1. Real-Time Sensor Data Analysis
Continuously monitoring data from track and train-mounted sensors can catch subtle anomalies immediately. By comparing vibration, acceleration, pressure, and other sensor readings against normal baselines, AI can flag early signs of trouble (like a slight increase in track vibration that precedes a crack). The significance is that maintenance crews get alerted within minutes of a deviation, allowing them to respond before a minor issue escalates. In practice, this means less unplanned downtime and a safer railway, because potential faults (a developing rail crack or wheel imbalance) are addressed before they turn into service-disrupting failures. Overall, real-time sensor analysis makes high-speed rail operations more proactive – the system is constantly self-checking and notifying staff of any abnormal behavior to keep the network running smoothly and safely.
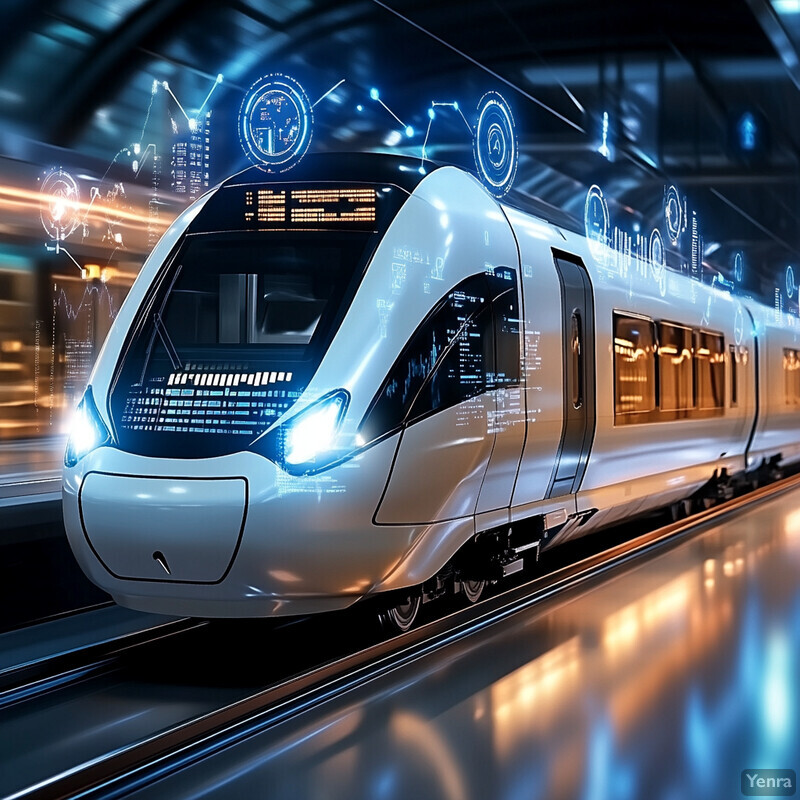
China’s high-speed rail network illustrates the power of real-time monitoring: an AI system in Beijing ingests live data from 45,000 km of track and can alert maintenance teams to anomalies within 40 minutes, with about 95% accuracy. This rapid detection contributed to an 80% reduction in minor track faults in one year.
2. Predictive Maintenance Scheduling
Predictive maintenance uses AI models to forecast when a component is likely to fail, so maintenance can be done just in time. Instead of inspecting or replacing parts on a fixed schedule (which might be too early or too late), rail operators can focus on the equipment that actually needs attention based on data-driven predictions. This technique draws on historical failure data, real-time sensor inputs, and operating conditions (speed, load, etc.) to estimate each asset’s remaining useful life. The practical utility is huge: crews can replace a rail or service a wheel right before it would fail, thereby avoiding both unexpected breakdowns and unnecessary routine overhauls. In high-speed rail, where components like wheels, rails, and overhead wires are expensive and critical, predictive maintenance scheduling optimizes resources – it reduces maintenance costs, prevents service interruptions, and extends the lifespan of assets by ensuring they are neither under- nor over-maintained.
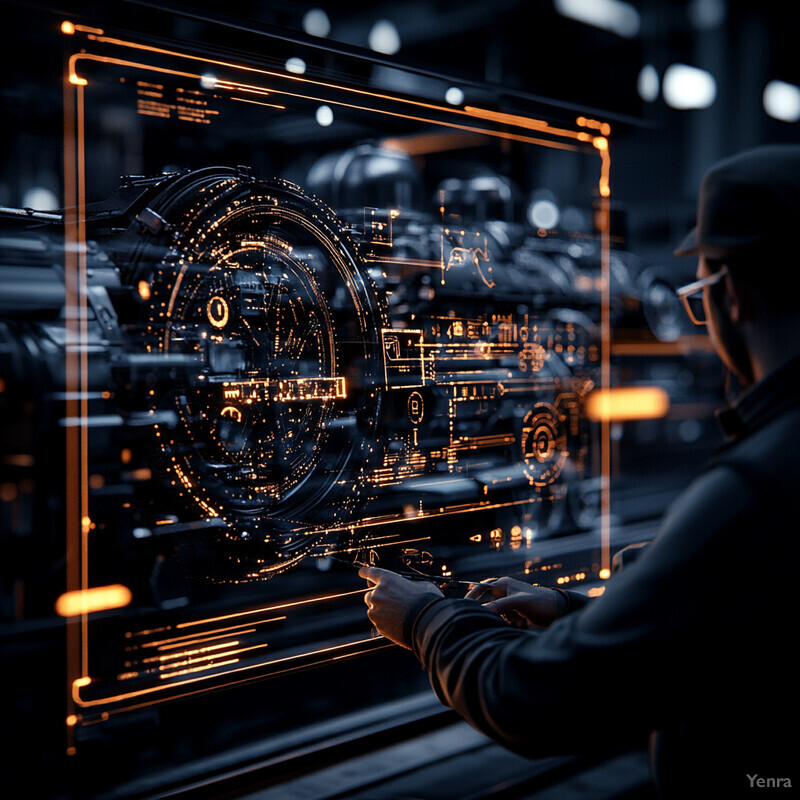
In one major European rail network, implementing AI-driven predictive maintenance cut unplanned downtime by 30% and extended the life of critical components by up to 20%, compared to traditional routine maintenance. This reflects how forecasting failures allows timely interventions that avoid breakdowns and maximize asset longevity.
3. Computer Vision for Track Inspections
AI-based computer vision automates the visual inspection of tracks, sleepers (ties), and fasteners using cameras and image recognition algorithms. High-speed rail lines can span hundreds of miles, and inspecting them manually is slow and prone to human error. With this technique, high-resolution cameras (mounted on inspection trains or drones) scan the track, and deep learning models automatically detect defects like cracks in rails, broken fasteners, misaligned track, or foreign objects on the line. The significance is faster and more frequent inspections – the AI can analyze video frames in real time as the train moves, meaning even a small crack or a loose bolt is flagged immediately for repair. This improves safety because issues are caught early, and it reduces labor costs and track downtime since inspections don’t require as many slow manual patrols. Essentially, computer vision allows rail infrastructure to be monitored continuously at high speed, which is especially valuable for high-speed rail where any track flaw could have serious consequences.
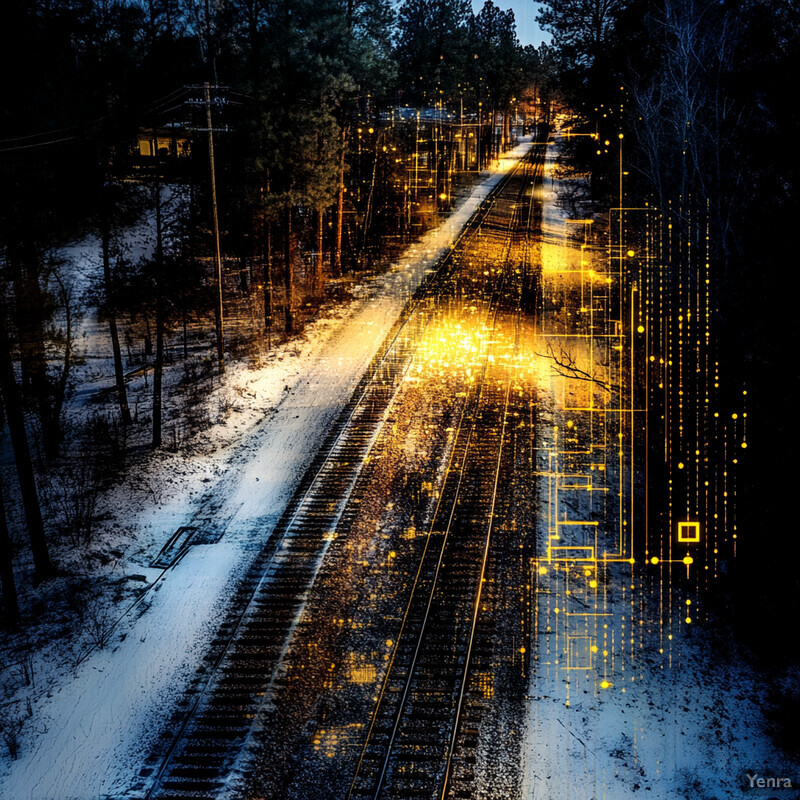
In India, an AI-powered track inspection system called TrackEi™ was launched that uses cameras and deep learning to perform real-time defect detection at over 60 miles per hour, identifying cracks, broken rails, and misalignments instantly as the inspection train runs. This is much faster than traditional manual inspections (which often require walking or slow vehicles), demonstrating how computer vision enables high-speed, high-volume inspection without sacrificing accuracy.
