1. Predictive Analytics for Demand Forecasting
AI-driven demand forecasting enables HVAC systems to “look ahead” and adjust proactively. By analyzing past weather, occupancy patterns, and energy usage, predictive models anticipate heating/cooling needs in advance. This helps smooth out peaks in demand – for instance, pre-cooling a building before a heat wave or dialing back during low occupancy – which maintains comfort while avoiding sudden energy spikes. In practical terms, predictive HVAC control reduces unnecessary run times and transitions equipment at optimal moments, extending system life. Over time, as the models learn from each cycle, their forecasts become even more accurate, continuously improving efficiency and reliability.
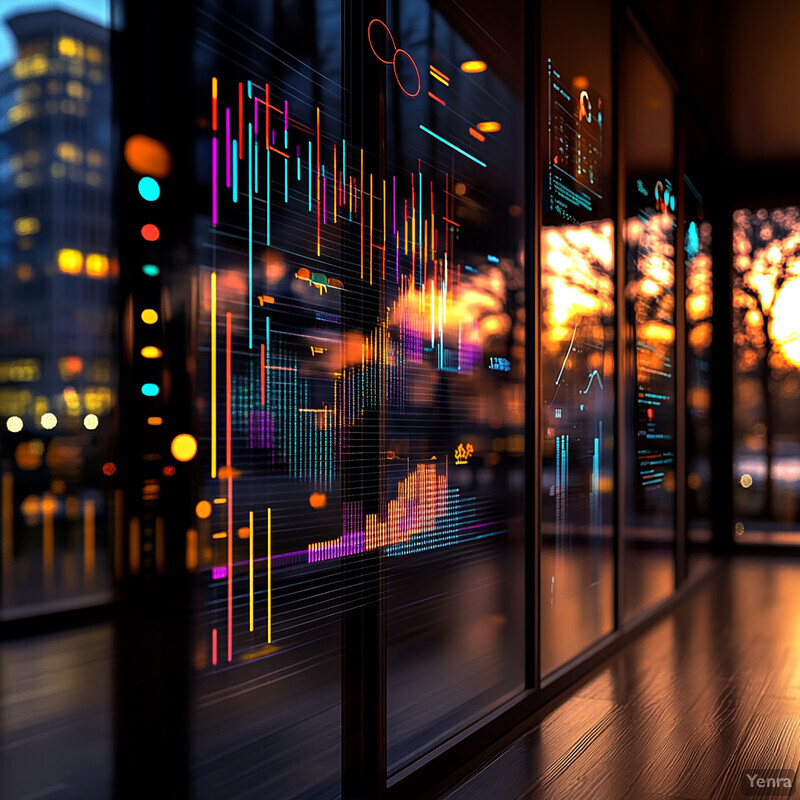
Field studies show that AI-based HVAC forecasting can yield major efficiency gains. For example, integrating local weather predictions into HVAC operations cut cooling energy use by up to 17.8% in one case. Likewise, an industry analysis found that AI-driven HVAC optimization (which uses demand forecasting) can reduce building energy consumption by up to 25%, while also cutting associated emissions by up to 40%. These results underline the substantial energy and carbon savings from predictive control.
2. Dynamic Setpoint Optimization
Dynamic setpoint optimization continuously fine-tunes HVAC temperature (and humidity) targets rather than holding static settings. By leveraging real-time inputs – current occupancy, indoor air quality, outdoor weather swings, even time-of-day energy prices – intelligent algorithms adjust setpoints on the fly. This means the system might ease off cooling slightly during an afternoon peak or pre-warm a space before people arrive, always staying within comfort thresholds. The practical benefit is a balancing act: energy is saved whenever possible without people noticing discomfort. It also reduces wear on equipment by avoiding over-correction. In essence, the HVAC system becomes responsive and context-aware, leading to both lower bills and happier occupants.
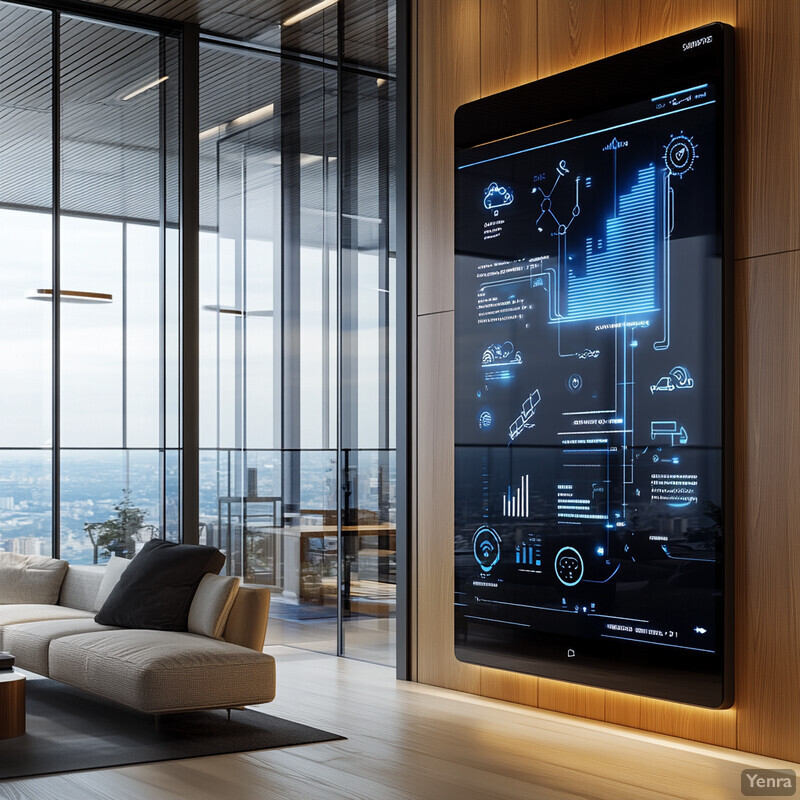
Research shows that smart setpoint strategies can unlock significant savings. In simulations across diverse buildings, optimizing thermostats and schedule “setbacks” (temperature relaxations when spaces are unused) yielded over 40% HVAC energy savings compared to fixed settings. Even more moderate field implementations often report 10–20% energy reductions from dynamic setpoint control, all while maintaining comfort. These results illustrate how continuous setpoint tweaking can dramatically improve efficiency versus one-size-fits-all operation.
3. Advanced Fault Detection and Diagnostics FDD
Advanced FDD uses machine learning and analytics to catch HVAC problems early – often before any obvious failure. By continually monitoring sensor data (temperatures, pressures, fan speeds, etc.), these tools learn the normal “signature” of HVAC operation. If something drifts off – say a chiller losing efficiency or a sensor misreading – the system flags it as an anomaly. The value is proactive maintenance: technicians get alerts for tune-ups or repairs before energy is wasted or occupants complain. In practical terms, FDD reduces surprise breakdowns and keeps systems running at peak efficiency. It also prioritizes issues (major vs. minor faults), so maintenance crews can focus on fixes that yield the biggest benefits in comfort and cost.
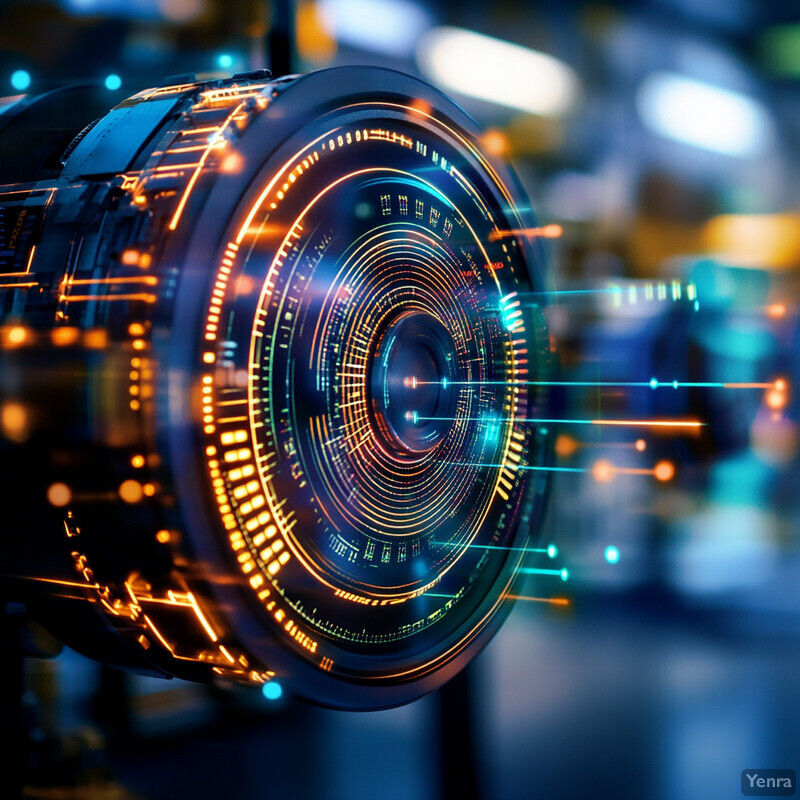
The U.S. DOE and researchers report that undetected HVAC faults are a huge source of energy waste – on the order of 5% to 30% of a commercial building’s energy use. Employing automated FDD can recapture most of that waste. For instance, a 2022 review found that implementing HVAC fault detection and diagnostics can cut energy consumption by about 20–30% on average in buildings. Early fault alerts not only save energy but also prevent costly damage – one industry survey showed predictive FDD programs yield a 10× return on investment via avoided breakdowns and efficiency gains.
