1. Real-Time Sensor Data Analysis
AI-driven systems can process immense volumes of sensor data (chemical, radiological) almost instantaneously, enabling immediate detection of hazardous substances. By aggregating inputs from multiple sensors and applying advanced algorithms, AI distinguishes meaningful spikes or patterns from background noise. This dramatically improves response time and accuracy – for example, differentiating a dangerous gas release from benign fluctuations in radiation or air quality. Such real-time analysis allows safety personnel to be alerted within seconds of anomaly detection, potentially preventing incidents. Overall, AI’s speed and pattern-recognition capabilities ensure rapid, data-informed decision-making that can save lives and reduce environmental damage.
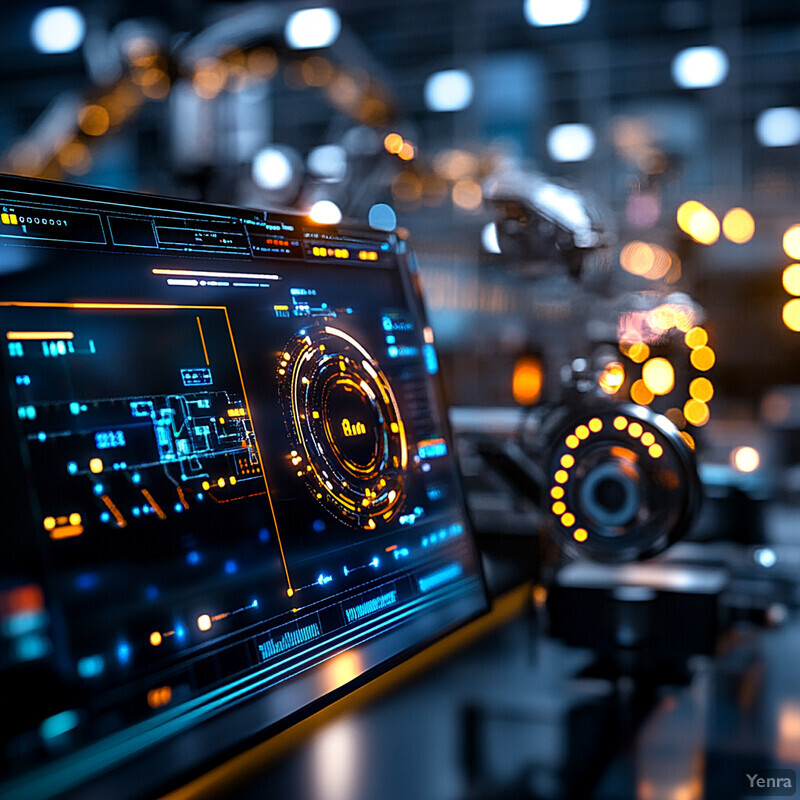
A recent study by the University of Virginia demonstrated the power of AI in real-time monitoring. Researchers developed an “artificial nose” system that uses a network of nano-sensors and neural networks to pinpoint toxic gas leaks in real time. In tests, the system accurately detected minute concentrations of nitrogen dioxide and even identified the leak source faster than traditional methods (Baek et al., 2024). Published in Science Advances in 2024, the AI model integrated sensor data and Bayesian optimization to optimize sensor placement, ensuring full coverage of an area. This real-world example highlights how AI can continuously sniff out hazardous gases with greater speed and precision than human monitoring, underscoring the life-saving potential of real-time AI analysis in industrial safety.
2. Advanced Pattern Recognition in Sensor Signals
Machine learning models can identify subtle, complex patterns in sensor outputs that static thresholds often miss. Traditional detectors might only alarm when a value crosses a set limit, but AI pattern-recognition analyzes the shape and combination of signals over time. This improves sensitivity – for instance, recognizing the faint, fluctuating signature that precedes a gas leak rather than waiting for a large spike. By learning normal vs. anomalous patterns, AI reduces false negatives and provides earlier warnings. These nuanced insights help organizations understand precursors to hazards and adjust protocols proactively. In essence, AI’s pattern recognition acts like a “sixth sense,” catching micro-signals and correlations invisible to human operators or simplistic alarms.
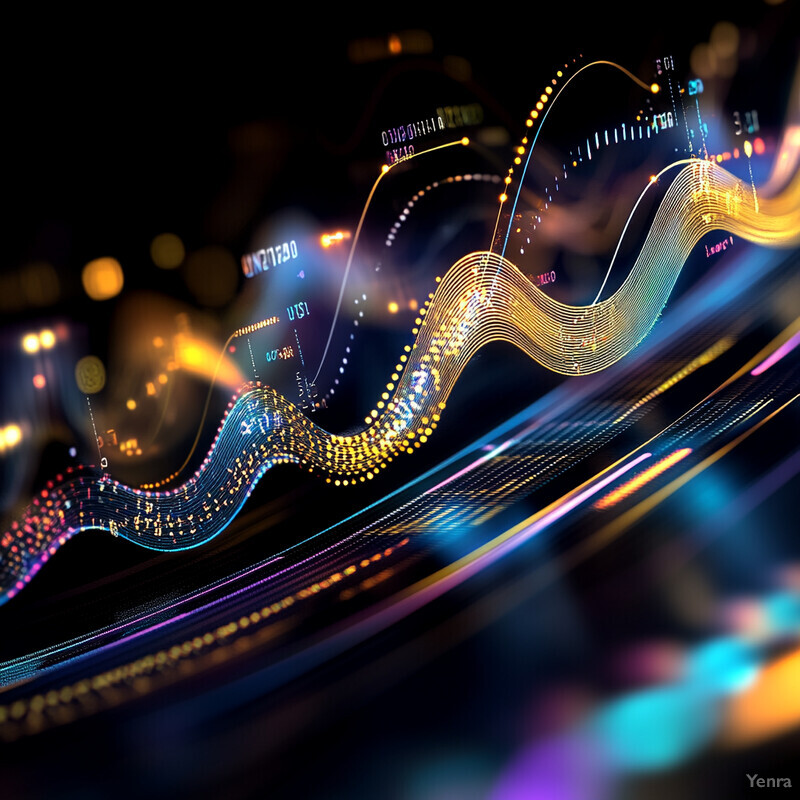
A compelling example is QGasBusters, a 2025 innovation that combines quantum sensors with AI to detect pipeline leaks. The system analyzes subtle anomalies in pipeline data with unprecedented sensitivity – identifying minute pressure drops or vibration changes that traditional systems would treat as noise. Developers reported that QGasBusters can provide critical early warnings of leaks, potentially saving thousands of lives by prompting fixes before a disaster occurs (Ibrahim, 2025). In essence, the AI spotted a leak before any human could see or hear it, by learning the complex pattern of sensor fluctuations that signal a micro-crack forming. This case illustrates how advanced pattern recognition enables “predictive detection,” catching hazards at the incubation stage and averting industrial disasters through timely intervention.