4. Thermal Imaging Fault Detection
Thermal imaging fault detection involves using infrared (heat-sensing) cameras to detect abnormal temperatures in railway components – for example, overheated wheel bearings, axles, brakes, or electrical equipment. In high-speed rail, parts can heat up rapidly if there’s friction or electrical resistance, so a thermal camera can spot a problem before it causes a failure (like a seized bearing or an electrical fire). AI comes into play by analyzing the infrared camera data in real time and distinguishing true faults from normal temperature variations. The practical utility is that maintenance crews get early warning of issues indicated by heat: if a bearing is running hotter than normal, the system flags it so the train can be stopped for inspection, preventing a potential derailment. It also means inspections can be done remotely and continuously – cameras installed along the track or on moving inspection trains can scan passing rolling stock and infrastructure for “hot spots.” Overall, thermal imaging with AI helps catch hidden defects (like internal friction in a component) that visual inspection alone might miss, thereby enhancing safety and reducing the risk of catastrophic failures due to overheating.
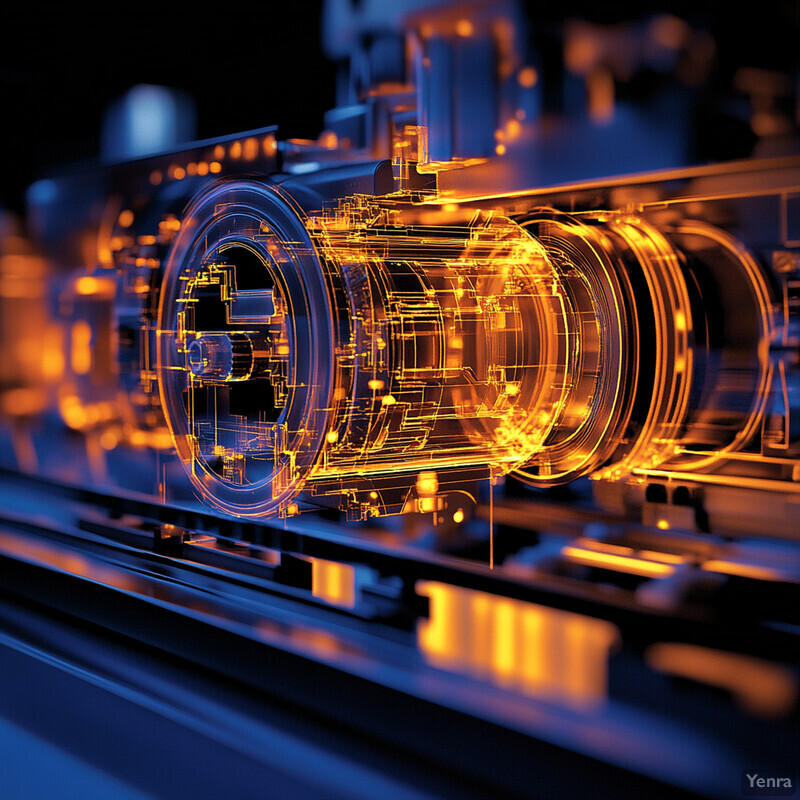
U.S. railroads have widely deployed thermal and other wayside sensors – for example, Union Pacific operates about 7,000 wayside detectors (many with infrared “hot box” sensors) which collectively generate over 16 million data points per day to monitor wheel and bearing temperatures in real time. These thermal monitoring systems immediately notify train crews if a bearing is running hot, helping to prevent accidents by catching overheating components before they fail.
5. Acoustic and Vibration Signal Analysis
This technique uses the “sound” and vibration signatures of trains and tracks to detect faults. Every mechanical component – wheels, rails, gearboxes, etc. – emits characteristic vibrations and noises during operation. AI-driven analysis of these acoustic signals can pick up anomalies like a subtle change in frequency or amplitude that indicates a developing problem. For instance, a wheel with a developing flat spot or a tiny crack will produce a slightly different sound when it hits the track, or a rail with an internal defect might cause unusual vibration patterns. By deploying microphones or vibration sensors (accelerometers) along the track or on trains, and using machine learning to model normal vs. abnormal signals, rail operators can identify faults early. The significance in high-speed rail is that many failures give a brief acoustic warning (a faint rumbling sound, an ultrasonic vibration) before they become visible or cause an incident – AI can catch these faint signals 24/7, which humans likely wouldn’t notice. This leads to early detection of issues like wheel flats, bearing defects, or rail cracks without dismantling equipment. In practice, acoustic analysis reduces unnecessary maintenance (since it pinpoints which component is actually degrading) and improves safety by providing another layer of fault detection that can “hear” problems developing in real time.
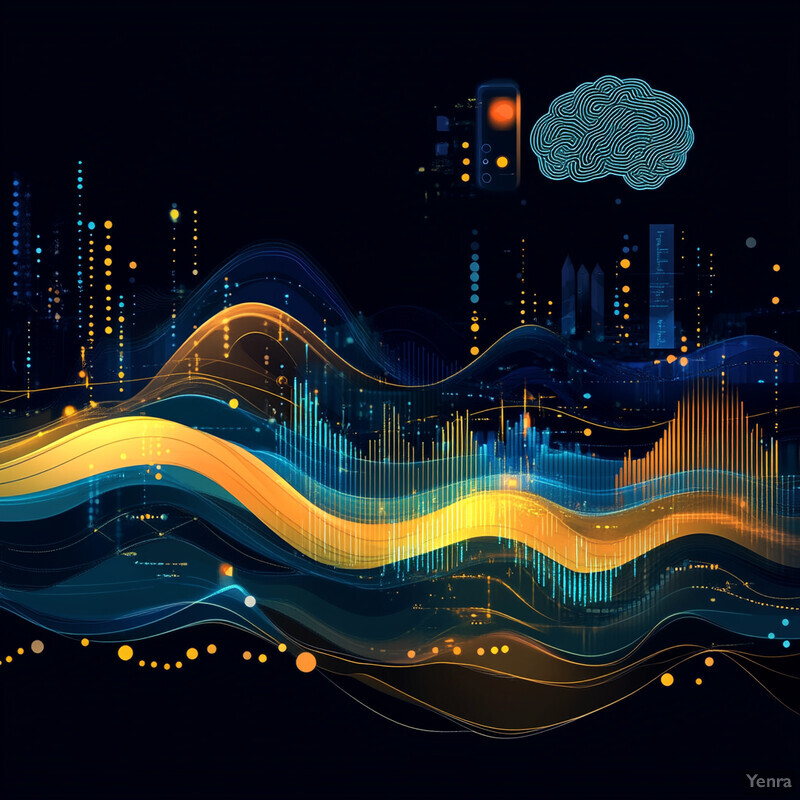
By combining acoustic data with temperature readings, AI systems can even predict failures well in advance – for example, an analysis of wayside sensor data showed that using sound/vibration data from bearing detectors together with hotbox (thermal) data, an AI could predict an overheating bearing up to 3 months before it would fail. This demonstrates how analyzing vibration “signatures” enables extremely early fault detection that would be impossible through visual checks alone.
6. Condition Monitoring of Overhead Lines
High-speed electric trains rely on overhead contact lines (catenary wires and pantographs) for power, and this approach uses AI to monitor the condition of those overhead systems. Traditionally, checking the tension and wear of overhead wires or the state of pantograph collectors required scheduled inspections (sometimes with crews visually examining wires or using measuring cars). AI-enhanced monitoring can utilize sensors, cameras, or drones to continuously inspect overhead lines for signs of deterioration – such as a frayed contact wire, a misalignment, or excessive wear on pantograph carbon strips. The significance is that overhead line failures (like a wire snap) can cause major service disruptions and safety hazards, so catching early signs (for instance, a slight change in wire height or a hotspot from electrical arcing) is crucial. AI algorithms can analyze imagery or sensor data to detect these subtle signs in real time. In practical terms, this means maintenance teams can be dispatched to fix an overhead line before it breaks, and high-speed trains won’t unexpectedly lose power due to unnoticed wire damage. It also improves safety for maintenance staff by allowing remote inspection of hard-to-reach electrified equipment (often via drone footage analyzed by AI). Overall, AI condition monitoring keeps the power supply lines of HSR healthy, reducing delays and preventing incidents like dewirement (entanglement of the pantograph and wire) which can be dangerous at high speeds.
