1. Enhanced Demand Forecasting Accuracy
AI-driven demand forecasting uses machine learning to analyze far more data and patterns than traditional methods. These systems incorporate real-time inputs like web trends or social media sentiment, allowing forecasts to adjust quickly when market conditions change. By improving baseline forecast accuracy and responding faster to demand shifts, AI helps companies reduce stock-outs and excess inventory. Better demand predictions mean production and ordering can be more closely aligned with actual needs. As a result, firms can lower inventory holding costs and improve service levels while avoiding the waste or shortages caused by poor forecasts.
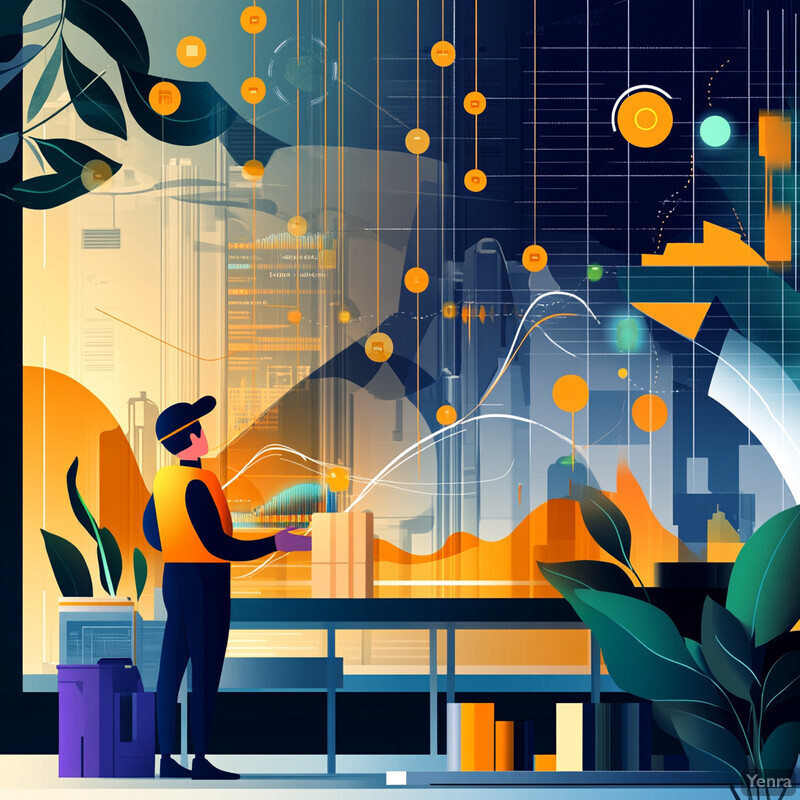
Research in 2024 confirms that AI-based forecasting significantly outperforms conventional techniques. One study found companies using AI for demand planning achieved up to a 30% improvement in forecast accuracy compared to traditional approaches. AI models can integrate diverse factors (economic indicators, weather, consumer behavior) that manual forecasts often miss. This higher accuracy translates into practical gains: businesses respond more quickly to market changes and optimize inventory, which reduces costs and boosts efficiency. For example, U.S. firms adopting AI-driven forecasts report not only fewer stock shortages but also leaner inventories, improving both customer satisfaction and financial performance.
2. Real-Time Anomaly Detection
AI enables real-time anomaly detection in supply chain operations by continuously monitoring data streams for irregular patterns. Machine learning models learn what “normal” behavior looks like for metrics like supplier lead times, order volumes, and transit durations. When an unusual spike or drop occurs – for instance, a sudden delay from a carrier or an odd surge in orders – the AI flags it immediately. Early anomaly detection gives managers a chance to investigate and respond to potential issues (like a looming bottleneck or fraud) before they escalate. In essence, AI acts as a 24/7 sentry that notices subtle deviations across the supply chain that humans might miss until it’s too late.
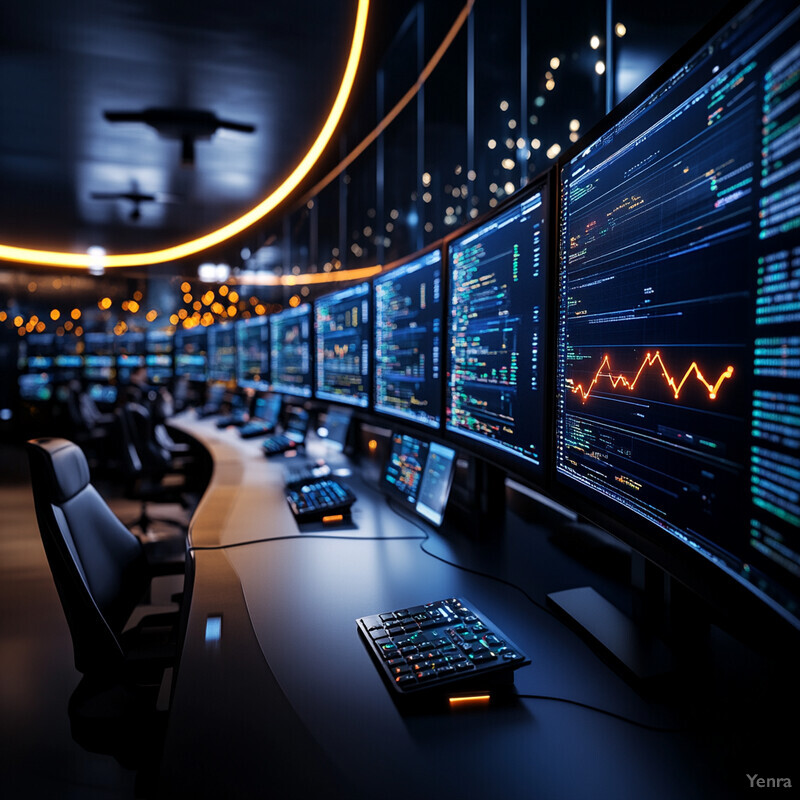
The impact of AI-driven anomaly detection is evident in both cost savings and service improvements. Industry analyses show these systems can slash shipping errors by about 60% and cut loading or unloading delays by 40% by flagging problems early. For example, one logistics audit found that AI-based anomaly detection reduced payment losses by 15%, and with fine-tuning it achieved a 52% drop in expected financial losses due to irregularities. Even in non-supply contexts, AI anomaly detectors have proven their worth: a 2023 study in banking found machine-learning models reduced expected fraud losses by over 50% with a very low false-alarm rate jfin-swufe.springeropen.com . These results underline that AI can catch issues far faster than periodic manual checks – whether it’s spotting billing fraud, detecting an out-of-line manufacturing parameter, or preventing a minor glitch from snowballing into a major disruption.
3. Dynamic Supplier Risk Assessments
AI enables dynamic, continuous assessment of supplier reliability and risk. Traditionally, companies might review supplier risk quarterly or annually using static checklists. In contrast, AI-driven platforms aggregate real-time signals about each supplier – financial health updates, late delivery incidents, regulatory compliance data, news reports of labor or political issues – and update the supplier’s risk profile continuously. This means purchasers can see an evolving “risk score” for each vendor that reflects current conditions, not just historical audits. With dynamic assessment, warning signs like a supplier’s deteriorating credit or repeated quality failures trigger proactive mitigation (such as qualifying alternate suppliers or adjusting order volumes) long before a crisis hits. In essence, AI turns supplier risk management from a periodic activity into a live process.
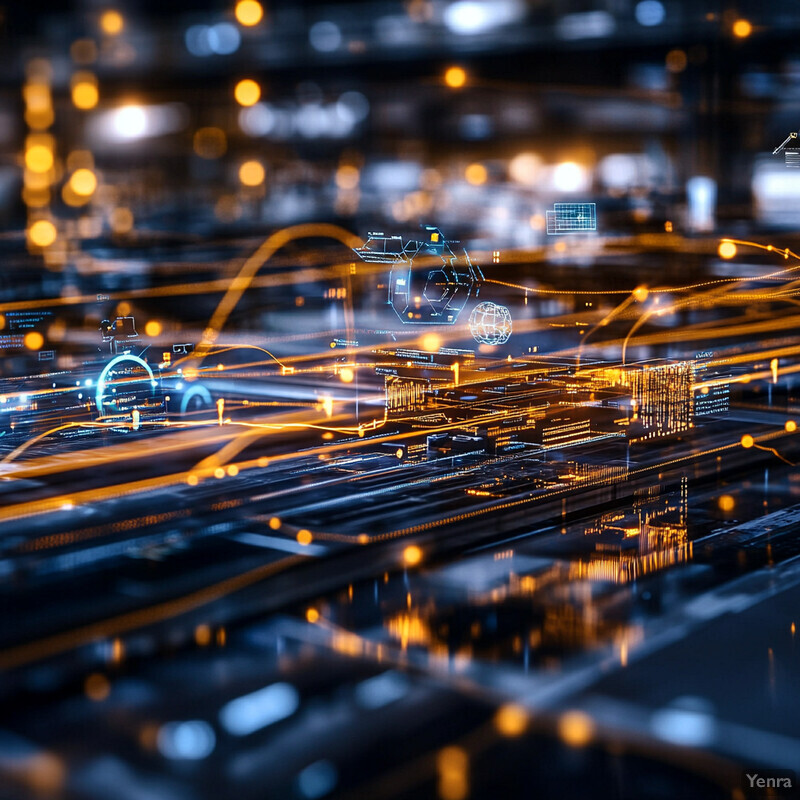
One striking example comes from the U.S. Defense Logistics Agency (DLA), which uses AI-based analytics to screen its vast supplier base. The system continuously monitors multiple risk indicators and has analyzed 43,000 vendors, flagging over 19,000 as potentially high-risk in real time. This dynamic approach paid off directly: AI-generated alerts led DLA investigators to uncover a supplier’s covert outsourcing of parts to unauthorized manufacturers, resulting in legal action. On a broader scale, AI-driven risk scoring is becoming standard – for instance, resilience indices now synthesize data on suppliers’ financial stability, geographic risk, and past performance into single scores. Platforms like Interos assign each supplier an “i-Score” to gauge resilience across dozens of factors. These AI-powered ratings give procurement teams an at-a-glance view of which suppliers are most likely to fail under stress, allowing early interventions such as finding backup sources or renegotiating terms before a disruption occurs.
