1. Resource Assessment and Prediction
AI models can greatly enhance the assessment and forecasting of tidal resource potential by analyzing extensive tidal, bathymetric, and environmental data. These models learn from historical flow measurements to predict future tidal currents and energy yields under varying conditions. Improved resource forecasts help planners estimate energy production, assess site viability, and integrate tidal power reliably. By accurately predicting tides and currents, AI-driven tools can reduce uncertainty in project planning and operation. Overall, AI-based resource assessment leads to better-informed decision-making and more effective exploitation of tidal energy.
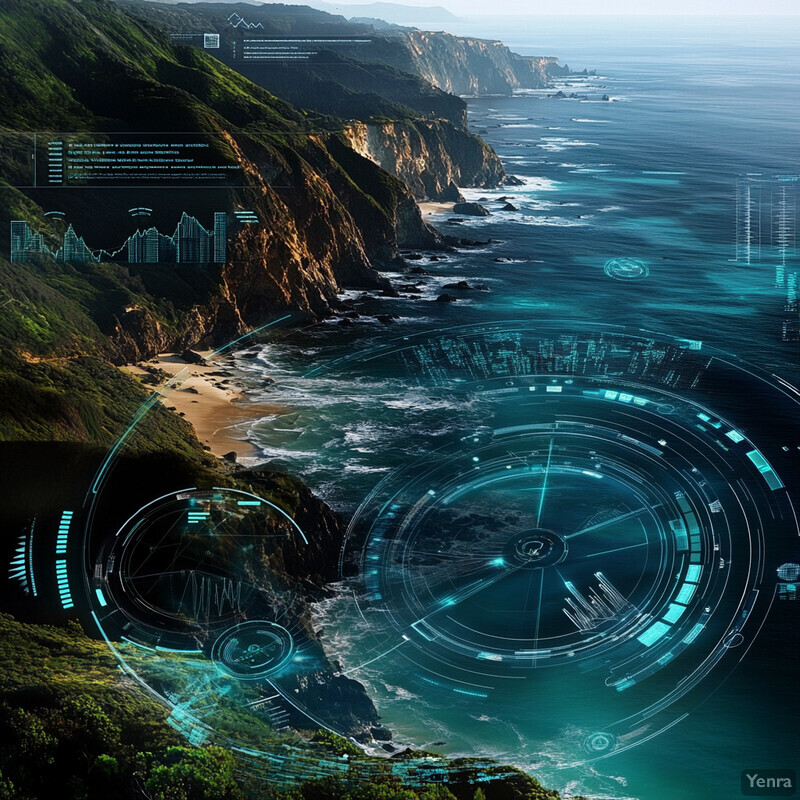
Recent studies demonstrate large accuracy gains in tidal flow and power forecasting using AI. For example, a hybrid neural network model achieved dramatic error reductions in multi-step tidal speed predictions – one report found mean absolute error (MAE) and mean square error (MSE) fell by up to 90.36% and 97.56% respectively compared to baseline models. In another case, an AI model validated on U.S. Gulf of Mexico tidal data boosted the prediction R² from 0.965 to 0.993 and cut mean-squared error by about 80%. These results indicate that modern machine learning frameworks can sharply improve tidal current forecasts. By reliably predicting long-term and short-term tidal variations, such AI tools provide data-driven resource estimates, reducing uncertainty for developers.
2. Site Selection Optimization
AI can automate and optimize the multi-criteria process of choosing ideal tidal farm locations. By integrating geographic, hydrodynamic, and environmental datasets, machine learning helps identify sites with strong currents, suitable depth, and minimal ecological impact. These AI-driven GIS analyses consider factors like bathymetry, tidal power density, grid access, and protected areas simultaneously. The result is faster, data-rich site selection compared to manual methods. In practice, this leads to better site choices that maximize energy yield while meeting environmental and engineering constraints. Overall, AI-enhanced site selection tools improve the efficiency and sustainability of planning tidal energy projects.
