1. Automated Defect Detection via Machine Vision
AI-powered machine vision systems can automatically identify weld defects (like cracks, porosity, or inclusions) in real time, greatly reducing reliance on human inspectors. High-resolution cameras coupled with deep learning models scrutinize weld images frame-by-frame, spotting tiny imperfections that might escape the naked eye. This continuous monitoring makes quality control faster and more consistent, catching defects early in the welding process. By detecting flaws immediately, such systems help prevent faulty welds from moving further down the production line. Overall, automated vision inspection leads to fewer missed defects, lower scrap rates, and more uniform weld quality.
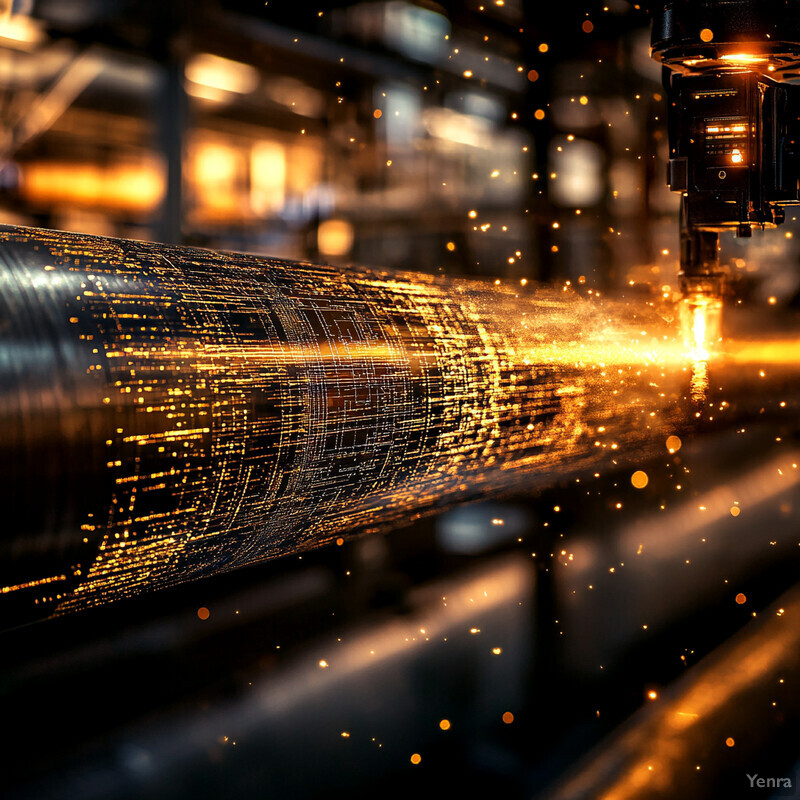
Recent research has demonstrated the effectiveness of AI vision in weld inspection. For example, an enhanced YOLOv8 deep-learning model achieved a weld defect detection mean average precision of about 90.5%, indicating very high accuracy in identifying weld anomalies. These AI models can also operate at high speed: lightweight versions of YOLO-based detectors have been reported to run at well over 150 frames per second, enabling true real-time inspection of weld seams. In practice, deploying such AI vision systems in a manufacturing setting led to significant improvements in defect detection rates compared to human inspection. One AI-based inspection solution was capable of examining 150 weld seams in only 40 seconds, far outpacing manual methods. These machine-vision inspectors not only flag surface defects immediately but can also categorize their types, providing data that supports faster corrective actions and continuous quality improvement.
2. Real-Time Weld Parameter Optimization
AI systems can dynamically adjust welding parameters (such as voltage, current, travel speed, and wire feed rate) in real time to keep the process in its optimal state. In welding, many variables must be continuously balanced to produce a defect-free joint; traditionally this relied on skilled operators fine-tuning settings. AI controllers now monitor sensor data (like arc signals, pool temperature, or weld bead dimensions) and instantly tweak parameters to compensate for any drift or disturbance. This ensures that the welding conditions stay within the ideal range even as material or environmental factors change. By automating parameter optimization on the fly, manufacturers can achieve more consistent weld quality, reduce the need for rework, and increase first-pass yield.
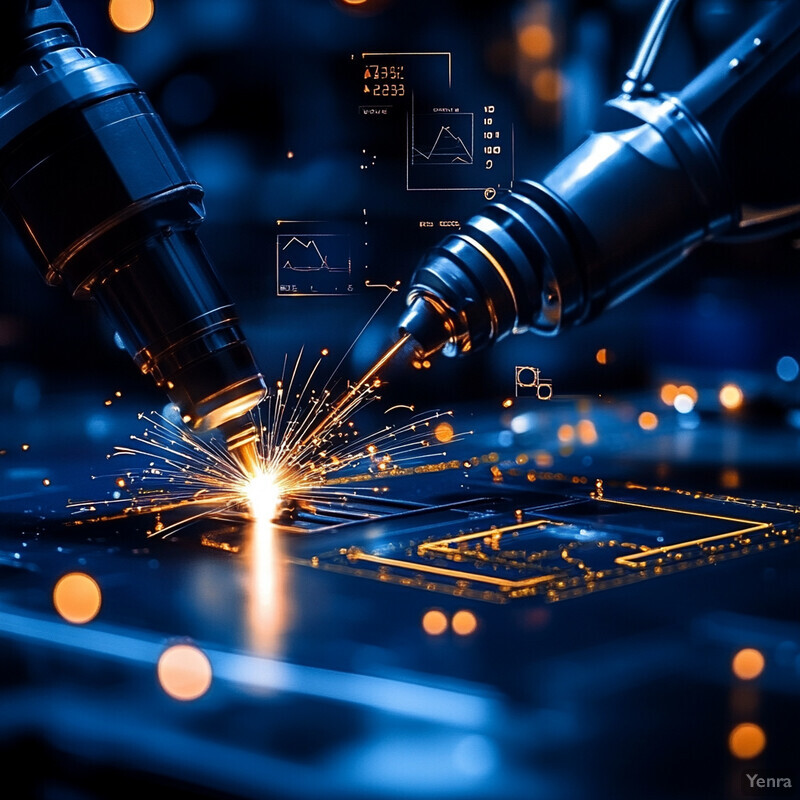
Emerging research highlights how physics-informed AI can enable proactive, self-correcting control of welding processes. In one 2025 study, engineers developed a hybrid AI framework that integrated welding physics with machine learning to anticipate and correct instabilities in real time. The system was able to predict welding instability with up to 98% accuracy just 50 milliseconds ahead and still maintained ~86% accuracy for predictions 1 second in advance. Crucially, this AI didn’t just predict problems – it also performed autonomous parameter adjustments (“autonomous model parameter optimization”) to stabilize the process on the fly. By leveraging such rapid prediction and feedback, the closed-loop AI controller could adjust heat input or travel speed almost instantly when sensors detected an anomaly, preventing defects before they formed. These results show that AI-driven control can react far faster than a human operator, maintaining optimal weld conditions under dynamic scenarios. As a result, real-world implementations of this approach have reported improved weld consistency and fewer defects, since the AI is essentially “steering” the welding arc to keep it within quality tolerances at all times.
3. Predictive Quality Assessment
By analyzing historical welding data alongside live sensor inputs, AI can predict whether a given weld will pass quality inspection before the weld is even completed. This predictive quality assessment uses patterns learned from past welds (including subtle trends in voltage, current, speed, temperature, etc.) to forecast the likelihood of defects or failures. Essentially, the system provides an early warning: if the model predicts a high chance of a defect forming (for instance, porosity or inadequate fusion), operators or automated controllers can intervene immediately—adjusting parameters or pausing the process—rather than discovering the issue later in final inspection. This proactive approach helps catch quality issues upstream, reducing rework and ensuring more welds meet standards on the first try.
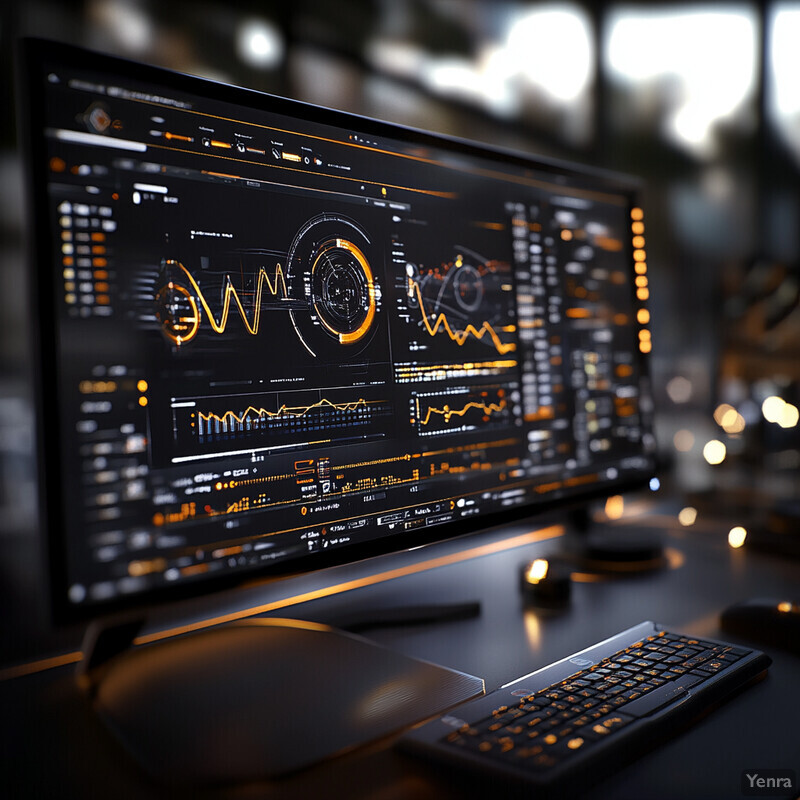
Recent advances in machine learning have made such predictive quality monitoring feasible. In one 2024 study, researchers developed a data-driven model to predict welding quality in shipbuilding. By training on sensor data and process parameters, their AI method achieved over 90% prediction accuracy for weld quality outcomes in plate welding tests. Similarly, in automotive manufacturing, AI models have been used to transition from periodic sample inspections to 100% weld inspection by predicting spot weld quality from process signals. For example, a published case showed that a machine learning system could reliably predict the tensile strength of resistance spot welds, allowing manufacturers to identify weak welds immediately during production. Predictive analytics have also been applied to specific defect modes: one research effort trained a model on arc sensor patterns to forecast the occurrence of porosity defects in TIG welds, enabling real-time adjustments to avoid those pores. These successes demonstrate that AI can mine the complex relationships between welding conditions and final quality, giving fabricators a powerful tool to foresee and prevent weld defects before they happen.
