and smart equipment are taking over many of these chores. For example, vision-guided robotic arms (controlled by AI image analysis) can identify where supports or excess material are on a printed part and carefully remove them without damaging the piece. Machine learning algorithms also optimize post-processing conditions (such as the ideal vibration frequency in a media tumbler for polishing, or the exact duration of heat treatment) to ensure each part meets quality specs with minimal intervention. For industrial users, this automation means faster turnaround and lower labor costs per part, making large-scale additive manufacturing more economically competitive. Small businesses also benefit as they can achieve professional-quality finishes on 3D prints without needing extensive craftsmanship. AI essentially connects the 3D printer to a smart finishing line, creating a more automated end-to-end production flow.
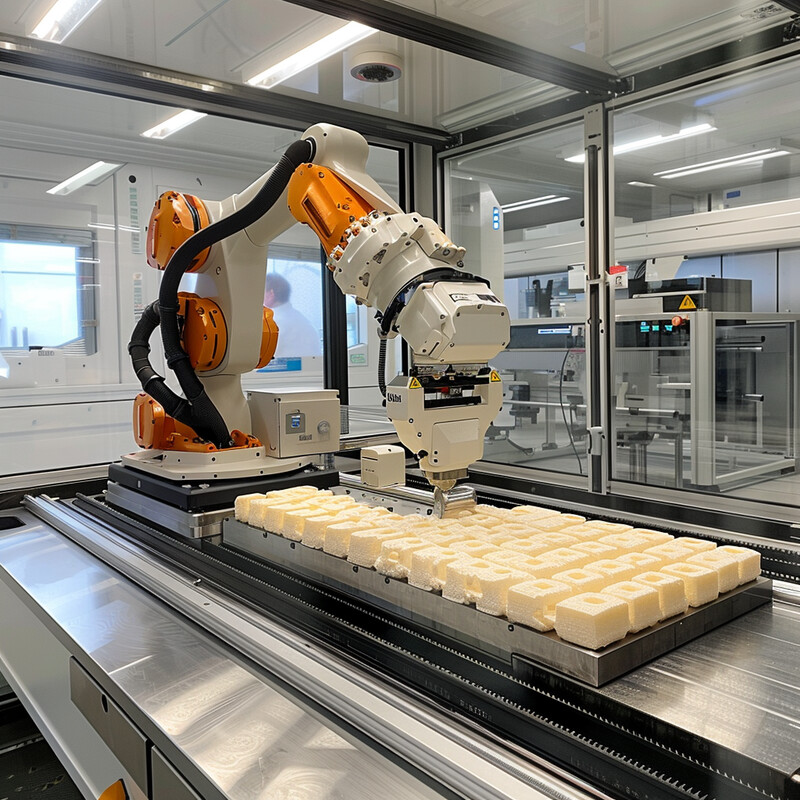
Automation can dramatically cut the time and labor required after printing. A recent collaboration between a 3D printer manufacturer and a post-processing technology company demonstrated that an AI-driven depowdering system (for powder-bed 3D printers) could reduce manual labor costs by over 75% while recovering more than 95% of unused powder for reuse (PostProcess Technologies, 2024). In this system, once a metal or plastic part is printed and comes out of the printer encased in excess powder, an intelligent machine takes over: it uses algorithms to agitate and suction away the powder automatically, instead of a technician cleaning the part by hand. The result was that tasks which used to occupy many hours of an employee’s time were completed with minimal human oversight. This not only lowers the cost per part, but also protects workers from inhaling powder and ergonomic strain. Across the industry, similar AI-enabled post-processing units (for support removal, sanding/polishing, or even painting parts) are reporting significant reductions in cycle times. By shortening post-processing from days to hours and freeing up skilled staff for higher-level work, AI-driven automation is helping 3D printing scale up in production environments.