4. Adaptive Control Strategies
Adaptive control means the HVAC system learns and evolves its control policies over time. Instead of fixed rules, it uses techniques like machine learning or rule-based AI that adjust based on feedback. For example, the system might learn that a particular conference room consistently overheats in the afternoon sun and start cooling it earlier, or it might discover more efficient ways to reach setpoints by trial and error (using reinforcement learning). The practical upshot is that the HVAC gets “smarter” about the building’s unique behavior and the occupants’ patterns. It continuously refines how it operates – similar to an experienced driver who anticipates road conditions – leading to optimal comfort with minimal energy. This adaptability also means the system can handle changes (like new office layouts or building expansions) with less reprogramming, since it self-adjusts to new conditions.
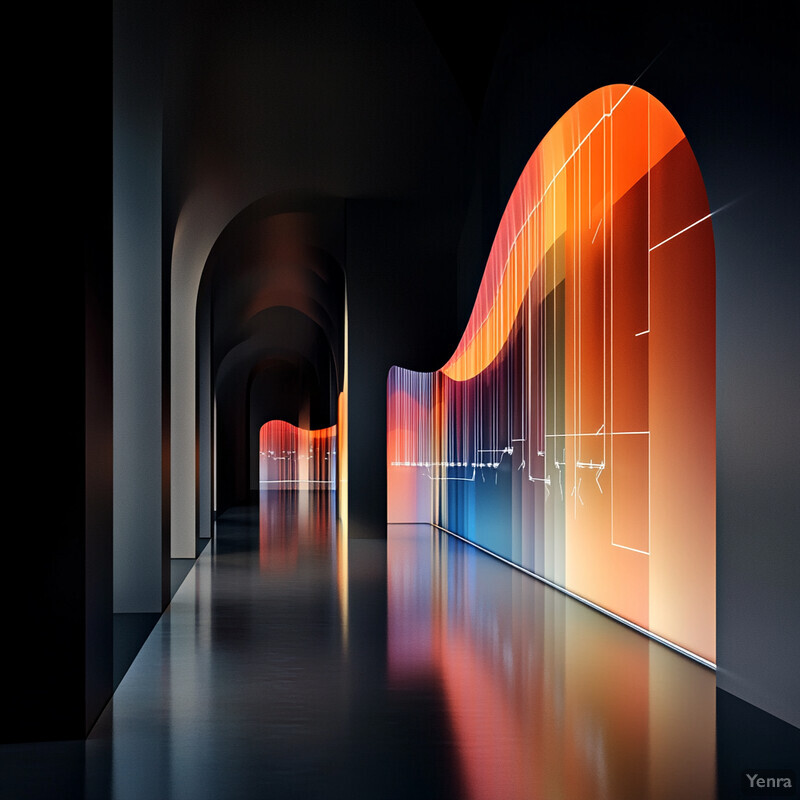
Studies indicate that adaptive HVAC controls can yield 15–30% energy savings compared to traditional static controls. For instance, recent experiments with reinforcement learning controllers showed up to 26% HVAC energy savings in simulations, and about 8–10% savings in real-world tests, relative to conventional control strategies. These improvements come while maintaining or even enhancing comfort. Such performance gains demonstrate why adaptive and self-optimizing controls are seen as a key to significantly better efficiency in buildings.
5. Occupant Behavior Modeling
Occupant behavior modeling involves predicting and responding to how people actually use the building. HVAC systems using this approach don’t treat occupancy as a fixed schedule – instead, they ingest data from motion sensors, badge systems, or even occupants’ calendars to foresee where and when people will be. Practically, this means air conditioning isn’t blasting in an empty conference room, and heating turns down when a zone is unoccupied for an extended period. By learning patterns (e.g., a certain office is usually empty by 5 PM, or only half of meeting rooms get used on Fridays), the system optimizes conditioning delivery. The benefit is a big reduction in energy wasted on empty spaces, while still ensuring comfort the moment people arrive. It effectively aligns HVAC operation in real-time with actual human presence and preferences.
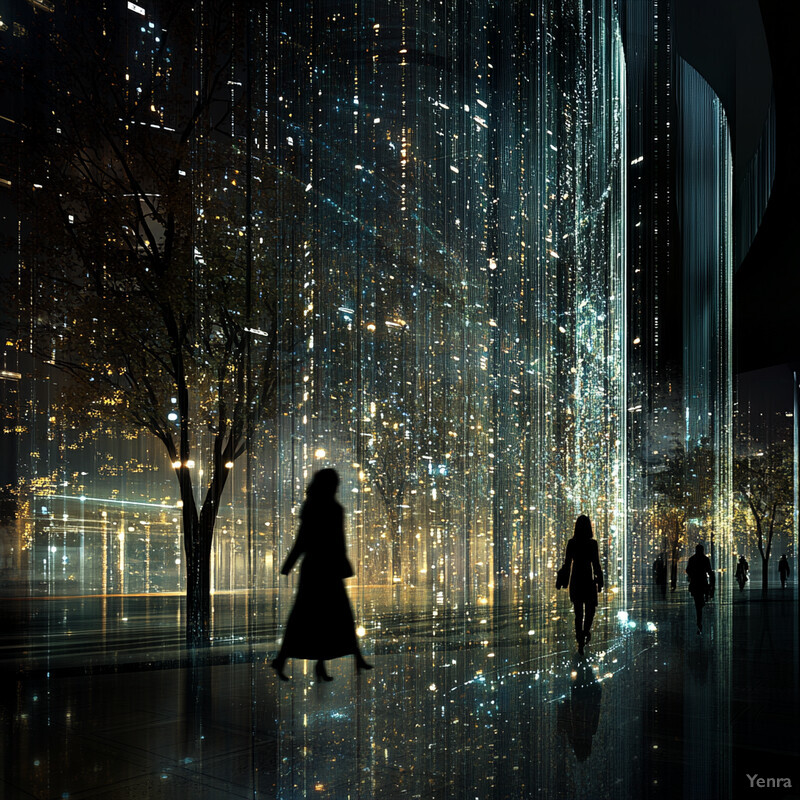
Tuning HVAC to real occupancy yields clear savings. A national laboratory analysis in 2023 found that occupancy-based HVAC controls can save about 5–15% of total building energy, depending on building type. In certain commercial scenarios, the savings can be even higher – one study noted that integrating occupancy sensors with HVAC could cut HVAC energy use by roughly 30% through smarter scheduling. On the comfort side, such modeling also reduces hot/cold complaints. Buildings that have implemented occupancy-driven control report significantly fewer comfort complaints and more consistent temperatures, since conditioning better matches where people actually are.
6. Weather-Adaptive Adjustments
Weather-adaptive HVAC control uses forecasts and outdoor sensor data to continually tweak indoor climate settings in harmony with Mother Nature. Instead of reacting after a building gets hot or cold, the system anticipates changes – for example, pre-cooling overnight before a blazing hot day, or temporarily lowering heating when a sunny afternoon will naturally warm the space. It also adjusts for humidity, storms, or cold snaps on the horizon. In practice, this means the HVAC system runs more smoothly with fewer extreme swings. Equipment ramps up or down gradually in sync with weather trends, which avoids inefficient “all at once” operation. The result is maintained comfort despite weather volatility, with less energy waste, since the system captures free benefits (like cool night air) and mitigates weather-related inefficiencies proactively.