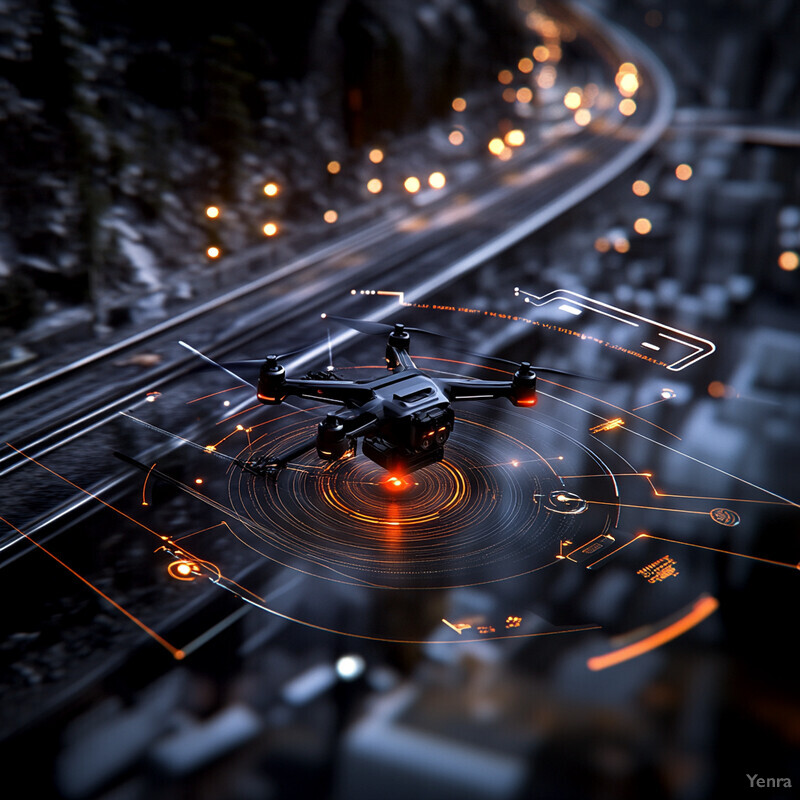
A European project (“tCat”) developed an automated overhead line inspection system that can dramatically cut maintenance efforts – it was reported to reduce overhead contact line maintenance costs by up to 80% by using a mobile mapping trolley with AI analysis. The system allows quicker and more precise checks of wire geometry and wear, highlighting how continuous AI monitoring can replace infrequent manual inspections and yield huge cost and efficiency benefits.
7. On-Board Edge Computing for Fault Diagnosis
On-board edge computing means installing AI processing units on the trains themselves (at the “edge” of the network) so that data from sensors can be analyzed locally, in real time, without relying on constant uplink to a central server. In high-speed rail, trains generate massive amounts of data every second (from accelerometers, gyroscopes, brake sensors, etc.). By equipping the train with an embedded AI computer, the system can instantly diagnose anomalies – for example, detecting a suspension issue or signaling fault and immediately advising the driver or triggering an automatic response. The significance of edge computing is the low latency: decisions (like slowing down due to a detected fault) can be made on the spot within milliseconds, which is vital at 300 km/h speeds. It also ensures fault detection continues even in areas with poor wireless connectivity, since the train isn’t dependent on sending data to a remote server for analysis. Practically, this approach improves resilience and speed of response; the train itself becomes a smart vehicle that can “know” when something is wrong. For maintenance, it means issues are logged and sometimes acted upon in real time (e.g., switching to a backup system) and then communicated to maintenance crews at the next station. Edge computing on trains ultimately enhances safety and reliability by making each train a self-diagnosing unit that doesn’t have to wait for instructions from a distant control center when a fault emerges.
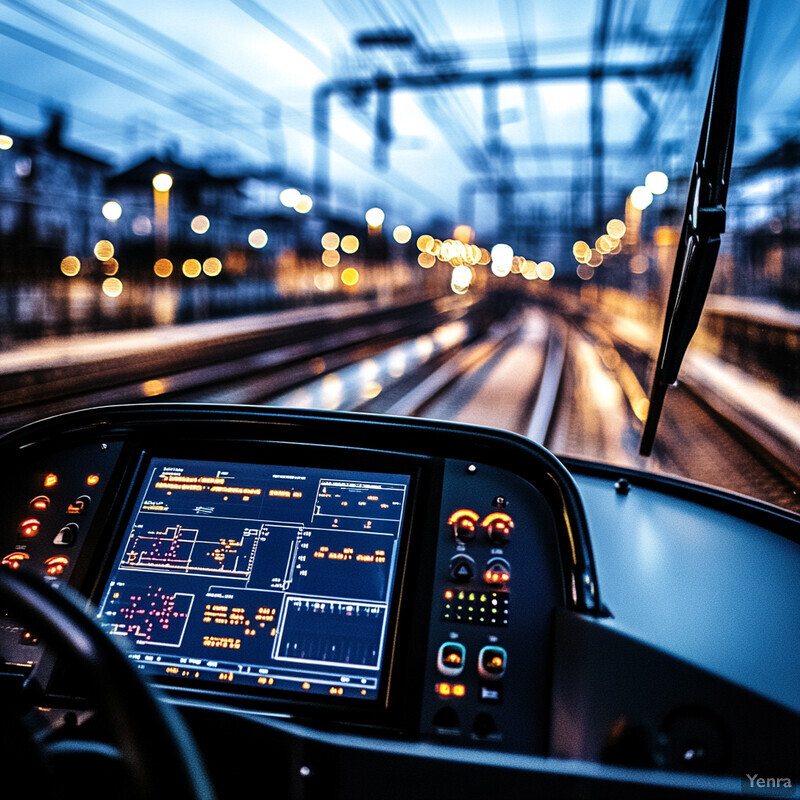
Modern high-speed trains generate enormous data streams – over 5 GB of sensor data per train per day in some cases – which is impractical to send constantly to the cloud. By processing this data on-board, AI models have achieved fault detection response times under 100 milliseconds. In other words, a train’s edge AI can recognize an anomaly virtually instantaneously (in a tenth of a second or less), then immediately signal the train to adjust or alert operators, long before a central system would even receive the raw data.
8. Sensor Fusion Techniques
Sensor fusion refers to combining data from multiple types of sensors to improve fault detection accuracy. In high-speed rail maintenance, different sensors capture different aspects of the system’s health – accelerometers might detect vibrations, microphones capture sound, LiDAR or cameras give visual positions, and so on. Individually, each sensor has some uncertainty and could produce false alerts (noise). AI fusion algorithms aggregate these diverse data streams and analyze them holistically, which often allows the system to confirm a true fault (when multiple indicators agree) or dismiss a false one (when only one sensor shows an anomaly and others do not). The significance is a higher confidence in detection and fewer false positives. For example, detecting a track flaw might be more reliable if an AI sees a pattern of a slight bump in acceleration data and a tiny crack in camera images at the same location – together they confirm a defect that either sensor alone might not definitively identify. Sensor fusion also helps in complex scenarios: one sensor might not work well under certain conditions (say, poor visibility for a camera), but another (like an ultrasonic sensor) can compensate, and AI will weigh inputs accordingly. In practice, this means more robust fault detection that works in all conditions and a reduction in missed faults or bogus alarms. For high-speed rail operators, fusion systems translate to a more stable and trustworthy monitoring system, since decisions (like issuing an alarm or not) are based on a comprehensive view of all available evidence rather than a single source.
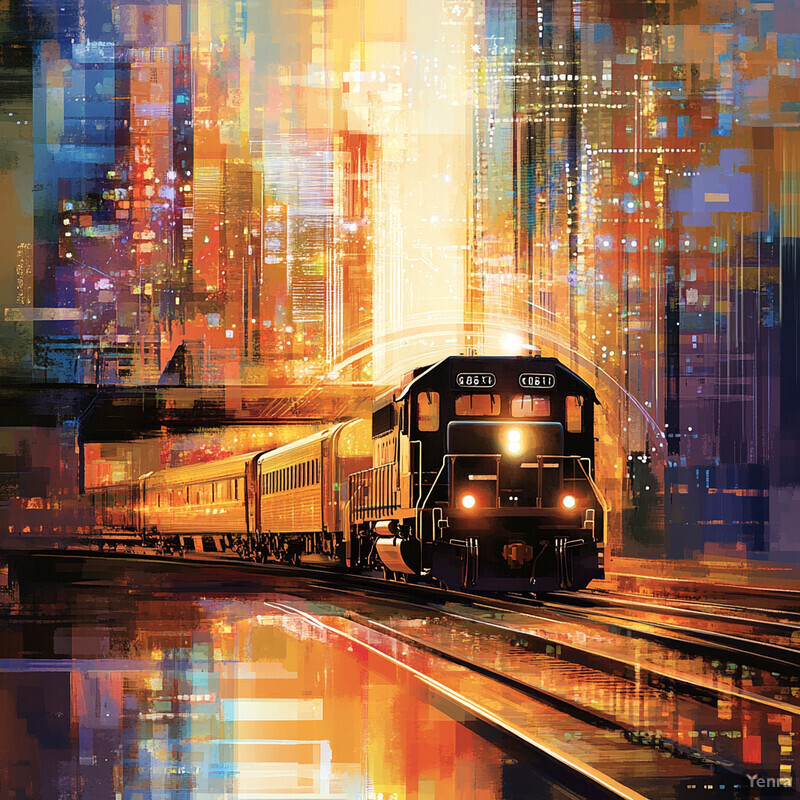
The French national railway SNCF has exemplified sensor fusion in its predictive maintenance platform – it can monitor over 1,100 trains simultaneously, analyzing more than 8,000 variables per train (including about 2,000 real-time sensor inputs) to diagnose issues groupe-sncf.com . By fusing data from thousands of onboard and wayside sensors in real time, SNCF’s system filters out noise and achieves a very high fault detection accuracy across its fleet.