4. Seam Tracking and Alignment
AI-enhanced vision systems can precisely locate and follow the joint seam during welding, ensuring that robotic torches stay perfectly aligned. Welding along complex or curved joints is challenging—any misalignment can cause defects like incomplete fusion or burn-through. Traditional seam tracking methods (like simple sensors or fixed guides) can struggle if the seam path varies or if there are gaps. By contrast, modern systems use cameras or laser scanners paired with AI algorithms to “see” the seam ahead of the torch and guide the robot in real time. These systems dynamically adjust the torch position and angle as needed, even if the part’s geometry is irregular or the seam wanders. The result is a consistently positioned weld bead, with far less risk of deviation. In essence, AI seam tracking acts as the welder’s eyes and hands, continually making fine alignment corrections that lead to stronger, more uniform welds.
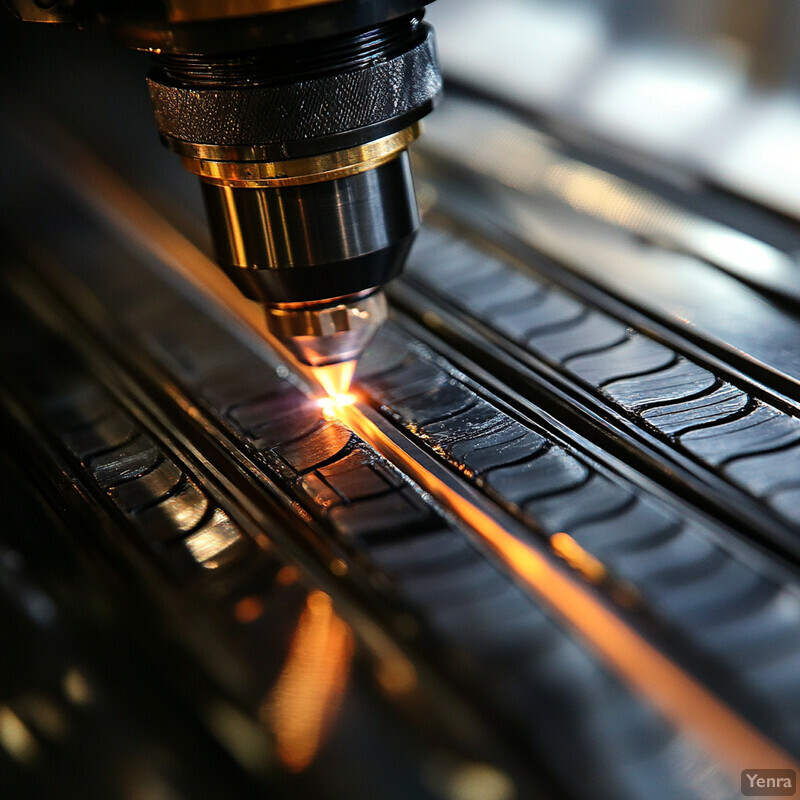
Experiments show that AI-driven seam tracking can attain extremely high precision. One vision-based tracking system, for instance, demonstrated it could keep a welding robot on course with a positional accuracy on the order of ±0.5 mm along the seam. In practice, this means the robotic torch deviated less than a hair’s width from the ideal path, even when the seam had slight bends or the workpiece fit-up was imperfect. Another study integrated an improved neural network (YOLOv8-Seg) to recognize weld seam features and guide a robot; it achieved 97.8% accuracy in identifying the seam location while running at up to 18–21 frames per second in an embedded controller. This real-time guidance allowed the robot to make on-the-fly adjustments, eliminating misalignment defects. Industries have reported that using AI seam tracking reduces weld rejections and rework – for example, avoiding overlap or missed joint areas – because the system continuously corrects the torch path. Overall, the introduction of AI for seam finding and alignment has significantly improved the consistency and quality of automated welding, especially for complex geometries.
5. Arc Stability Monitoring
The stability of the welding arc is critical for achieving consistent weld penetration and bead shape. AI-based monitoring systems can detect very subtle fluctuations in arc behavior (in electrical signals, sound, light, etc.) and instantly take action to correct them. For example, if the arc length suddenly changes or the arc starts sputtering due to contamination, an AI system can recognize this pattern as a precursor to a defect like porosity or spatter. It can then adjust parameters (such as voltage or wire feed) or alert the operator before the weld quality is compromised. By continuously “listening” to and analyzing the arc in real time, these systems prevent small instabilities from snowballing into larger weld defects. In short, AI arc monitoring acts as an ever-vigilant guardian of the welding process, ensuring the arc remains smooth and steady for optimal weld quality.
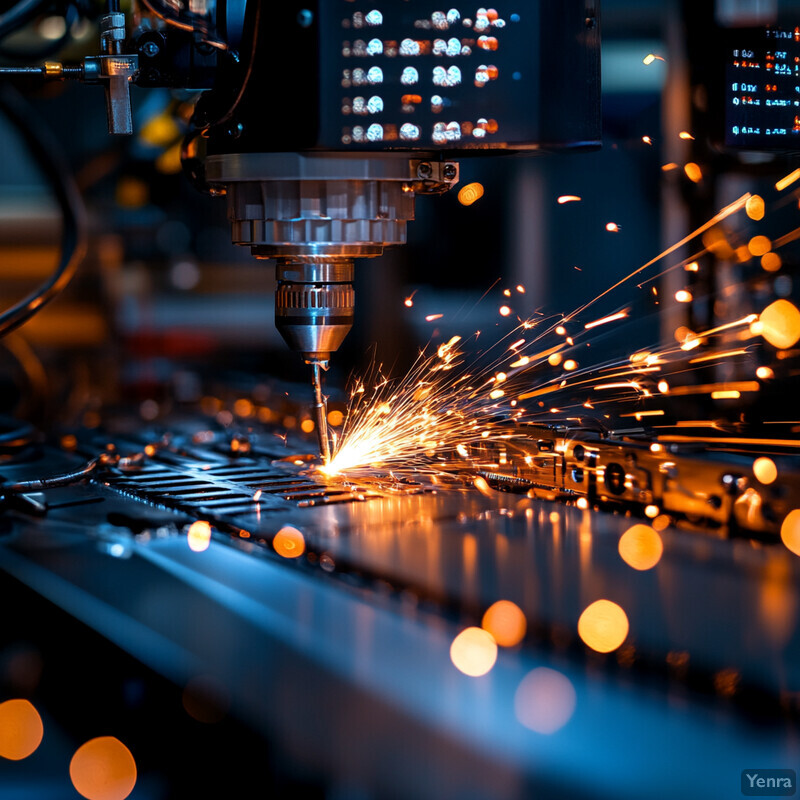
Research in this area has shown promising results in using sensor data for defect prediction and arc control. One approach used the acoustic signature of the welding arc to predict the formation of porosity defects: a 2024 study trained a machine learning model on arc sound frequencies and achieved high accuracy in detecting when conditions would produce internal porosity. In another case, a deep learning system monitored the welding voltage signal in a submerged arc welding (SAW) process and was able to predict 80% of impending pore defects within 10 milliseconds of instability, effectively providing real-time warnings. Crucially, these AI models don’t just predict issues—they enable rapid intervention. Industrial implementations have combined such models with adaptive controls: for instance, if an AI detects an unstable arc (via abnormal current fluctuations or unusual sounds), it can instantly trim the wire feed speed or adjust the torch position to re-stabilize the arc. Field reports indicate this has reduced weld defects related to arc instability (like undercut or inconsistent penetration) by catching problems faster than a human could. As Dr. Tapia Suárez and colleagues noted in their 2024 work, these “learning machines” can now read arc data and readjust welding parameters on the fly, bringing the process back into balance within milliseconds.
6. Thermal Profile Analysis
AI-driven thermal analysis involves using infrared cameras and smart algorithms to monitor the temperature distribution (thermal profile) across the weld and surrounding material in real time. A proper thermal profile is key to weld integrity: it ensures the weld achieves sufficient penetration without causing excessive heat-affected zone damage. By analyzing heat maps of the weld pool and plate, AI can detect if certain areas are too hot or too cold relative to the ideal profile. For instance, if a section of the weld is cooling too quickly (risking cracks) or staying too hot for too long (causing distortion), the system flags it immediately. It can then adjust parameters or cooling rates to bring the profile back in line. This technology helps reduce issues like insufficient fusion (from too low heat) or thermal warping and microcracking (from poor heat distribution). Ultimately, AI thermal profiling ensures that each weld experiences the right temperatures at the right times for optimal metallurgical quality.