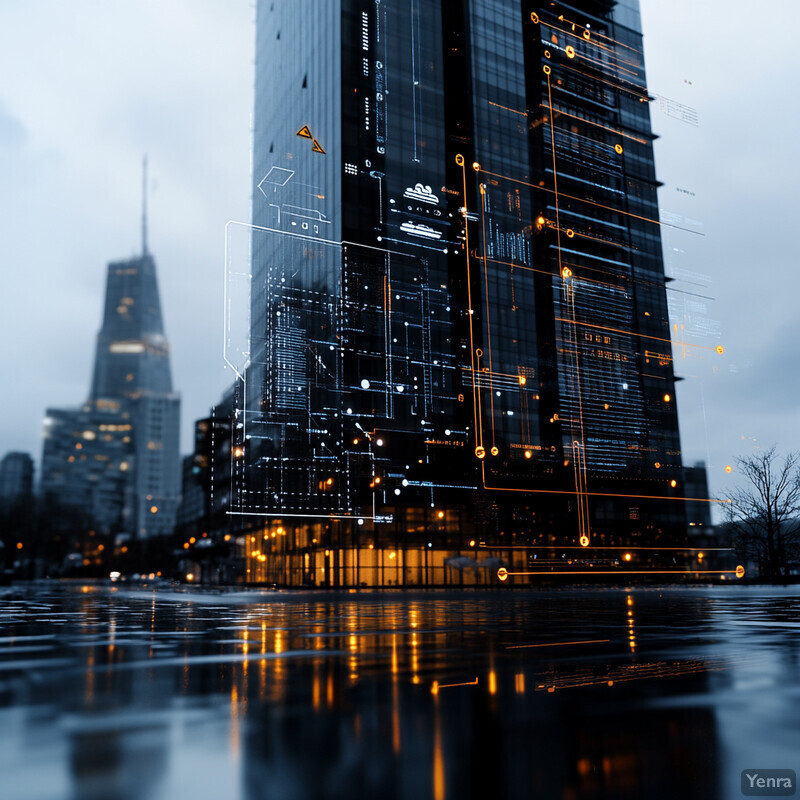
Incorporating weather forecasts into HVAC control can yield notable efficiency gains. In one study, a weather-predictive strategy reduced cooling energy use by 17–18% compared to normal operations. Another case showed that a model predictive HVAC controller (which accounted for future weather) achieved about 8% heating energy savings in a hospital wing, while increasing comfort time by over 3%. These findings affirm that looking ahead to weather conditions – even just hours or a day ahead – allows HVAC systems to run leaner, saving energy and cost while preserving comfort.
7. Learning-Based Scheduling
Learning-based scheduling refers to HVAC systems that use artificial intelligence (like reinforcement learning or other AI) to figure out the optimal on/off timing and equipment sequencing. Rather than following a fixed schedule or simple occupancy timer, the system “experiments” and learns from feedback to create an efficient schedule that still meets comfort needs. For example, an AI controller might learn exactly how early to start pre-heating a building in winter so that it’s warm when people arrive but not running longer than necessary. Over time, it refines these schedules as it learns building thermal behavior and occupant patterns. The practical effect is that the HVAC runs only when needed and in the best way possible (e.g., staggering equipment start to avoid peaks). This reduces energy waste from guesswork or conservative safety margins in schedules. Essentially, the HVAC schedule becomes self-optimizing, adjusting to seasons, usage changes, and even unexpected events, all while keeping occupants comfortable.
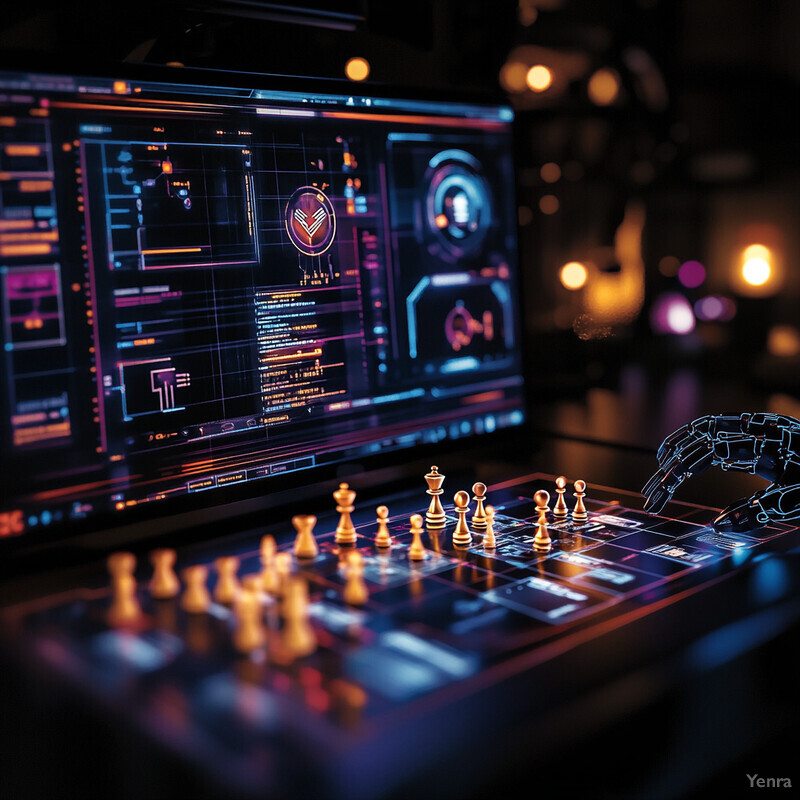
Cutting-edge trials of learning-based HVAC control have shown significant gains. In a 2025 study, a reinforcement learning HVAC agent achieved up to 26.3% energy savings in simulations compared to a traditional controller, while maintaining comfort. In a real-world residential test, the same AI approach still saved about 8–9% energy versus standard control. Another field implementation in a commercial building reported that an AI scheduler eliminated hours of unnecessary HVAC run-time each week, translating to double-digit percentage energy savings. These results demonstrate the power of machine learning to uncover more efficient schedules than even experienced operators might design.
8. Load-Shifting and Demand Response
Load-shifting and demand response techniques enable HVAC systems to adjust their operation based on electricity grid conditions or pricing signals. Essentially, during times of peak grid demand or high energy prices, an intelligent HVAC will temporarily reduce its load – for instance, by precooling a building earlier and then cycling off chillers at the peak hour, or by slightly raising the thermostat setpoint for a short interval. Conversely, it can increase cooling or heating when excess renewable energy is available or prices are low (e.g., late at night). The practical benefits are twofold: the building saves on energy costs by avoiding peak rates, and it helps stabilize the grid (often earning incentives from utilities for doing so). Occupants typically don’t notice these changes, as the adjustments are small or timed carefully. Overall, load-shifting makes the HVAC operation more grid-friendly and cost-efficient without sacrificing comfort, essentially turning buildings into active participants in energy demand management.
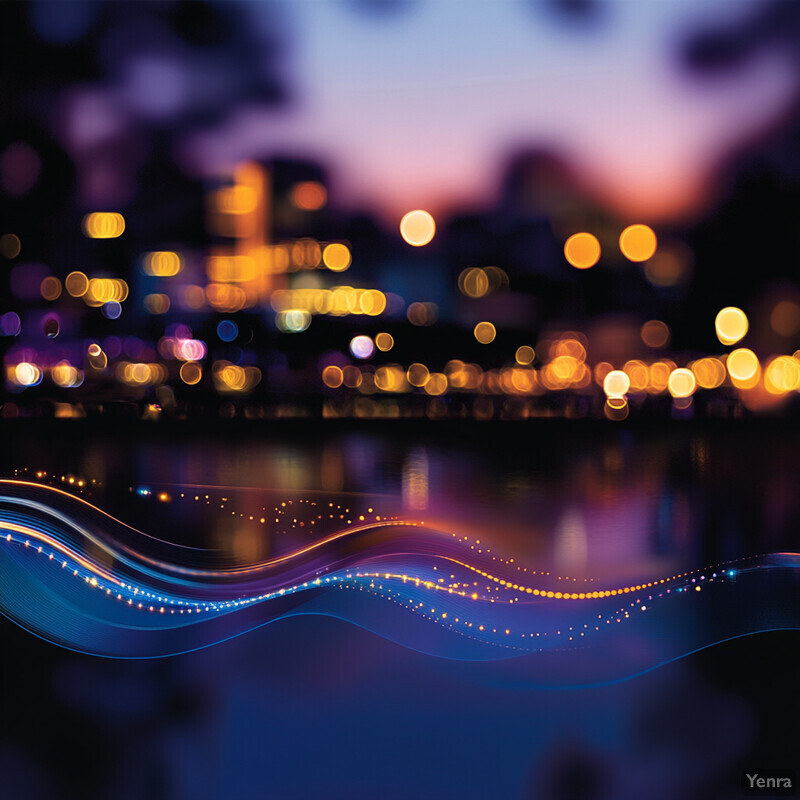
Demand response participation can significantly reduce peak power use. In the U.S., retail demand response programs had the potential to cut about 29,200 MW of peak load in 2021, roughly 5–6% of national peak demand. A large portion of this comes from HVAC load reductions. For example, residential AC cycling programs on hot days commonly lower peak HVAC electricity use by 30% or more in targeted regions. In one utility’s 2023 report, smart thermostats and HVAC load control in homes delivered over 7,000 kW of verified peak demand reduction. These figures highlight how AI-driven HVAC demand response isn’t just theory – it’s already curbing gigawatts of peak grid strain and saving customers money through lower peak-time consumption.