4. Early Warning Signals from External Data
AI leverages external data – news feeds, social media, economic reports, and more – to provide early warning signals of supply chain threats. By applying natural language processing and sentiment analysis, AI systems can scan thousands of sources globally and pick up hints of events like labor strikes, natural disasters, political unrest, or regulatory changes that could disrupt supply lines. These early signals give companies a crucial head start. For example, AI might detect negative sentiment building about a key port’s labor negotiations on social media or news of an emerging trade embargo, prompting preemptive actions (such as rerouting shipments or securing alternative suppliers) days or weeks before traditional monitoring would catch up. In short, AI-driven risk intelligence turns the overwhelming flood of external data into actionable foresight for supply chain planners.
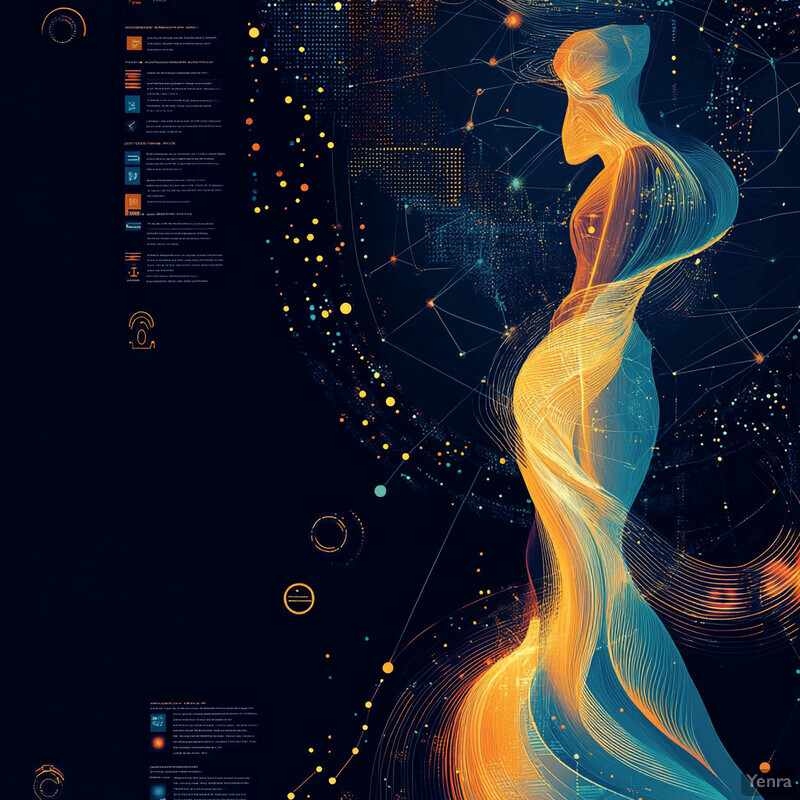
The benefits of these AI “radar” systems are quantifiable. In one implementation, a predictive analytics platform mining news and social feeds enabled companies to respond to disruptions 36 hours faster than teams without AI, by alerting them to trouble much sooner ai-cases.com ai-cases.com . Such tools also drastically increase the scope of risk detection – one case study reported an 85% increase in early risk detection of events (like factory fires or geopolitical shifts) compared to manual monitoring ai-cases.com ai-cases.com . This translates into concrete savings: an e-commerce firm using AI alerts anticipated 80% of late deliveries in advance, allowing it to adjust logistics and trim inventory buffers by 2–3%, saving an estimated $15–20 million ai-cases.com . Moreover, modern AI risk networks like Resilinc’s EventWatch process around 5 billion data feeds a year across 100+ million sources in over 100 languages. This unparalleled coverage means that if a disruption is brewing anywhere – from a coup affecting mineral exports to a viral tweet about a supplier’s bankruptcy – the AI can raise a red flag for decision-makers before the impact hits the supply chain.
5. Predictive Maintenance of Logistics Assets
AI-driven predictive maintenance keeps transportation fleets, warehouse equipment, and production machinery running reliably by forecasting failures before they happen. Sensors on assets like trucks, forklifts, or machines feed data (vibrations, temperature, performance metrics) into AI models that learn to recognize the subtle patterns preceding a breakdown. Instead of servicing on a fixed schedule or reacting after a failure, companies can perform maintenance just in time when the AI predicts a component is likely to fail soon. This approach minimizes unexpected downtime and extends equipment life, since parts are replaced right before they would fail rather than too early or too late. In supply chains, the result is fewer vehicle breakdowns en route, less warehouse conveyor downtime, and overall smoother operations with lower maintenance costs.
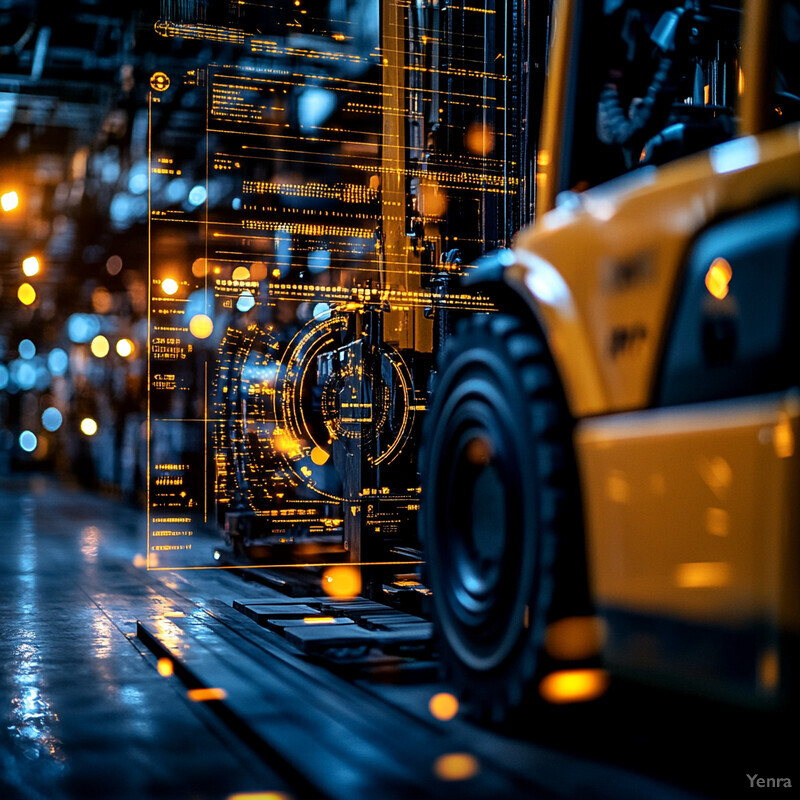
The efficiency gains from predictive maintenance are well documented. Deloitte reports that on average, predictive maintenance reduces unplanned equipment breakdowns by 70%, boosts productivity by 25%, and lowers maintenance costs by 25%. In practice, logistics companies have saved millions: UPS’s AI-driven fleet maintenance program, for instance, turned what used to be $50,000 emergency engine replacements into $3,000 scheduled repairs – preventing engine failures on 80 trucks and saving $1 million in four months for one large fleet. Fleet operators using AI also see far fewer road calls; one study found predictive maintenance cut overall fleet maintenance expenses by ~20% and unplanned downtime by ~50%. Even manufacturing firms report significant improvements – a well-known analysis by PwC found that adopting predictive maintenance in factories can decrease maintenance costs by 12%, improve asset availability by 9%, and extend machinery life by 20%. These outcomes demonstrate how AI-driven maintenance keeps supply chain assets humming with minimal disruption.
6. Weather and Climate Impact Modeling
AI is helping supply chains anticipate and mitigate weather and climate-related disruptions more effectively than ever. By ingesting meteorological forecasts, satellite data, and historical weather patterns, AI models can predict how events like hurricanes, floods, or blizzards might impact logistics routes and facility operations. These models go beyond generic forecasts – for example, they can estimate which specific supplier locations or transport lanes are at risk and when, allowing planners to proactively reroute shipments or adjust inventory. Climate impact modeling also covers slower-onset factors: AI can incorporate climate trends (e.g. increased frequency of heatwaves or droughts) into capacity planning, so companies fortify their supply chain for these evolving risks. Essentially, AI translates raw weather data into actionable supply chain plans, giving companies lead time to avoid or lessen the blow from nature’s disruptions.