3. Adaptive Thresholding
Rather than relying on fixed alarm thresholds, AI systems dynamically adjust trigger levels based on context and learned behavior. This adaptive thresholding means the system “learns” normal baseline variations (due to temperature, humidity, etc.) and raises alarms only for truly abnormal deviations. The result is fewer false alarms and fewer missed real events. For example, if overnight sensor readings drift slightly, an AI can recalibrate the threshold in real time to avoid a needless alarm. Conversely, if subtle changes imply a worsening trend, the AI can lower the alert threshold to flag a problem sooner. By continuously updating what is “normal,” adaptive AI thresholds maintain a constant false alarm rate – keeping the false alarm rate low while still catching genuine hazards (Liu et al., 2023). This improves operator trust and ensures that when an alarm sounds, it truly demands attention.
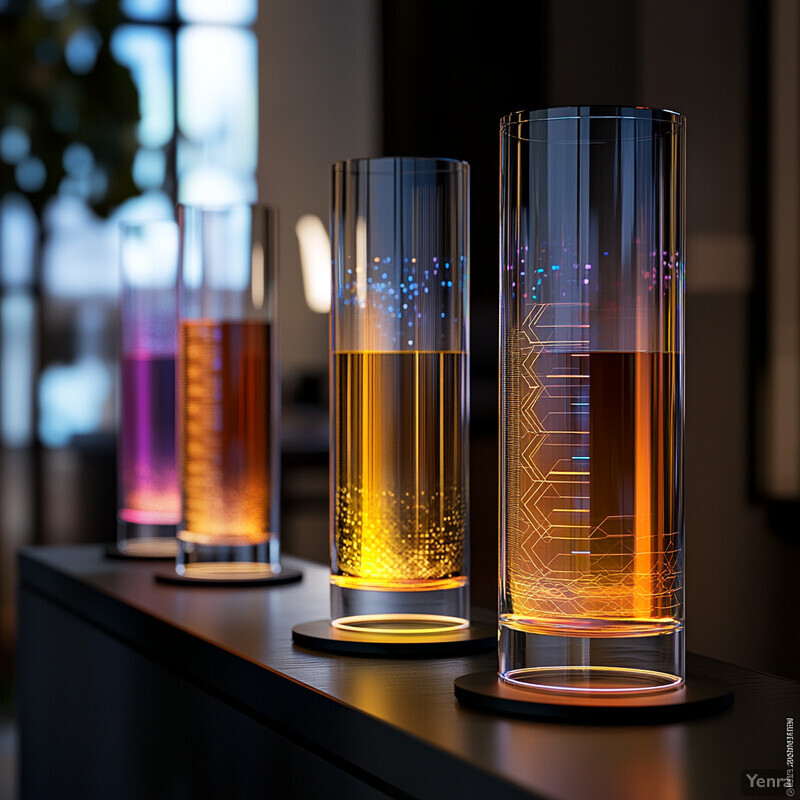
Adaptive thresholding has been successfully applied in pipeline leak detection. A 2023 study introduced an improved CFAR (Constant False Alarm Rate) algorithm, borrowed from radar technology, to detect pipeline leaks from acoustic sensor data (Liu et al., 2023). The AI-driven method adjusts detection thresholds on the fly based on ambient noise levels. In tests simulating gas pipeline leaks of various sizes, the dynamic threshold approach achieved over 94% detection accuracy while keeping false alarms below 2%. This is a dramatic improvement over static thresholds, which often either missed small leaks or triggered dozens of false alarms. The adaptive system could, for instance, distinguish harmless pressure fluctuations from the acoustic signature of a 5 mm leak hole. These results demonstrate how continuous learning and threshold adjustment by AI yield more reliable hazardous leak detection in practice.
4. Predictive Analytics for Leak Detection
AI enables a shift from reactive to proactive leak management. By analyzing historical incident data, maintenance records, and real-time sensor trends, machine learning models can predict where and when leaks are likely to occur (Magnificent Plumbing, 2023). In practical terms, this means AI might flag that a particular pipeline segment, given its pressure fluctuation trends and past minor leaks, has an X% probability of failure in the next month. Armed with such foresight, companies can repair or reinforce equipment before a leak happens. Predictive analytics thus minimizes unplanned downtime and environmental releases. In fact, industry case studies show that AI-based predictive maintenance can reduce unplanned equipment downtime by 20–50%, translating to fewer opportunities for leaks to develop (Datategy, 2023). Overall, AI’s ability to forecast failures transforms leak detection into leak prevention, making operations safer and more reliable.
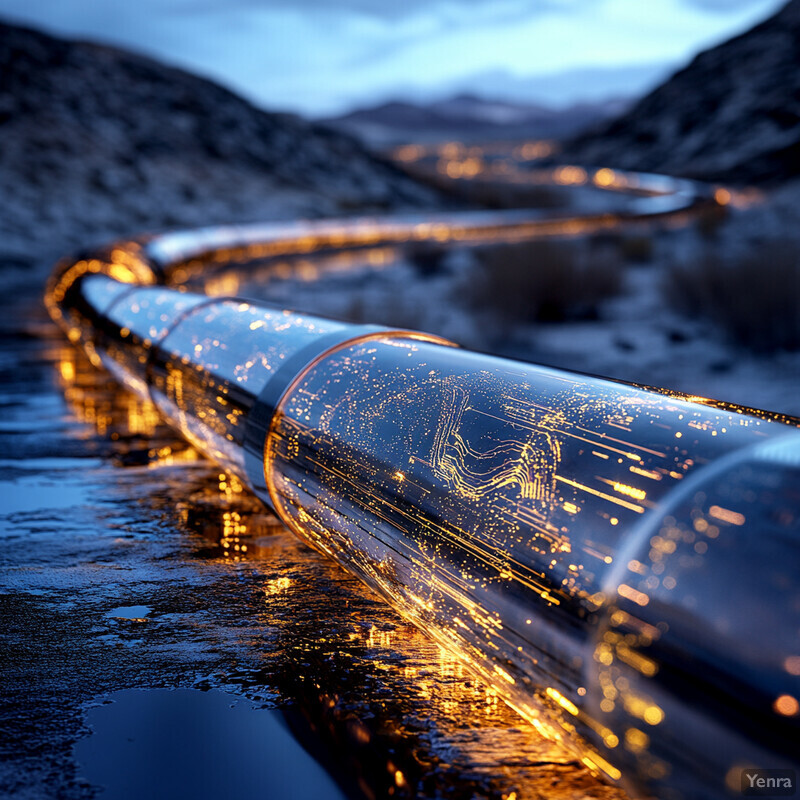
In 2025, oil and gas operators began using AI to catch leaks before they happen. For example, one refinery’s AI system learned to recognize the early warning signs of a potential tank rupture – a subtle pattern of rising temperature and declining pressure retention over weeks. According to a sector report, such AI systems can identify early warning signs like gradually dropping pipeline pressure or minor temperature fluctuations that signal a developing leak. Maintenance teams are then alerted proactively, allowing them to repair a weak gasket or corroded valve before any hazardous release occurs. In one pilot, an AI model predicted a critical gasket failure in a chemical plant days in advance; the gasket was replaced in time, preventing a major acid spill. These examples underscore how predictive analytics powered by AI is revolutionizing leak detection: instead of waiting for alarms, companies fix problems in advance, vastly reducing the occurrence of actual hazardous material leaks.