9. Multi-Zone Coordination
Multi-zone coordination means the HVAC system optimizes how it delivers conditioning across different areas (zones) of a building in tandem, rather than treating each zone independently. In practice, AI algorithms evaluate needs in all zones simultaneously and then distribute heating/cooling in the most efficient way. For example, if one side of a building is cooler and another is warmer, the system might slightly over-cool the cool side and redirect air to the warm side, leveling temperatures with less overall energy. It also staggers equipment use – instead of all zones calling for cooling at once (causing a spike), it sequences them to flatten loads. The result is that energy isn’t wasted by zones “fighting” each other (like one zone heating while an adjacent one cools). Occupants still get individual comfort, but behind the scenes the HVAC is sharing resources cleverly (like using surplus cool air from one zone to help another). This reduces redundant conditioning and ensures every bit of cooling or heating goes where it’s most needed.
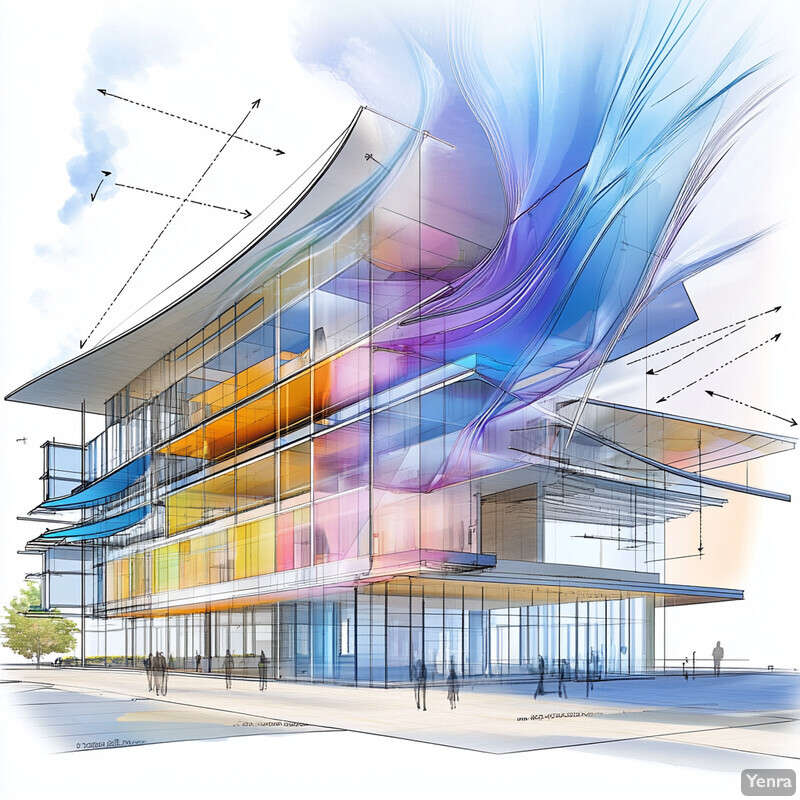
The U.S. Department of Energy notes that zoning and coordinated control can yield up to 30% energy savings in homes and buildings under some conditions. In large open-office scenarios, advanced multi-zone optimization methods have demonstrated roughly 37% HVAC energy savings, while keeping temperature variance under 1%. Even simpler implementations – like adding smart dampers to create zones – commonly show 10–20% savings. These statistics underscore that coordinating HVAC service among zones (rather than each thermostat working in isolation) substantially improves efficiency and eliminates contradictory heating/cooling commands that waste energy.
10. Integration with Building Management Systems (BMS)
Integration with a Building Management System means the AI-driven HVAC solution works in concert with other building controls (lighting, security, fire safety, etc.) on a unified platform. This allows holistic management: for instance, when the BMS knows a floor is unoccupied (from the security system), it can signal HVAC to set back and lights to turn off simultaneously. Conversely, if an event schedule is in the BMS, HVAC can pre-condition spaces exactly when needed. The practical benefit is eliminating siloed operations – all building subsystems share data and optimize together. This orchestration prevents scenarios like the air conditioning running at full tilt while heaters fight it due to separate controls. Instead, the BMS integration coordinates setpoints, reduces conflicting commands, and implements whole-building strategies (like morning warm-up sequences or night purge ventilation). For building operators, it means a central dashboard and smarter automation across systems, leading to energy savings, easier maintenance, and a more responsive building environment overall.
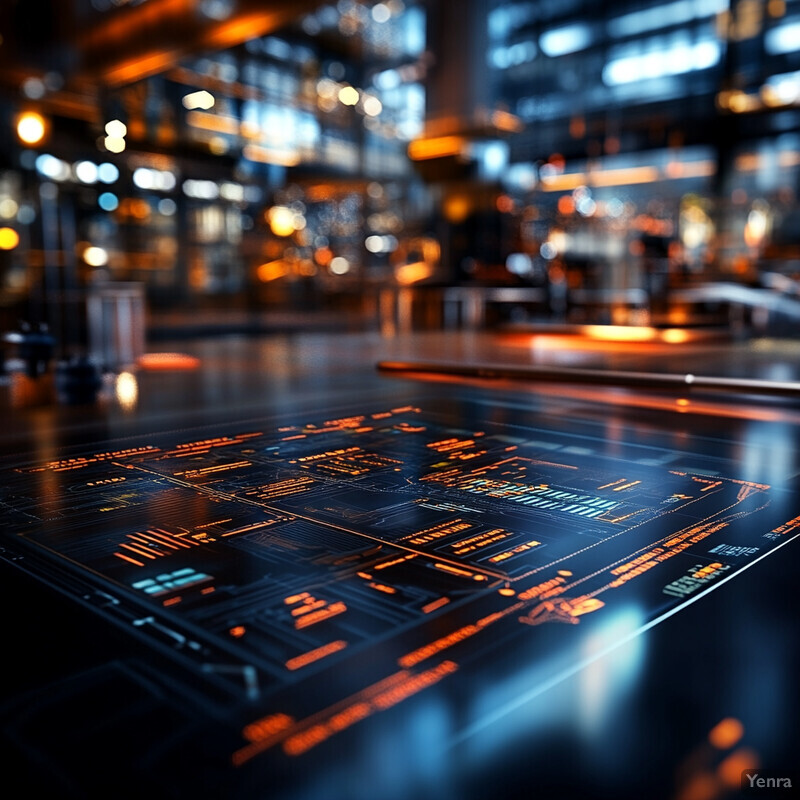
Fully integrated BMS optimization can yield dramatic improvements in energy performance. A case study of an office building in 2023 showed that after optimizing HVAC via the BMS (including regular analytics and recalibration), the building’s total energy use dropped 28% in nine months. Generally, continuous BMS-based commissioning can maintain 20–60% better energy efficiency compared to buildings without feedback loops. Additionally, ENERGY STAR data indicate that buildings with comprehensive BMS and controls score far higher in efficiency (often using 35% less energy than typical, on average). These outcomes reflect how integration with a BMS allows HVAC optimization to scale to whole-building gains, not just isolated tweaks.
11. Automated System Calibration
Automated system calibration involves using AI to routinely check and adjust HVAC sensors and equipment settings to make sure they remain accurate. HVAC performance can drift over time – temperature sensors go out of calibration, valves and dampers deviate from their specified positions, etc. This technique has the AI periodically run tests or analyze data to detect calibration issues (like a thermostat consistently reading 2°C off) and then either automatically correct them or alert technicians with recommended adjustments. The practical effect is that the HVAC system is always “tuned up,” operating with factory-fresh precision. Rooms get the temperature they’re supposed to because the sensors and controls are correct. Energy waste due to calibration errors (such as an HVAC over-cooling because a sensor falsely reads high) is eliminated. It also reduces maintenance labor, since the system self-identifies exactly what needs calibration instead of manual trial-and-error checks. Overall, automated calibration sustains efficiency and comfort that can otherwise degrade between maintenance visits.