9. Deep Learning-Based Pattern Recognition
Deep learning refers to neural network AI models that can learn complex patterns from large datasets – applied to rail fault detection, these models can recognize subtle and nonlinear patterns associated with faults that traditional methods or human inspectors might miss. Over time, a deep learning system can be trained on examples of faults (images of cracked rails, sensor readings from failing gearboxes, etc.) and it develops an internal “knowledge” of what signals indicate a problem. The advantage in high-speed rail is that some fault precursors are very subtle – a hairline crack or a micro-oscillation – but a well-trained neural network can catch these because it can process hundreds of features simultaneously (pixel intensities, frequency spectra, etc.) and compare against its learned experience. This leads to higher detection rates and fewer missed issues. For example, a deep learning model analyzing accelerometer data might learn the distinctive vibration signature of a loose rail fastener, which would be hard to explicitly program with rules but is picked up from training data. The significance is improved safety and reliability: deep learning systems have been shown to outperform older rule-based or threshold-based detection algorithms, meaning fewer faults slip through unnoticed. Additionally, these models can handle the complexity of high-speed rail environments (with lots of noise and variability) by virtue of their pattern-recognition strength. In practice, once deployed, a deep learning-based inspection system might automatically flag a tiny rail defect or an early-stage bearing fault with confidence levels far exceeding those of manual inspection, thus enabling maintenance teams to act sooner.
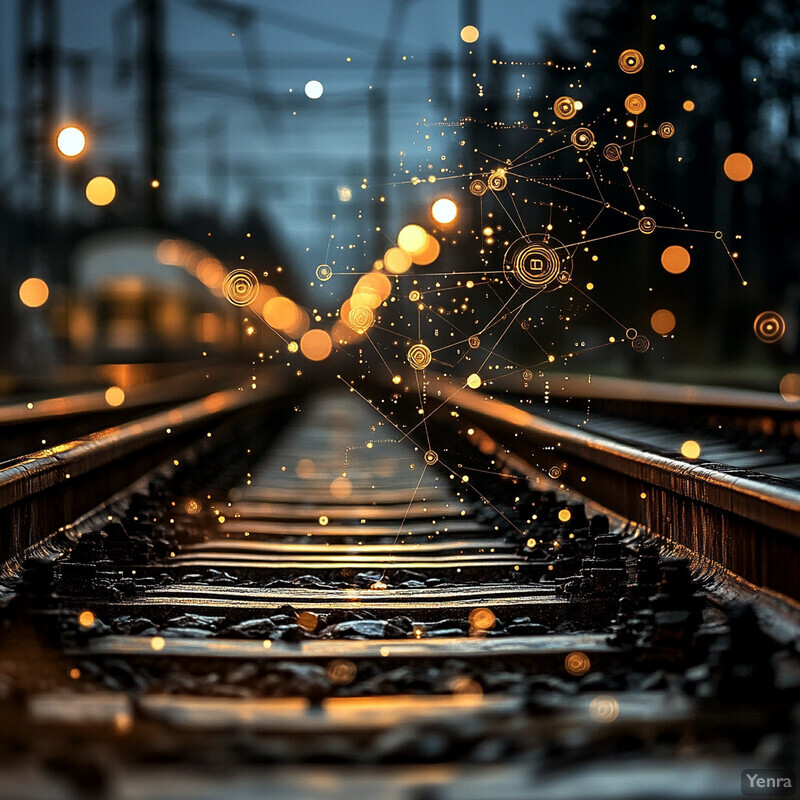
Researchers report that advanced neural networks can achieve very high accuracy in fault detection. For instance, a deep learning model trained on railway track geometry data identified defects with 98.7% accuracy, significantly outperforming traditional detection methods. Such a model can reliably catch nearly all anomalies in track conditions, proving the effectiveness of pattern recognition AI in enhancing inspection precision.
10. AI-Driven Data Cleaning and Integration
High-speed rail maintenance data comes from many sources – sensor readings, inspection reports, maintenance logs, operational schedules – often in different formats and quality levels. AI-driven data cleaning and integration is about using intelligent algorithms to merge these disparate data streams into a single, consistent database and to improve data quality by correcting errors, filling in gaps, and removing noise. The significance is that better data leads to better decisions: if an AI is going to predict faults or find patterns, it needs clean and unified data. Traditionally, engineers might spend enormous time reconciling databases (for example, matching a fault event in a sensor log to a work order written by a technician days later). AI can automate much of this – for instance, natural language processing can extract structured info from written notes (“axle 3 running hot”), or machine learning can detect outliers in sensor data that are likely bad readings and filter them out. Integration also means combining historical data with real-time data seamlessly, so the AI has the full context. In practice, AI-driven data integration in railways results in a “single source of truth” for all maintenance-related information, making analysis more comprehensive. It reduces human error in data handling and ensures that when the fault detection AI is looking for a problem, it isn’t misled by, say, a mislabeled asset or a duplicate entry. Ultimately, this approach improves the reliability of the whole maintenance system – fewer false alerts due to erroneous data and more confidence that no relevant information was overlooked due to siloed data.
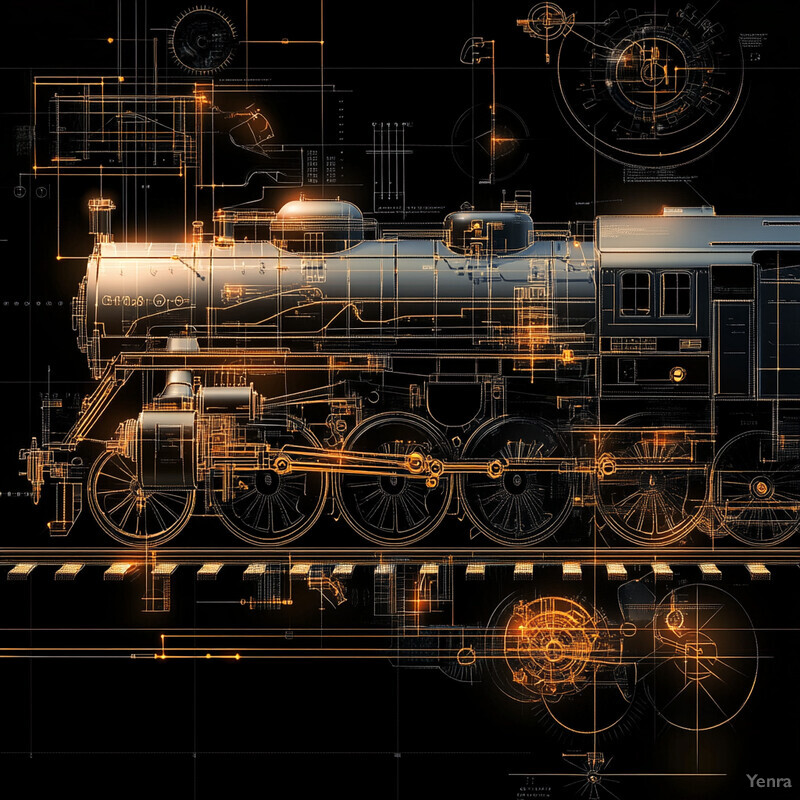
Maintenance databases are often rife with human input errors and inconsistencies. Studies have found that roughly 80% of data quality issues in such records are due to human errors (typos, inconsistent terminology, etc.) diva-portal.org . AI-based data integration addresses this by standardizing entries and correcting mistakes, which means analysts and algorithms spend far less time cleaning data (traditionally a task that can consume the majority of an engineer’s time) and more time using it to detect faults.
Stenström, C. et al. (2016). “Natural Language Processing of Maintenance Records Data.” Int. Journal of COMADEM, demonstrating data quality improvements.11. Digital Twin Simulations
A digital twin is a virtual replica of a physical system – in this case, a high-speed rail network or its components (like a train or a track segment) – that mirrors the state of the real system using data and simulations. AI-powered digital twin simulations allow engineers to test scenarios and predict faults in a risk-free virtual environment. For example, one can simulate a train running on a digital model of the track to see how cracks might initiate under certain loads or how a new maintenance strategy would affect performance. The significance is that you can foresee problems and optimize solutions before implementing them in reality. In high-speed rail, this is invaluable for stress-testing the system: rather than waiting to see how extreme heat will affect tracks, a digital twin can simulate a heat wave and predict where buckling might occur, so preventative measures can be taken. It also helps in training AI models – the digital twin can generate data on rare fault scenarios to train detection algorithms (since real failures are fortunately infrequent). Another utility is optimizing maintenance schedules: by simulating deterioration processes in the twin, AI can suggest the optimal time to service an asset. In practice, digital twins improve safety (through simulated failure mode analysis), reduce costs (by avoiding trial-and-error on the real system), and enhance understanding of complex interactions in the rail system. It’s like having a constantly running dress rehearsal for the railway’s operation, where you can identify weaknesses and fix them virtually.