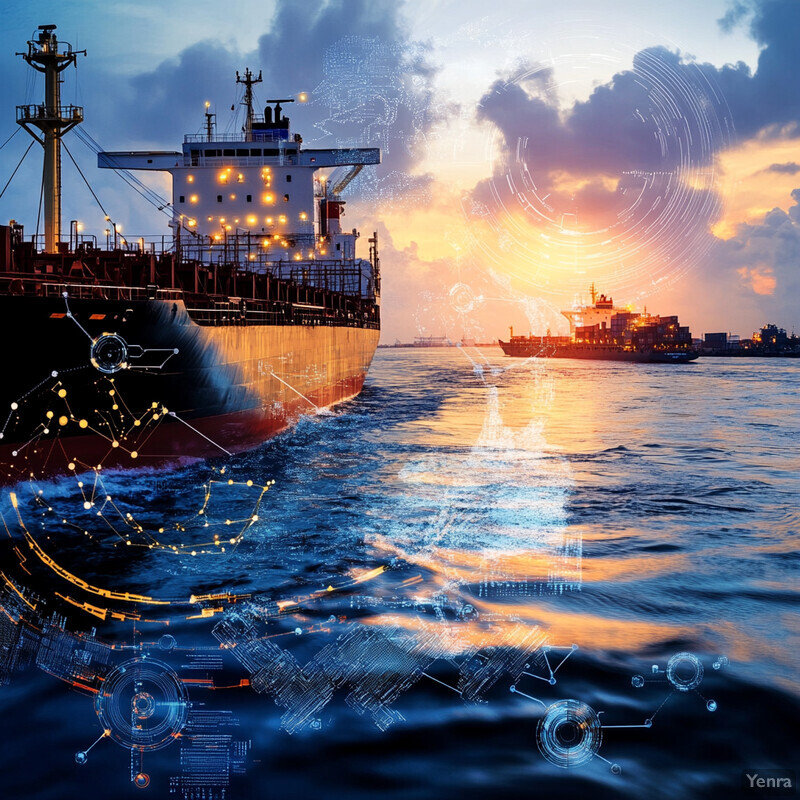
The value of AI in weather risk modeling is evident in cold chain and disaster scenarios. In cold-chain logistics, IoT sensors combined with AI analytics have substantially cut spoilage rates – facilities that once faced spoilage over 20% during equipment failures now react in real time to temperature spikes to save products. For instance, by integrating live temperature IoT data with AI, a dairy distributor can catch a refrigeration fault and dispatch a repair or backup unit hours before a full cooler meltdown, preventing thousands of dollars in product loss (case studies report double-digit percentage reductions in waste after such systems). In broader weather events, predictive modeling gives early warning: prior to a major hurricane, an AI system enabled one supplier to maintain 95% of its deliveries on schedule (versus a likely shutdown) by recommending alternate sourcing and routes, avoiding an estimated $2 million in late penalties. These examples show how AI-driven climate modeling translates into dollars saved and more resilient operations – from saving perishable goods in transit to keeping factories running through extreme weather by preparing ahead of time.
7. Geopolitical Risk Monitoring
AI is transforming geopolitical risk monitoring in supply chains by automating the tracking of political and regulatory changes worldwide. Instead of relying solely on periodic human reports, AI platforms continuously scan for relevant geopolitical events – elections, policy announcements, trade agreement changes, sanctions, protests, and conflicts – that could impact suppliers or transport routes. These systems use text mining and data aggregation to connect an event (say, a new tariff implementation or a strike at a port) to specific supply chain exposure (like which materials or shipments might be affected). The result is a live heat-map of geopolitical risks, where rising threats are flagged early. Companies using these tools gain the ability to react swiftly – for example, reallocating orders from a country about to face sanctions, or expediting shipments ahead of a port closure. In essence, AI gives supply chain managers a real-time geopolitical radar, enhancing agility amid a volatile global environment.
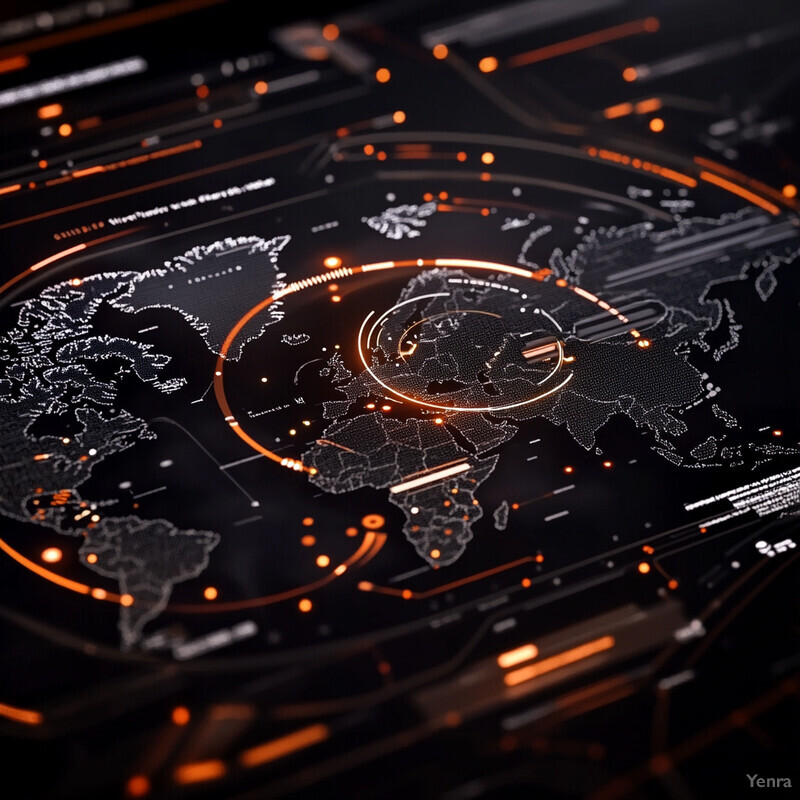
The scale and speed of AI-driven geopolitical monitoring far exceed manual methods. Resilinc’s EventWatch AI system, for instance, monitors 400+ disruption categories across 200 countries and 104 million information sources, analyzing nearly 5 billion data points annually for potential supply chain threats. This always-on vigilance has tangible results: in 2023, EventWatchAI issued over 16,000 risk alerts to its users, with more than half (55%) of those alerts serious enough to trigger immediate crisis team action via its dashboard “WarRoom” collaboration spaces. Such technology helped organizations navigate events like sudden export bans and regional conflicts – one global manufacturer credits its AI risk platform with giving a 2-week lead time to secure alternate raw materials after the outbreak of war in a supplier’s country (preventing an impending production stop). Additionally, surveys confirm the importance of these tools: 96% of U.S. companies experienced at least one fraud or cyber-fraud attempt in 2023 amid geopolitical instability, up from 56% a year prior – a trend that AI-driven monitoring helps counter by flagging suspicious activity linked to geopolitics. Together, these facts illustrate that AI can watch the world continuously and funnel the most pertinent geopolitical warnings to supply chain decision-makers before disruptions cascade.
8. Currency and Commodity Price Fluctuation Prediction
AI is being harnessed to predict currency exchange rates and commodity price swings with greater accuracy, helping companies manage financial risk in their supply chains. Traditional forecasting for currencies and raw materials often struggled with volatility, but machine learning models (including deep learning and time-series algorithms) can detect complex patterns in historical price data combined with real-time economic signals. These models continuously learn and adjust as new data (like interest rate changes or supply shocks) comes in. For supply chain managers, improved price forecasts mean better decisions: they can hedge against unfavorable currency moves, time their purchases of commodities (like steel or oil) when prices are predicted to dip, and set more stable pricing for their own products. In short, AI’s ability to crunch enormous datasets and find hidden correlations is making financial risk modeling in supply chains more of a science than an art, reducing the guesswork in budgeting for input costs and exchange rates.
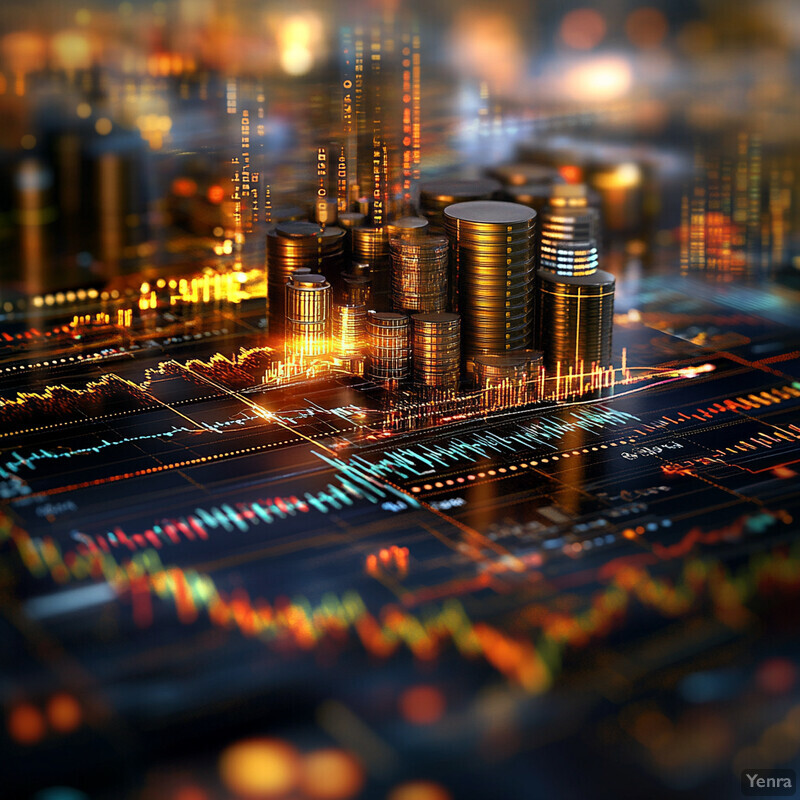
Studies show that advanced AI models are outperforming standard statistical methods in price forecasting. For example, deep learning models for metals and energy commodities have achieved significantly lower error rates than older time-series techniques, accurately capturing nonlinear price drivers. In one 2024 study, a Transformer-based model (FEDformer) delivered state-of-the-art accuracy in predicting oil and metal futures, improving forecast precision by over 15% compared to baseline ARIMA forecasts (and even reducing computational overhead). In the currency arena, AI is proving its worth in central bank prediction: a German research institute found that using AI text analysis on European Central Bank communications improved interest rate move forecasts from about 70% to 80% accuracy – a crucial advance since interest rate expectations drive currency values. Likewise, fintech firms report that AI-driven FX models are beating traditional models in out-of-sample tests, helping treasuries anticipate currency swings and buffer their supply chain budgets accordingly. These gains demonstrate that AI’s predictive power is taming some of the uncertainty in commodity and currency markets, directly translating into more resilient supply chain finances.