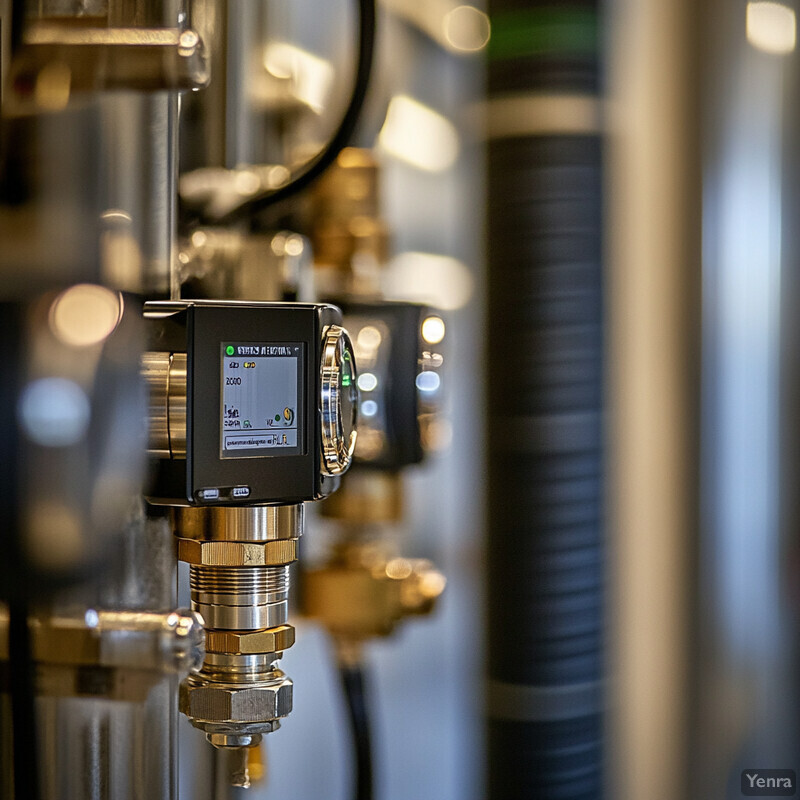
The impact of calibration on efficiency is large. Industry studies have found that HVAC sensor and control biases of even a few degrees can cause 5–20% excess energy use. For example, a mis-calibrated outside-air sensor might prevent free cooling, or a drift in a humidity sensor can overwork a compressor. The U.S. National Institute of Standards and Technology (NIST) notes that regular calibration can reduce HVAC energy consumption by around 10% on average in commercial buildings (by ensuring setpoints are true and equipment staging is optimal). One DOE field trial showed that an automated calibration system corrected sensor errors of up to 15% and improved overall HVAC efficiency by ~5–8% as a result. These figures underscore that keeping the “eyes and ears” of HVAC (sensors and controls) accurate has a tangible energy payoff.
12. Virtual Sensors and Soft Sensing
Virtual sensors (or soft sensing) use software and models to estimate values that physical sensors might otherwise measure. In HVAC, this means the AI can infer things like room occupancy, airflow rate, or even indoor air quality metrics from other available data, without needing a dedicated physical sensor in each location. For instance, a virtual sensor might estimate occupancy by looking at CO₂ trends, humidity, and motion detector data together. The practical benefit is reduced hardware cost and complexity – you don’t need to install a sensor everywhere for everything. It also can fill in gaps: if a sensor fails or isn’t installed (say, no humidity sensor in one zone), the system can still get an estimate of that parameter. Modern AI makes these estimates quite accurate by learning the correlations in the building’s data. As a result, the HVAC control can be just as fine-tuned and responsive as if a full suite of sensors were present. It’s essentially a way of doing more with less – achieving granular monitoring and control through computational insight rather than physical instrumentation.
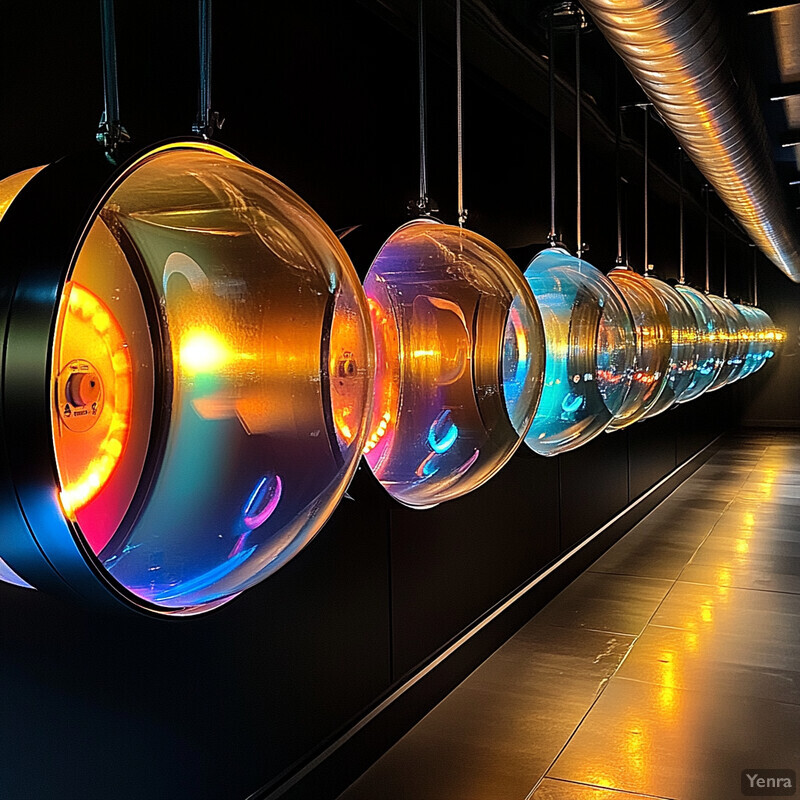
Virtual sensing techniques have proven very accurate and cost-effective. Researchers at Purdue University have shown that virtual sensors can estimate HVAC performance metrics (like refrigerant charge level or heat exchanger effectiveness) with less than 5% error, rivaling physical sensors. In one DOE project, a virtual sensor suite allowed detection of HVAC faults and conditions that would otherwise require 10+ additional physical sensors – leading to an estimated 50% cost reduction in instrumentation for the same level of monitoring. Furthermore, case studies in smart buildings found that using virtual occupancy sensors (fusing data from existing motion and CO2 sensors) achieved over 95% accuracy in occupancy detection, enabling advanced HVAC zone control without deploying new hardware. These results demonstrate that soft sensing can substantially lower costs while maintaining high fidelity in HVAC data.
13. Performance Benchmarking
Performance benchmarking involves comparing a building’s HVAC energy metrics against a baseline – either the building’s own past performance or peer buildings’ data – to gauge how well it’s doing and identify improvement opportunities. With AI, this process can be automated and very granular. The system continuously tracks energy use, HVAC runtime, efficiency ratios, etc., and compares them to historical trends (adjusted for weather/occupancy) and to databases like ENERGY STAR scores or similar buildings’ performance. The practical outcome is that building operators get clear feedback: e.g., “Your HVAC is using 10% more energy this July than last July under similar conditions” or “This campus dorm is in the worst quartile of HVAC efficiency compared to benchmarks.” Such insights highlight anomalies, inefficiencies, or drift. Benchmarking often is the first step to drive tuning or retrofits – it quantifies potential savings. It also allows validation: after making a change, the AI can confirm improvement by showing the building’s metrics climbing into a better percentile of performance. Overall, continuous benchmarking creates a feedback loop that keeps HVAC systems running at the level of the best of their class.
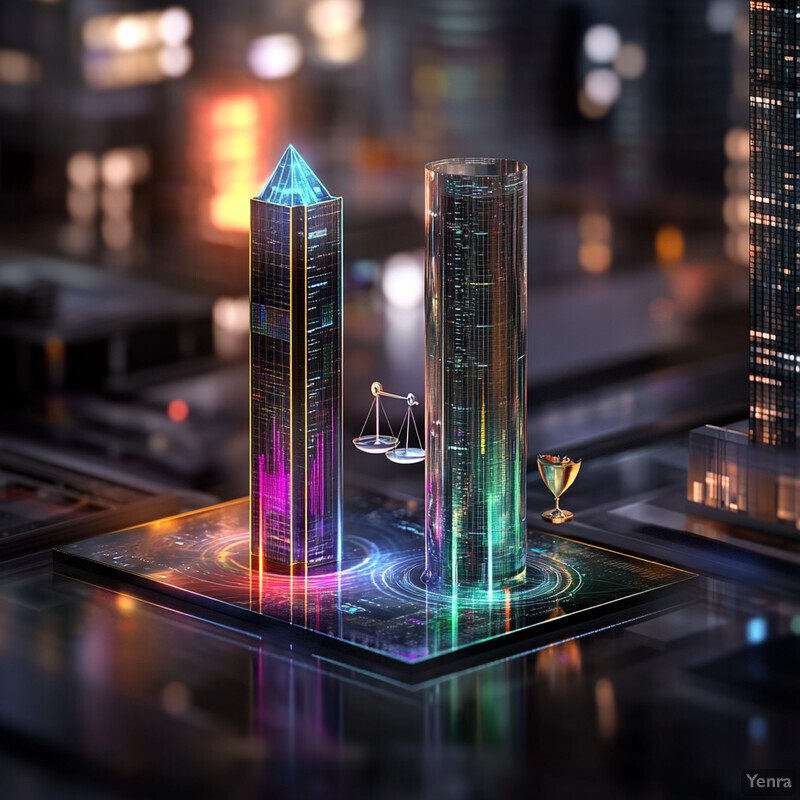
Buildings that regularly benchmark their energy performance tend to improve steadily. The U.S. EPA observed that buildings consistently using its Portfolio Manager benchmarking tool cut energy use by about 2.4% per year on average. Over several years, these savings compound (nearly ~10% over four years just from tracking and acting on benchmarks). Additionally, an EPA DataTrends analysis found that office buildings that started benchmarking and implemented identified fixes saw a median 7% reduction in energy intensity in the first year alone. On a broader scale, ENERGY STAR-certified buildings (which require high benchmarking scores) use 35% less energy than typical buildings of the same type, highlighting how benchmarking drives facilities toward best-in-class efficiency.