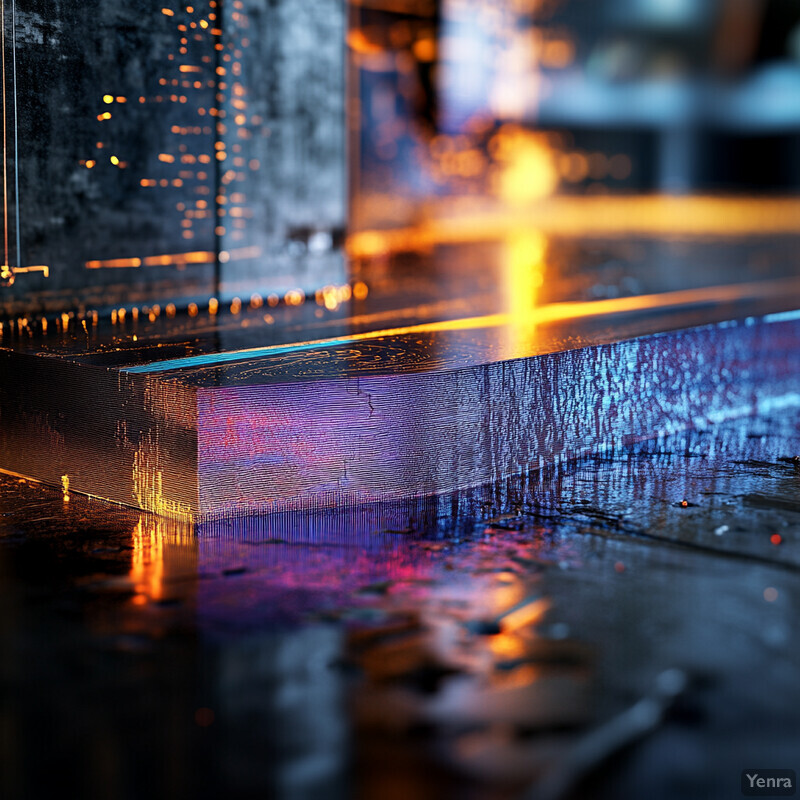
Recent developments have combined infrared thermography with deep learning to perform advanced weld monitoring. In one case, researchers applied an infrared camera and a trained YOLOv5-based algorithm to evaluate weld “coverage” on complex heat sink fins. The AI could detect areas where the thermal signature indicated a poor bond (i.e. fin not properly welded to base), effectively quantifying welding quality non-destructively. Another study demonstrated using thermal imaging to predict weld bead geometry: by analyzing the thermal footprints during welding, a neural network could infer bead penetration depth and width with high correlation to actual measurements. In practical use, companies have begun employing data-enhanced thermal imaging to catch issues like lack of penetration or overheating. For example, an aerospace manufacturer reported using real-time IR monitoring with AI analysis to ensure each weld pass stays within a tight thermal window, which cut down on post-weld inspections and rework. These data-driven thermal analyses are essentially giving welders a “smart thermal eye” – maintaining proper heat distribution and alerting operators when the thermal profile deviates from the norm that produces high-quality welds.
7. Adaptive Filler Material Control
AI can intelligently manage how filler material is added during welding, ensuring the right amount and type of filler is used at each moment. In manual welding, an operator adjusts filler feed rate or even switches filler rods based on how the weld pool looks – too little filler can cause underfill or burn-through, too much can lead to overlap or cold laps. AI systems replicate and enhance this decision-making. Using sensors (camera views of the weld pool, or electrical signals indicating pool size), a machine learning model can predict when the weld pool needs more wire or if a different filler alloy might better bridge a gap. The AI then directs the wire feeder or even selects from multiple filler materials on the fly. This leads to an “adaptive” filler deposition: the system might slow down filler feed on a thin section to avoid excess buildup, then speed it up on a wide gap to ensure proper fill. Such fine-grained control yields a more consistent bead and reduces defects related to poor filler handling (like porosity from incorrect wire positioning or lack of fusion from insufficient filler).
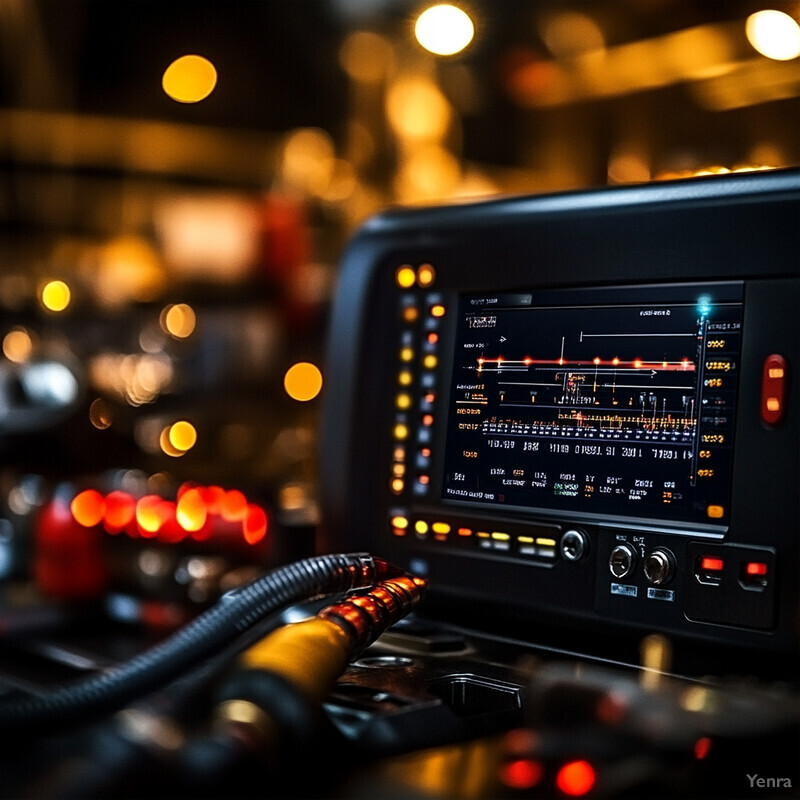
Cutting-edge experiments have shown the feasibility of AI-guided filler control. Researchers from RWTH Aachen, for example, developed an AI-driven GTAW (TIG) system with two neural networks: one that uses vision to identify features like the weld pool and wire position, and another that predicts the resulting weld bead geometry. This setup enabled autonomous multi-pass welding, where the AI plans and executes the filling of a complex groove by determining how much filler to deposit in each pass. The system can adapt the filler wire feed and torch path based on the groove shape in real time, something traditionally done by a highly skilled welder. In another demonstration, a machine learning-based welding procedure expert system was able to recommend optimal filler material and parameters for specific weld scenarios by analyzing a large database of prior welds. By inputting material type and joint configuration, the system outputs the best wire type (e.g. alloy composition) and feed settings, learned from what produced the highest quality weld in the past. Early industrial trials of adaptive filler control report fewer welding defects like undercuts or incomplete fill, since the AI continuously balances the filler rate with heat input. This illustrates how AI can merge human welding expertise with big data to ensure the right filler material usage at every moment of the weld.
8. Expert System Integration
AI-based expert systems in welding act as a digital knowledge base and advisor, combining human expertise with real-time data. These systems are programmed with welding domain knowledge – for example, rules about which process to use for a given material thickness, or remedies for common weld defects – and they continuously ingest live production data. When a welding challenge arises (say an unusual material or position), the expert system can suggest solutions that a seasoned welding engineer might – such as adjusting preheat, changing electrode type, or modifying travel speed. Unlike a static handbook, however, the AI expert evolves by learning from each weld and outcome. Over time it “learns” new best practices by analyzing successful (and unsuccessful) welds in the database. This integration of a knowledge base with machine learning means the system can provide on-the-spot guidance to operators or automatic adjustments to equipment. The goal is to capture the nuanced decision-making of veteran welders and scale it across an organization, leading to consistently high-quality welds even when less experienced personnel are at the helm.
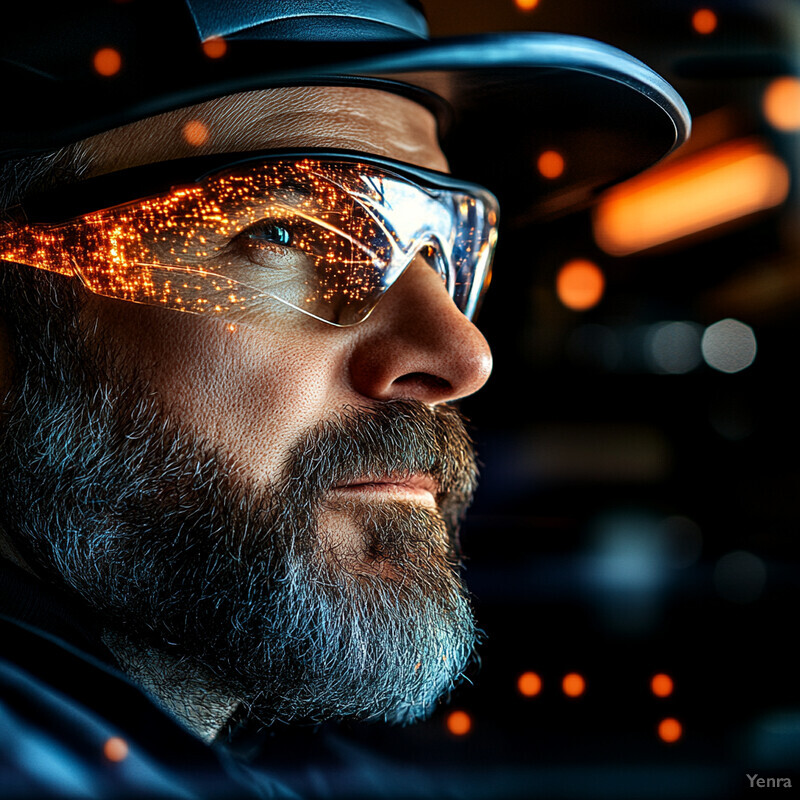
Modern welding expert systems have demonstrated impressive capabilities by fusing expert rules with AI learning. In 2023, Wang et al. introduced an intelligent GMAW (MIG welding) procedure design system that encapsulated welding standards, experienced welders’ knowledge, and machine learning algorithms. This system could automatically generate optimized welding parameters and procedures for a given task – for instance, selecting the appropriate process (GMAW vs. TIG), filler wire, shielding gas, and initial settings – by referencing its knowledge base and prior data. It significantly reduced the trial-and-error normally needed to develop a new weld “recipe.” In evaluations, the AI’s recommendations closely matched those a human expert would make, and in some cases even unveiled non-intuitive parameter combinations that improved quality (insights beyond the human experts’ experience). Additionally, expert systems have been applied to weld defect troubleshooting: a prototype knowledge-based system in China was reported to diagnose weld cracks and suggest remedies by reasoning through rules in its database (e.g., if a hot crack is detected in aluminum alloy, check for improper filler or cooling rate) – essentially acting like a virtual welding consultant. These examples show that AI-integrated expert systems can standardize welding best practices and assist with complex decision-making, helping less experienced operators achieve expert-level results. Notably, such systems continuously improve; as new data on weld outcomes is fed in, the AI refines its rules and solutions, making the knowledge base richer over time.