5. Automated Chemical Identification
AI is greatly accelerating the identification of unknown substances by analyzing their unique “signatures.” Deep learning models trained on vast libraries of spectral data (e.g. infrared spectra, mass spectrometry readings) can recognize chemicals in seconds that would take a human expert much longer to identify. This means first responders or lab analysts can feed an unknown sample’s data into an AI and get a probable ID (with confidence level) almost immediately. The significance is huge in emergencies: knowing whether a leak is, say, ammonia versus chlorine gas changes the response strategy. AI-based identification is also more consistent – it can catch subtle differences in spectra or molecular fingerprints that humans might overlook, reducing misidentification. Ultimately, automating chemical identification with AI leads to faster, more informed decision-making in hazmat incidents, improving safety for responders and the public.
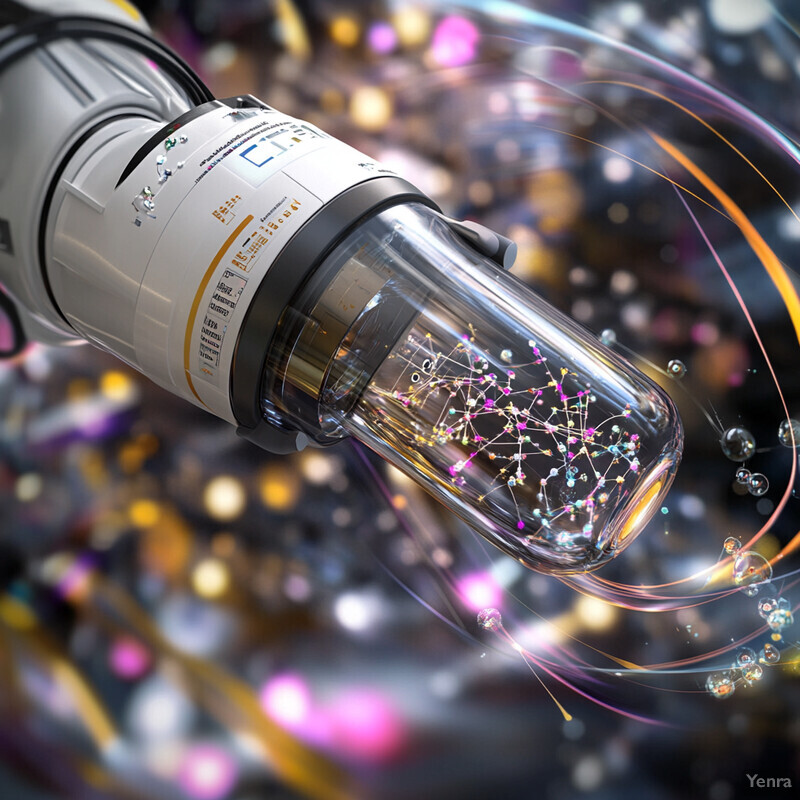
A recent advancement in this domain is an AI system for field detection of chemical warfare agents using computer vision. Sojeong Bae et al. (2025) developed a lightweight deep learning model (based on YOLOv8) to interpret colorimetric sensor readouts and instantly classify toxic agents. In trials, their on-device AI accurately detected substances like sulfur mustard and nerve agents with over 90% precision, all in real time (Bae et al., 2025). The system uses a camera to read a reactive test strip’s color pattern and the AI identifies the chemical by matching the pattern to its training data. Importantly, it runs on a portable device and proved robust under different lighting and backgrounds. This AI tool effectively gives first responders in the field a rapid “lab in your hand” – for example, a hazmat team could scan a unknown liquid spill with a handheld sensor and the AI would name the substance (and even concentration) on the spot. Such examples show how AI-driven chemical identification brings laboratory-level analysis to the field, vastly speeding up the hazard characterization in emergencies.
6. Image and Video Analytics for Visual Inspection
AI-powered computer vision is augmenting visual inspections by automatically analyzing images and video for signs of hazardous materials. This includes recognizing spills, leaks, corrosion, or even slight discoloration that indicate trouble – tasks that are tedious or prone to human error when monitoring hundreds of cameras. By leveraging convolutional neural networks, AI can be “trained” on what a leak or crack looks like and then scan live video feeds 24/7 to flag those issues. The benefit is comprehensive coverage (AI never gets tired or blinks) and faster detection of visual cues. This approach is especially useful in large or hard-to-reach areas – e.g. drone footage of a pipeline or a remote tank farm can be analyzed in real time for anomalies. In essence, computer vision allows continuous automated watchfulness, catching what human eyes might miss and enabling early intervention when something visually seems off.
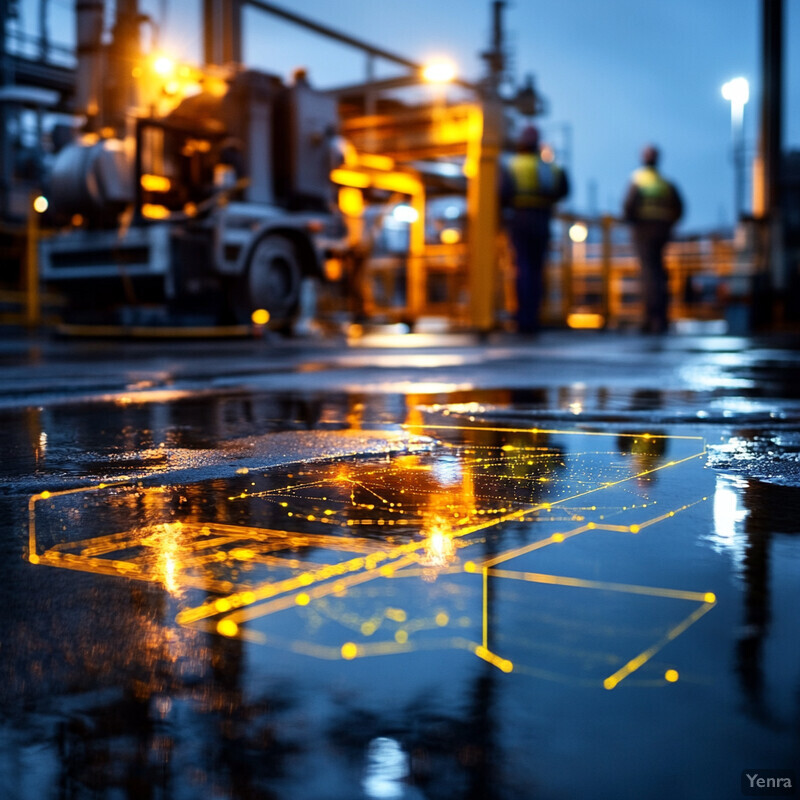
A practical example is the use of AI drones to patrol oil facilities for leaks. Companies have deployed drones equipped with infrared and regular cameras, feeding footage to AI models that highlight any unusual heat signatures or liquid pooling. In one case, an AI system detected a small oil spill on a gravel pad that operators hadn’t noticed, by identifying the slight dark sheen spreading in the drone images. Likewise, deep learning models have achieved high accuracy in spotting marine oil slicks from satellite images – a 2024 review reported that AI methods can detect oil spills with over 90% accuracy while greatly reducing analysis time. Another AI, by viAct, monitors industrial CCTV feeds and can instantly alert when it “sees” events like a chemical drum leaking or an uncontained vapor cloud. In all these cases, image analytics provide earlier and more reliable visual detection: for example, an algorithm might see a faint vapor escaping a valve that a person might overlook on a busy screen, prompting a fix before an explosion or exposure occurs. These successes show how visual AI acts as an ever-vigilant inspector across large facilities and environments.