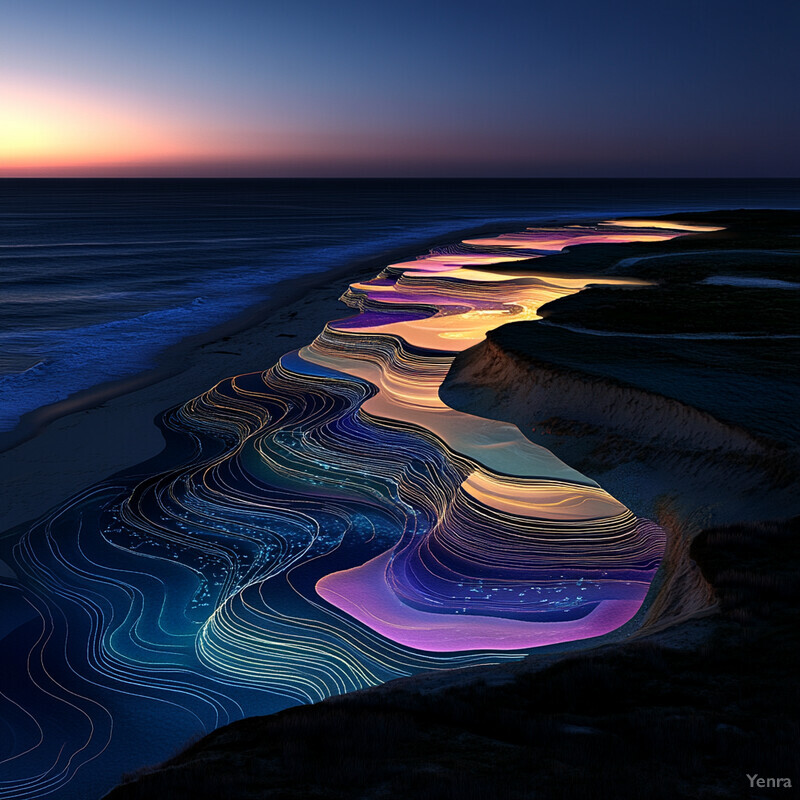
Recent research shows AI/GIS systems can pinpoint optimal array layouts and account for environmental constraints. One study demonstrated that a GIS+AI framework “enables automated identification of optimal sites for energy generation” while improving site choice and energy output forecasting. In a practical case, a multi-criteria GIS tool applied in Irish/UK waters identified the “potential and optimum areas for deployment of both wave and tidal energy devices”. The same work emphasized that site selection must filter out unsuitable zones by considering “several core geospatial criteria” (technical, environmental, logistical). These results confirm that AI-powered analysis can systematically evaluate complex site factors. By uncovering new candidate areas and reducing planning effort, AI-driven methods significantly enhance tidal site selection processes.
3. Predictive Maintenance Scheduling
AI analytics can predict component wear and failures ahead of time, enabling smart maintenance scheduling. By analyzing operational data (vibration, oil particles, temperatures, etc.) from turbines, machine learning models forecast when parts like blades, bearings, or gearboxes will need service. This predictive approach replaces fixed-interval maintenance with condition-based actions, reducing unexpected downtime and maintenance costs. Effective AI scheduling maximizes turbine availability by servicing units just before failure. The outcome is lower lifecycle costs and safer, more reliable operations for tidal farms.
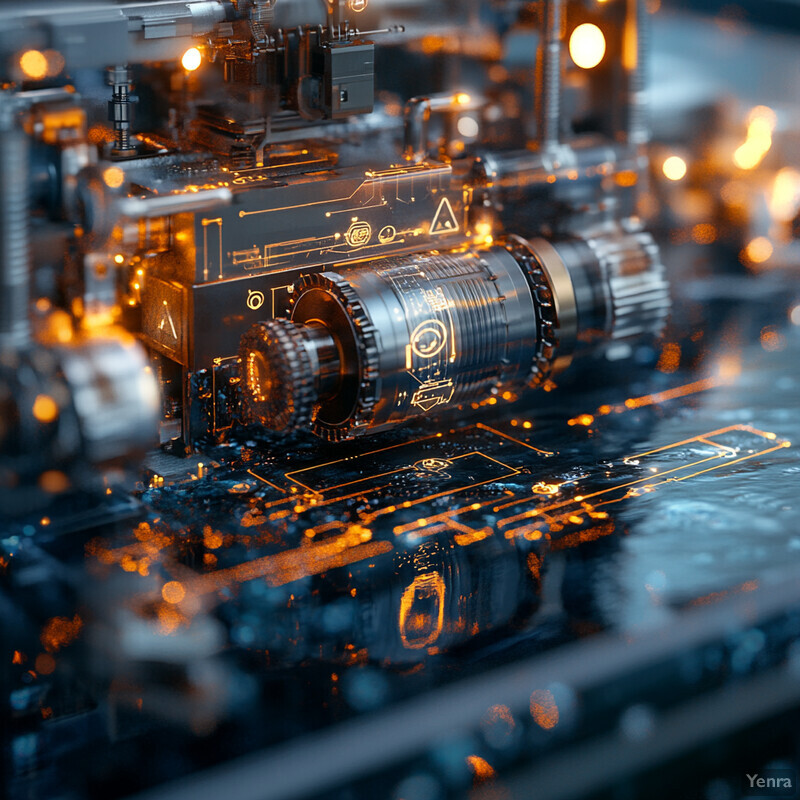
AI-based predictive maintenance has been shown to significantly improve reliability in related energy systems. One machine learning framework predicted equipment failures with 92% accuracy and reduced unplanned downtime by about 35% across wind and hydro plants. Similarly, an AI ensemble model for tidal turbines achieved R² = 0.989 in performance prediction and 98.4% accuracy in detecting biofouling on turbine surfaces. These high-accuracy predictions enable timely maintenance actions (e.g., cleaning fouled blades or servicing gears). Such studies suggest that AI models can effectively anticipate mechanical or environmental issues, allowing operators to schedule maintenance just-in-time and avoid catastrophic breakdowns.