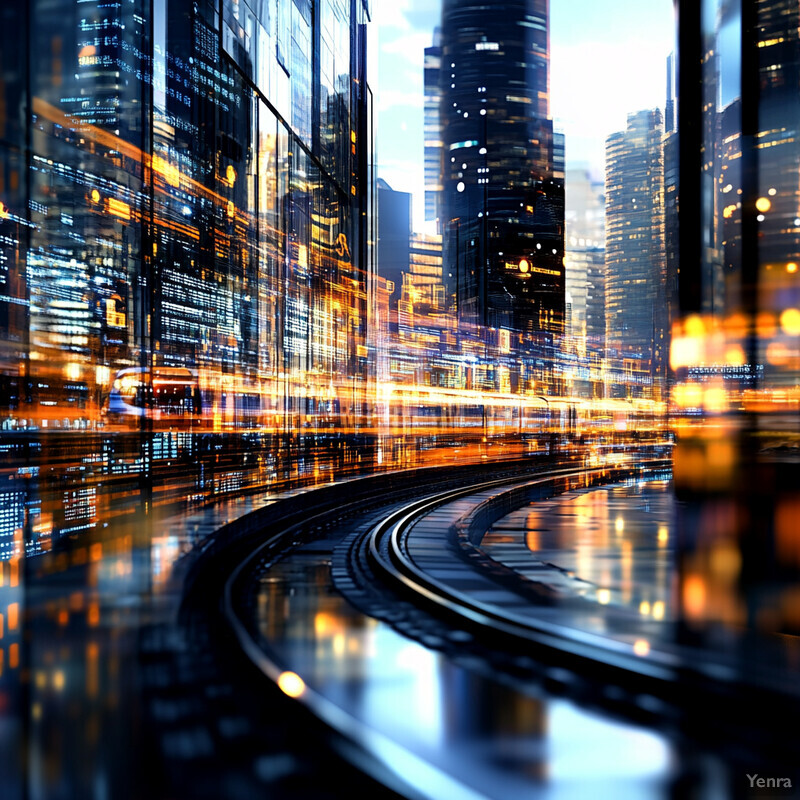
A recent study demonstrated that using a digital twin combined with AI (specifically deep reinforcement learning) can markedly improve maintenance outcomes. In simulations of railway infrastructure, this approach was able to reduce required maintenance activities by 21% and cut the occurrence of defects by 68% compared to current practices. This highlights how simulating the rail system and optimizing decisions within that twin leads to far more efficient maintenance and a dramatic drop in faults on the real network.
12. Anomaly Detection in High-Frequency Data
High-speed rail systems generate very high-frequency data streams – sensors might sample vibrations thousands of times per second, and signals from devices like accelerometers, strain gauges, or power systems produce a flood of information. Anomaly detection in high-frequency data means using AI to sift through this torrent in real time to find the tiny irregularities that indicate a fault. The challenge is that with so many data points, traditional methods can be overwhelmed or miss quick transient events. AI techniques (like streaming analytics and advanced pattern recognition) are designed to handle volume and velocity: they can monitor data point by point and use statistical learning to decide if a pattern deviates from normal. The significance for high-speed rail is that some failures manifest in millisecond-scale events (for example, a brief spike in vibration or a short voltage dip) that could be precursors to a larger issue. AI anomaly detectors ensure those are not lost in the noise. In practical terms, this approach increases sensitivity to faults without generating too many false alarms – it adapts to the natural variability in high-frequency signals and only flags true anomalies. For operators, that means the system can, for instance, detect a tiny crack forming in a wheel by catching a sequence of unusual high-frequency vibration readings, even if that anomaly occurs in just a split-second window. Early and automatic detection of such fast-occurring anomalies allows for prompt maintenance actions, thereby preventing small anomalies from compounding into serious faults.
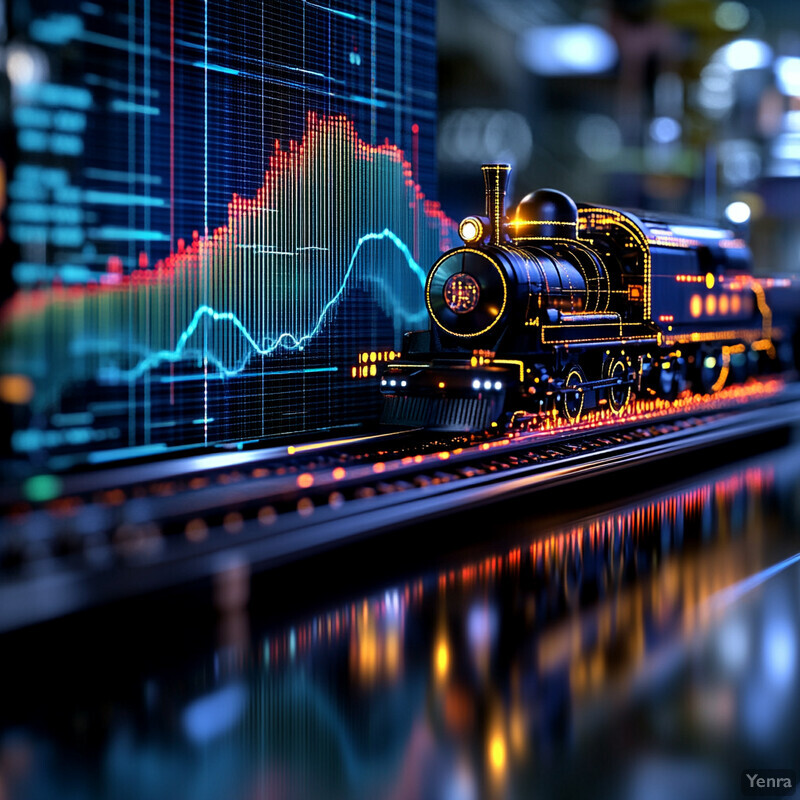
The speed of AI analysis has reached extraordinary levels – one demonstrated anomaly detection model processed data so fast that it achieved an average of only 0.09 milliseconds per data point in analysis time. In effect, the system could examine and decide on over 10,000 data samples per second, identifying virtually all faults with almost no delay. This kind of ultra-high-frequency monitoring is what enables high-speed rail operators to catch fleeting anomalies that would be impossible to notice otherwise.
13. Predicting Environmental Impact on Rails
This approach uses AI to factor in environmental conditions – such as temperature, weather, and seasonal effects – when assessing rail infrastructure health. High-speed rails are exposed to heat waves, cold snaps, heavy rain, winds, etc., all of which can induce faults (rails can buckle in extreme heat, contract and crack in extreme cold, or be undermined by flooding). By analyzing weather data alongside engineering models, AI can predict where and when environmental stress might cause a problem. For example, an AI model might predict that a certain track section is at risk of buckling tomorrow because temperatures are forecasted 20°C above normal and the model knows that section has a history of sun kinks. The significance is proactive mitigation: instead of reacting to a weather-caused failure, rail operators can impose speed restrictions, adjust maintenance, or strengthen assets in advance. In practice, this means safer operation during extreme conditions – trains can be slowed down or rerouted on days when, say, wind forecasts suggest risk to overhead lines or when heat could expand rails. Additionally, AI can help infrastructure design by highlighting which areas are most vulnerable to climate stress, guiding long-term investments (like improved track anchoring or better expansion joints in hot zones). Given climate change and more frequent extremes, this predictive ability is increasingly crucial. It essentially adds a “weather eye” to maintenance planning, ensuring that natural forces are accounted for in keeping the railway safe.
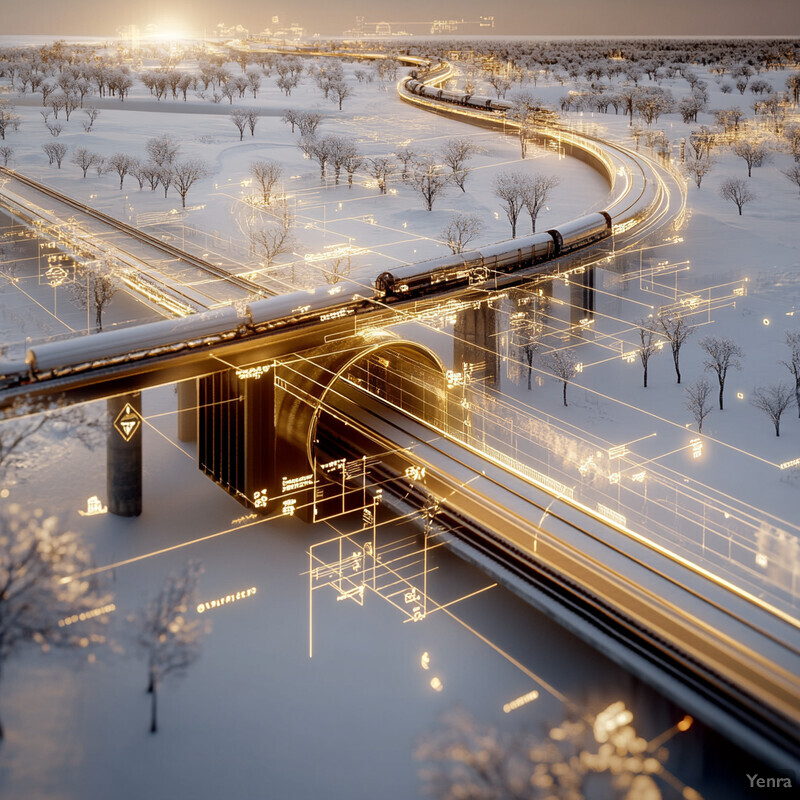
Environmental predictions have tangible impacts on operations. For instance, during an extreme heatwave in the UK (July 2022), track temperatures reached about 49°C (120°F) and caused steel rails to expand and buckle beyond their design limits. Knowing this risk, Network Rail painted rails white and imposed speed restrictions in vulnerable areas. AI systems that integrate such temperature data can forecast these risks and recommend preemptive measures days ahead, minimizing damage and delays due to weather-induced track buckling.