7. Customization and Personalization:
AI is enabling mass customization through 3D printing, making it easier to tailor products to individual needs and preferences. Unlike traditional manufacturing (where making one-off custom items is very expensive), 3D printing already offers flexibility for customization, and AI enhances this by automating the design adjustments needed for each unique item. In healthcare, for instance, AI can convert medical scan data (like a 3D scan of a patient’s limb) into a perfectly fitted prosthetic or orthotic device model, ready for 3D printing—dramatically reducing the time clinicians spend modifying designs. In consumer goods, companies use AI to let customers co-create products: a customer might input desired features or biometrics into a user-friendly interface, and AI algorithms generate a printable model (such as a shoe insole contoured to the person’s foot, or eyewear frames styled to their face). Small businesses can leverage these tools to offer personalized products (jewelry, furniture, gadgets) at scale, because AI handles the heavy lifting of redesigning each item. The combination of AI and 3D printing essentially flips the old mass production model on its head: instead of one design for many, we get “many designs for one,” without a big cost penalty. This improves customer satisfaction and can better meet niche requirements—for example, athletes getting equipment optimized to their body, or patients receiving implants matched to their anatomy.
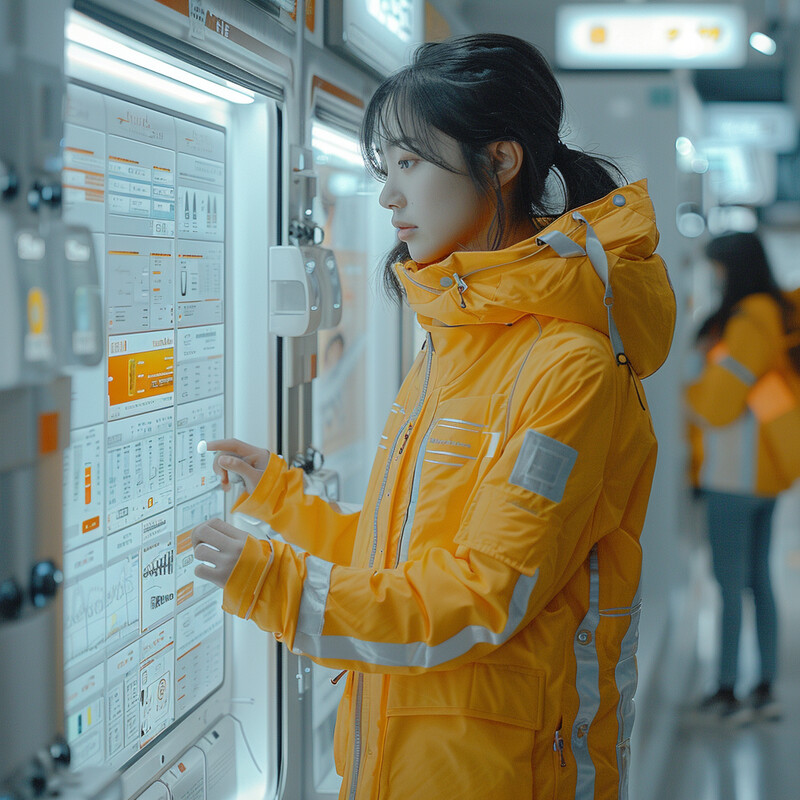
The impact on cost and accessibility of personalized products is significant. In medicine, producing custom prosthetic limbs has traditionally been very expensive and slow, but AI plus 3D printing is changing that. Engineers at the University of California reported that using personalized 3D scans and AI-driven design, they could 3D-print prosthetic limbs far more efficiently—cutting costs by 50% to as much as 90% compared to conventional fabrication methods (Patringenaru, 2022). For example, advanced prosthetic legs that might cost tens of thousands of dollars can potentially be made for only a few thousand or even a few hundred dollars with these techniques. Moreover, the turnaround time drops from weeks or months to just days. Similar savings and customization benefits are seen in other areas: dental aligners and hearing aids are now often AI-modeled and 3D-printed to fit individuals, which has made them more affordable and widely available. In the retail space, surveys show consumers are willing to pay a premium for personalized items, yet AI-driven 3D printing is actually managing to reduce the cost of customization – a win-win that is driving broader adoption of bespoke solutions.