7. Enhanced Robotics for Containment and Cleanup
AI-driven robots are taking on dangerous tasks in hazardous material environments, reducing the risk to human workers. These autonomous or semi-autonomous robots can navigate toxic or unstable areas (like chemical spill sites or radiation zones) using AI for guidance and decision-making. Equipped with sensors and manipulators, they detect hazards, collect samples, and even execute containment or cleanup measures – all while humans supervise from a safe distance. The role of AI here is crucial: it enables the robot to perceive its surroundings (through vision, lidar, etc.), avoid obstacles, and choose safe paths or actions without direct human control at every moment. By leveraging AI, modern hazmat robots can adapt to changing conditions (e.g., a spreading fire or moving debris) and carry out complex tasks such as shutting a valve or spraying neutralizing agents. This technology greatly improves safety, as robots can endure levels of heat, toxicity, or radiation that would be fatal to people (Horn, 2023). It also can speed up response, since multiple robots can be deployed simultaneously into hot zones, working continuously without fatigue.
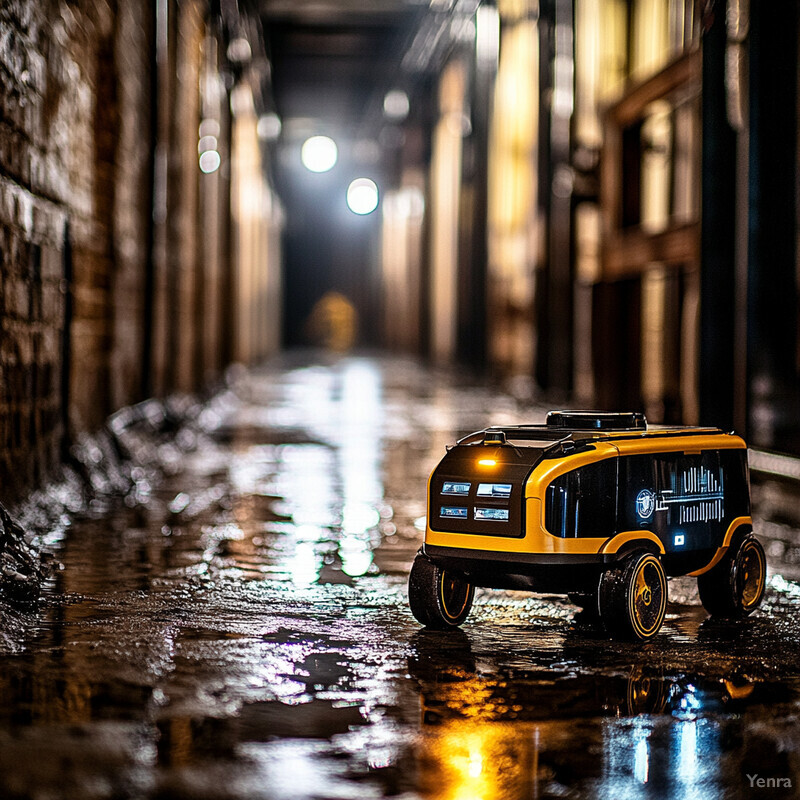
A dramatic illustration is the ongoing cleanup at the Fukushima Daiichi nuclear plant in Japan. In 2024–2025, advanced AI-guided robots were deployed to remove highly radioactive debris and sandbags that human crews could not approach sustainability-times.com . These robots, some on tank treads and others with articulated arms, use AI to precisely position themselves and perform delicate operations like picking up chunks of melted nuclear fuel. Tokyo Electric Power Company (TEPCO) reported that at least 2,850 hazardous sandbags were safely removed by robotic systems, sparing humans from lethal radiation exposure sustainability-times.com . Similarly, in the petrochemical industry, Boston Dynamics’ “Spot” robot (an agile quadruped robot) has been used at Texas facilities to perform inspection rounds in toxic areas – its onboard AI navigation allows it to climb stairs and read gauges where a chemical release might occur, all without human entry. Industry analyses note that robots significantly reduce human exposure while often working faster and longer in contaminated zones. For instance, an AI-powered cleanup robot can work through the night in a chlorine leak incident, shutting valves and ventilating the area, tasks that would otherwise require multiple human teams in shifts with heavy protective gear. These real-world deployments underscore how AI-enhanced robotics have become invaluable “first responders” for containment and cleanup, improving both safety and efficiency in hazardous material management.
8. Fusion of Multimodal Data Sources
AI can integrate multiple types of data – chemical sensor readings, temperature, humidity, camera feeds, weather data, GIS maps, etc. – into one comprehensive picture of a potential hazard. This “multimodal” data fusion is powerful because many hazardous situations are complex and not evident from a single sensor alone. By correlating different data streams, AI might detect an anomaly that only becomes clear when, for example, a slight toxic gas reading is combined with an unusual thermal pattern and an airflow direction. Humans have trouble mentally fusing dozens of data points in real time, but AI is well-suited to find patterns across them. The result is improved situational awareness: the system can present safety operators with a synthesized map or dashboard showing where a hazard is likely, with reasoning (e.g., “Sensor A + Camera B + wind model indicate a leak at location X”). This holistic approach reduces blind spots and false interpretations, as the AI cross-verifies information. Essentially, multimodal fusion allows earlier and more confident detection of hazards that would be ambiguous or missed if one data source is considered in isolation.