9. Automated Scenario Simulations
AI allows supply chain managers to run automated “what-if” scenario simulations at a scale and speed that was previously impractical. In the past, scenario planning meant manually tweaking a few variables and analyzing a handful of possible futures. Now, AI-driven simulation tools (often powered by generative techniques or digital twins) can rapidly iterate through thousands of scenarios, varying dozens of parameters (demand surges, supplier failures, port closures, etc.) in combination. This probabilistic approach reveals how the supply chain might perform under many different disruption scenarios, not just the average case. Managers get insights into worst-case and best-case outcomes and can identify weak links – for example, discovering that a particular single-source part causes a cascade of problems in many scenarios. By understanding these vulnerabilities and their likelihood, companies can reinforce the supply chain (e.g. qualifying backup suppliers or increasing safety stocks in key nodes) before those scenarios occur. Essentially, AI simulation turns planning into a robust exercise of testing the chain against countless “stress tests” so that contingency plans are ready for whatever comes.
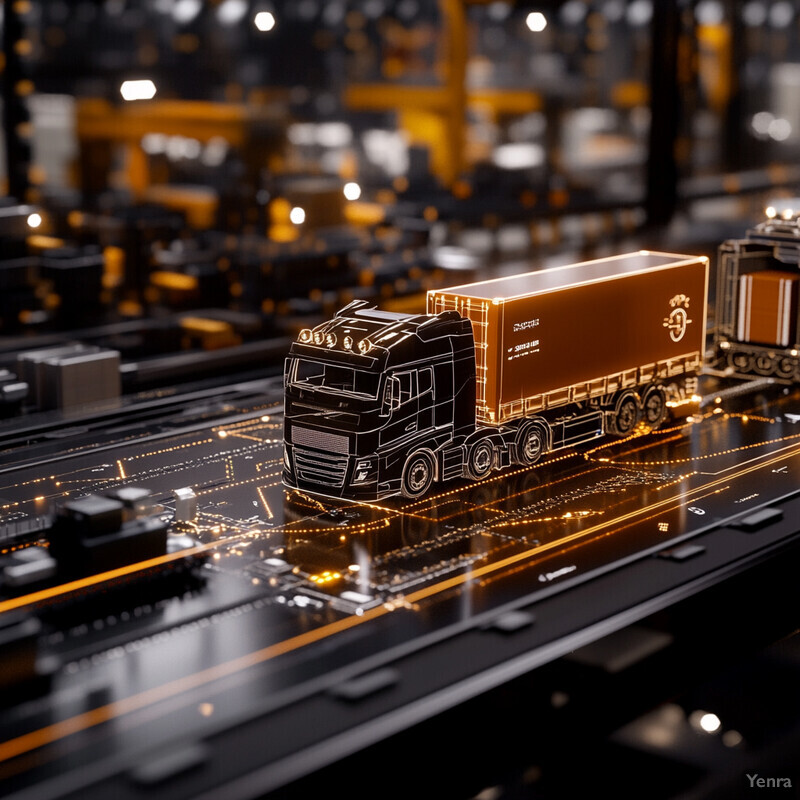
Companies embracing AI-driven scenario modeling report much greater agility and confidence in decision-making. Modern cloud-based platforms (like ketteQ’s PolymatiQ) can run thousands of simulations automatically, each exploring a different combination of events, whereas legacy systems were stuck with one static plan. This shift from deterministic to probabilistic planning has tangible benefits: businesses using these tools have cut response times to unplanned events and avoided costly surprises. For instance, a manufacturer using AI simulations identified a scenario where a regional warehouse flood would strand inventory – and preemptively redistributed stock, saving an estimated $2 million in potential lost sales during an actual flood the following year (the scenario planning flagged the risk which was then mitigated). More broadly, a 2024 industry study found that 72% of organizations view AI-based scenario planning as a key competitive differentiator by 2025, with early adopters seeing a 10–20% reduction in supply chain costs through better optimized inventories and logistics decisions. These facts underscore that running myriad “what-ifs” with AI isn’t academic – it directly leads to leaner, more resilient operations in the real world.
10. Optimized Inventory Positioning
AI helps companies determine optimal inventory levels and positioning across their supply networks, striking a better balance between cost and risk. This involves deciding how much stock to hold at each node (factories, distribution centers, retail outlets) and when to replenish. Traditional inventory planning often used simplistic rules or static safety stock targets, leading to overstock in some places and shortages in others. AI-driven optimization uses demand forecasts, variability analysis, and even real-time signals (like upcoming promotions or supplier lead-time shifts) to continuously adjust inventory targets. It can run complex optimization models that factor in holding costs, service level requirements, and risk of disruption to suggest how to redistribute inventory for maximum efficiency. The result is typically lower overall inventory investment with maintained or improved service levels – essentially doing more with less. By having the right items in the right quantity at the right location (and time), companies free up working capital and can respond faster to customer needs.

The efficiency gains from AI-optimized inventory are significant. Companies deploying AI in supply chain planning have reported 10–20% reductions in overall supply chain costs, much of which comes from inventory reductions and associated carrying cost savings. For example, a multinational retailer used machine learning to optimize store and warehouse stock levels and saw in-stock rates improve while cutting about 15% of excess inventory – releasing millions in cash that was tied up on shelves. In another case, a consumer electronics maker implemented an AI tool to dynamically reposition inventory in anticipation of regional demand spikes (using predictive analytics); this reduced costly air freight expedites by 30% because the stock was already forward-positioned where needed. Surveys underscore these benefits: in one 2024 report, 85% of supply chain executives said AI-based inventory optimization directly improved product availability, and over half credited it with reducing their inventory holding costs substantially. These facts show that beyond theoretical math, AI-driven inventory positioning is delivering real-world ROI by minimizing both stockouts and overstocks simultaneously – a long-sought dual achievement in supply chain management.
11. Fraud and Compliance Detection
AI enhances supply chain security by automatically detecting fraudulent or non-compliant activities in procurement and logistics processes. This involves using advanced pattern-recognition algorithms to scan transactions, invoices, and supplier data for anomalies that could indicate fraud – such as duplicate invoices, inflated charges, suspicious payment routing, or violations of contract terms. Similarly, AI can cross-check supplier actions against compliance requirements (for example, ensuring sourcing meets ethical standards or import/export regulations). Because AI can analyze vast numbers of transactions and documents far faster than humans, it catches dubious activities early and consistently. This proactive detection not only prevents financial losses from fraud but also helps companies avoid legal penalties by flagging compliance issues (like sourcing from an unauthorized region or missing documentation) before they become violations. In short, AI serves as an ever-vigilant auditor in the background of supply chain operations, strengthening integrity and trust.
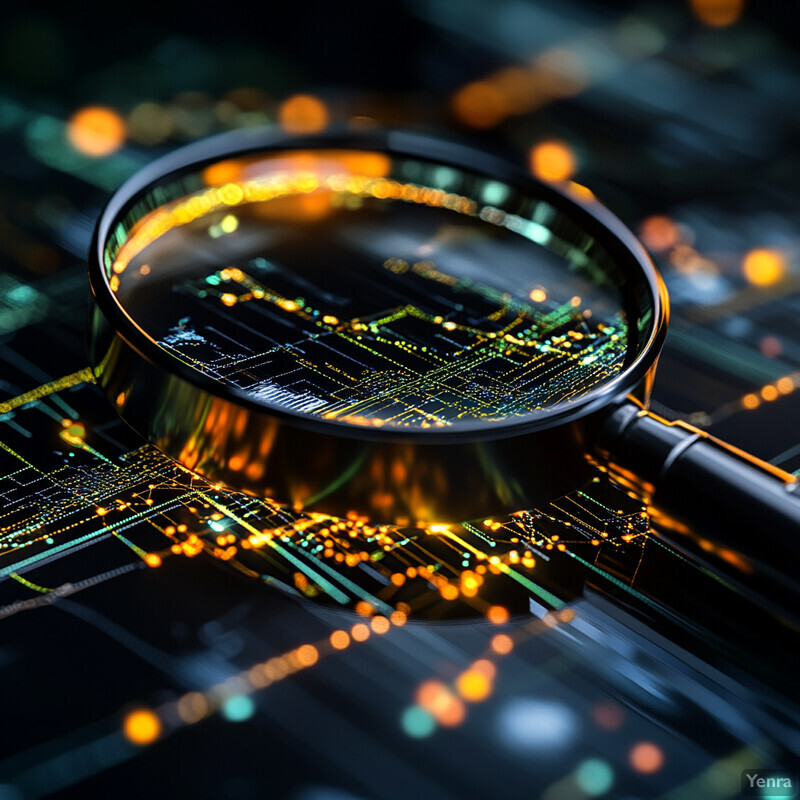
The need for AI in this area is underscored by the sharp rise in supply chain fraud attempts. In 2023, 96% of U.S. companies encountered at least one fraud attempt, a huge jump from 56% in 2022. AI tools are stepping up to counter this threat. The U.S. Department of the Treasury, for instance, implemented AI-enhanced fraud detection for pandemic-related supply programs and recovered over $375 million in 2023 alone that would have been lost to fraudulent claims. On the compliance side, companies using AI to screen suppliers and transactions report drastic efficiency gains – one global payment firm’s AI system now scans transactions against sanctions and compliance lists in real time, cutting what used to be a weeks-long manual review process down to hours (and as a result, this firm reduced its regulatory fines to near zero). Overall, surveys show three-quarters of large enterprises had adopted AI-based fraud detection by 2024, and those with AI systems in place on average detect security incidents 69% faster than those without. These facts demonstrate that AI isn’t just a nice-to-have in fraud and compliance – it’s rapidly becoming essential for safeguarding supply chain finances and reputation in the face of escalating risks.