8. Supply Chain Integration
AI is integrating 3D printing into supply chains, making manufacturing and distribution more agile. In a traditional supply chain, companies must forecast demand and mass-produce parts, then store inventory in warehouses—an approach that can lead to overstock or shortages. With AI and 3D printing combined, the model shifts to on-demand production: AI systems analyze real-time sales data, logistics, and even external factors (like weather or geopolitical events) to predict what parts or products are needed and when. Instead of keeping large inventories, companies can maintain digital inventories (CAD files) and use 3D printers to produce items as orders come in, at locations close to the customer. AI helps by automatically scheduling print jobs across a network of printers (perhaps in multiple facilities or stores), optimizing for fastest delivery or lowest cost. It can also decide whether it’s more efficient to 3D print a part locally versus shipping it from a central stock. This is particularly useful for spare parts in industries like automotive or aerospace: an AI might identify that a certain component is likely to fail and trigger a print of the replacement at the nearest service center, just in time. For small businesses and consumers, AI-driven supply chain integration might mean when you order a product, the system finds the closest 3D printer hub to you that can make it, reducing shipping time. Overall, AI makes supply chains more responsive and reduces dependence on large physical inventories by intelligently leveraging 3D printing’s flexibility.
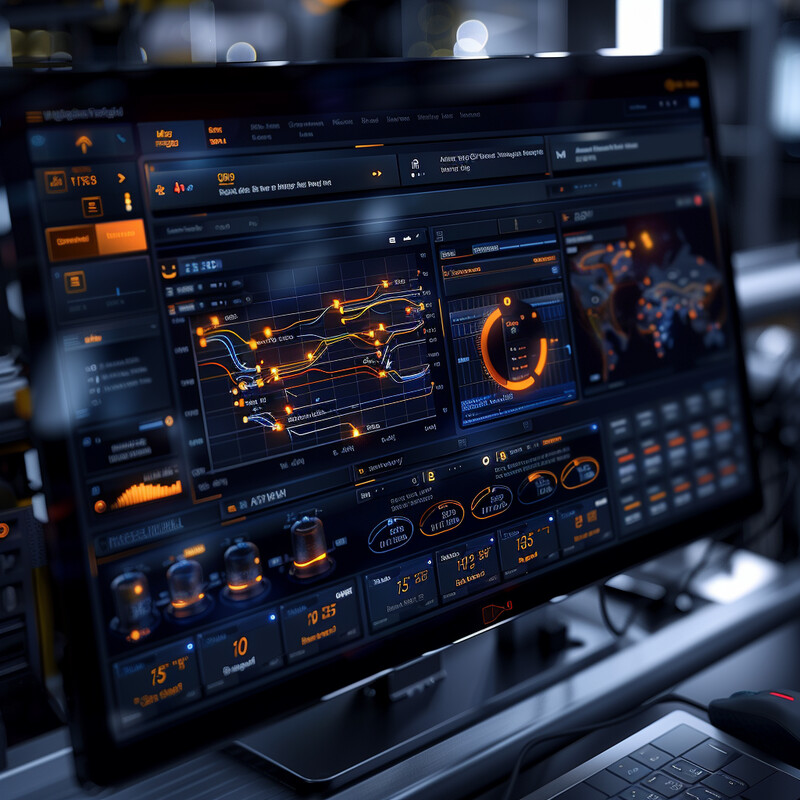
Companies adopting AI-coordinated, on-demand 3D printing have reported major savings in inventory and logistics costs. Siemens, for example, implemented a digital supply chain for some of its replacement parts and used 3D printing to produce spares as needed rather than stockpiling them. As a result, Siemens was able to reduce its inventory costs by about 85% by printing on demand (Freeman, 2025). This huge reduction illustrates the economic benefit of not tying up capital in stored goods that might become obsolete. Instead, their AI-driven system monitors equipment and orders a 3D print of a part only when required, often at a location near the point of use. Additionally, this approach shortened lead times dramatically—parts that might have taken weeks to arrive from a central warehouse can be printed and in service within days, or even hours, avoiding downtime. On a broader scale, supply chain studies have found that using distributed 3D printing and AI logistics management can cut overall supply chain costs by 20–30% through a combination of reduced storage, fewer expedited shipments, and minimization of waste from overproduction. These data points are encouraging many industries to rethink manufacturing and inventory strategies around AI and 3D printing integration.