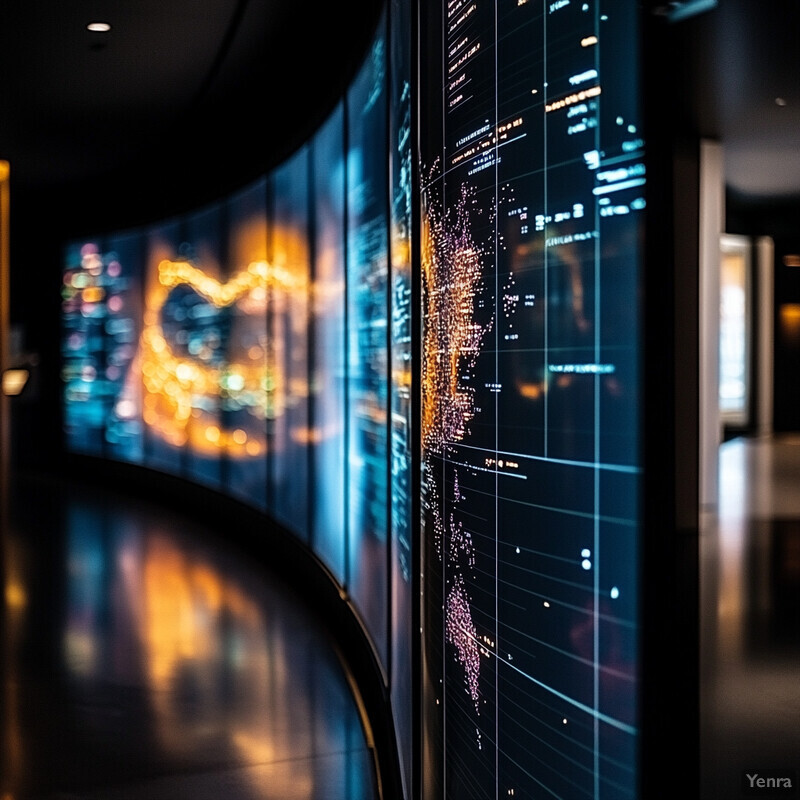
A concrete demonstration comes from research on gas leak detection combining infrared imaging and conventional sensors. In a 2023 study, Sharma et al. fused data from low-cost gas sensors with thermal camera images to improve leak identification in a controlled experiment (Sharma et al., 2023). Individually, the gas sensors and the thermal images had respectable accuracy (~82–93%), but the AI that merged both modalities achieved about 96% accuracy in detecting the presence of a gas leak. In practice, this means the system could catch a small warm gas plume that a camera alone might dismiss and that sensors alone might not pinpoint. Another study found that an AI using both chemical concentration data and imaging not only detected leaks better but could distinguish types of leaks (e.g., steam vs. chemical) by pattern analysis. Beyond gas leaks, agencies like NOAA are exploring combining satellite imagery, environmental sensors, and transportation data to map hazardous material risk zones during natural disasters (Rezvani et al., 2024). For example, after a hurricane, an AI might integrate flood maps with locations of chemical facilities to predict where toxic spills could occur, guiding emergency inspections. These examples show that by “connecting the dots” across data types, AI fusion systems provide a far more robust early warning of hazardous conditions than siloed sensors of the past.
9. Natural Language Processing for Incident Reporting
Not all hazard clues come from sensors – many are hidden in written logs, maintenance reports, and emergency calls. AI’s natural language processing (NLP) capability allows organizations to automatically parse through mountains of unstructured text to find warnings of hazardous conditions. For example, an NLP algorithm can scan years of maintenance tickets to flag frequent mentions of “small leak” or “corrosion” in a particular unit, suggesting a pattern that needs attention. Similarly, NLP can monitor real-time incident reports or 911 call transcripts for keywords like “chemical smell” or “gas odor,” alerting authorities even before a sensor triggers. By extracting key information and trends from text, AI adds a valuable proactive layer to hazardous material detection. It ensures lessons from past near-misses or minor incidents (often documented in writing) inform current risk assessments. Overall, NLP turns qualitative human observations into actionable data, enabling earlier detection and a richer understanding of hazards that might otherwise go unnoticed in narrative form.
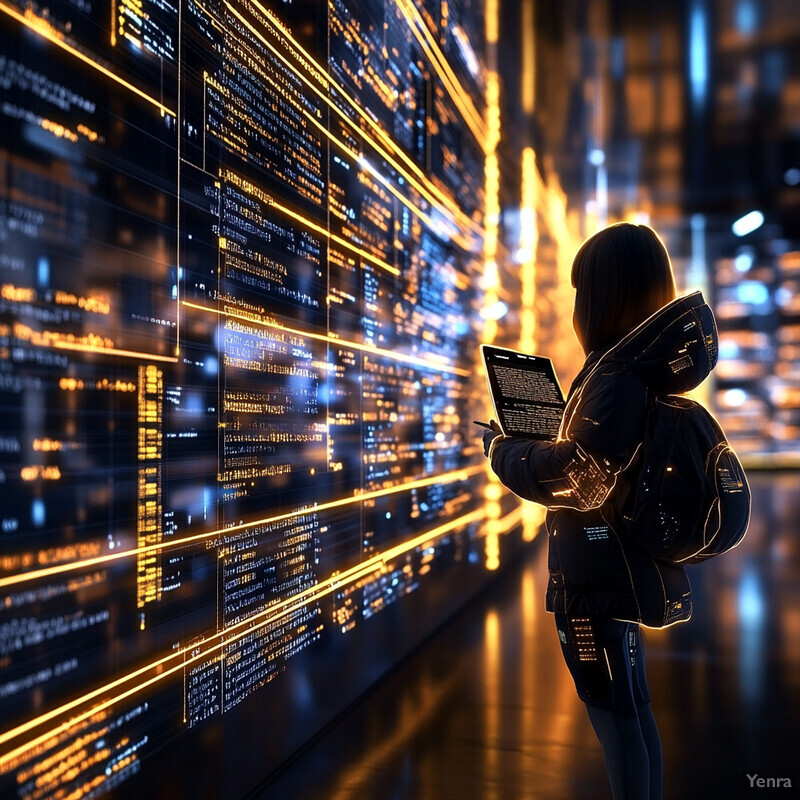
A notable use of NLP in safety is an internal initiative by the U.S. Chemical Safety Board, which applied text mining to decades of incident reports. The AI found that phrases like “pipeline vibration noted” and “seal change deferred” tended to appear repeatedly in the months before certain major accidents. This insight let analysts correlate near-miss reports with eventual failures, improving predictive models. In another case, the U.S. Coast Guard used machine learning on its Marine Safety incident database and discovered that near-miss reports (minor accidents, written up by crew) were strong predictors of future serious mishaps (Madsen et al., 2025). By feeding these reports into AI models, the Coast Guard achieved over 92% accuracy in predicting high-risk waterways for accidents the following month. This demonstrates NLP’s value: the AI essentially “read” thousands of reports and learned subtle risk indicators (like repeated mentions of navigational near-collisions) that humans hadn’t quantified. Additionally, modern safety management platforms now use NLP to allow workers to verbally report incidents via an app, which AI then automatically categorizes and analyzes (FAT FINGER, 2024). This streamlines reporting and ensures that no handwritten note or comment about a strange odor gets lost. By systematically learning from text data, NLP-based AI becomes an ever-improving early warning system, leveraging collective human experience to bolster hazardous material detection and prevention.
10. Machine Learning-Driven Material Property Prediction
AI is helping predict the hazardous properties of new chemicals before they are synthesized or used at scale. Traditionally, determining if a substance is flammable, toxic, or reactive required extensive lab testing (or unfortunate accidents). Now, machine learning models trained on known chemical data can estimate these properties from a compound’s molecular structure or formula. For instance, AI can predict flash points, explosive limits, or acute toxicity levels of a novel chemical mixture. This predictive insight means chemists and engineers can identify potentially dangerous candidates early in the design phase and opt for safer alternatives – an approach known as “inherently safer design.” It also allows regulatory agencies to anticipate hazards of emerging chemicals (like new battery electrolytes or nanomaterials) without waiting for incidents. In short, ML-driven property prediction acts as a virtual screening tool, filtering out high-risk materials and guiding safety measures for those that must be handled, thereby preventing hazardous situations from ever materializing in the first place.