4. Structural Health Monitoring (SHM)
AI methods can monitor the structural integrity of tidal turbines in real time by processing sensor measurements (e.g. strain, vibration, acoustics). Machine learning algorithms classify structural responses to detect cracks, delamination, or impact damage on blades and support structures. By interpreting data continuously, AI can alert operators to early-stage damage that would be hard to spot manually. In practice, this means proactive maintenance can be done before minor damage grows critical. Overall, AI-powered SHM enhances safety and extends the lifespan of tidal components by ensuring issues are caught quickly.
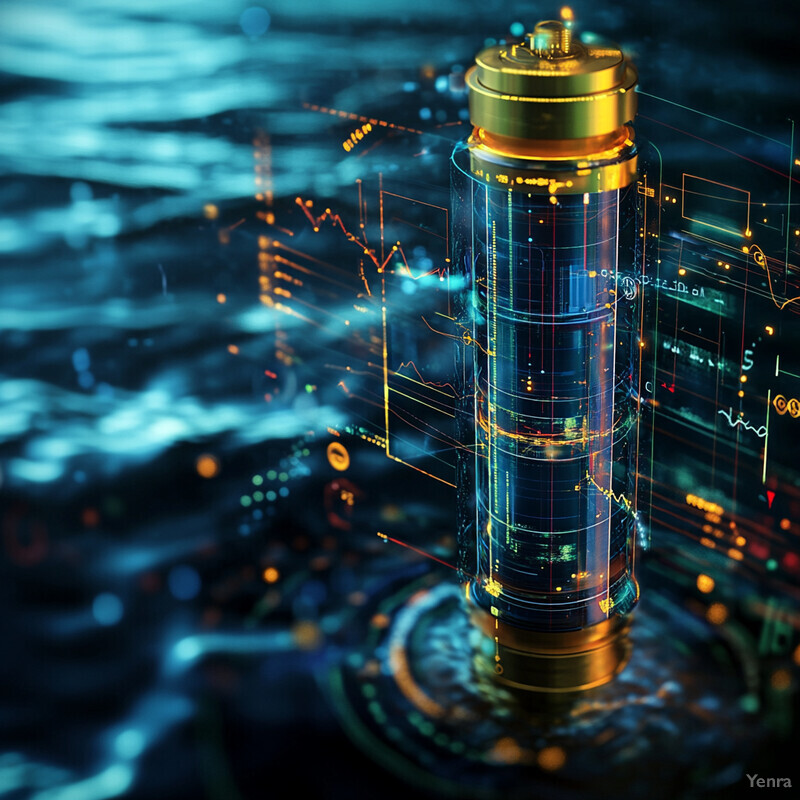
Recent research projects have begun developing AI-based SHM systems for tidal blades. For example, Syed et al. (2023) proposed an explainable AI framework for real-time detection of damage in tidal turbine blades. Their approach uses sensor data and machine learning models to classify various nonlinear damage modes (impact, delamination, cracks) during operation. While quantitative field results were not reported, this work establishes that AI-based monitoring frameworks are feasible and can be integrated with ICT infrastructure for continuous blade health assessment.
5. Hydrodynamic Modeling and Simulation
AI and machine learning accelerate detailed hydrodynamic simulations of tidal flows. Surrogate models (e.g., neural networks informed by physics) are trained on high-fidelity CFD data to predict flow fields much faster. These AI models can capture complex 3D current patterns around devices with high accuracy but at a fraction of the computational cost. This makes it easier to run many design simulations or scenario analyses. By quickly generating flow predictions, AI-assisted modeling helps in site assessment and turbine design. In sum, AI-enhanced hydrodynamic simulation tools allow faster exploration of flow dynamics and array interactions.