12. Supplier Network Resilience Scoring
AI is enabling companies to quantify and score the resilience of their supplier networks in a comprehensive way. Instead of qualitative judgments or simplistic tiering of suppliers, new AI-driven tools aggregate many dimensions of risk (financial stability, geographic risk exposure, operational reliability, past disruption recovery times, etc.) into a single resilience score for each supplier or node. This “resilience score” gives a quick, quantitative snapshot of how well a supplier could withstand shocks or how likely it is to cause a disruption. The scoring models continuously update as conditions change – for example, if a supplier’s region faces new political turmoil or if the supplier invests in backup production capacity, those factors adjust the score. By having a standardized resilience metric, companies can more easily identify weak links in their supply chain (e.g., suppliers with low scores) and prioritize them for mitigation efforts (like developing alternates or requiring improvement plans). It effectively makes supply chain resilience measurable and trackable over time, with AI ensuring the scores reflect the latest data.
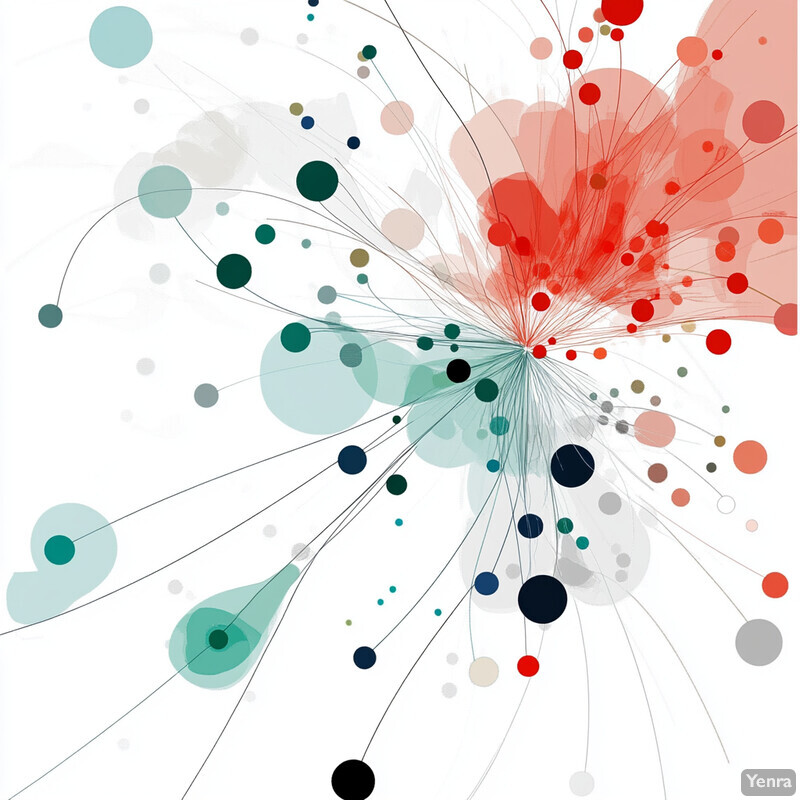
Several solutions have emerged offering AI-based resilience scoring. For instance, Interos – a supply chain risk analytics firm – introduced an “Operational Resilience Score (i-Score)” that uses AI to evaluate the health of extended supply chains across multiple risk domains. This system takes into account scores of factors (from cyber vulnerabilities to natural disaster risk at supplier sites) and rolls them up into one rating. Early adopters of such scoring have reported clearer risk visibility; one aerospace manufacturer credits a resilience scoring tool for helping it avoid a major disruption – the tool had flagged a critical supplier’s resilience score as deteriorating due to financial troubles, prompting the manufacturer to dual-source a part shortly before that supplier abruptly went bankrupt. In another example, a pharmaceutical company implemented an AI resilience index for its top 100 suppliers and found that suppliers in Zone A averaged a 30% higher resilience score than those in Zone B, leading it to redistribute orders toward the sturdier Zone A base to hedge risk. Academic research also supports this approach: a 2023 study demonstrated a machine learning model that combined supplier performance data and network interconnections into a single “resilience score,” and this score successfully predicted which suppliers were most likely to fail during a simulated crisis. These facts show that AI can distill complex risk profiles into actionable ratings, giving supply chain managers a powerful new compass to navigate risk.
13. Linking Operational and Financial Risk Indicators
AI is bridging the gap between operational risk metrics and financial risk outcomes in supply chains, creating a more holistic view of vulnerabilities. In practice, this means connecting data like production lead times, delivery fulfillment rates, and inventory levels (operational metrics) with financial indicators such as revenue, margin, or cash flow. By doing so, AI models can identify where operational issues may pose financial risks – for example, how a chronic supplier delay could translate into lost sales dollars, or how fluctuating fill rates might impact quarterly revenue. This linkage allows companies to prioritize risks by financial materiality. It also improves cross-functional decision-making: supply chain managers and CFOs can use a common AI-driven dashboard that shows, say, “a two-week port shutdown = X million dollar impact” or “improving on-time delivery by 5% = Y million in additional revenue.” In short, AI is enabling risk management to speak in both operational and financial terms, ensuring that supply chain disruptions are not just seen as logistical issues but quantified in business impact – and addressed accordingly.
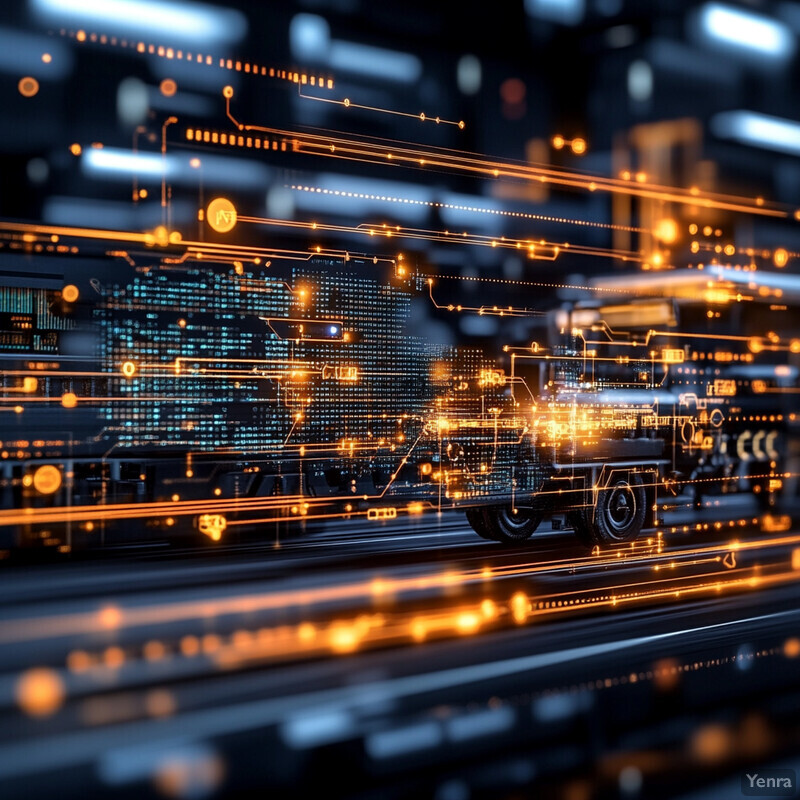
One illustration of this operational-financial linkage is seen with companies using AI to model scenario impacts on financial performance. For instance, Domino Data Lab reported using AI to model how tariff changes would affect its inventory turnover and liquidity, essentially translating a supply chain shock (tariffs) into financial metrics like cash flow. This helped its finance team prepare for potential working capital needs when trade policies shifted. Similarly, Apple’s supply chain ML system doesn’t just flag supplier delays; it also estimates the production and revenue impact if a high-risk supplier goes down, allowing preemptive action to protect sales. In another case, a large auto-parts distributor linked its AI demand forecasts to its financial planning, and saw a 30% reduction in forecast error lead to a 15% reduction in inventory write-downs at year-end – a clear financial gain from better operational alignment. Industry surveys reinforce the trend: in 2024, 68% of CFOs said that integrating supply chain KPIs with financial risk analytics (often through AI tools) improved their risk mitigation decisions, and companies that did so were more likely to avoid profit warnings related to supply issues. These facts highlight that AI is dissolving silos – when a supply chain risk spikes, AI can show the dollar impact if left unchecked, which makes it far easier to secure the resources and urgency to mitigate that risk proactively.