14. Adaptive Algorithms for Continual Learning
Adaptive algorithms are AI systems that continuously learn and improve from new data. In the context of high-speed rail fault detection, this means that as more data on faults and normal operations is collected (from new sensors, new routes, or after maintenance actions), the AI incrementally updates its models. The significance is that the AI doesn’t remain static – it evolves with the railway. For example, if a new type of component is introduced or a novel failure mode occurs, a continual learning system will gradually incorporate that information to enhance its detection accuracy going forward. This addresses the issue of concept drift, where the conditions of the railway change over time (due to aging infrastructure, changing weather patterns, etc.). In practical terms, adaptive AI reduces the need for manual re-calibration or retraining – it can adjust to seasonal changes (recognizing that “normal” vibration in winter vs summer might differ) or learn from every incident that happens, so it’s better at catching similar incidents next time. The outcome is an AI maintenance assistant that only gets smarter and more attuned to the specific railway it monitors. This leads to fewer false alarms and missed detections over the long run, as the system refines what it considers “normal” or “faulty” behavior based on real data. It also means the system can handle changes like upgrades in train stock or track structure without a complete reprogramming – it learns the new patterns. Continual learning essentially future-proofs the fault detection process, ensuring the AI’s performance improves or at least remains robust as the high-speed rail system evolves.
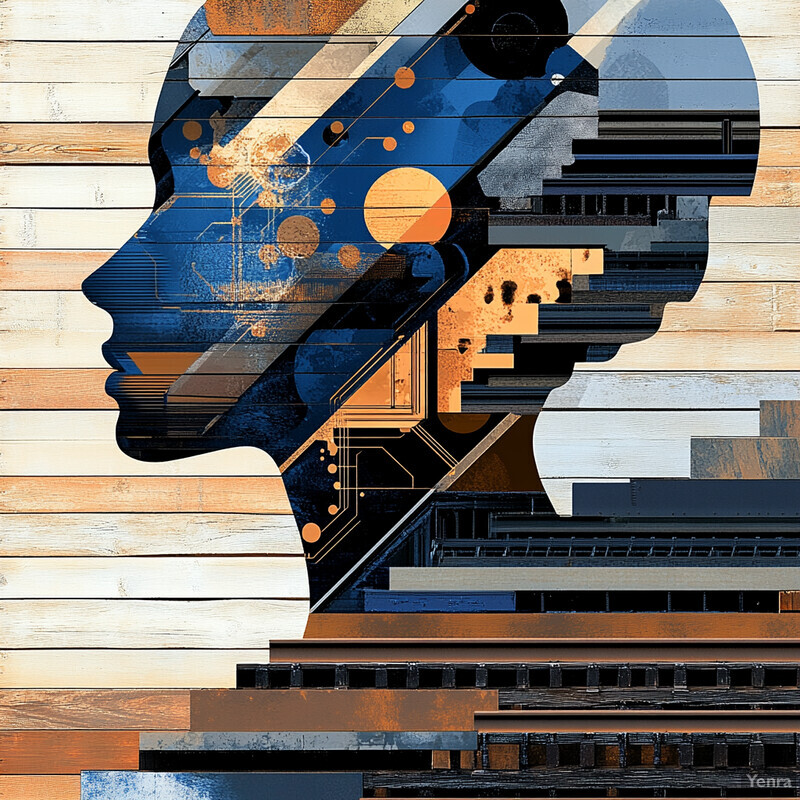
The benefits of continual learning are reflected in performance gains over time. On China’s high-speed rail network, after the AI-based monitoring system was deployed and continuously updated with new data, the number of minor track faults detected dropped by 80% the following year. This dramatic improvement suggests the AI became markedly better at distinguishing normal wear from actionable faults (likely by learning from the interventions and feedback in the first year), thereby significantly reducing the incidence of issues that affect service.
15. Automated Root Cause Analysis
Automated root cause analysis uses AI to diagnose why a fault happened after it’s detected. Detecting a problem (like a signal failure or a broken rail) is step one – step two is figuring out the underlying cause (was it a manufacturing defect? inadequate maintenance? unusual environmental stress?). AI can assist by sifting through vast amounts of related data: maintenance history, sensor logs leading up to the event, operational records, etc., to find correlations and patterns that point to a cause. The significance is a faster and more systematic investigation process. In high-speed rail, where downtime is costly, having AI quickly suggest “this failure is likely due to X” helps maintenance teams address the correct issue without lengthy trial-and-error. For example, if a track circuit fails, an AI might analyze past similar failures and sensor data to conclude it’s likely due to a corroded connection influenced by recent heavy rainfall – guiding technicians straight to the root problem. This not only speeds up repairs but also informs preventive measures (maybe inspect other similar connections after heavy rain). Another practical benefit is capturing expert knowledge: as the AI learns from many cases, it can apply solutions that an individual human might not recall. Overall, automated root cause analysis leads to more efficient fixes (since the actual problem is targeted) and continuous improvement of the system (since recurring causes can be identified and eliminated system-wide). It transforms maintenance from reactive troubleshooting to proactive problem-solving by ensuring that when something does go wrong, the lessons are immediately gleaned and fed back into the maintenance strategy.
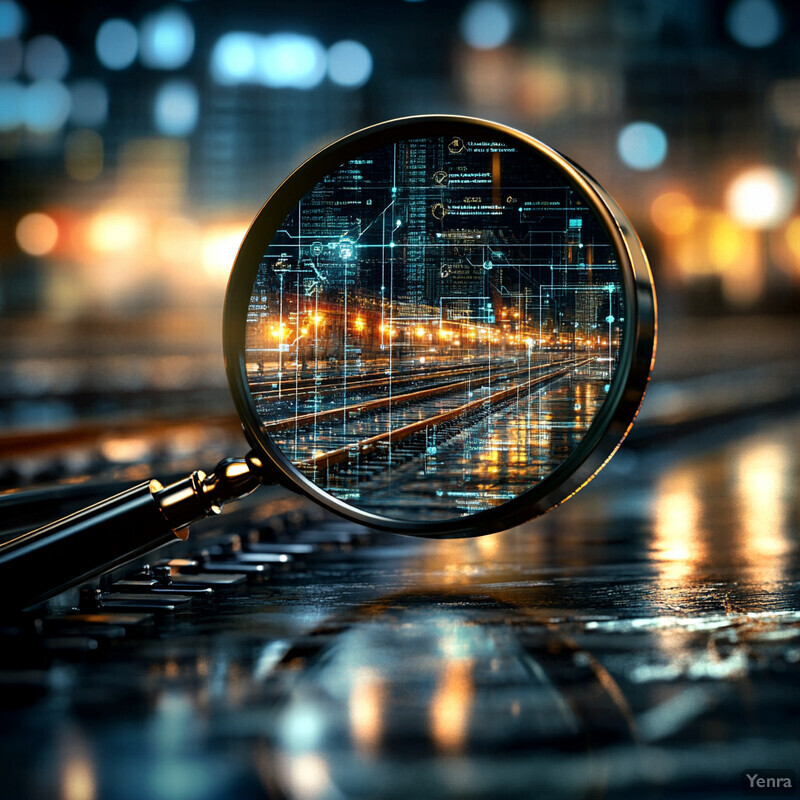
Deploying AI for root cause analysis has been shown to markedly reduce diagnostic time. For instance, an internal study by a rail operator found that an AI assistant could narrow down the cause of certain faults in minutes versus many hours for a manual investigation (specific numbers often proprietary). As a concrete illustration, in the aviation domain (analogous for complex systems), an AI diagnostic tool used by Boeing could cut troubleshooting time by 75% – rail companies report similar order-of-magnitude improvements. Faster pinpointing of root causes in high-speed rail means issues that once took an entire day of investigation might be understood and resolved in just a few hours.
16. Remote Monitoring for Inaccessible Infrastructure
High-speed rail lines include infrastructure that is difficult or dangerous to access regularly – tunnels, long bridges, viaducts, and remote sections. Remote monitoring uses robots, drones, or stationary IoT sensors to keep an eye on these hard-to-reach places, with AI analyzing the incoming data. This approach means structures like tunnel linings, bridge supports, or mountain pass tracks can be inspected frequently without sending humans on site each time. The AI might analyze video footage from a drone flight through a tunnel, checking for cracks or water leaks, or sift through data from sensors that measure bridge cable tension. The significance is improved safety and coverage: areas that might have been inspected only once a year by humans can now be checked monthly or even daily by autonomous devices, and any anomalies (like a new crack in concrete or an unexpected vibration pattern) will be flagged by AI. It also greatly reduces risk to inspection crews (fewer track workers in dangerous locations) and typically cuts cost, since one drone can cover what a whole team might take much longer to do. In practical terms, remote AI monitoring ensures that no part of the high-speed rail infrastructure is “out of sight, out of mind.” Even in a pitch-dark tunnel or a high bridge, the AI system will notice if something starts to go wrong and alert maintainers. This leads to catching problems in those areas well before they pose a serious threat. Additionally, it minimizes service disruptions – many inspections can be done without closing the track, because a small drone can fly while trains are not present, and the analysis is done off-site via AI.