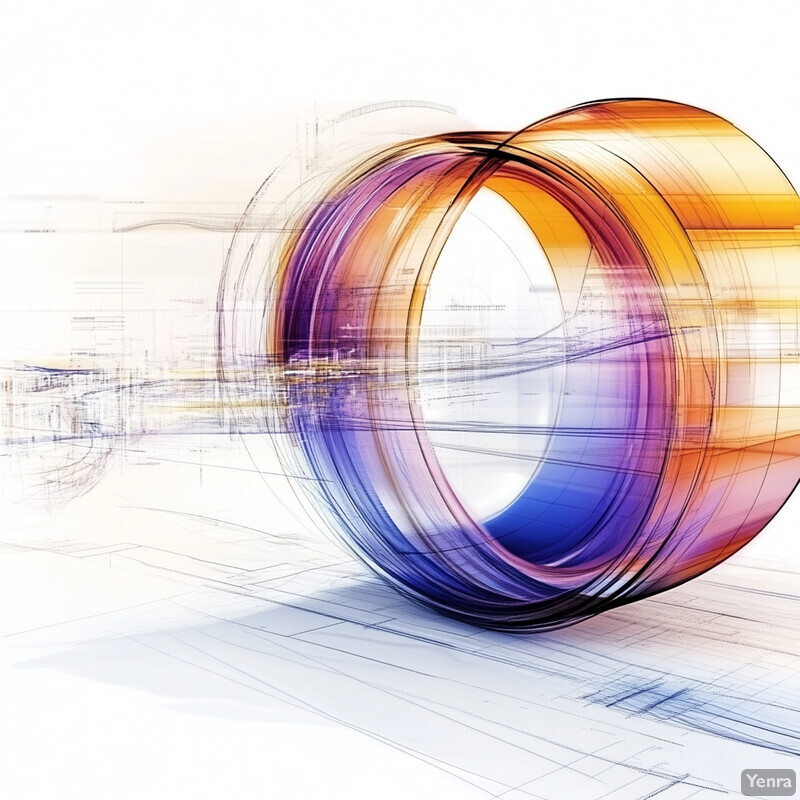
A recent ECCOMAS conference study showed that a physics-informed neural network surrogate for tidal flow simulation outperformed a conventional ML model by ~10–20% across accuracy metrics. The authors encoded conservation laws into the learning model to avoid overfitting, resulting in much more physically consistent predictions. This improvement demonstrates that AI surrogates can approach the fidelity of full numerical models. By providing faster simulations with similar accuracy, such PINN models offer robust alternatives for long-term and high-resolution tidal simulations.
6. Array Layout Optimization
AI-driven optimization algorithms (genetic algorithms, particle swarm, etc.) can greatly improve the layout of multiple turbines in a tidal farm. These tools simulate wake interactions and test numerous configurations to maximize total power and efficiency. By considering complex wake effects and site geometry, AI finds layouts that manual design would miss. The output is typically an array arrangement that yields higher energy capture or lower costs. In effect, AI layout optimization ensures that turbine placement is tuned for collective benefit, boosting overall farm output.
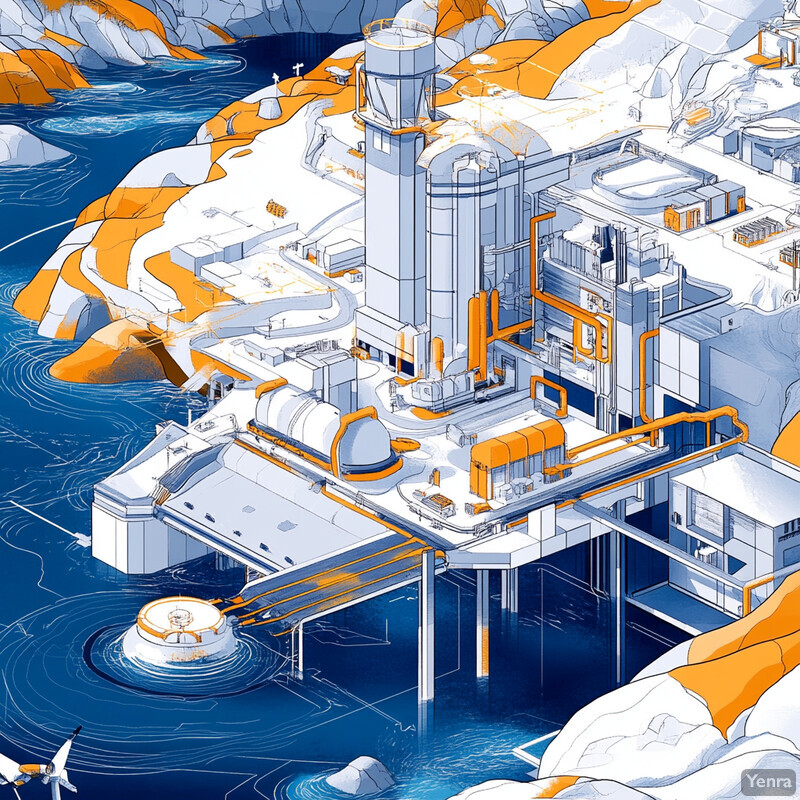
Studies report significant performance gains from AI-optimized layouts. In one case, a quantum-inspired particle swarm algorithm was applied to optimize a real tidal farm’s layout. Compared to a regular grid pattern, the AI-optimized layout raised total power generation by ~19% (flood tide) and 16% (ebb tide). This reconfiguration also cut the levelized cost of energy (LCOE) by roughly 12–15% and reduced the required sea area by ~24%. Such results demonstrate that data-driven layout design can substantially increase energy yield and economic efficiency in tidal arrays. The AI method’s superior performance confirms that accounting for wakes and turbine interactions is critical for maximizing array output.