9. Root Cause Analysis for Defects
AI analytics can sift through vast amounts of welding process data to pinpoint patterns and root causes of defects. In a complex manufacturing environment, a weld defect (like porosity or a crack) might result from a subtle combination of factors – e.g., a slightly dirty material surface plus a minor power fluctuation. Traditionally, engineers rely on experience and trial-and-error to diagnose such issues. AI can dramatically speed up this analysis by correlating quality outcomes with process parameters, environmental conditions, operator actions, and more. Essentially, it learns what sequences of events or settings often precede a defect. Armed with that insight, quality engineers can address the true root cause – whether it’s a faulty gas regulator causing porosity or an improper weld sequence causing distortion. Over time, this leads to continuous improvement: the same defects are less likely to recur because their underlying causes have been identified and eliminated. AI-based root cause analysis turns a wealth of shop-floor data into actionable knowledge for improving welding processes.
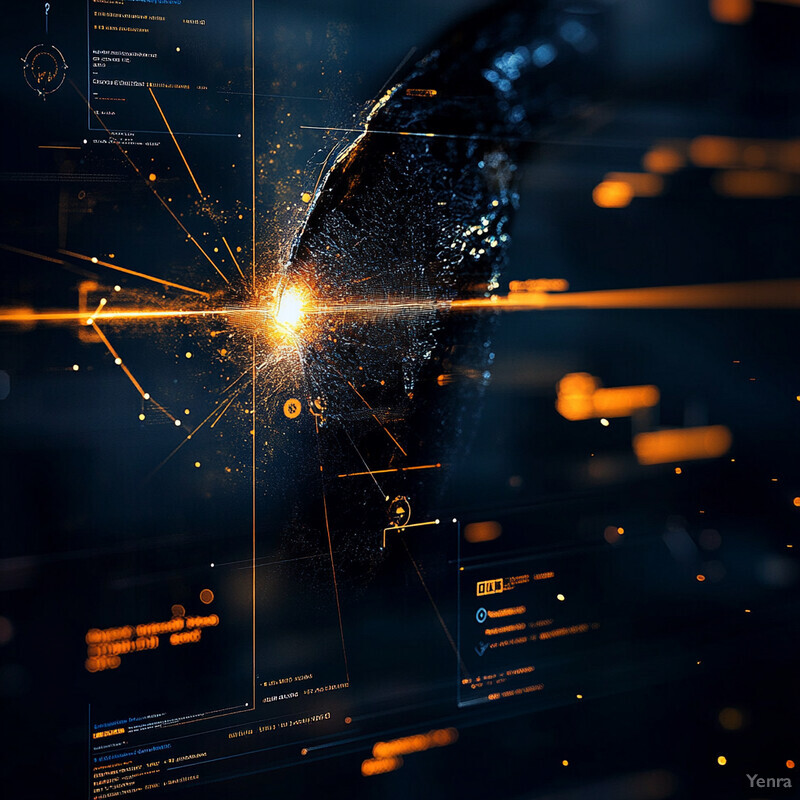
Implementations of AI for root cause analysis have shown tangible benefits in welding quality improvement programs. For example, an AI system at an automotive manufacturer analyzed hundreds of variables from robotic welding cells (current, wire speed, humidity, fit-up gap, etc.) along with the occurrence of defects in each weld. The model discovered that a specific combination of slightly low shielding gas flow and high travel speed was statistically linked to increased porosity rates in one weld line. By flagging this pattern, engineers traced the root cause to a mis-calibrated flow meter and corrected it, reducing porosity defects by ~40% in subsequent production. Similarly, advanced AI inspection platforms now not only detect defects but categorize their specific types, which greatly aids root-cause analysis. For instance, an AI vision system might distinguish between undercut vs. overlap vs. crater crack. Each of those defect types has different causes; by identifying them, the system can suggest targeted remedies (e.g., overlap might prompt “check travel speed consistency”). In one reported case, an AI-driven analysis tool processed welding incident reports, sensor logs, and even operator notes to find that a certain batch of steel had a slight chemical variation leading to weld cracking. This level of analysis – considering materials data that a human might overlook – allowed the company to adjust its material specification and virtually eliminate that crack issue. The key theme is that AI can reveal cause-effect relationships hidden in large data sets, giving engineers a data-backed diagnosis for welding problems rather than educated guesswork.
10. Wear and Tear Prediction on Equipment
AI-powered predictive maintenance is helping foresee when welding equipment and consumables will wear out or fail, so they can be replaced before causing quality issues. In welding, components like contact tips, nozzles, electrodes, and even robotic joints gradually degrade with use. Traditionally, these might be changed on a fixed schedule or when an obvious problem occurs (e.g., a torch tip burns back). Now, AI models monitor signals of wear – subtle increases in electrical resistance, changes in arc stability, shifts in force feedback, etc. – and learn to predict the remaining useful life of those parts. For example, the system might recognize that a slight increase in welding voltage variance correlates with a contact tip nearing end-of-life. Armed with that prediction, maintenance can be performed proactively during a scheduled downtime rather than after a sudden failure mid-production. This minimizes unplanned stops and ensures weld quality isn’t compromised by worn equipment (since, for instance, a worn spot-welding electrode can produce weak welds). In essence, AI is moving welding maintenance from reactive to predictive, improving both reliability and quality.
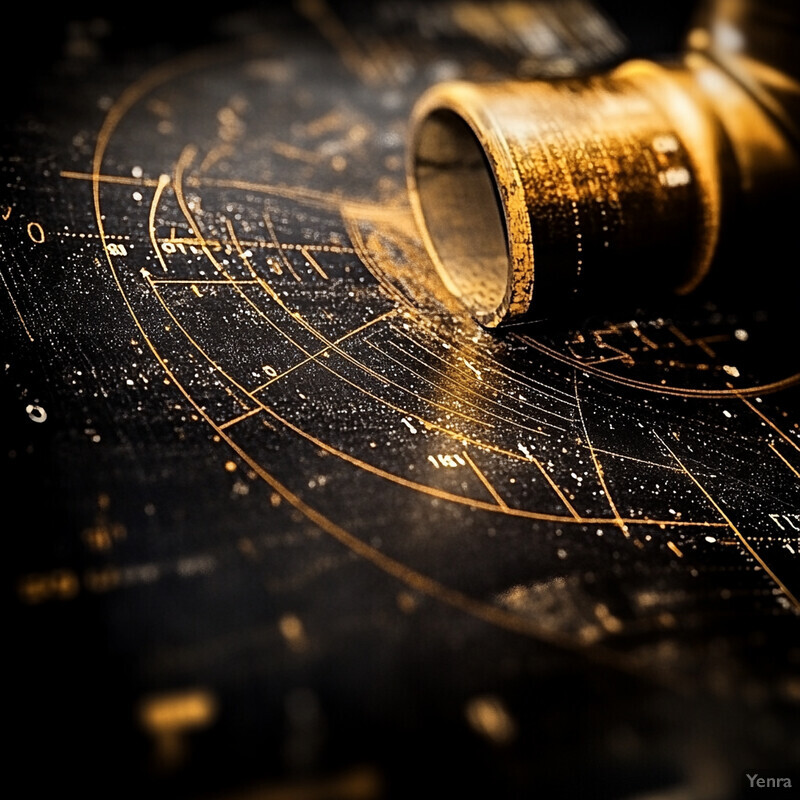
A clear example comes from resistance spot welding (RSW) in the auto industry, where electrode cap wear directly affects weld strength. A 2024 study by Panza et al. developed a machine learning tool to assess the impact of electrode wear on spot weld quality. By analyzing sensor data like electrode displacement and force over many welds, their AI could classify welds into quality categories with about 90% accuracy, effectively gauging when electrode wear had degraded weld strength beyond acceptable limits. This enabled them to recommend exactly when to redress or replace the electrode caps to maintain quality, rather than relying on a fixed number of welds or guesswork. In another case, a welding robot manufacturer used AI to monitor the torque and current draw of robotic axes during welding; the AI predicted incipient wear in a robot’s drive system months in advance, allowing a planned component swap that avoided a line stoppage. These predictive systems often draw on multi-sensor inputs: for arc welding, combining electrical signal analysis with visual monitoring of the arc and sound can yield a comprehensive “health signature” of the welding torch. As one report noted, AI can even use vibration and thermal imaging data from welding machines to predict failures of components like wire feeders or power supplies. The overall impact is significant reduction in downtime and more consistent weld quality – by ensuring the equipment is always in good condition, weld variability due to tool wear is substantially minimized.
11. Machine-to-Machine Communication
In advanced “smart factories,” AI enables welding machines and robots to communicate and cooperate with each other directly. Rather than operating in isolation, multiple robotic welders on a production line can share quality data and coordinate their actions in real time. For example, if one robot’s weld is running hot, it could signal the next robot down the line to adjust its parameters for the remaining welds on that part. Or, in a scenario where two robots weld opposite sides of a large structure, AI coordination ensures their work is synchronized (avoiding distortion or conflict). This machine-to-machine (M2M) communication, facilitated by AI algorithms, leads to a more harmonized production flow with all robots working as a team. The benefit is improved consistency across all welding stations and the ability to adapt collectively to variations in the production (like speeding up or slowing down together to match line throughput). In essence, AI acts as the conductor of an orchestra of welding robots, ensuring they work in concert for optimal quality and efficiency.