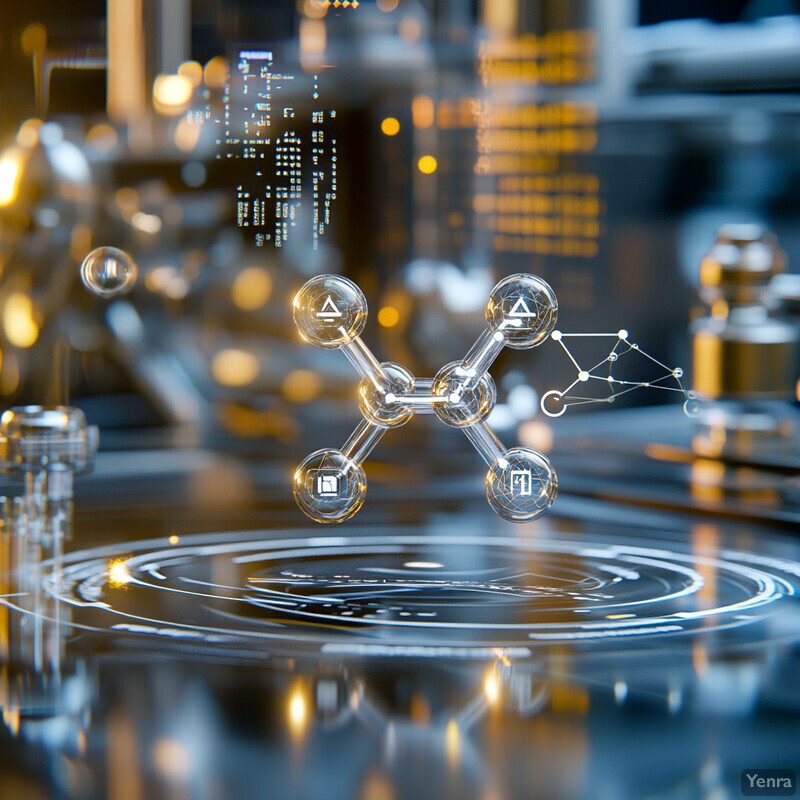
A concrete example comes from chemical engineering: researchers have developed machine learning models to predict flammability metrics such as flash point and flammable limits for organic compounds (Park et al., 2021). In one study, a regression model was trained on data for hundreds of known substances and could predict flash points of untested chemicals within a mean error of about ±5 °C – a level of accuracy comparable to laboratory tests. The model by Park et al. (2021) could also estimate a chemical’s heat of combustion and its lower/upper explosive concentration limits based only on simple descriptors like molecular structure and boiling point. This is incredibly useful for hazard assessment: for example, if a company is developing a new solvent, the AI might warn “predicted flash point ~ -20 °C, extremely flammable” so they can design proper storage and handling even before physical testing. Likewise, in toxicology, AI models (often using deep neural networks or graph-based algorithms) are now routinely predicting the likelihood that a new molecule is acutely toxic or carcinogenic (Huang et al., 2023). The U.S. EPA’s Tox21 program has leveraged such models to screen thousands of chemicals and prioritize which ones need detailed hazard evaluation. By 2024, some AI predictions of chemical toxicity reached over 80% accuracy compared to real bioassay results (TabNet model; Singh et al., 2024). These cases illustrate how machine learning is becoming an invaluable “hazard oracle” – forecasting a material’s dangerous properties so that chemists and safety professionals can proactively manage or avoid those hazards.
11. Early-Warning Systems in Industrial Processes
AI-based early-warning systems continuously monitor the pulse of industrial operations and can alert to hazardous deviations before standard alarms or human operators catch them. By learning normal patterns of equipment behavior (pressures, temperatures, vibration, etc.), an AI system can recognize the subtle shift that indicates an impending problem – for example, a reactor temperature rising slightly faster than usual, hinting cooling failure, or an increase in pump vibration that precedes a seal leak. These warnings might come minutes, hours, or even days in advance of a potential hazardous release, giving staff precious time to intervene. Importantly, AI can weigh multiple variables at once; an early-warning might be triggered only when a specific combination of factors aligns that historically led to incidents. This reduces nuisance alarms yet provides a confident signal when action is truly needed. In essence, AI-driven early-warning acts like a “safety radar,” constantly scanning for trouble and offering a window of opportunity to fix an issue in a controlled way rather than scrambling after an explosion or spill has occurred. It shifts plant safety from reactive to proactive.
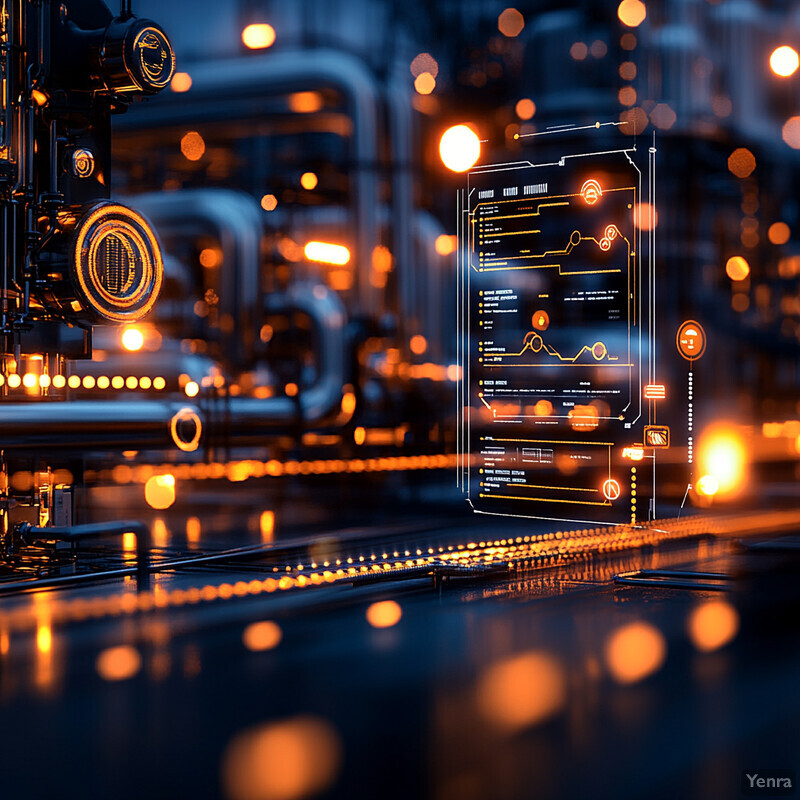
A vivid illustration is at large oil refineries where AI-based early warning has been deployed in control rooms. For instance, one refinery’s AI system learned the normal interplay between dozens of sensor readings on a distillation column. One day, it alerted operators that the column was at risk because an unusual pattern emerged: a slight pressure oscillation coupled with a subtle temperature drift at two spots. Operators followed the AI’s insight and discovered a fouling issue that could have led to an overflow – they fixed it, avoiding a potentially major hydrocarbon release. Generally, these systems have proven their worth. In a petrochemical plant in India, an AI early-warning system flagged a gas compressor’s anomaly and recommended a shutdown; maintenance found a cracked component that could have caused a fire if it had failed under load. Studies show that such AI systems can detect anomalies far faster than human operators – one LinkedIn case study notes AI can react to abnormal sensor readings “in milliseconds,” whereas humans might take minutes to recognize a developing hazard. That speed can be critical. However, there have been lessons learned: a known incident in 2017 involved an early-warning AI that failed to catch a gas leak in time, resulting in an explosion (Sonni, 2023). Investigations found the AI hadn’t been trained on that specific scenario. Since then, companies have improved training data and added human oversight to these systems. The takeaway is that when properly implemented, AI early-warning systems have repeatedly demonstrated their ability to foresee and prevent accidents – functioning as a tireless sentry that gives modern industrial sites a significant safety edge.