7. Data-Driven Design of Turbine Blades
AI enables rapid, innovative blade design by exploring vast design spaces. Machine learning and generative models can propose airfoil shapes or blade geometries optimized for higher lift, lower drag, and structural strength. Designers can specify performance targets, and AI-driven inverse design tools quickly suggest blade profiles meeting those criteria. This dramatically speeds up the iterative design process compared to traditional CFD-driven optimization. AI-influenced designs can achieve better performance with reduced design time. As a result, data-driven methods are accelerating the development of more efficient and robust tidal turbine blades.
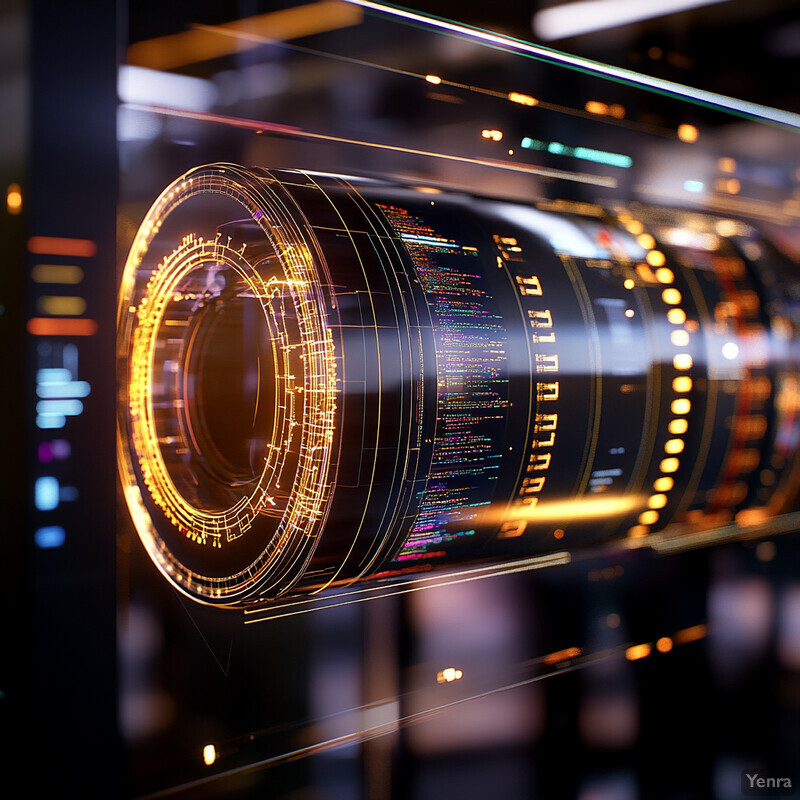
Promising examples exist from related fields. For instance, NREL researchers used an invertible neural network to optimize wind turbine airfoils, achieving roughly a hundredfold speed-up over conventional design methods while meeting target performance. This shows that AI can dramatically accelerate blade design workflows. By analogy, similar AI tools could be applied to tidal turbine blades. Although direct tidal-focused results aren’t yet available, the wind-turbine case indicates that AI-driven blade design can greatly reduce computation time while satisfying aerodynamic requirements.