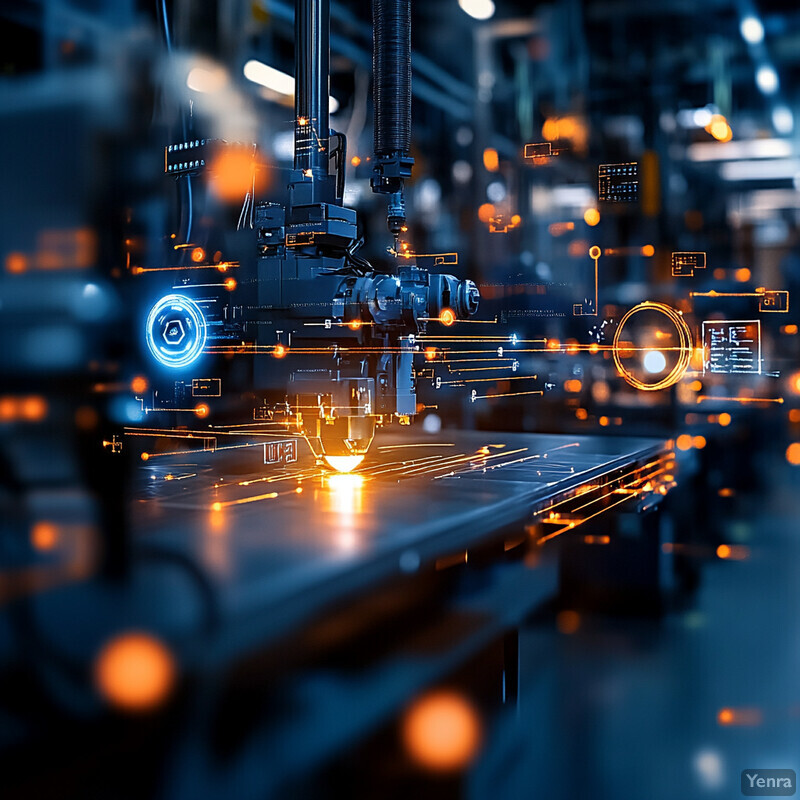
Researchers are beginning to demonstrate tangible benefits of coordinated, AI-driven robot networks in manufacturing. A 2024 review on welding automation noted that robotic collaboration involves the coordination of multiple welding robots to perform tasks collectively, and that machine learning techniques are being applied to manage this coordination. In practical terms, one implementation in a car factory linked six welding robots so that they dynamically balanced their workload: if one robot detected a slight delay (perhaps due to a sensor calibration cycle), it notified upstream robots to add a small buffer in their cycle so as not to pile up parts – all autonomously. This AI scheduler improved overall line throughput by a few percent and prevented quality drops that occur when robots are rushed or waiting. Another case from aerospace had dual robots welding a single large component; by sharing positional data and using AI to adjust their paths, the two robots managed to weld simultaneously without interfering, something that reduced total weld time by 30% compared to sequential welding. The key enabler is the AI “brain” that processes input from all machines and optimizes the global outcome (like minimizing total cycle time or ensuring uniform heat input across multiple welds). In a 2025 study, an AI-based scheduling algorithm for a multi-robot cell achieved ~34% better performance (in makespan reduction) than a baseline approach, highlighting how effective global optimization can be. These results underscore that connecting welding robots via AI not only improves quality consistency but also raises productivity by orchestrating their actions intelligently.
12. Adaptive Positioning in Complex Geometries
AI helps welding robots intelligently navigate and weld complex part geometries that were traditionally very challenging. In intricate assemblies – with tight corners, deep grooves, or hard-to-reach joints – a fixed programming approach might not guarantee proper torch orientation or reach. AI-powered systems use sensor feedback (like 3D vision or laser scanners) to understand the geometry in real time and then adjust the robot’s path or posture adaptively. Essentially, the robot “figures out” how to approach a difficult joint: it might alter its angle of approach or sequence of motions to ensure the weld bead is placed correctly. This is often combined with advanced path-planning algorithms (sometimes using machine learning or optimization) that can avoid collisions and find feasible trajectories in confined spaces. The result is that even highly complex or enclosed weld joints can be welded with precision, without manual intervention. This capability expands the range of parts suitable for robotic welding, improves consistency in areas that previously relied on human welders, and reduces the risk of missed or defective welds in complicated assemblies.

There have been significant strides in this area using deep learning and optimization techniques for robot path planning. A 2024 study by Shi, Zhang, and Kong integrated a deep neural network with a genetic algorithm to achieve optimal welding robot path planning for obstacle-rich environments. Their method improved the smoothness of motion through complex joint configurations, finding collision-free paths with faster convergence than traditional planners. In practical terms, the AI-planned paths allowed the robot to weld in narrow grooves with fewer re-orientations and no crashes, something that would be difficult to program manually. Another example comes from shipbuilding: multi-robot systems have been used to weld large ship sections where each robot’s access is limited. An AI-based scheduler had to decide buffer positions and approach strategies so that all welds in cramped layouts were completed optimally. The success of that system – which outperformed basic algorithms by over 30% in efficiency – underscores AI’s role in solving complex spatial problems in welding. Industrially, companies like Boeing have reported using AI-driven robotic cells where vision systems map an aircraft component’s geometry and automatically generate weld paths that navigate around fixtures and tight spots. They’ve noted improved weld consistency in these hard-to-reach areas and a reduction in the need for expensive custom tooling. As these examples show, adaptive positioning enabled by AI means robots can “think” their way through challenging geometry, maintaining precise alignment and travel even in less-than-ideal circumstances.
13. Real-Time Weld Pool Geometry Control
AI systems can monitor the shape and behavior of the weld pool in real time and adjust conditions to maintain the ideal pool geometry. The weld pool (the molten metal puddle during welding) is a key indicator of weld quality – its size and shape influence penetration depth, bead width, and avoidance of defects like undercut or overlap. Traditionally, controlling weld pool geometry is a skill that experienced welders develop by eye, adjusting heat or speed as needed. Now, with sensors like high-speed cameras or photodiodes observing the pool, AI algorithms can continuously evaluate features such as pool width, length, and oscillation. If the pool starts to get too wide (risking excessive penetration or sagging), the AI might decrease current or increase travel speed; if it’s too narrow (risking lack of fusion), it can slow down or add heat. These adjustments happen in fractions of a second. By keeping the molten pool within optimal dimensions throughout the weld, AI ensures the resulting solidified bead has the desired geometry and strength. This capability greatly reduces defects and variability, leading to more consistent weld quality even across varying positions or operators.
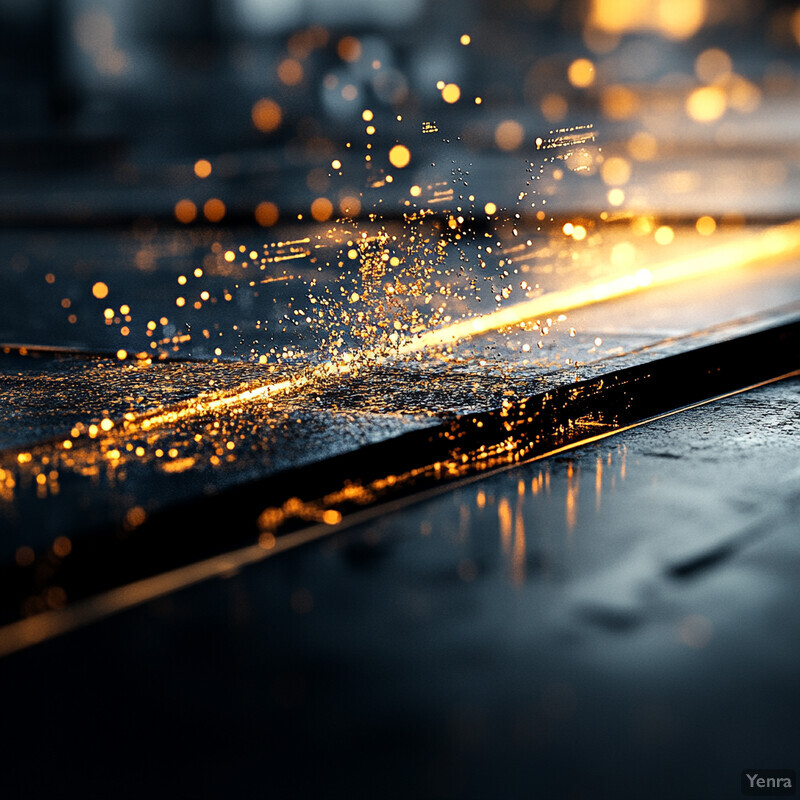
Cutting-edge work in adaptive welding control underscores how effective real-time pool monitoring can be. One example is an AI system for GTAW (TIG welding) that uses a vision-based CNN to detect the weld pool and electrode positions and then predict the resulting bead geometry on the fly. This neural network-driven feedback loop essentially mimics a skilled welder’s eyes and intuition. In trials on a multi-pass weld, the AI managed to keep bead width and reinforcement within tight tolerances pass after pass, whereas manual control showed more variation. Academic studies have also shown that incorporating weld pool sensors into closed-loop control yields tangible improvements: a 2023 paper reported that an image-based algorithm could adjust welding current in real time to correct bead width deviations under different groove conditions, improving bead width consistency by over 25% compared to open-loop welding. Moreover, companies are exploring laser-based pool sensing – measuring pool oscillation frequency – combined with AI models to adjust parameters for optimal penetration. For instance, if the AI detects via infrared sensors that the trailing end of the pool is cooling too quickly (implying potential undercut), it can momentarily pause or weave the torch to deposit more metal there. Early adopters of these technologies in pipe welding have noted reductions in defects like lack of fusion and more uniform weld cross-sections. All these developments point to AI’s ability to do what was once only possible by the most practiced human welders: understand and control the molten pool in real time for perfect bead shapes.
14. Data-Driven Tool Selection
AI is enabling a smarter selection of welding tools and consumables (such as electrode types, filler wires, shielding gases, and even welding machines) based on data rather than trial-and-error. Traditionally, choosing the optimal welding wire or parameters for a new job can involve consulting manuals and performing multiple test welds. Now, manufacturers are building databases of past welding projects – including materials, joint types, welding settings, and quality outcomes – and using machine learning to identify which combinations yielded the best results. When a new job comes up, the AI can quickly recommend, for example, a particular wire alloy and diameter and a specific gas mixture that have a proven high success rate on that material and thickness. It can also suggest starting parameter sets that are most likely to succeed. This data-driven approach reduces guesswork and setup time. In effect, the AI learns from thousands of welds and becomes a recommendation engine for optimal tools and settings for any given task, ensuring that welding operations begin with the best possible setup to achieve quality and efficiency.