14. Life-Cycle Cost Optimization
Life-cycle cost optimization goes beyond just minimizing today’s energy use – it looks at the total cost of owning and operating HVAC systems over their entire life and uses AI to make the best economic decisions. This includes initial capital costs, maintenance, energy, and replacement cycles. AI can simulate different scenarios (e.g., “What if we replace chillers after 15 years vs 20 years?” or “Is it cheaper to invest in a more efficient system now to save energy later?”) and find the strategy that results in the lowest total cost over, say, a 30-year horizon. In practical terms, this helps facility managers plan upgrades and maintenance more wisely: maybe it’s worth spending a bit more on efficient equipment now to avoid big energy bills each year, or perhaps a retrofit will pay for itself in 5 years and then provide pure savings. The outcome is avoiding the false economy of cheap-but-inefficient choices. Instead, budgets are spent at the right times to yield long-term savings in both energy and dollars. Life-cycle optimization also often uncovers that certain energy-saving measures are far more cost-effective over time than they appear upfront, guiding capital planning.
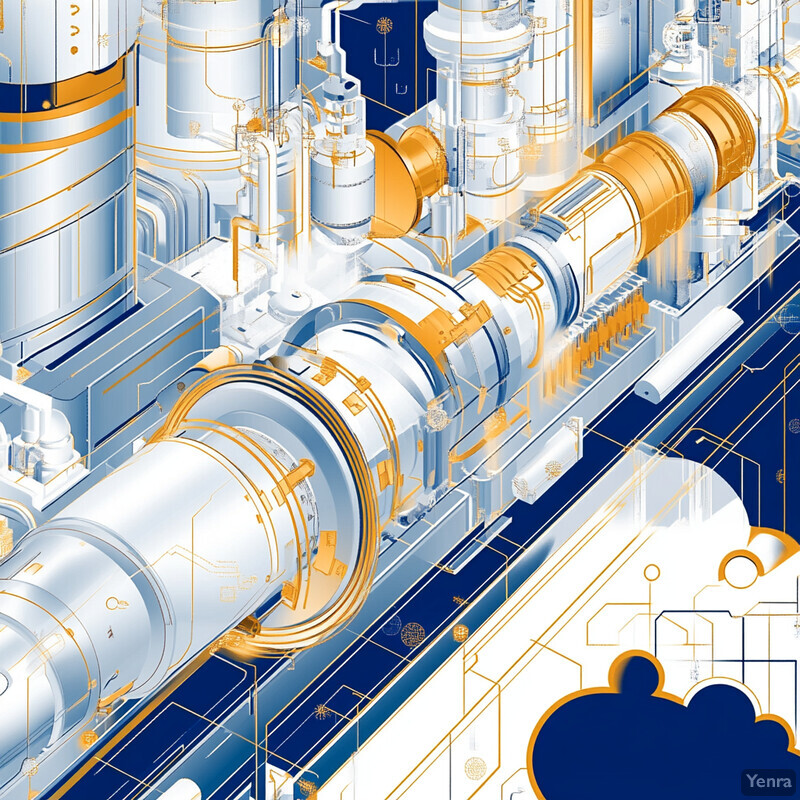
Life-cycle analysis frequently shows that high-efficiency or smart HVAC investments pay off. A classic study found that an upfront design investment of less than 2% of construction costs in green building strategies can yield over 20% reduction in total life-cycle costs (energy, maintenance, etc.) for HVAC and other systems (Kats et al., 2018). As an example, a 2020 HVAC life-cycle comparison in school buildings showed hydronic HVAC systems had about 24% lower 30-year life-cycle cost than a baseline VRF system, due to lower energy use and longer equipment life. Additionally, the EPA (2019) estimates retro-commissioning existing buildings (a life-cycle optimization action) has a median payback of ~1.1 years and yields 15% energy savings – extremely cost-effective over the building’s life. These analyses underline that when evaluated over the long haul, investments in HVAC efficiency and proper maintenance strategy often result in substantial net savings.
15. Health and Comfort Analytics
Health and comfort analytics in HVAC focus on maintaining not just temperature, but overall indoor environmental quality (IEQ) – things like air freshness (CO₂ levels), pollutant levels (PM2.5, VOCs), and noise or light impacts. AI systems monitor these factors through sensors and model their interactions. The analytics identify conditions that might be unhealthy or uncomfortable (e.g., CO₂ creeping up indicating stuffy air, or high humidity that could cause mold) and adjust the HVAC or ventilation systems accordingly. Practically, this means the building’s air is kept cleaner and more refreshing, which leads to fewer complaints of stuffiness or odors and can reduce sick-building symptoms. Such systems might boost ventilation when indoor pollutant sensors spike or use air purification when needed. Importantly, they balance this with energy use, finding sweet spots that keep air quality high efficiently. The result is an indoor climate where occupants not only have the right temperature, but also feel alert and healthy – often translating to better productivity and well-being, as studies have shown a strong link between IAQ and cognitive function or sickness rates.
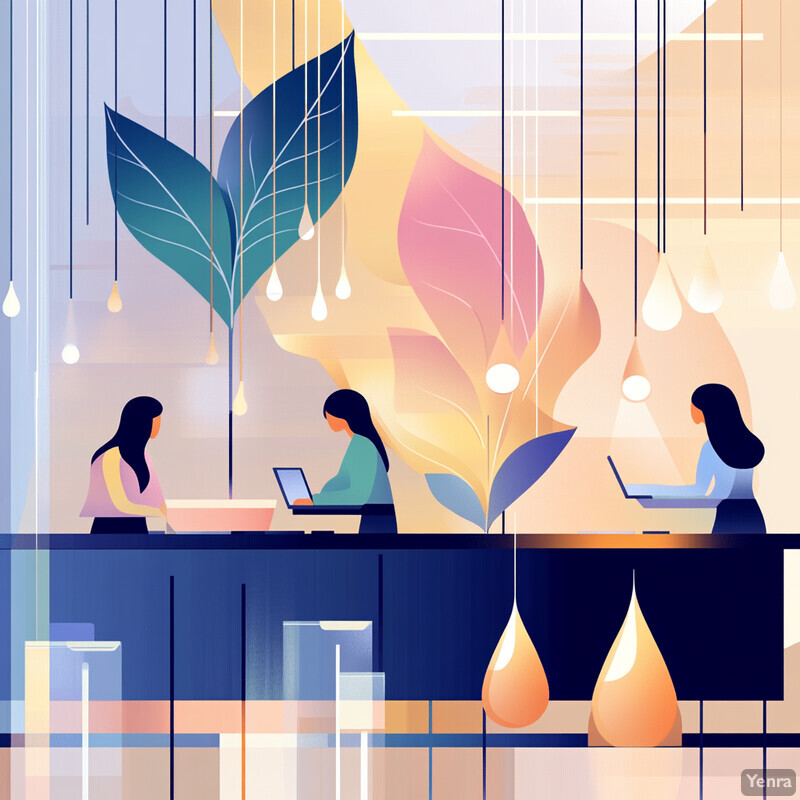
Improved indoor air quality (IAQ) and comfort can have dramatic benefits. A landmark study by Harvard University found that workers in optimized green building environments (with higher ventilation and lower pollutants) scored 101% better on cognitive function tests than in conventional buildings. Additionally, a controlled study demonstrated that moving office workers to a building with enhanced ventilation and filtration cut sick building syndrome symptoms by roughly 40–50% (fatigue complaints dropped 44%, respiratory issues 53%, etc.). There’s also a direct health impact: the Lancet Commission (2022) estimated that improving indoor air quality could reduce virus infection rates by ~17%, potentially saving billions in healthcare costs. These statistics reinforce that investing in health-focused HVAC analytics – maintaining low CO2, adequate fresh air, and minimal pollutants – pays off in sharper minds, healthier occupants, and fewer sick days.