8. Noise and Environmental Impact Minimization
AI can help minimize the acoustic and ecological footprint of tidal installations. For noise, AI models can predict how sound propagates underwater and guide quieter operation strategies (e.g. adjusting thrust or timing around sensitive species). For overall environmental impacts, machine learning can analyze monitoring data to evaluate turbine effects on habitat (e.g. fish behavior or sediment changes). By modeling complex sound and disturbance patterns, AI enables designers to mitigate harmful noise. In practice, AI-assisted simulations and sensing allow engineers to plan quieter turbine designs and operation schedules that reduce ecological harm, making tidal energy more eco-friendly.
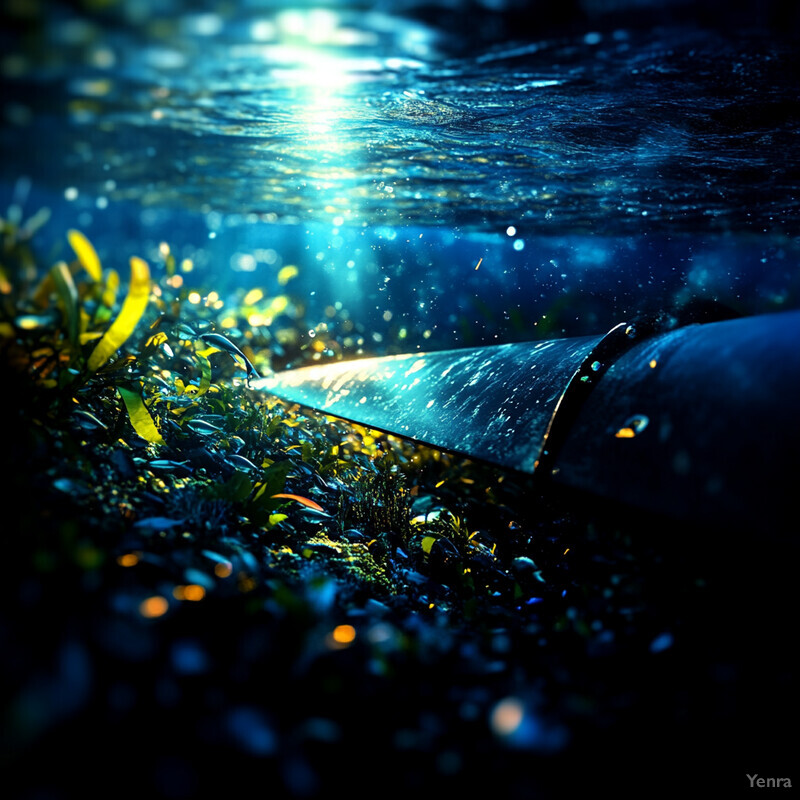
New AI-driven modeling tools are being developed to reduce underwater noise impact. For example, University of Glasgow researchers created an AI system that accurately simulates underwater sound propagation. This model can predict how noise spreads from human activities (shipping, wind farms, etc.) through the ocean environment. Such a tool could allow tidal energy planners to assess noise footprints and design mitigation measures (e.g. noise-shielding or alternate operation times) to protect marine life. By providing detailed sound modeling at much lower computational cost, AI systems like this promise to help industries proactively minimize ecological noise pollution.
9. Predicting Marine Life Interactions
AI is increasingly used to detect and predict wildlife interactions with tidal installations. Computer vision and sensor data allow automatic identification of marine animals near turbines. For instance, underwater cameras with AI can recognize fish species and behaviors, alerting operators to high presence of wildlife. Similarly, AI-analyzed sonar or optical data can track animal movement patterns around turbines. By forecasting where and when animals will occur, AI helps schedule shutdowns or design protective measures. These tools help minimize collisions and habitat disturbance, supporting coexistence of tidal energy with marine ecosystems.