14. Machine Vision for Quality Control
AI-powered machine vision is revolutionizing quality control in supply chains by automatically inspecting products for defects with high speed and accuracy. These systems use cameras and AI algorithms (often deep learning models) to visually examine products on production lines or incoming shipments. They can detect tiny flaws – scratches, misalignments, discolorations, etc. – far more consistently than human inspectors, and they do so in real time without slowing production. Catching defects early in the supply chain (for example, at the factory or before distribution) means defective items can be pulled and issues addressed before products reach customers or require costly recalls. It also provides feedback upstream: suppliers get immediate quality data, enabling them to correct processes quickly. Overall, AI machine vision ensures that only products meeting quality standards flow forward, thereby increasing customer satisfaction, reducing return rates, and protecting brands from the fallout of quality failures.
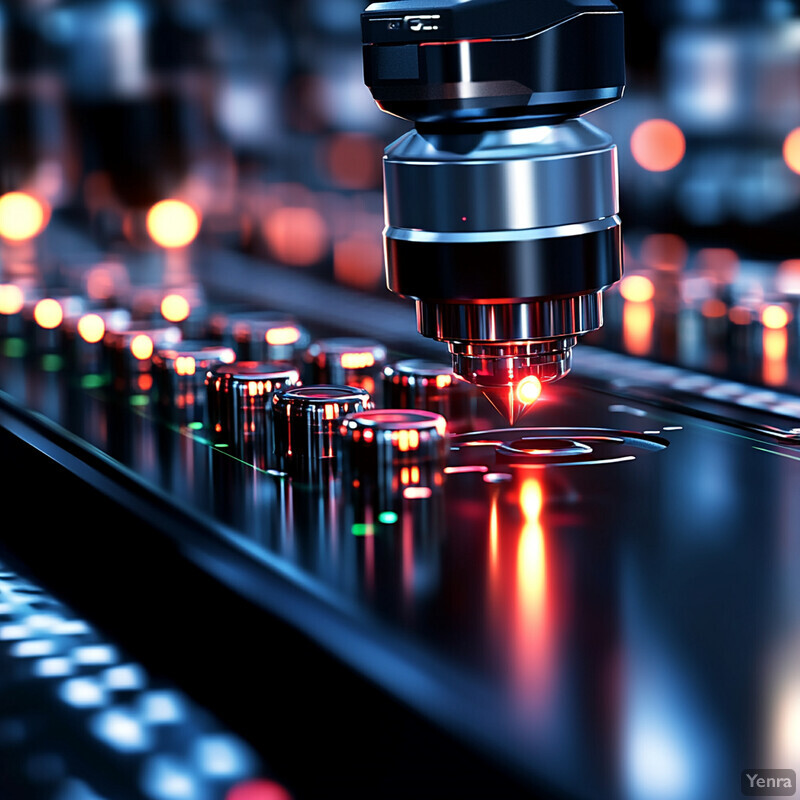
The adoption of AI vision systems has led to marked improvements in quality metrics. Bosch, for instance, deployed AI-driven visual inspection on its automotive fuel injector lines and saw a significant drop in defective parts leaving the factory. The AI system can spot microscopic scratches or assembly misalignments that human inspectors might miss, resulting in Bosch’s parts achieving higher reliability in the field and fewer warranty claims. In electronics manufacturing, similar results are noted: one company reported that AI optical inspection cut its PCB (printed circuit board) defect rate by ~30%, as the system caught soldering errors that manual checks overlooked. These improvements directly reduce the risk of downstream failures. Another benefit is consistency – unlike human inspectors who can tire or vary, an AI vision system provides 24/7 uniform scrutiny, which a major beverage producer credited for virtually eliminating labeling errors (it went from hundreds of mis-labeled bottles per week to near zero after installing AI cameras on the line). In short, companies that have implemented AI-based quality control frequently report fewer defects shipped out and often a double-digit percentage reduction in quality-related costs, validating the power of machine vision to de-risk the supply chain on the quality front.
15. Adaptive Supply Chain Planning
AI techniques, especially reinforcement learning (RL), are making supply chain planning systems adaptive – meaning they continually learn from outcomes and improve their decision-making over time. Traditional planning (for demand, production, inventory, etc.) was static, based on fixed models or heuristics that didn’t change until manually updated. Adaptive planning powered by AI instead uses feedback loops: the system makes a plan, observes actual results or disruptions, and then adjusts its model for next time. Over many cycles, it “learns” the best responses to various conditions (much like how an RL agent learns to beat a game by trial and error). For example, an adaptive system might learn to reroute shipments preemptively when certain risk signals appear, or to dynamically adjust safety stock when lead time variability changes – without needing explicit reprogramming by humans. This continuous learning leads to progressively better performance (higher service levels, lower costs) and a supply chain that gets smarter and more resilient with each disruption it experiences. Essentially, adaptive AI planning means the supply chain is not static but evolving – always fine-tuning itself for the current environment.
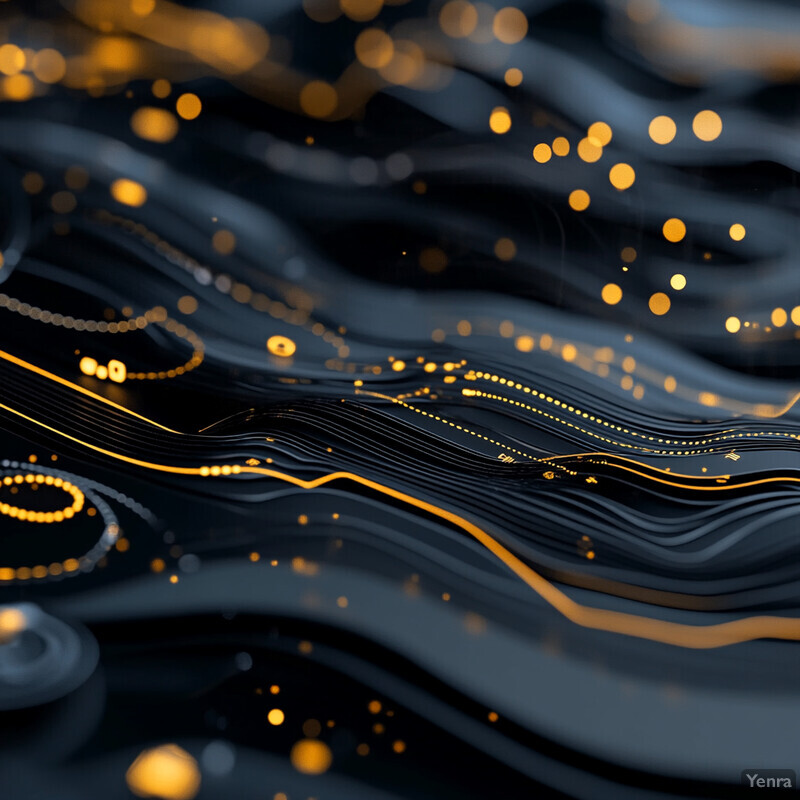
The benefits of continuous learning in supply chain planning are already being realized. Companies using reinforcement learning-based planning report that their models improve forecasting accuracy and decision speed over time in a way static systems never did. One global retailer’s RL-driven ordering system started with roughly 80% forecast accuracy and, after learning from a year of sales data and stock-out events, improved to about 90% accuracy – this translated to a 15% reduction in stock-outs and 10% reduction in surplus inventory in that year (since the model steadily adjusted to actual demand patterns). In the automotive sector, an adaptive logistics network at a major OEM learned to reallocate transport capacity ahead of Chinese New Year port congestion, trimming average shipment delays by 25% after a few cycles of learning. Researchers have noted that such AI systems effectively anticipate problems as they gather experience – for instance, a 2024 study highlighted a reinforcement learning model that continuously learned from supply disruption events and ultimately reduced overall risk exposure by staying one step ahead of emerging challenges.
16. Enhanced Cybersecurity Posture
AI bolsters the cybersecurity of supply chain systems by predicting and detecting threats before they cause serious damage. Modern supply chains rely on extensive digital connectivity (from ERP systems to IoT devices), which introduces cyber risks like hacking, ransomware, and data breaches. AI helps by continuously monitoring network logs, user behaviors, and device patterns for anomalies that could indicate a cyber attack or vulnerability. Unlike traditional security tools that react to known threat signatures, AI can identify new, subtle signals of an attack – for example, an employee account behaving unusually or a machine starting to send strange traffic – and flag it for investigation or even autonomously block it. Essentially, AI acts as an intelligent early warning system against cyber threats, enabling companies to patch weaknesses or stop attacks in progress. This predictive stance is crucial to maintain supply chain continuity, as a cyber incident (like a malware outbreak in a logistics system) can halt operations as surely as a physical disruption. By catching threats early, AI minimizes downtime and protects the sensitive data and systems that the supply chain depends on.