9. Error Recovery
AI doesn’t just detect errors; it can also help recover from them, turning potential print failures into successes. In 3D printing, errors like misaligned layers, filament jams, or overheating can ruin a print. Traditionally, once a print goes bad, the machine might keep going, wasting material and time, or the user has to stop it manually and start over. AI systems change this by actively managing the print process. For instance, an AI monitor can recognize the signature of a printing error (through a camera image or sensor data) and immediately pause the print. Some advanced research even enables the printer to adjust and continue: for example, if a small defect is detected, the AI might alter the toolpath on the fly to compensate, or if material runs low, it triggers a refill routine and resumes printing seamlessly. In scenarios where a print is paused, AI can help by recalculating a “resume print” plan that blends the new material with the already printed section, so the final piece is still usable—this is like repairing the print mid-process. For both industrial and home users, these capabilities mean fewer aborted prints and more finished parts from each attempt. AI-driven error recovery is especially valuable for long prints (taking many hours or days), where encountering a minor error no longer means the entire build is lost. It boosts overall success rates and gives users more confidence to attempt complex prints.
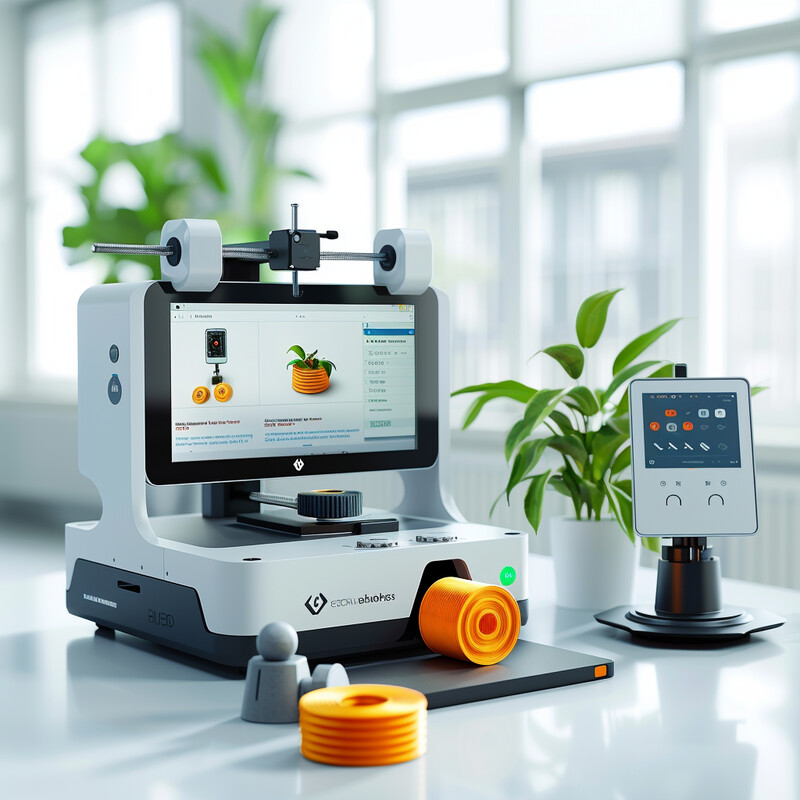
Users are seeing tangible improvements in print success rates thanks to AI error detection and intervention. As reported by a 3D printing cloud platform in 2025, many organizations using AI-based print monitoring have seen 30–50% fewer failed prints than before (3DPrinterOS, 2025). This reduction in “unsuccessful prints” is attributed to the AI catching problems early—such as spaghetti-like filament tangles or parts detaching from the print bed—and halting the process or alerting operators in time to fix the issue. The result is a significant cut in wasted material and printer wear-and-tear. For a small business printing dozens of parts a day, this improvement can save hundreds of dollars in filament and many hours of machine time each month. In industrial additive manufacturing, higher yield (fewer scrapped builds) directly improves throughput and lowers per-part cost. This level of error mitigation is made possible by machine learning models trained on images and sensor readings of print failures; they continuously learn and become more accurate over time. As AI continues to evolve, we can expect even more advanced recovery techniques—perhaps future printers will not only pause, but also perform self-corrections (like automated nozzle cleaning or recalibration) and then resume printing without any human intervention at all.