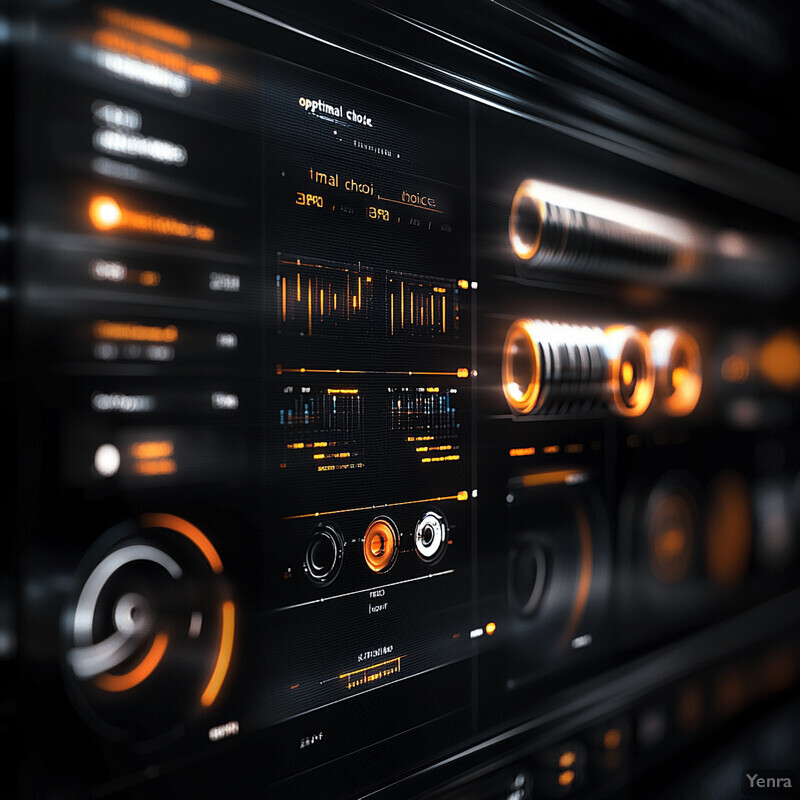
Practical implementations of this concept have emerged in recent years. One system, developed as part of an “AI assistant” for welding design, uses historical welding procedure qualification records to recommend consumables and parameters. In a pilot with a heavy equipment manufacturer, the AI analyzed past welds on high-strength steel and discovered that using a particular low-hydrogen electrode brand consistently led to higher impact toughness in cold temperatures. The company adopted this recommendation for similar welds and saw a reduction in weld failures in cold climate field tests. On the research front, Wang et al. (2023) demonstrated how an expert system combined with machine learning could generate welding process plans automatically. Their system would take input requirements (base metal grade, thickness, joint type) and output a suggested welding process, including which filler material and shielding gas to use and what parameters to set, drawn from its knowledge of what worked best in the past. During evaluation, many of its suggestions matched the choices that human experts had made independently, validating the approach. Furthermore, the system uncovered some non-obvious recommendations – for instance, it suggested a slightly higher humidity tolerance stick electrode for an outdoor repair weld, citing past success under similar conditions, which wasn’t immediately obvious from standard guidelines. The aerospace industry is also leveraging such AI: when qualifying welds for new alloys, AI algorithms parse through material properties and prior weld data to highlight candidate filler metals that maximize properties like tensile strength and corrosion resistance. By adopting AI-driven tool selection, companies have reported shorter procedure development times and more consistent quality, since the chosen consumables and initial settings are optimal from the start rather than found through costly experimentation.
15. Virtual Welding Simulations
AI is advancing welding through sophisticated virtual simulations that predict welding outcomes before any actual welding is done. These AI-powered simulators allow engineers and welders to test different welding parameters, sequences, or techniques in a computer environment that behaves like the real world. For example, one can simulate how changing heat input or travel speed would affect weld penetration and distortion on a particular joint design. Because the simulations are informed by both physics and AI (often trained on real welding data), they can forecast results with high accuracy. This means fewer physical trial-and-error welds are needed. By using virtual welding simulations, teams can optimize procedures (like finding the combination of settings that yields a defect-free weld) and even train operators in a risk-free setting. Ultimately, this leads to improved first-pass weld quality, since the process has been refined digitally; it also saves time and material that would otherwise be spent on experimental welds.
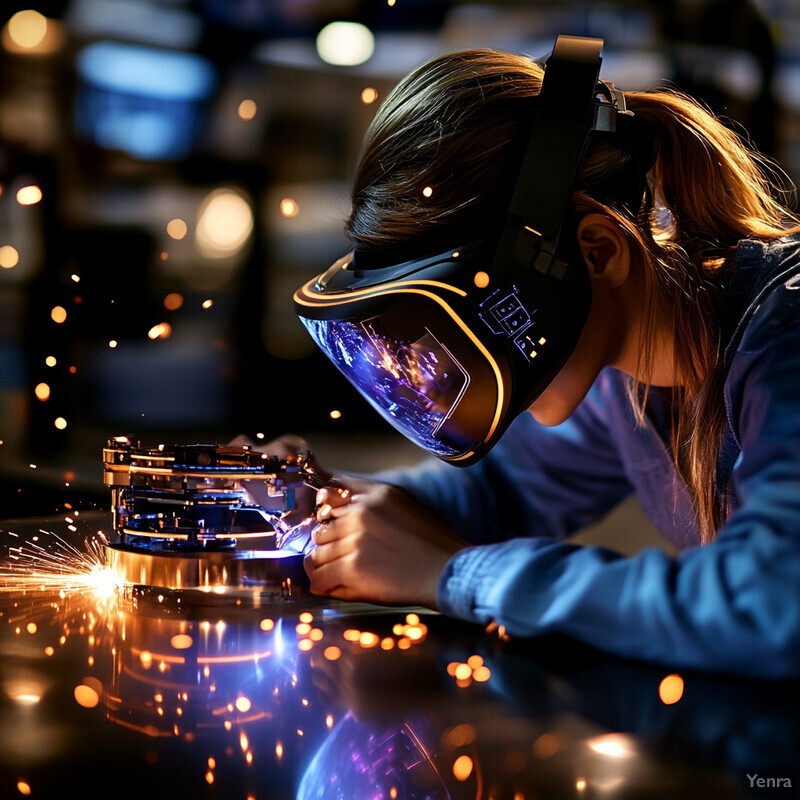
The concept of a “digital twin” for welding has become a reality in recent years. In friction stir welding (FSW), for instance, researchers developed a 5-dimensional digital twin model of the robotic welding process that runs in parallel to the real operation. This model integrates real sensor data with a simulation – effectively an AI-enhanced simulation – to understand and predict weld pool evolution and potential defects. In testing, the digital twin could predict issues like improper tool penetration or material flash and suggest parameter tweaks before those issues occurred in the real weld. Similarly, commercial simulation software (like FLOW-3D WELD, released in 2025) uses AI to more accurately model complex phenomena such as fluid flow and heat transfer in welding arcs. Manufacturers report that by using such simulators they achieved “right-first-time” welds much more often. One automotive supplier shared that after simulating and optimizing a weld sequence on an AI-driven platform, their first physical prototype had 90% fewer distortion problems – a huge improvement over previous methods. Additionally, virtual reality (VR) welding training systems augmented by AI (which simulate welding with realistic feedback) have been shown to improve trainee outcomes: a study found that students who practiced with an AI-driven simulator made significantly fewer mistakes when they moved to real welding, as the simulator had already taught them proper technique and parameter selection. All these examples highlight that AI is making welding simulations far more predictive and useful. They’re not just animations; they are decision-support tools that closely mirror reality, enabling scenario testing and optimization in the digital space.
16. Enhanced Training Programs
AI is transforming how welders are trained by providing real-time feedback and personalized coaching. Traditional welding training relies on an expert instructor observing a student and giving advice after a weld is done (or pausing them mid-weld). With AI-enhanced training tools, feedback is instantaneous and data-driven. For example, a trainee might wear an augmented reality helmet that shows prompts or corrections (like “slow down” if their travel speed is too high, or adjusting their torch angle in real time). AI systems can analyze a trainee’s welding in terms of measurable parameters – stick out length, travel angle, speed consistency, arc stability – and compare them against optimal ranges learned from experienced welders. The trainee then gets actionable suggestions on the spot. Additionally, AI can track progress over time and tailor exercises to address a learner’s specific weaknesses (much like a virtual coach). This not only accelerates the learning curve, allowing novices to attain proficiency faster, but also standardizes training quality (every student gets thorough feedback, not just the ones the instructor can physically observe at a time). Overall, AI-driven training means better-skilled welders and a more competent workforce.