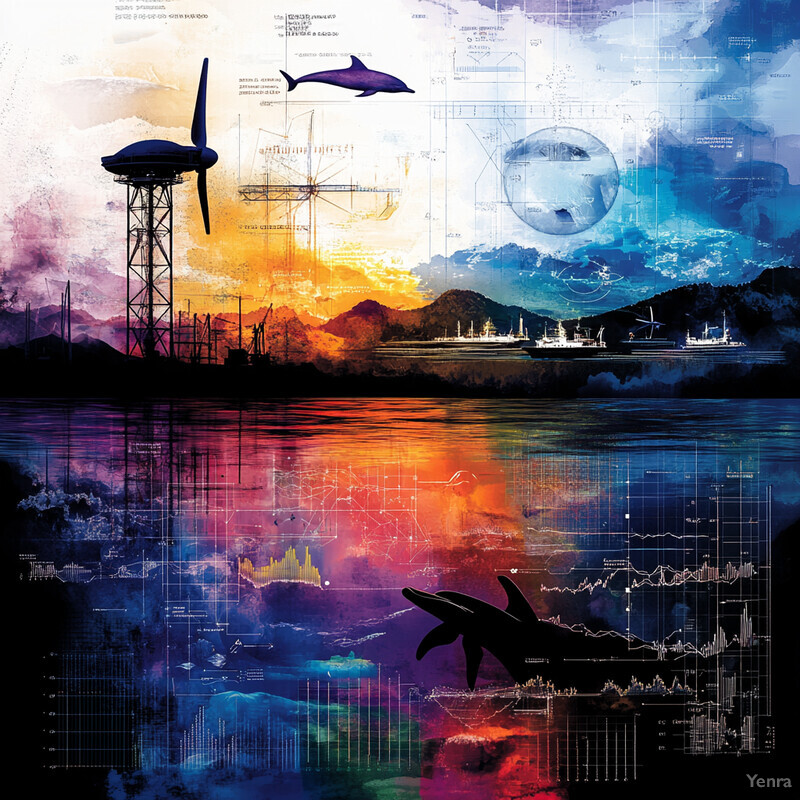
Cutting-edge AI systems are already being applied to marine monitoring. Google’s X lab (“Tidal”) developed an underwater camera and AI platform that “can detect and interpret fish behaviors (such as feeding) and model fish behaviors over time”. In another example, U.S. DOE researchers created an autonomous survey vehicle (SEARCHER) that uses AI to recognize specific marine targets like bioindicator species (e.g. sand dollars). This system maps sand-dollar distributions to detect ecosystem changes after energy devices are installed. These developments illustrate that AI vision and pattern-recognition tools can monitor wildlife around marine energy sites, enabling data-driven assessments of ecological interactions.
10. Condition-Based Monitoring of Gearboxes and Generators
AI-based condition monitoring systems analyze sensor signals (vibrations, temperatures, oil debris, etc.) to detect mechanical faults in gearboxes and generators. Machine learning algorithms learn normal operating patterns and flag anomalies indicating wear or damage. This enables operators to service components (gears, bearings, generators) precisely when needed rather than on fixed schedules. By catching issues early, AI fault detection prevents major breakdowns. In practice, this leads to safer operation and reduced maintenance costs for powertrain components in tidal turbines.
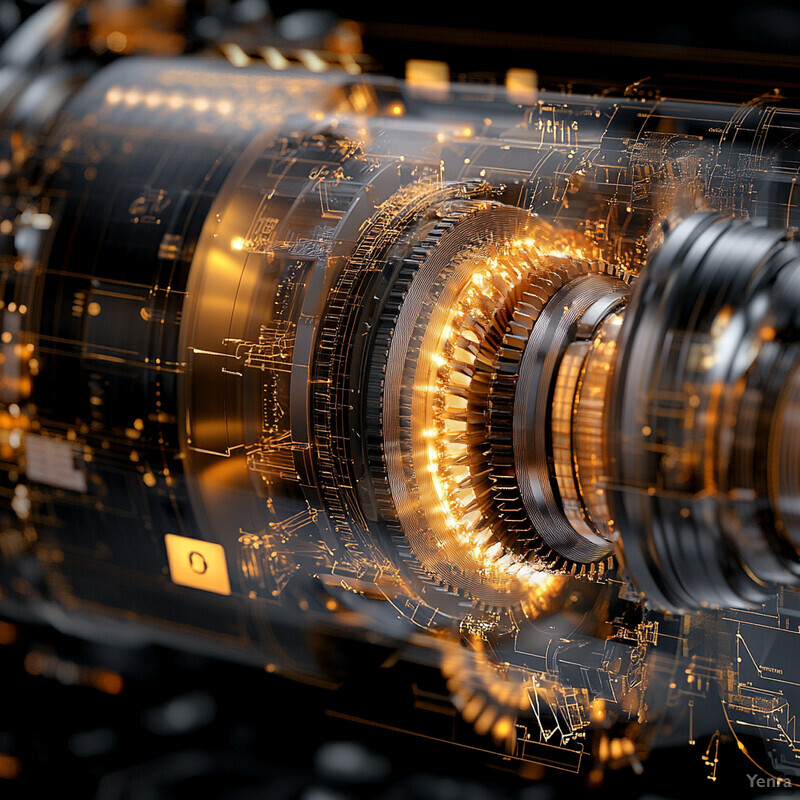
AI prognostics have shown high reliability in related contexts. For example, one study applied AI to wind and hydro systems and achieved ~92% accuracy in predicting equipment failures, cutting unexpected downtime by 35%. While that work was general, it demonstrates ML’s effectiveness in diagnosing mechanical faults. In tidal turbines, similar techniques applied to gearbox data could yield comparable benefits.