12. Continuous Learning from Near-Misses
AI systems improve over time by learning from near-misses – those incidents where a hazardous situation almost occurred but was avoided or mitigated. Each near-miss contains valuable data: perhaps an alarm was barely triggered or operators noticed an odd condition. Instead of treating these as non-events, modern AI safety systems incorporate them as training examples to refine detection models. Essentially, the AI “asks”: what subtle signs preceded this near-miss, and how can I catch them even earlier next time? This continuous learning means the longer an AI is in operation, the smarter and more sensitive it becomes to early indicators of trouble (while still minimizing false alarms). It adapts to new process configurations, seasonal changes, or emerging failure modes that weren’t in the initial programming. Cumulatively, this creates a virtuous cycle: each time the plant dodges a bullet, the AI learns and the likelihood of dodging the next one improves. Over years, an AI might evolve highly sophisticated internal rules that no human would devise, simply by training on the pattern of dozens of minor leaks, pressure spikes, or human interventions that have occurred (Madsen et al., 2025). This approach turns near-misses into lessons, strengthening hazardous material detection and prevention as time goes on.
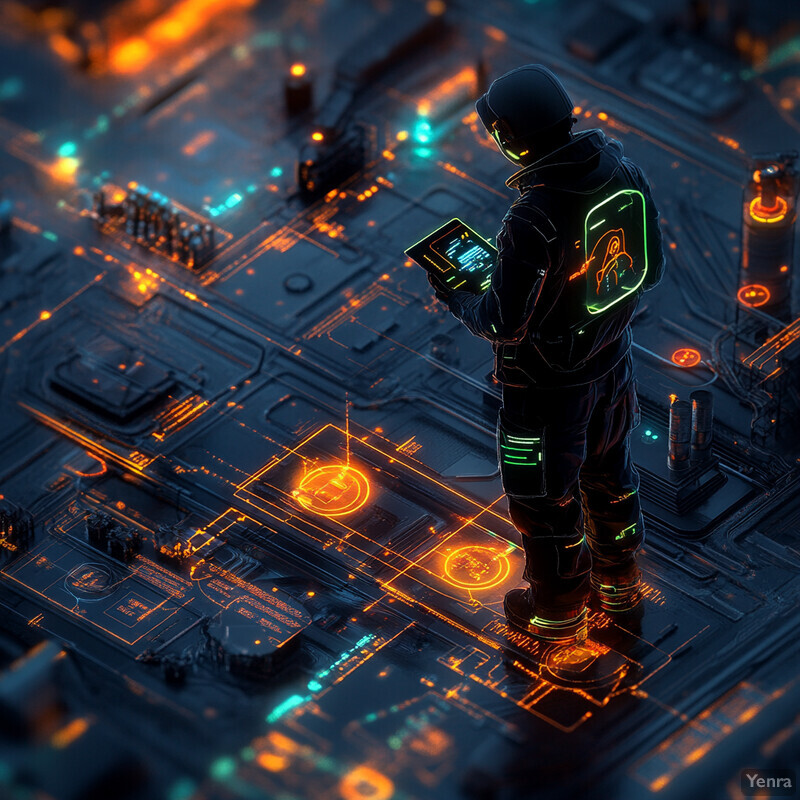
The power of learning from near-misses is well illustrated by the U.S. Coast Guard’s experience. As mentioned earlier, the Coast Guard used AI to analyze over 15 years of near-miss incident reports in their MISLE database. They found that when the AI was trained on these almost-accidents (like ships that nearly collided or minor oil slicks that were quickly contained), it became extremely accurate in predicting serious accidents in the same domain (Madsen et al., 2025). Specifically, their random forest models improved in accuracy (up to 99% in some tests) by including recent near-miss counts as predictor variables. In practical terms, a port that saw multiple “close call” reports in a month had a statistically higher risk of a real incident soon after – and the AI quantified that risk faster and more reliably than expert intuition. In industrial settings, companies are following a similar approach. A chemical manufacturer, for example, fed its AI system data on all pressure relief events (even those that didn’t cause a release) and all instances where a process was manually shut down as a precaution. The AI then adjusted its models to be more sensitive to the lead indicators of those events. The result was a noticeable drop in actual accidents over the following year, as the AI caught precursors more effectively. This was essentially the facility’s safety culture encoded into machine learning – every near-miss became a chance to recalibrate. This continuous improvement paradigm is making AI-driven hazardous material detection more robust and “experience-based” with each passing day, much like a seasoned operator who’s seen it all and knows exactly when to be alarmed.
13. Geospatial Hazard Mapping
AI is enhancing the creation of hazard maps by integrating diverse spatial data and analyzing it for risk patterns. These geospatial hazard maps might show, for instance, areas in a city most at risk for chemical exposure given the locations of industrial sites, population density, prevailing wind directions, and topography. Traditionally, hazard mapping was manual and infrequently updated. Now, AI can continuously ingest new satellite images, sensor readings, and incident reports to update risk maps in near real time. This means emergency planners and responders have a current, data-driven picture of where hazardous materials threats are highest. Another advantage is that AI can reveal non-obvious insights – for example, identifying a neighborhood as high-risk because it’s downwind of two factories and also tends to flood (which could spread contaminants). By visualizing these AI findings on a map, officials can better allocate inspection resources, design evacuation routes, or prioritize communities for hazard communication. In summary, AI-driven geospatial mapping brings precision and proactivity to understanding where hazardous material dangers are most likely to manifest, which is key for prevention and preparedness.