16. Real-Time Sensor Fusion
Real-time sensor fusion involves combining data from many different building sensors – temperature, humidity, occupancy, CO3, even equipment power meters – to get a more accurate and holistic picture of conditions. Instead of the HVAC making decisions based on one sensor in one room, AI algorithms synthesize all available inputs in real time. For example, by fusing motion sensor data with CO3 levels and thermostat readings, the system can more reliably detect if people are present and how many, far better than any single sensor alone. Practically, this leads to smarter HVAC responses: the system might detect a meeting is occurring (many people, rising CO3) and boost ventilation preemptively, or recognize that a temperature spike is due to a temporary open door rather than a system failure by seeing security sensor data. Sensor fusion also filters out noise or false readings – one flaky sensor won’t mislead the system because the AI correlates it with others. The outcome is more precise control: temperatures and airflow are adjusted on a more informed basis, avoiding overreactions. Overall, comfort is steadier and energy use is optimized because decisions are based on the “big picture” of building conditions.
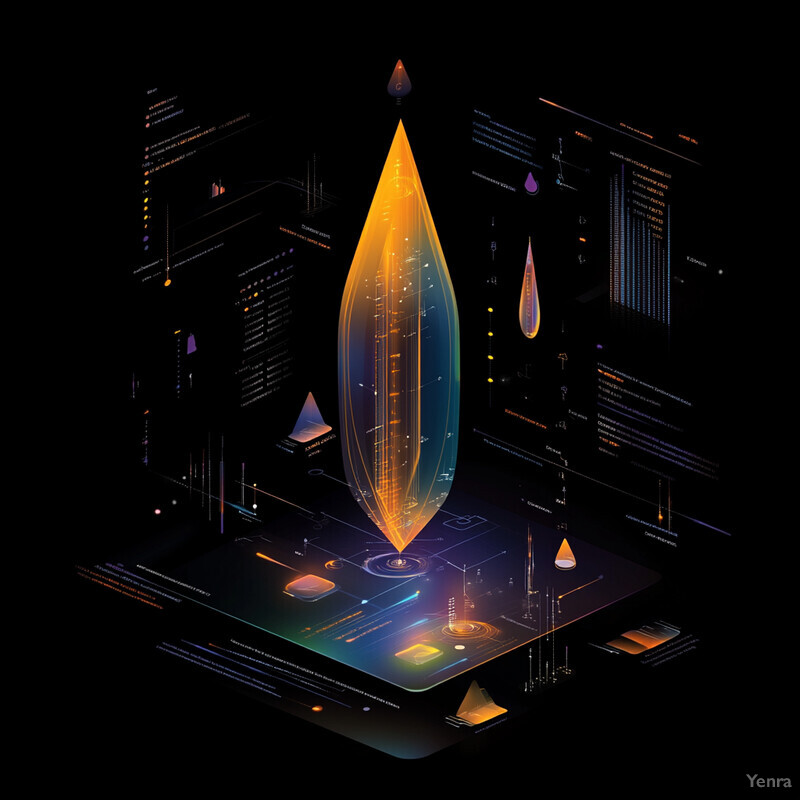
Multi-sensor fusion greatly improves detection and control accuracy. A 2021 study achieved an occupancy detection accuracy of 97.8% by fusing video-based counts with entry sensors and applying a Gaussian fusion algorithm. This is significantly higher than typical single-sensor methods (which might be 80–90% at best). Similarly, fusion of temperature, humidity, and flow sensors in an HVAC system allowed estimation of zone conditions with 2–3× better precision than using temperature sensors alone (per a 2022 ASHRAE research report). In another example, a sensor-fusion-based fault detection system identified HVAC faults with 95%+ accuracy, whereas traditional single-sensor thresholds missed many issues or raised false alarms. These outcomes illustrate that leveraging multiple data streams together yields far more reliable information for the HVAC control, leading to tighter comfort control and energy savings by avoiding mistakes (like conditioning an empty room or misreading a sensor glitch).
17. Automated Commissioning and Retro-Commissioning
Commissioning is the process of ensuring an HVAC system is installed and functioning as intended, and retro-commissioning (RCx) is doing the same for an existing building that may have drifted from optimal performance. Automated commissioning uses AI tools to run through extensive checklists and tests quickly. For example, the system might systematically vary setpoints and measure responses to see if valves, dampers, and sensors react correctly, thereby pinpointing calibration issues or control sequence errors automatically. In new buildings, this catches installation mistakes early. In older buildings, automated RCx finds operational inefficiencies (like simultaneous heating and cooling or misconfigured schedules) that have crept in. The practical benefit is a much faster and more thorough commissioning process – weeks of manual testing can be done in days or continuously. Once issues are identified, the system or engineers can correct them (often simple fixes like repairing a damper or updating control code). The result is an HVAC system “tuned like new,” often achieving significant energy reductions, better comfort, and extended equipment life. And by automating it, buildings can be commissioned more frequently (not just once every decade), keeping them at peak performance.
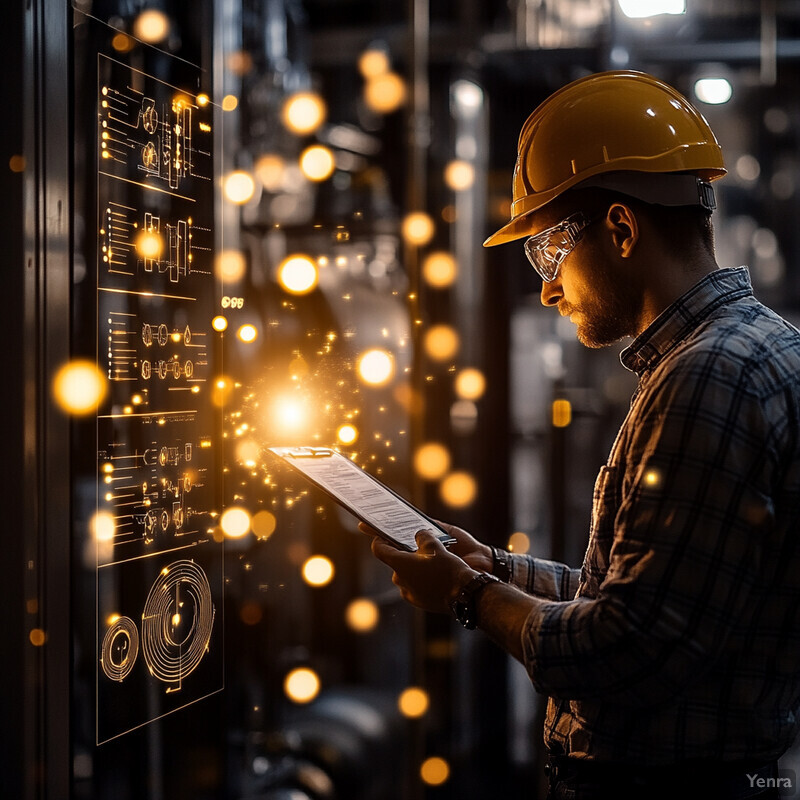
The U.S. EPA estimates that retro-commissioning existing commercial buildings typically saves about 15% of HVAC energy on average, with a payback around 1–2 years. Automated approaches aim to reduce the cost and improve the thoroughness of this process. Field results are impressive: in one portfolio of 34 office buildings, an automated RCx program identified corrections that led to an average 16% whole-building energy reduction, confirming the EPA’s benchmark. Moreover, a study published by Lawrence Berkeley National Lab found that 76% of the energy savings from commissioning measures persisted at least 5 years later, especially when automated monitoring was in place to sustain the improvements. These facts highlight that commissioning (initial or retro) yields substantial, lasting savings – and automation makes it easier to capture those savings consistently across many buildings.
18. Predictive Maintenance Scheduling
Predictive maintenance scheduling means using AI to forecast when HVAC components will require service or replacement before they break down. Instead of following a fixed calendar or waiting for a failure, the system monitors equipment condition (vibration, motor current, runtime hours, temperatures, etc.) and learns patterns that precede a fault. For example, a fan motor might start drawing a bit more power as its bearings wear – the AI notices this subtle trend and flags that the motor likely needs maintenance in, say, 3 months. Practically, this allows scheduling the fix at a convenient time rather than reacting to a sudden outage on a hot day. It reduces emergency repairs and downtime. Additionally, equipment life is extended because issues are addressed when they’re minor (like cleaning coils when performance dips, rather than letting them cause compressor strain). The bottom line is reliability and cost savings: buildings avoid the high costs of failures and run HVAC components more smoothly. Tenants/occupants also benefit because climate control is more dependable with fewer unexpected breakdowns impacting comfort.