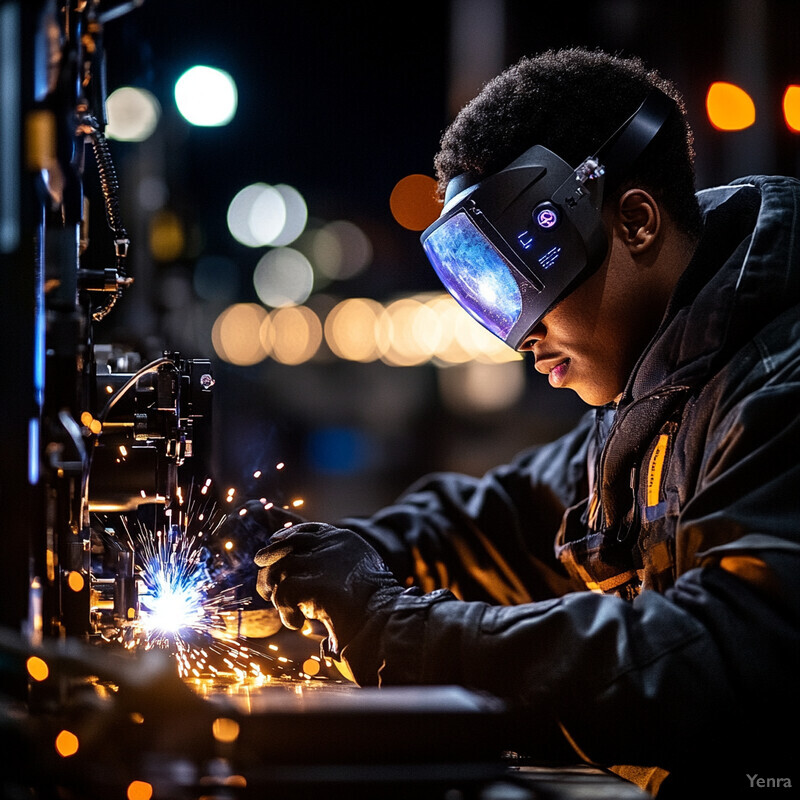
A striking example comes from Carnegie Mellon University, where researchers developed an extended reality (XR) welding helmet with an AI model for feedback. In trials, student welders using this system received visual cues in their helmet display that guided them to maintain correct gun angle and travel speed. The AI would detect deviations – for instance, if the torch tilted too much – and immediately flash an icon or arrow indicating how to adjust, all without the student breaking their focus on the weld. Over a cohort of trainees, those who trained with the AI-XR system achieved proper technique faster and produced higher-quality practice welds compared to those under traditional instruction. Another project (“AI-Weld Coach”) employed machine learning to evaluate welding audio signals: since expert instructors often judge weld quality by sound, the AI was trained to do similarly and give feedback like a human coach (“increase current” if the sound indicated a cold weld) in real time. In a vocational school pilot, the AI-Weld Coach’s guidance led to a 25% improvement in student pass rates on certification weld tests. Furthermore, an IEEE study in 2024 demonstrated an AI system for objective skill assessment – it analyzed factors like bead profile and consistency to score trainees’ welds, removing human bias and giving learners concrete targets to improve. Welding instructors involved in these trials noted that AI doesn’t replace them but amplifies their reach: while an instructor can’t watch every student at every second, an AI can, ensuring no bad habit goes unchecked. The end result is more efficient training sessions and welders who are production-ready in less time.
17. Closed-Loop Control Systems
Closed-loop control in welding means the process can self-correct in real time without human intervention, and AI is making this a reality. In a traditional open-loop setup, a welding machine runs preset parameters and doesn’t adjust if conditions change; closed-loop control, by contrast, constantly monitors outputs (weld quality indicators) and adjusts inputs (parameters) to stay on target. AI brings advanced sensing and decision-making to closed-loop welding. It can continuously compare the actual weld results (via sensors like cameras, temperature probes, arc sensors) against the desired outcome, and if a deviation is detected – say the weld pool is a bit too cold – the AI controller immediately tweaks settings (like bumping up current for a moment) to compensate. These adjustments happen in fractions of a second and repeat continuously, forming a feedback loop. The result is a remarkably stable welding process that can maintain stringent quality tolerances even with external disturbances (like minor part fit-up issues or power fluctuations). AI essentially gives the welding machine a form of “autopilot,” actively keeping the process within spec.
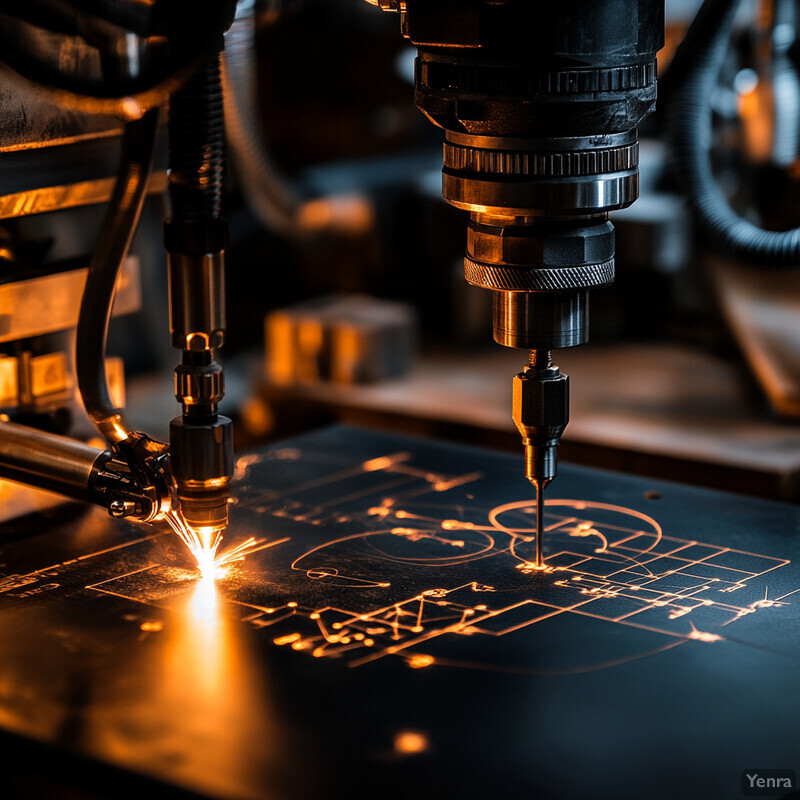
Industry researchers have highlighted the impact of AI in achieving true closed-loop welding control. Dr. Carlo Holly of Fraunhofer ILT remarked that “AI has the potential to close control loops”, enabling machines that readjust themselves during the process based on continuous data evaluation. We see this in practice with systems like laser welding lines where AI monitors seam position and adjusts robotic path in real time – if the seam drifts by even 0.1 mm, the AI-controlled robot corrects its course mid-weld, something impossible with pre-programming alone. A concrete example is an AI-driven MIG/MAG welding system that was demonstrated to adjust its wire feed speed and voltage on the fly to maintain a consistent weld bead height. In tests, when plate thickness was varied unexpectedly, the closed-loop AI controller still produced uniform beads, whereas a conventional open-loop setup resulted in over-penetration on thinner sections. Moreover, a 2024 study presented an “inline machine learning-driven closed-loop quality control” for welding, which merged multiple sensor signals to predict weld quality in real time and auto-correct parameters accordingly. This system was able to reduce the occurrence of defects by approximately 50% compared to a similar line running in open-loop mode, primarily by catching and correcting issues (like slight torch-to-work distance changes) instantaneously. These developments illustrate the power of AI in closing the loop: welding processes that once needed constant human oversight can now self-regulate. The result is not only higher quality and consistency but also a more autonomous operation that can adapt to variations on the fly, essentially “learning” the optimal control actions to produce defect-free welds every time.
18. Intelligent Scheduling and Workflows
AI is being used to optimize the scheduling of welding operations and to manage workflows in a fabrication setting, ensuring that quality is maintained while improving efficiency. In a busy production line, there are many welding tasks that need to be sequenced: which welds to do first, how to allocate tasks among multiple welding stations, when to perform inspections or cooling periods, etc. Traditionally, setting up these schedules is manual and based on experience, which may not be fully efficient. AI scheduling algorithms can analyze all the variables – machine availability, welding durations, required cooling time between passes, worker shifts, priority of jobs – and produce an optimized plan. For example, an AI might schedule critical welds earlier in a shift when welders are most alert, or stagger the start times of robotic welders to even out power load. It can also dynamically reschedule on the fly if conditions change (say a machine goes down or a rush job comes in). The benefit is a smoother workflow: no station is overburdened or waiting idle unnecessarily, and each weld is given the appropriate amount of time and resources, indirectly boosting quality (since rushed or delayed welds can cause defects). Essentially, AI acts like a smart coordinator, orchestrating the welding production to run at peak performance without compromising quality standards.
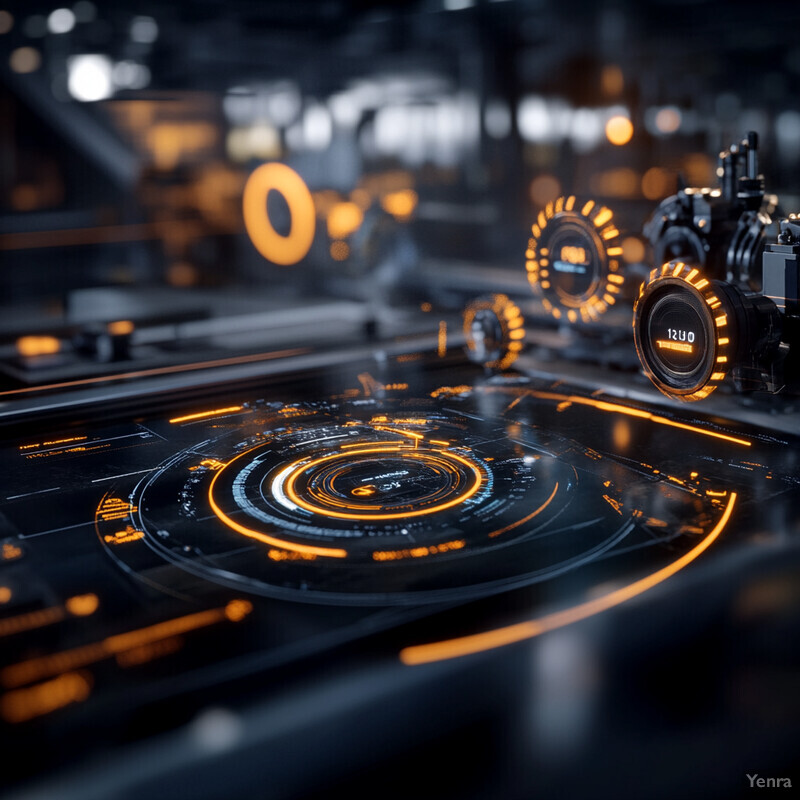
The impact of intelligent scheduling is evidenced by case studies in manufacturing. A Scientific Reports study in early 2025 addressed a complex multi-robot welding job shop scheduling problem with AI techniques. By using a genetic algorithm optimized with domain knowledge, the AI scheduler was able to reduce the overall production makespan by approximately 34% compared to a baseline algorithm. This is a dramatic efficiency gain, meaning jobs finished much faster, yet none of the weld quality checks were skipped or rushed. Another example comes from heavy equipment manufacturing, where implementing AI scheduling for welding and machining tasks led to an estimated 20% increase in throughput. The AI system in that case constantly reprioritized welding tasks and coordinated with upstream material prep so that welders always had the right parts at the right time, avoiding idle time. Importantly, it also scheduled in preventive maintenance for machines (as predicted by AI) so that breakdowns would not interrupt critical weld sequences. According to a World Economic Forum report, manufacturers leveraging AI for “autonomous planning – continuous, closed-loop, fully automated planning” are able to keep supply chain and production performance high even under volatile conditions. For welding operations, this translates to meeting deadlines without last-minute scrambles that often cause quality to slip. AI agents can consider myriad parameters to find the best way to maximize throughput with minimal cost or risk. Companies that have adopted such systems report not only efficiency improvements but also more consistent quality, as welders or robots are scheduled in a way that avoids fatigue and ensures proper sequencing (e.g., ensuring adequate cooling between weld passes by scheduling other tasks in between). In sum, AI-driven scheduling creates a win-win: faster production
19. Multi-Modal Inspection
AI enables the fusion of multiple types of inspection data – visual (camera images), infrared thermal, ultrasonic, acoustic (sound) – to provide a comprehensive assessment of weld quality. Different NDT (non-destructive testing) methods can catch different defect types: for instance, visual cameras might see surface flaws, ultrasonic can detect internal cracks, and acoustic sensors can hear anomalies in the arc or cooling process. Traditionally, these methods are used separately and results are interpreted in isolation. AI can combine them, correlating findings from each modality to improve accuracy. By analyzing multiple data streams together, the AI can confirm a defect through multiple evidences (e.g., a hot spot in IR and a void indication in ultrasound at the same location), reducing false positives. Conversely, it can also filter out noise that might trick a single method. The outcome is a more reliable and sensitive inspection system that can detect subtle or hidden defects that no single sensor could catch alone. This multi-modal approach gives inspectors a “holistic X-ray” of the weld – essentially seeing and hearing everything at once – to ensure nothing is missed.