10. Enhanced Security
AI is strengthening the security aspect of 3D printing in multiple ways, from protecting intellectual property to preventing sabotage and counterfeit parts. As 3D printing becomes part of digital supply chains, there’s a risk that confidential design files could be stolen or misused; AI can help by monitoring network traffic and user behavior to detect unauthorized access or downloads of sensitive 3D model files. In manufacturing environments, AI-driven anomaly detection systems keep an eye on printer operations for signs of tampering—if a hacker were to subtly alter printer settings or a design file to produce faulty parts, the AI could notice unusual patterns (like a deviation in power consumption or print head movement) and alert operators. Moreover, AI algorithms are being used to create digital “watermarks” or unique signatures in printed objects (tiny geometric patterns or material infusions not visible to the eye) to ensure authenticity; an AI-trained scanner can later verify that a part is genuine and produced from the original file, which helps combat counterfeiting. For small-scale users and enterprises alike, AI enhances security by adding an intelligent, automatic layer of defense that works in the background. It reduces the burden on humans to constantly supervise for potential breaches or quality issues caused by malicious interference. In essence, as 3D printing merges more with the digital world, AI acts as a guardian—safeguarding data, processes, and end products from security threats.
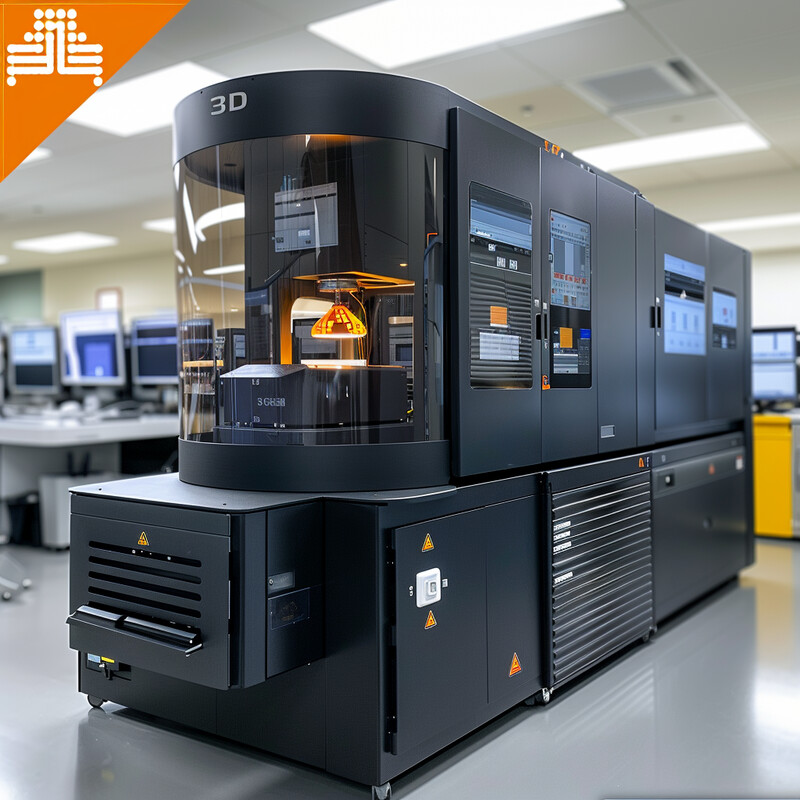
The need for improved security in 3D printing is very real. In a survey of manufacturers, a majority (about 63%) of respondents expressed concern about protecting their intellectual property when sending 3D designs to third-party printing services (Nano Dimension, 2016). This highlights fears that proprietary CAD files could be copied or leaked during outsourcing. AI tools are now being introduced to alleviate such worries—for example, by ensuring files are encrypted and only accessed in approved ways, and by automatically flagging any anomalous access that might indicate a breach. On the production side, researchers have demonstrated possible cyber-attacks on 3D printers that introduce internal defects into critical components; in response, AI-based detection systems have been able to catch these sabotage attempts by recognizing telltale signals (one study showed power usage patterns can reveal a malicious print alteration with high accuracy). Industry reports also note that companies view security measures (including AI-driven ones) as both a barrier and an enabler for wider 3D printing adoption—the barrier is the risk, and the enabler is the technology (like AI) that can manage that risk (Adu-Amankwa & Daly, 2023). As of 2025, leading firms are investing in AI-enhanced security protocols so they can confidently expand 3D printing in their operations without exposing themselves to IP theft or compromised product integrity.