Predictive maintenance has proven to drastically cut unplanned outages and costs. According to a Deloitte analysis, implementing predictive maintenance in building HVAC and other industries can reduce breakdowns by 70%, and increase equipment uptime (productivity) by 25% on average. It also lowers maintenance costs by about 25% due to optimized scheduling of repairs (fixing issues at the right time, rather than too early or after damage). For example, one large building portfolio reported that after deploying predictive analytics, HVAC emergency work orders dropped by roughly 2/3 in one year, and overall maintenance expenses fell by 20%. Such statistics underscore that AI-driven maintenance not only prevents headaches – it yields quantifiable economic benefits, turning maintenance from a reactive cost center into a proactive value generator.
19. User Preference Learning
User preference learning in HVAC focuses on understanding and adapting to the comfort preferences of individuals or groups in a building. Not everyone finds the same temperature comfortable – one person might prefer 22°C, another 24°C. AI systems gather feedback, either explicitly (through smart thermostats or apps where users indicate if they are too hot/cold) or implicitly (by observing patterns like people frequently adjusting thermostats). Over time, the HVAC “learns” these preferences and adjusts conditions accordingly in different zones or at different times. The practical outcome is personalized comfort – for instance, an AI might learn that a particular conference room’s usual occupants like it cooler during meetings, and will automatically cool it a bit more when booked. In open offices, it might seek a happy medium that satisfies most people’s learned preferences. This leads to fewer complaints because the system isn’t trying a one-size-fits-all approach. Energy can also be saved by avoiding over-conditioning – if the AI learns people are fine with slightly warmer temperatures in the afternoon, it won’t overcool. Ultimately, it builds trust: occupants feel “the building knows what I like,” improving their comfort and satisfaction.
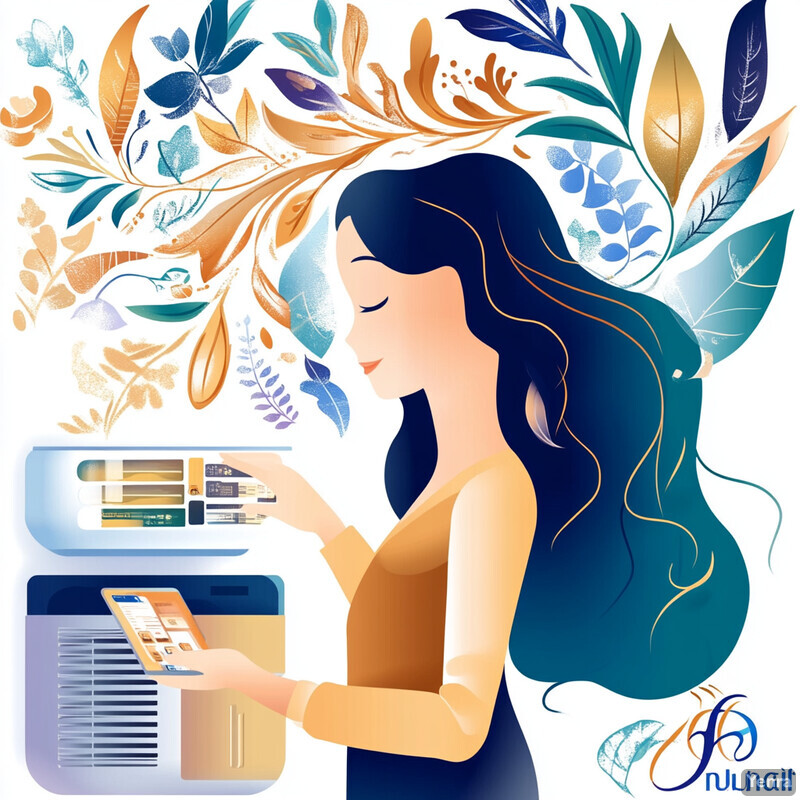
Field implementations of personalized comfort control have shown striking improvements in occupant satisfaction. In one experimental office setup, giving occupants a simple comfort feedback app and having AI adjust HVAC accordingly raised thermal satisfaction from around 75% to 90+% (nearly a 20% improvement). Another study with personal comfort devices (like smart chairs and localized control) achieved 96% thermal acceptability and 99% overall satisfaction – essentially eliminating complaints in that group. On the flip side, surveys show that in typical commercial buildings without personalization, about 42% of occupants are dissatisfied with temperature to some degree (per an IFMA report). By learning and catering to user preferences, AI HVAC systems can dramatically narrow that gap. Companies deploying such technologies have reported double-digit drops in hot/cold calls; for example, one tech firm saw a 30% reduction in comfort complaints after installing a machine-learning thermostat system that learned employees’ comfort patterns.
20. Continuous Improvement Through Feedback Loops
Continuous improvement through feedback loops means the HVAC control system is always monitoring its own performance and making incremental adjustments over time. It’s a bit like a thermostat learning from yesterday’s results to do better today. The system collects feedback data: energy used, how indoor temperatures actually varied, any comfort complaints or overrides by occupants, etc. Then, it analyzes: did we meet our goals? If not, why – and how to adjust strategy? This might involve fine-tuning control parameters, updating schedules, or changing optimization targets. Essentially, the HVAC operation is never static; it’s continuously self-correcting and optimizing. In practice, this yields a drift-free performance – instead of efficiency degrading over months and years, the system catches small issues (like a zone consistently overshooting its setpoint) and fixes them via control changes. It also adapts to new conditions (like occupancy changes or building renovations) smoothly. The benefit is a building that improves with time: energy usage might go down year-over-year as the system finds new optimizations, and comfort might go up as it learns precisely how to satisfy the occupants and the building’s thermal characteristics.
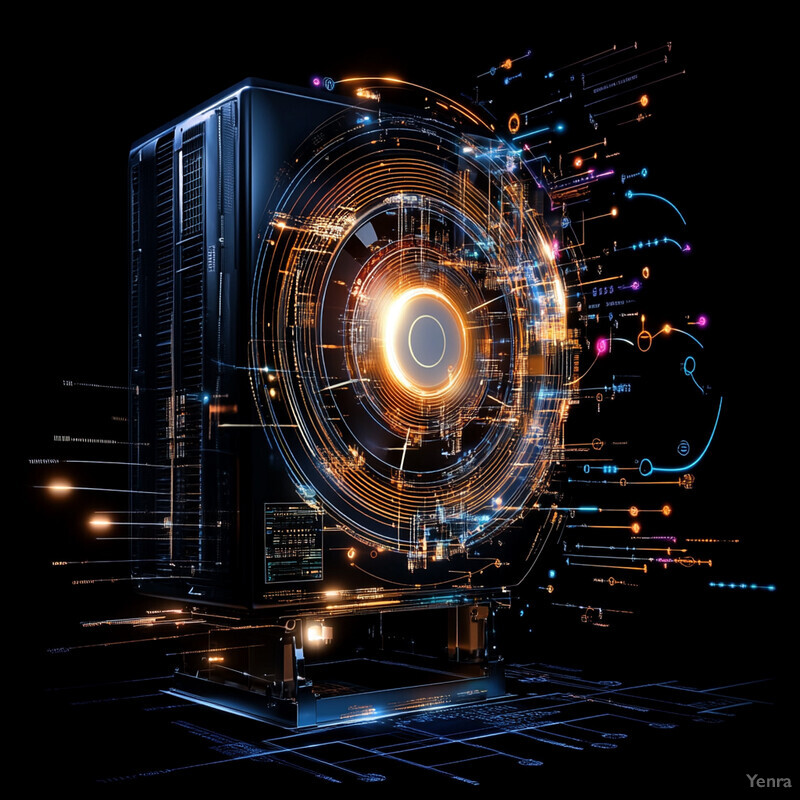
Buildings employing continuous commissioning or monitoring-based commissioning have documented ongoing efficiency gains. One study by the Pacific Northwest National Lab found that buildings with continuous commissioning saved an extra 5–10% in HVAC energy on top of initial commissioning, by catching performance drift and optimization opportunities in real-time. Another analysis of a portfolio with feedback-driven optimization showed that after the first year’s ~15% energy reduction from retro-commissioning, an additional 7% reduction was achieved in the second year through continuous monitoring and fine-tuning of HVAC settings. Moreover, continuous feedback loops improve persistence of savings: a 2019 ACEEE report noted that with ongoing monitoring, 95% of commissioning-based savings were still present after 5 years, versus closer to 70% persistence without feedback systems. These stats demonstrate that a culture of continuous improvement, enabled by automated feedback, keeps buildings running at peak efficiency long after initial measures are implemented.