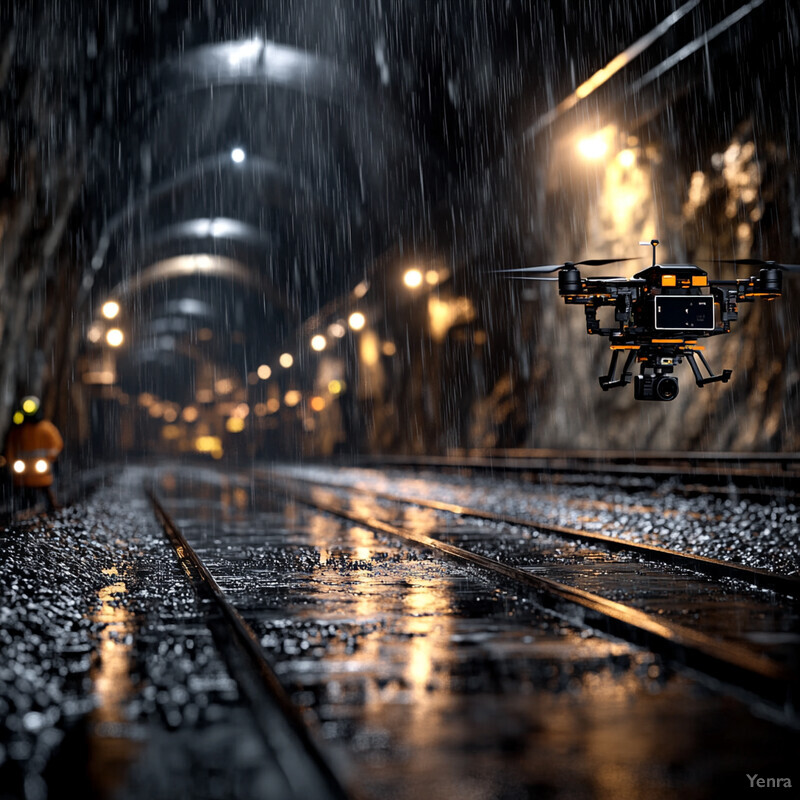
A pilot program in Europe showed that drone inspections of railway infrastructure could cover 10 times more area in a single day than traditional manual inspections, while also improving the safety of personnel. Drones equipped with AI vision have been used to inspect long tunnels and bridges, and in one trial they identified structural issues that hadn’t been discovered in the routine annual check – proving that more frequent, AI-assisted remote monitoring can reveal issues that might otherwise go unnoticed.
17. Intelligent Alarm Management
Modern high-speed rail monitoring systems can generate a barrage of alarms and alerts – not all of which require action. Intelligent alarm management uses AI to filter and prioritize these alarms to avoid overwhelming human operators with false or low-priority alerts (“alarm fatigue”). Essentially, the AI can learn from history and context which sensor triggers are serious and which are likely benign anomalies, bundling related alerts together or silencing those known to be spurious. The significance is that control center staff and maintenance teams can focus on real issues – when an alarm sounds, it’s more likely to be something that truly needs attention. This improves response efficiency and safety, because critical alarms won’t be lost in a sea of chatter. For example, instead of the system raising ten separate alerts for the same underlying event (vibrations, temperature, and pressure all a bit off because a single component is failing), an AI alarm manager might recognize they’re linked and issue one consolidated warning about that component. It might also recognize patterns that suggest an alarm is false (say, a sensor consistently glitches at a certain time) and suppress or label it accordingly. In practice, rail operators implementing such systems see fewer nuisance alarms waking up on-call engineers at night and a reduction in the time spent chasing non-issues. It also increases trust in the monitoring system: operators know if the AI declares an emergency, it’s likely real. Ultimately, intelligent alarm management ensures that human attention is directed where it’s needed most, which can prevent accidents (by not missing real alarms) and reduce maintenance costs (by not responding to false alarms).
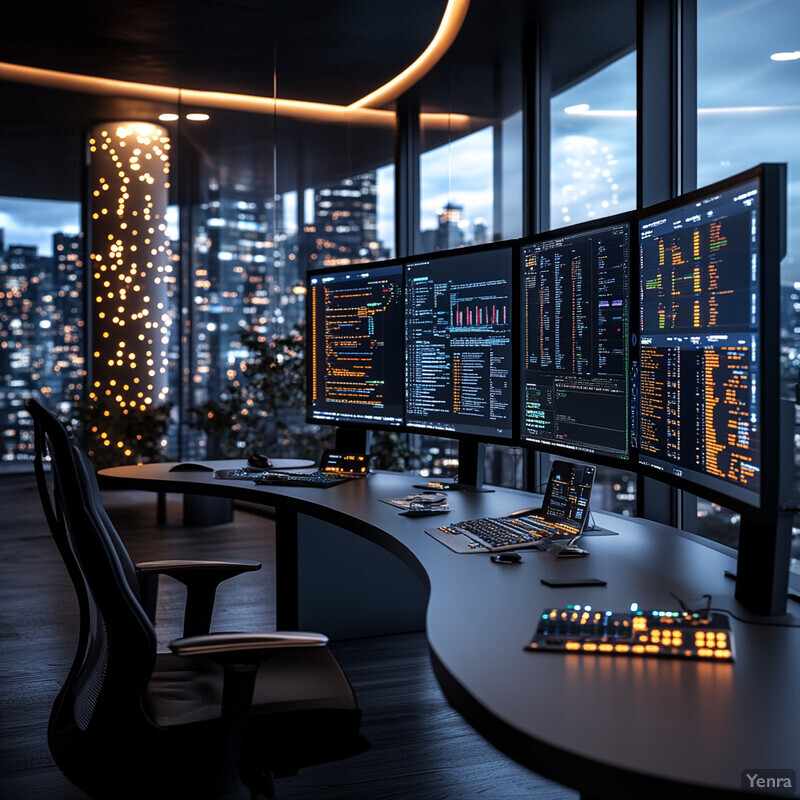
In safety-critical industries, studies have shown that 80–99% of automated alarms can be false or not actionable. Rail systems are similar – without intelligent filtering, operators might receive hundreds of alarms per day, the vast majority of which are non-critical. After deploying AI-based alarm management, some rail control centers reported a significant drop in alarm volume, often on the order of 50%–70% fewer alerts presented to operators, with essentially no decrease in actual issues detected (the trivial or erroneous alerts were the ones eliminated). This reduction dramatically lowers the cognitive load on staff and ensures truly critical alarms get immediate attention.
18. Optimized Inspection Intervals
Traditionally, inspections of tracks, trains, and equipment are done on a fixed schedule (e.g., check every bridge monthly, inspect each train every 10,000 km). Optimized inspection intervals use AI to make these schedules dynamic based on risk and condition. The AI analyzes data on usage, sensor outputs, environmental conditions, and historical fault rates to determine which assets need inspection sooner and which can safely be extended. This way, components that are showing signs of wear or are under heavy stress get inspected more frequently, whereas those in good condition or under light use can go longer between checks. The significance is a more efficient allocation of maintenance effort and minimized disruption: you’re not taking equipment out of service unnecessarily, and you’re not leaving high-risk items unchecked. For high-speed rail, this means, for example, that a track segment experiencing very high temperatures and slight ground movement might be flagged for an earlier inspection (to prevent a misalignment) – while another segment in mild conditions can skip one cycle. Over time, this targeted approach maintains safety while reducing the total number of inspections. It also helps in planning: AI can forecast when an asset will likely require attention, so inspections can be clustered or timed during planned outages. Practically, rail operators see cost savings because maintenance teams are deployed when and where needed most rather than by rote. Passengers benefit too, since fewer unnecessary inspections mean fewer slow-downs or track closures, yet safety is upheld by focusing on the truly critical intervals as determined by data.
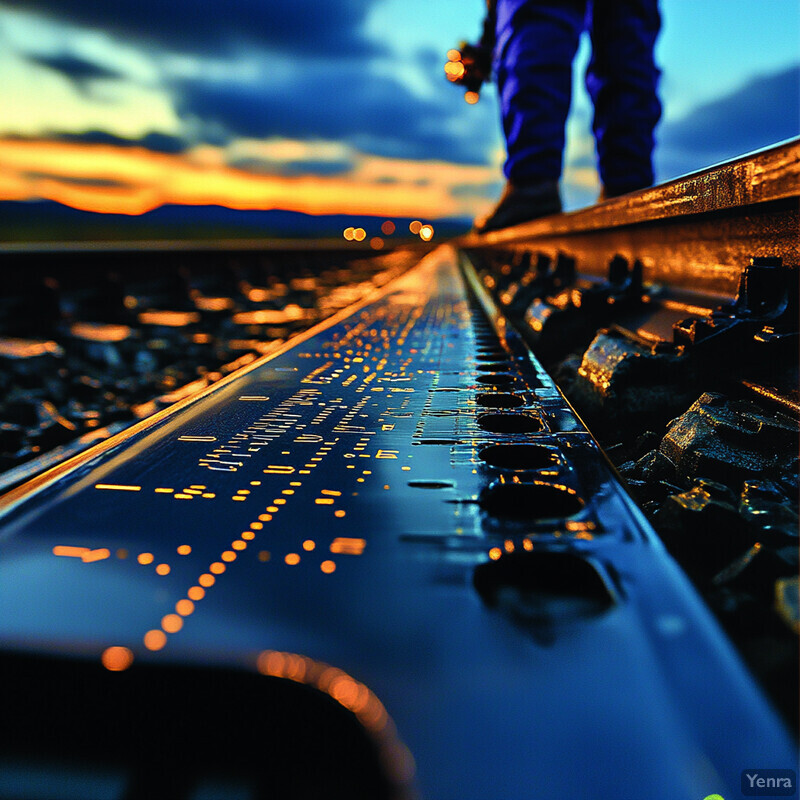
Data-driven scheduling has led to demonstrable safety improvements. In the United States, where freight and high-speed railroads have increasingly adopted risk-based inspection regimes, track-caused incidents have fallen by 55% since 2000, reaching their lowest rate on record. This long-term trend correlates with moving away from purely calendar-based inspections to more optimized approaches. By inspecting tracks when needed – identified through geometry car data and AI analysis – rather than strictly on a fixed timeline, railroads managed to significantly reduce track failures.