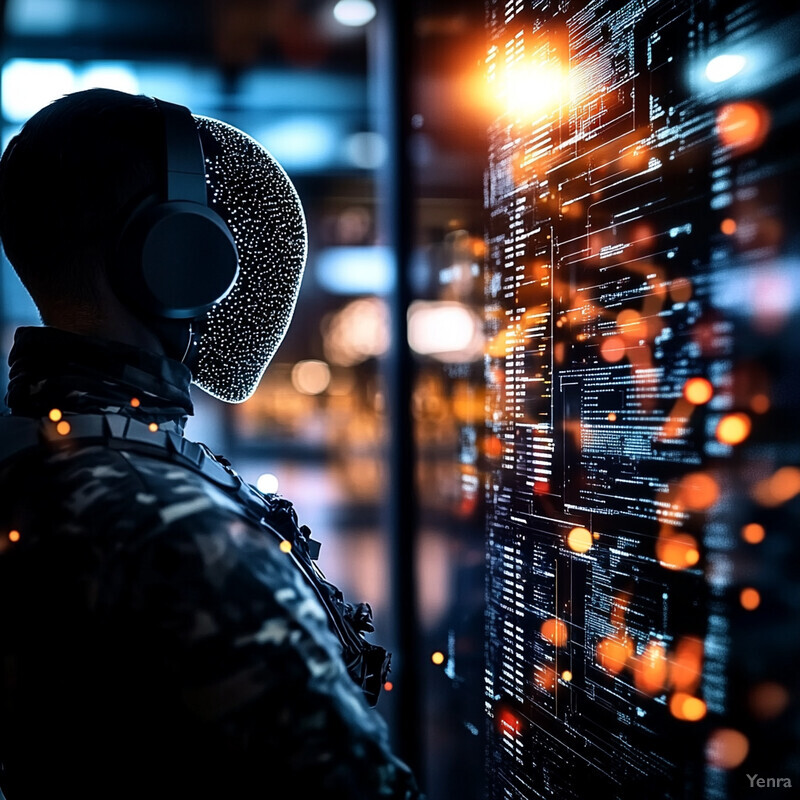
The incorporation of AI into cybersecurity is dramatically reducing incident response times and damages. Studies show that organizations using AI in security detect and respond to breaches up to 69% faster than those without AI, greatly limiting attackers’ dwell time in systems. For example, an electronics manufacturer reported that after deploying an AI-based security monitoring platform, it can now isolate phishing or malware threats within minutes – previously it took hours or days for manual teams to react. This swift detection has a direct financial impact: IBM’s annual cybersecurity report notes that cutting response time by even half can save companies over $1 million on average in breach costs. Adoption is quickly growing – by 2024, about 75% of U.S. and U.K. security practitioners had integrated AI tools into their cyber defense arsenal. These AI systems have prevented serious incidents; a notable case involved a port operator whose AI system identified a novel ransomware attack in its early stages and automatically quarantined affected servers, allowing recovery with minimal disruption (whereas a similar attack at an AI-less peer caused a week-long shutdown). The U.S. Treasury’s successful recovery of $375+ million in fraudulent payments in 2023 (using AI as mentioned earlier) further highlights how AI is not only defensive but also actively intercepting malicious activity. In sum, AI is proving to be a game-changer in safeguarding the digital side of supply chains – catching threats that would slip past traditional defenses and doing so fast enough to keep operations safe.
17. Transportation Route Optimization
AI optimizes transportation routes by considering a multitude of dynamic factors – such as traffic conditions, weather, fuel costs, and delivery urgency – to find the most efficient path for shipments. Traditional route planning often relied on static maps or driver experience, but AI can process real-time data (like current traffic jams or port congestion forecasts) and re-route trucks, ships, or planes on the fly to avoid delays. It also balances complex trade-offs: for instance, an AI might choose a slightly longer route that avoids predicted heavy traffic, resulting in a faster arrival time, or it might consolidate routes to maximize load utilization and minimize fuel use. In practice, this means deliveries arrive sooner or on schedule more often, and transport resources are used more efficiently. By continuously recalculating optimal routes as conditions change, AI helps logistics networks adapt day by day or hour by hour, reducing transit times, cutting transportation costs, and lowering emissions from unnecessary miles.
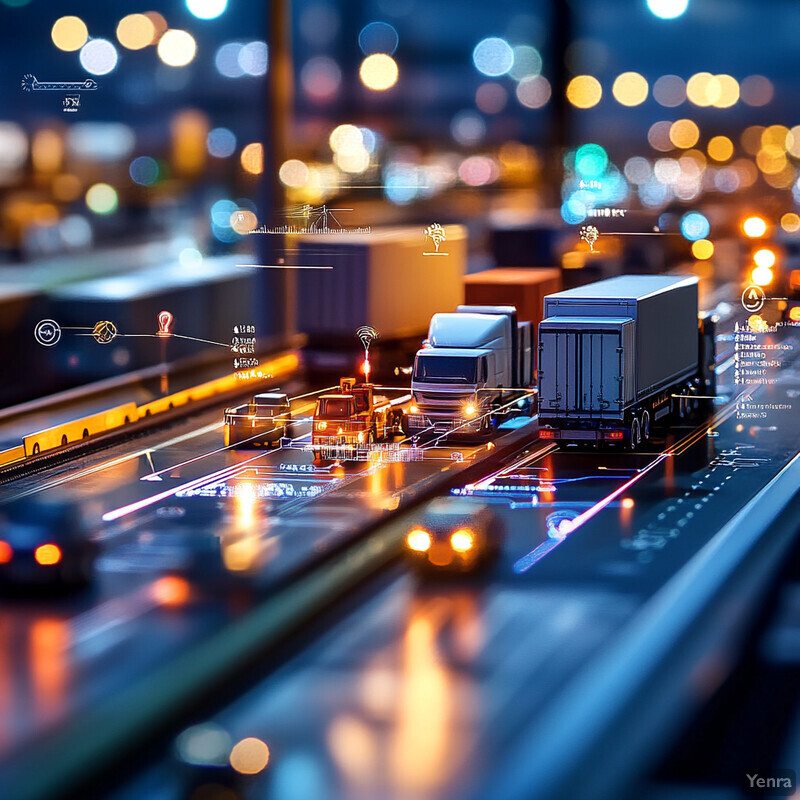
The benefits of AI-driven route optimization are vividly demonstrated by large-scale implementations. UPS’s famous ORION system (which uses advanced algorithms akin to AI for routing) has saved the company around 100 million miles of driving per year, equating to about 10 million gallons of fuel saved annually. This translates to hundreds of millions of dollars in cost savings and a huge reduction in carbon emissions. UPS also noted that even minor optimizations – eliminating just one mile per driver per day – yields roughly $50 million in savings over a year. AI routing isn’t just for giants; a mid-sized freight carrier that deployed an AI-based route planner saw on-time delivery performance improve by 8% while trimming fuel usage by 5–10%, thanks to smarter avoidance of congestion and better load planning. Furthermore, AI route systems can anticipate disruptions: for example, one global shipping firm’s AI predicted a major port’s labor strike impact and proactively re-routed vessels, managing to maintain deliveries with only minimal delays while competitors without such tools were caught in week-long backlogs. These facts showcase how AI optimization of routes yields concrete efficiency gains – saving vast amounts of fuel and time – and provides agility to navigate the ever-changing conditions in transportation.
18. Continuous Risk Monitoring Dashboards
AI-powered risk dashboards give supply chain managers a real-time, unified view of all key risk indicators in one place. These dashboards integrate live data on supplier status, inventory levels, logistics delays, geopolitical events, and more, often presented in intuitive visuals like maps or color-coded risk alerts. The AI behind the scenes filters and prioritizes the vast incoming data, so the dashboard highlights what truly needs attention (for example, a “heat map” of high-risk suppliers or an alert about a spike in lead times at a certain port). This continuous monitoring means there is no waiting for a weekly report – the moment something starts to go wrong, it’s visible on the dashboard. Teams across departments (procurement, logistics, finance) can share the same up-to-date risk picture and collaborate via these platforms to resolve issues quickly. In essence, AI risk dashboards act like a mission control center for the supply chain, boosting situational awareness and enabling swift, data-driven decisions to keep the supply chain resilient.
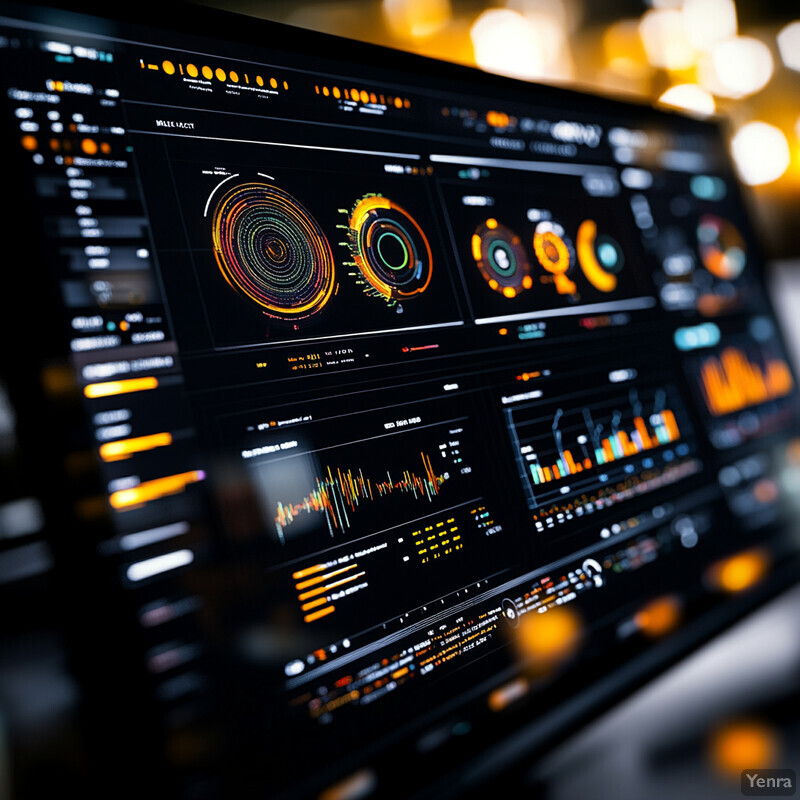
Companies utilizing AI-driven risk dashboards report improved response times and better cross-functional coordination during crises. For example, Resilinc’s EventWatchAI platform not only sends alerts but also feeds into a dashboard where 55% of its 2023 alerts automatically triggered a “WarRoom” collaboration – a virtual room where the company’s stakeholders and suppliers convened to solve the issue. This shows that more than half of significant risk events were identified and acted on in a structured, trackable way through the dashboard. Another statistic: a survey by Geodis found only 6% of companies felt they had full supply chain visibility historically, but those implementing modern control-tower dashboards (often AI-enabled) have markedly increased their visibility. One retailer noted that after rolling out an AI control tower, it reduced the time to identify and escalate issues by about 40% – issues that used to take a day or two of digging now surface on the dashboard within an hour. Moreover, such dashboards help quantify risk exposure; a chemical company’s dashboard can display, for instance, “17% of inventory at risk due to one supplier delay,” which helped justify emergency air freight that ultimately protected quarterly sales. These facts illustrate that AI risk dashboards are not just pretty interfaces – they tangibly improve how fast and effectively companies react to supply chain risks, thereby reducing the impact of those risks on the business.