11. Sensor Fusion and Data Integration
AI excels at integrating diverse data streams (e.g. SCADA telemetry, vibration sensors, acoustic monitors, environmental sensors) for holistic analysis. By fusing these inputs, machine learning can detect patterns not apparent from any single sensor. For instance, combining flow speed, blade strain, and power output data can yield better fault diagnostics than each alone. Sensor fusion also improves prediction robustness (e.g., confirming a signal spike across multiple sensors before flagging an issue). Overall, integrated data analysis enhances situational awareness and enables more accurate performance and health assessments of tidal systems.
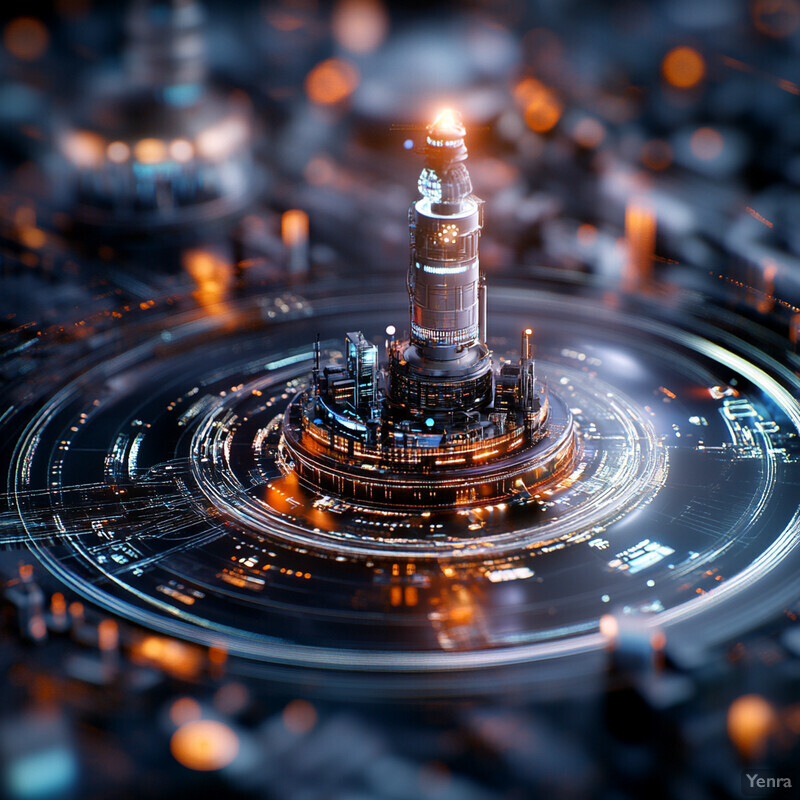
Studies highlight the use of large-scale multi-source datasets in AI models. For example, Bello et al. (2024) trained their predictive models on extensive datasets from operational wind, solar, and hydro plants. This implies that merging various data types (such as SCADA logs, vibration readings, and meteorological data) is feasible and beneficial. Using rich, integrated data sources in machine learning leads to more reliable predictions. In practical terms, tidal operators can similarly combine SCADA data with external sensors to feed AI systems for more comprehensive analysis.
12. Automated Anomaly and Fault Detection
Advanced AI models (e.g. deep learning, anomaly detection algorithms) are used to automatically identify unusual behaviors in tidal turbines. These methods continuously analyze sensor streams (torque, vibration, temperature, etc.) to spot deviations from normal patterns. When an anomaly is detected (e.g. unusual vibration signature), the system alerts operators or triggers a safety protocol. Automation speeds up fault recognition and reduces reliance on manual monitoring. Consequently, AI-driven anomaly detection improves reliability by catching subtle faults (bearing wear, sensor errors) early.

High accuracy has been reported in AI fault-detection tasks. In one case, an ensemble machine learning model achieved 98.4% accuracy in identifying biofouling on tidal turbine blades. This illustrates AI’s ability to detect specific anomalies from operational data. In another renewable energy application, AI predicted failures with 92% accuracy and cut downtime by 35%, implying similar gains could apply to mechanical fault detection in turbines. While not tidal-specific, these results indicate that AI can reliably flag faults and anomalies, enabling timely intervention.