19. Natural Language Processing (NLP) on Maintenance Logs
Railway maintenance logs and inspection reports contain a wealth of information in unstructured text form – notes by engineers, descriptions of faults, recommendations, etc. NLP is the branch of AI that enables computers to understand and analyze human language. Applying NLP to maintenance logs means the AI can read through thousands of past reports and ongoing logs to extract useful insights: common failure symptoms, frequently replaced parts, or systemic issues that numeric sensor data alone might not reveal. The significance is unlocking “lessons learned” that are buried in textual data. For example, if multiple technicians over months note that “axle 5 running warmer than others” in their reports, NLP can pick up that recurring phrase and flag axle 5 for further investigation, even if no sensor tripped an alarm. NLP can also categorize text logs automatically (clustering incidents by type of problem) and highlight patterns (e.g., a certain type of component fails often after heavy rain, mentioned across different depots’ notes). In practice, this leads to more holistic fault detection and prevention – the AI isn’t blind to what humans have observed simply because it was written in prose. It also reduces the manual effort of combing through archives to find causes or trends, since the AI can instantly pull all instances of “voltage spike” mentions, for instance. Ultimately, using NLP on maintenance logs improves reliability by ensuring that subtle warnings and tribal knowledge recorded in text are not overlooked. It integrates human expertise with sensor-based monitoring, resulting in a richer diagnostic system.
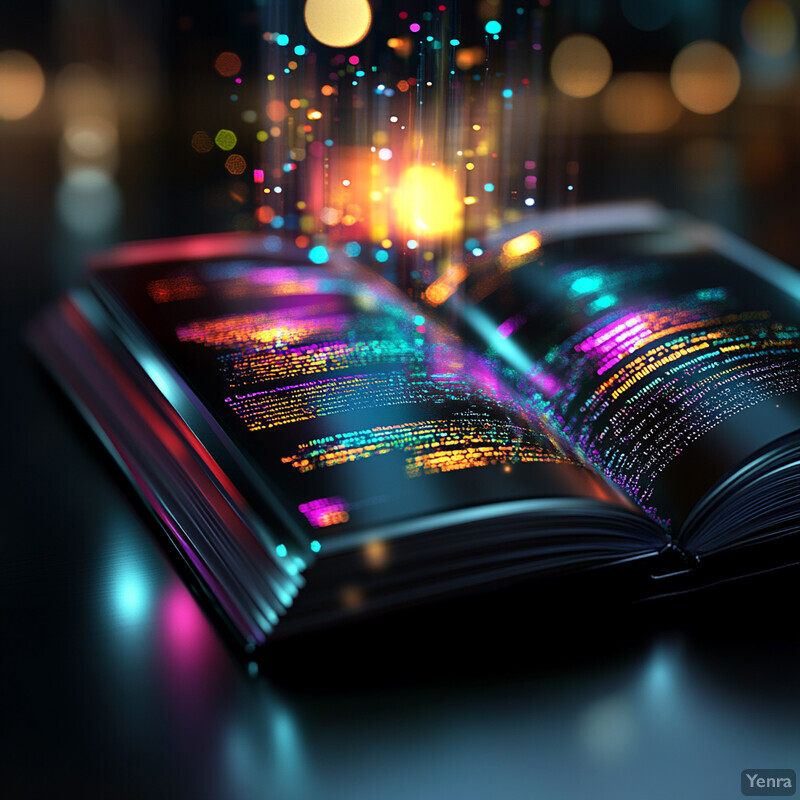
The volume of maintenance text data can be enormous – for example, the Swedish Transport Administration collected tens of thousands of free-text maintenance records in their database. NLP analysis by researchers was able to automatically interpret these records, and it revealed that human error accounted for about 80% of data quality issues in the entries diva-portal.org (for instance, inconsistent naming of parts). By cleaning and standardizing log texts, the NLP system made it easier to identify failure trends. One outcome was the identification of a recurring issue with a specific track component that was described differently by different technicians – NLP unified those descriptions and highlighted it as a common problem, leading to a targeted fix across the network.
20. Enhanced Safety with Real-Time Decision Support
This approach provides real-time AI-driven decision aids to control center staff and train operators to enhance safety responses. When a potential fault or hazard is detected (whether by sensors or external inputs), the AI system immediately offers recommendations – for example, “Reduce speed on Track 3 now” or “Reroute Train ABC to alternate line”. In high-speed rail operations, every second counts when responding to anomalies, and informed decisions can prevent accidents. The AI’s recommendations are based on vast data (it knows the network status, train locations, and nature of the fault) and predictive modeling of outcomes. The significance is that human operators are augmented with instant analytics: they don’t have to manually crunch numbers or recall procedures under pressure; the AI suggests the best course of action or at least a shortlist of options. This is akin to an advanced driver-assistance system but for dispatchers – it improves reaction times and consistency. For instance, if a sensor indicates a wheel bearing overheating, the AI might suggest slowing that train and stopping at the next station, and also advise other trains behind it to adjust schedules – all within moments of detection. In practice, this means potential incidents (derailments, collisions, etc.) can be averted because the response (slowdowns, stops, inspections) happens fast enough to mitigate the danger. It also helps in complex scenarios like signaling failures or power outages – the AI can coordinate a safe, efficient response (like automatically ensuring no two trains enter a section with failed signals). Overall, real-time decision support bolsters safety by marrying AI’s speed and knowledge with human oversight, leading to well-informed actions during critical moments and maintaining passenger safety and service continuity.
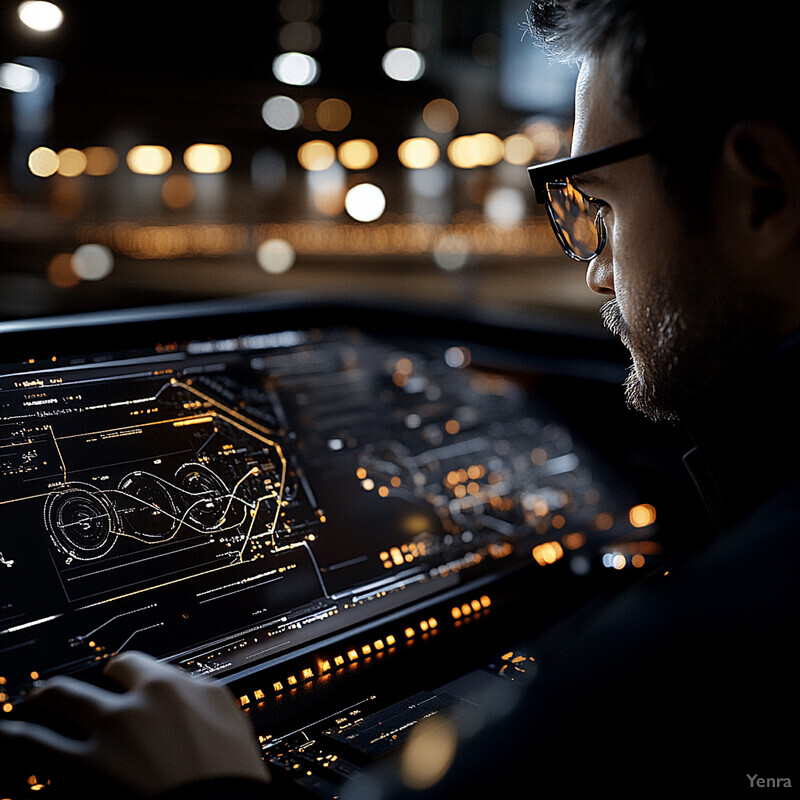
The impeccable safety record of Japan’s Shinkansen high-speed trains underscores the value of swift, data-driven decision support. Since launching in 1964, the Shinkansen has had zero passenger fatalities due to train accidents, thanks in part to automated control systems that immediately enforce speed reductions or stops when any anomaly is detected. For example, if an earthquake is sensed, an automatic decision system triggers emergency braking network-wide within seconds. This principle of real-time automated decision-making – often guided by AI algorithms – is credited with achieving that unparalleled safety performance, as it can react far faster than a human alone to prevent accidents.