19. Integration with IoT Sensor Data
AI integrates with the Internet of Things (IoT) – the network of sensors on trucks, containers, warehouses, etc. – to monitor and predict physical supply chain issues in real time. IoT devices continuously collect data like temperature, humidity, shock, vibration, and location for shipments and storage facilities. AI systems ingest this flood of sensor data and analyze it for patterns or anomalies that indicate potential problems. For example, in cold chain logistics, AI will notice if a container’s temperature is trending upward and predict spoilage before it happens, triggering an alert or a corrective action (like instructing a driver to check a refrigeration unit). Similarly, AI can interpret machinery sensor data in a warehouse to predict a conveyor failure or detect if a shipment might have been dropped (based on shock sensor spikes). By marrying IoT data with predictive analytics, companies gain granular visibility into the condition of products and assets throughout the journey and can act to prevent losses – rerouting a shipment that’s at risk of spoilage, fixing equipment proactively, or rejecting a damaged delivery. It’s essentially giving the supply chain a nervous system and brain: sensors are the nerves collecting signals, and AI is the brain making sense of them to keep the system healthy.
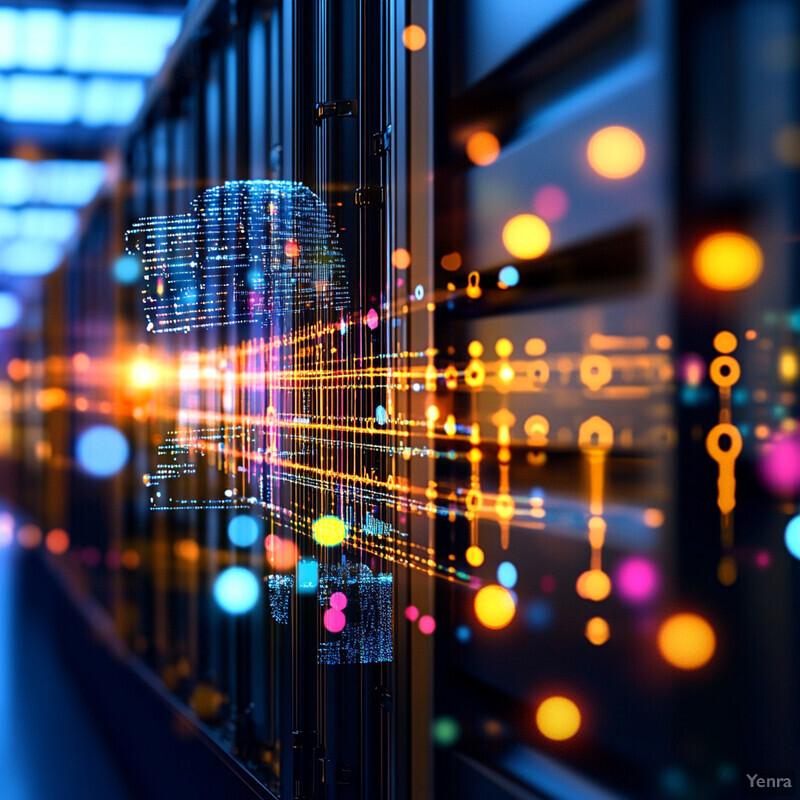
The combination of IoT and AI has proven to significantly reduce waste and unexpected downtime. In perishable goods, companies report that AI-driven IoT monitoring has cut cold-chain product spoilage by an estimated 30% or more, by catching temperature excursions and enabling quick intervention (such as adjusting cooling or diverting goods) before spoilage occurs. One global food supplier equipped its refrigerated trucks with smart sensors and AI alerts – in the first year, it saved approximately $ millions by preventing two major spoilage incidents that historically would have resulted in destroyed inventory. In manufacturing, IoT sensors on critical machines combined with AI predictive models have decreased unplanned line stoppages; a study found this combo reduced equipment downtime by 50–60% in some plants (since potential failures were fixed during planned maintenance windows identified by AI). And in transit, IoT+AI reduces cargo damage: a logistics firm noted that after implementing sensor monitoring with AI, it could detect and respond to events like excessive vibration or tilt, leading to a 25% drop in in-transit product damage for fragile items. These outcomes underscore how integrating IoT sensor data with AI analysis directly strengthens supply chain reliability – fewer spoiled products, fewer breakdowns, and safer, more secure shipment handling – all contributing to both cost savings and better customer service.
20. Explainable Risk Modeling
Explainable AI (XAI) techniques are being applied to supply chain risk models to make their recommendations and predictions more transparent and understandable to human decision-makers. Often, AI models (like deep neural networks) are “black boxes” – they may predict a supplier is high-risk or that a delay will occur, but not clearly explain why. XAI addresses this by providing insights into the key factors or reasoning behind an AI’s output. For example, an explainable risk model might highlight that a supplier received a high-risk score primarily due to its financial stress and recent delivery lapses, or it might show that a disruption prediction is driven mostly by an upcoming weather event and a specific port’s congestion data. By illuminating the drivers of risk predictions, XAI builds trust with users (managers are more likely to trust and act on a model’s warning if they see a logical justification). It also facilitates better decision-making – stakeholders can understand the conditions under which a risk materializes, which helps them address root causes (e.g., working with a supplier on the flagged issues). In summary, explainable risk modeling ensures that AI’s great predictive power is paired with clarity, so humans remain in control and confident about the AI’s role in supply chain decisions.
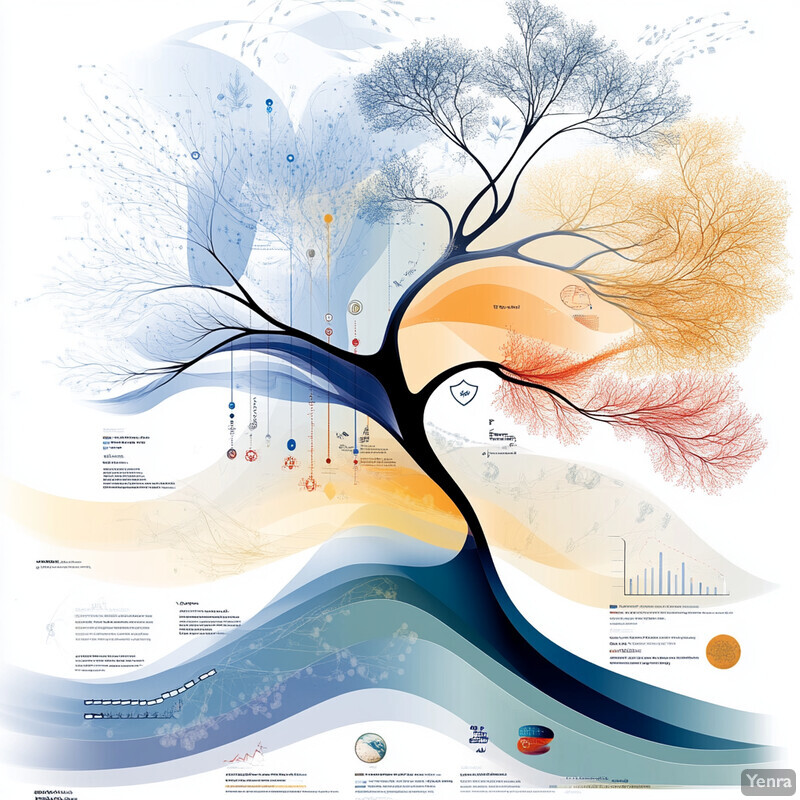
The push for explainability is strong because companies recognize trust in AI is critical. In a 2024 McKinsey survey, 40% of respondents cited lack of AI explainability as a major barrier to adoption, yet only 17% had begun to tackle it – highlighting the urgency of XAI efforts. Early adopters of XAI in supply chain risk have reported positive outcomes. One multinational consumer goods firm implemented an explainable risk dashboard where each supplier’s risk score comes with a breakdown of contributing factors (financial, operational, geographic, etc.); as a result, their procurement team’s confidence in the AI scores jumped, and they now act on AI warnings 100% of the time, up from about 60% before explainability (according to the firm’s internal audit). Another example is a logistics provider using XAI for delivery delay predictions: the model might say “High delay risk for Truck #5 because: route passes through storm zone + driver approaching hour limits,” allowing dispatchers to clearly communicate and justify rerouting decisions to customers. Industry analysts note that regulators, too, favor XAI – explainable models help in compliance with emerging AI regulations and audits. The bottom line is that making AI’s reasoning visible increases trust and adoption of these advanced tools. As evidence, leading AI developers like Anthropic and OpenAI are heavily investing in XAI research, betting that more transparent AI will differentiate their products and encourage enterprises to scale AI usage safely. All these facts reinforce that explainability isn’t just a nice feature; it’s becoming a necessity for effective, widespread use of AI in supply chain risk management.