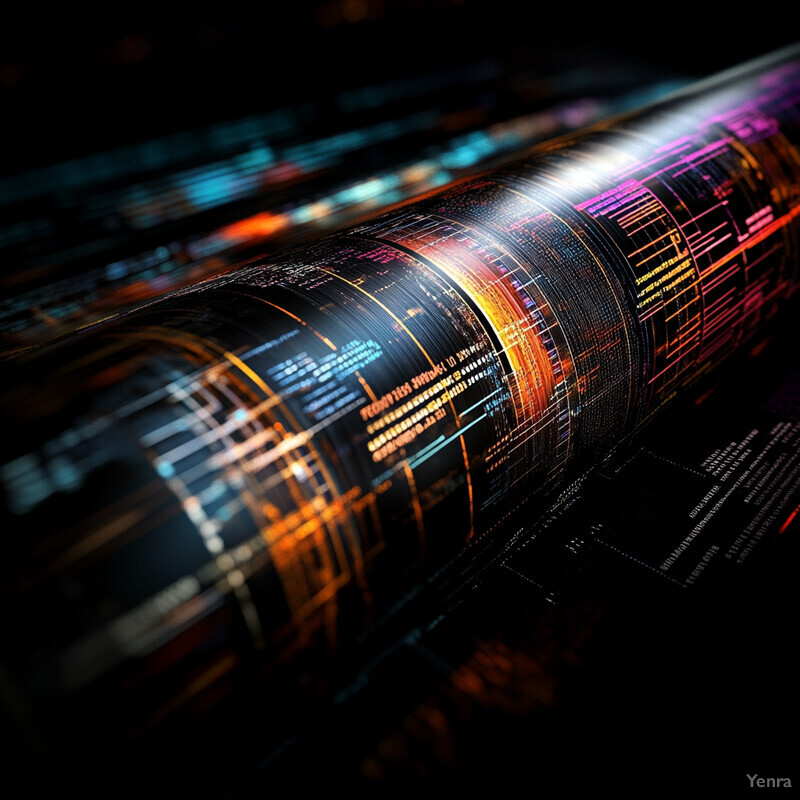
A 2024 multi-modal inspection study demonstrated the power of combining sensor data. Researchers collected over 4,000 weld samples with both camera footage and microphone audio of the welding process. Using an unsupervised deep learning model, they showed that real-time defect detection was feasible from both audio and video, and that a combined audio-visual AI model achieved an AUC (Area Under Curve) of 0.92 across 11 categories of weld defects. This high AUC indicates excellent defect discrimination performance. Essentially, some defects that produced only a slight visual indication but a clear sound signature (or vice versa) could still be caught by the AI when using both modalities. In industry, multi-modal systems are emerging as well. For example, an AI inspection solution by IBM uses both acoustic emission sensors and high-speed cameras; it was able to detect a tiny internal weld flaw in a pipeline by noticing a combination of a subtle temperature anomaly on the weld surface and a high-frequency sound burst – either signal alone was not conclusive, but together they signaled a defect, which subsequent X-ray testing confirmed. Another case at a railcar manufacturer used laser ultrasonic sensors plus optical imaging analyzed by AI: it achieved nearly a 98% detection rate for subsurface weld inclusions, far better than either method on its own. These successes align with expert commentary that integrating data from multiple inspection methods yields a “holistic view” of weld integrity, catching hidden flaws that single-method inspections could miss. Multi-modal AI inspection reduces the risk of letting defective welds slip through and increases confidence in the final product’s quality.
20. Integration with Industry 4.0 Ecosystems
Modern welding quality systems are increasingly connected into the broader Industry 4.0 ecosystem of smart factories. This means welding stations are no longer isolated; they communicate with other machines, enterprise databases, and supply chain systems. AI facilitates this integration by translating weld quality data into useful information for other processes. For instance, if a weld is identified as sub-par, the AI can automatically alert upstream processes (like cutting or fit-up) to check if a misalignment might be the cause, or downstream processes (like painting) to hold off on that part. All weld data can be tied into the product’s digital twin or manufacturing execution system, providing traceability – one can trace a defect back to the exact machine, operator, settings, and material batch. Over time, this connectivity allows continuous improvement across the supply chain: design engineers get feedback on how certain designs affect weld quality; procurement can see if a certain batch of material led to more defects, etc. Essentially, welding quality assurance becomes a node in the smart factory network, contributing to and benefiting from the collective intelligence of the whole production ecosystem. The result is a more agile and transparent manufacturing process where quality issues are caught and addressed not just at the weld, but holistically.
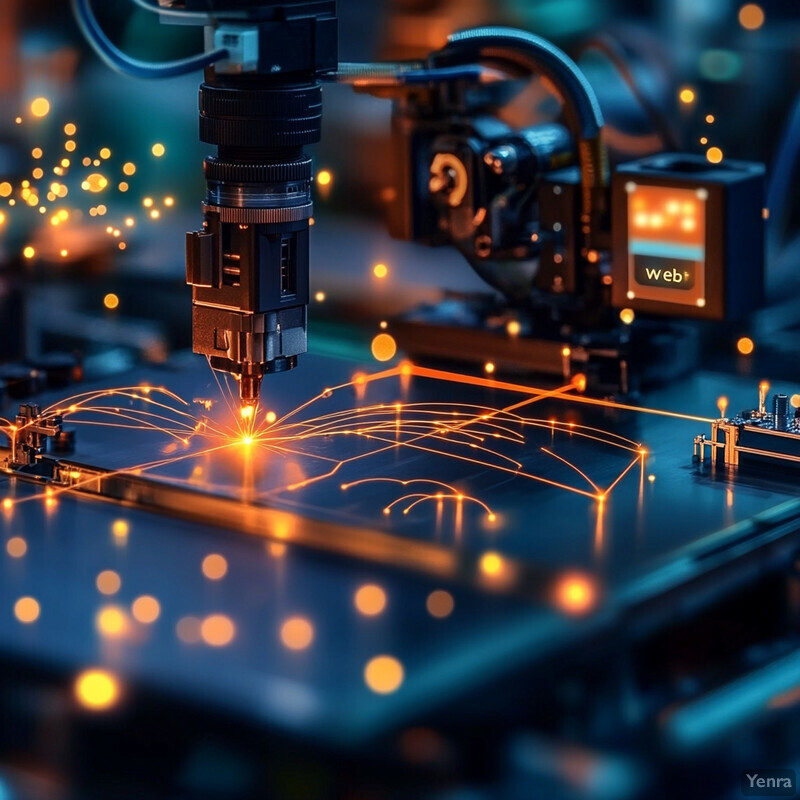
In practice, companies adopting Industry 4.0 approaches report significant benefits from this kind of integration. One example: A heavy machinery manufacturer integrated their AI weld inspection data with their manufacturing execution system. When the AI flags a weld defect, the system automatically checks the part’s history (via the digital thread) – it might find, for instance, that the part came from a certain supplier batch or was formed on a particular press that had calibration issues. This traceability has enabled root-cause fixes beyond just re-welding the joint file-ecnl4spmwbvep3mtrdpwgj file-ecnl4spmwbvep3mtrdpwgj . Additionally, at an automotive plant, weld quality data is shared in real time with assembly robots further down the line. If a weld on a car frame is slightly below ideal (but still acceptable), the assembly robot is instructed (by the central AI system) to adjust its tightening sequence to compensate for the marginally weaker joint – effectively using quality data to inform downstream process settings, which improved overall product robustness. Industry-wide, analysts note that 80% of all people will interact with smart robots daily by 2030, many of those in manufacturing. In welding, this trend is seen through collaborative robots (cobots) working with humans and feeding data to centralized AI. For example, a cobot welding a custom order will feed its quality data to a cloud AI, which might adjust the welding procedure for the next custom job based on collective learning from many factories (this is already being piloted in some networked job shops). The continuous, closed-loop planning that AI enables at the supply chain level ensures that when a welding issue is discovered, not only is that weld fixed, but the information propagates through design, planning, and logistics to prevent recurrence. A concrete metric from a case study: an aerospace supplier integrated weld QA data with their inventory system and reduced material waste due to welding defects by 15%, because the AI could suggest re-routing slightly non-conforming parts for rework or different use instead of scrapping them outright. These examples show how AI-driven welding QA, when woven into the Industry 4.0 fabric, yields a smarter, more responsive production system where quality is a shared responsibility and continuous improvement is data-driven across the board.