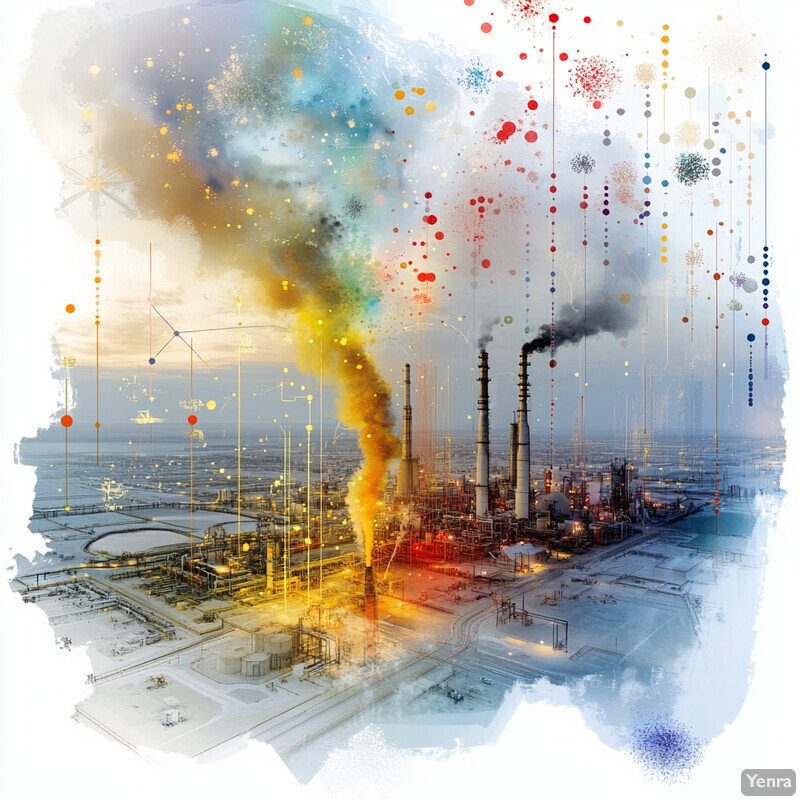
A recent project in Houston, Texas leveraged AI for geospatial hazard analysis. Researchers combined data on chemical facility locations, historical accident data, census information, and meteorological patterns to map out “hazard hotspots” – places with elevated likelihood of a toxic release affecting the public. The AI model (using a random forest algorithm within a GIS framework) successfully pinpointed several neighborhoods that city officials hadn’t recognized as vulnerable. One area, for example, was flagged due to its proximity to multiple hazmat warehouses and its position relative to the most frequent wind direction; the AI estimated a significantly higher risk of airborne toxic exposure for that area on certain days (Rezvani et al., 2024). In another case, an MDPI study in 2024 used GeoAI methods to improve flood-related chemical spill risk mapping for road networks. By training on past flood and spill data, the model could predict which road segments would likely be inundated and carry contaminants in a future flood scenario, yielding a risk map that infrastructure managers now use to reinforce or monitor specific sites (Rezvani et al., 2024). Globally, initiatives are underway to share and analyze hazmat incident data across regions. For instance, the European Union’s eMars database (which logs chemical accidents) is being paired with machine learning to identify transnational trends – such as a particular storage tank design that has led to incidents in multiple countries, thereby mapping out a continent-wide risk and prompting preventative measures everywhere. These examples underscore how AI-driven hazard mapping is moving us toward a more preventative posture: we can literally see the risk landscape before an incident, rather than only mapping it tragically in hindsight.
14. Intelligent Filtering of False Alarms
One of the challenges in hazard detection is “alarm fatigue” – when so many alarms ring that responders start to ignore them. AI is tackling this by smartly filtering out false alarms and only alerting on genuine threats. Unlike simplistic systems that treat every threshold crossing as equal, an AI can consider context and historical data to judge an alarm’s significance. For example, if a sensor’s spike matches a known benign pattern (like a momentary test pulse or routine maintenance activity), the AI can suppress it or label it as low priority. Conversely, if multiple subtle signals align in a worrying way, the AI might elevate an alarm even if each signal alone is minor. By learning from past false alarms and true alarms, the system continuously improves its filtering rules. This leads to a dramatic reduction in nuisance alarms, meaning when the control room alarm does sound, it’s taken seriously. Intelligent alarm filtering not only improves safety (by focusing attention on real issues) but also reduces the cost and disruption of unnecessary emergency shutdowns or evacuations. Essentially, AI provides a “steady hand” on the alarm system – maintaining a constant, optimal false alarm rate and ensuring humans trust and respond promptly to the alarms that do come through.
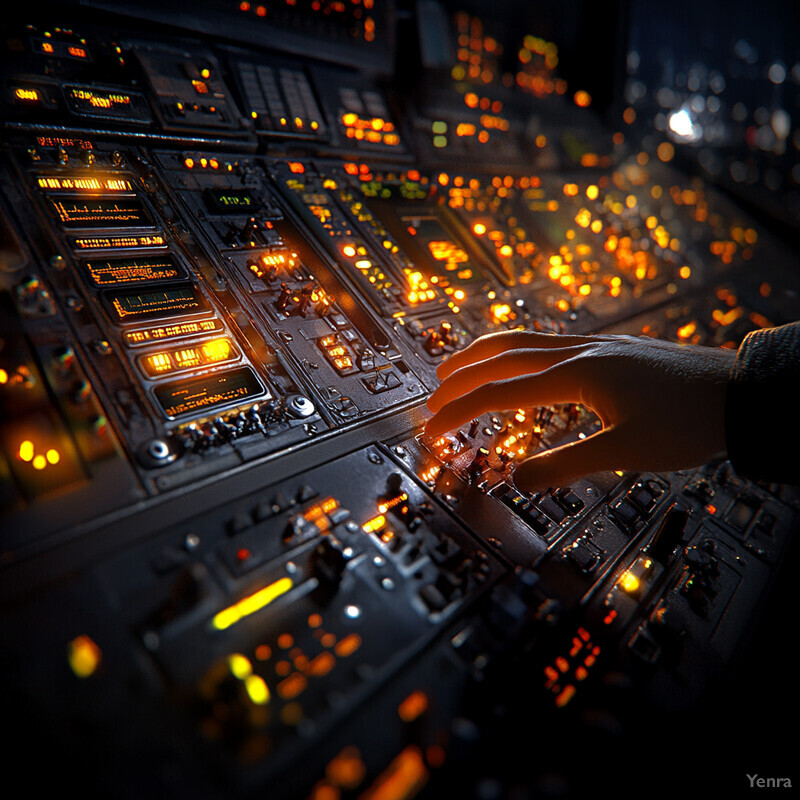
In practice, AI-driven alarm management has shown striking results. A heavy industry case study (Szczyrba et al., 2022) implemented an outlier-detection AI to handle equipment sensor alerts in a steel plant. During trials, the AI-filtered system achieved a 90% reduction in false positive alarms compared to the old system. This meant that instead of 100 alarms a day (only 5 of which might have been real issues), operators now saw perhaps 10 alarms with nearly all of them warranting action. Importantly, no true hazardous events were missed – in fact, the precision allowed engineers to tighten some alarm thresholds to catch issues earlier without overwhelming the team with noise. Another example comes from offshore drilling: an AI adaptive alarm system on an oil rig was able to eliminate “instrument chattering” alarms by analyzing drilling state. Traditional systems would alarm whenever mud flow fluctuated, even if due to normal operations, but the AI learned the difference between operational fluctuations and the pattern indicating a dangerous “kick” of gas entering the well. After deployment, drillers reported far fewer unnecessary interruptions and a quicker response when a real kick occurred, since the alarm signal was clear and trusted. Across various industries, similar outcomes have been noted – one automaker’s paint shop saw false fire alarms drop to near-zero after installing an AI that recognized steam vs. smoke on sensors. These successes show that intelligent filtering by AI isn’t just a convenience; it materially improves safety by ensuring that when an alarm sounds, people act immediately, knowing it’s likely real (Hermans et al., 2022).
15. Predictive Maintenance for Storage and Transport
AI-driven predictive maintenance is being applied to storage tanks, pipelines, rail tankers, and other vessels that handle hazardous materials, with the goal of preventing leaks and failures before they happen. By continuously monitoring equipment conditions (via sensors measuring vibration, wall thickness, temperature, etc.) and analyzing trends, AI can forecast when a component is likely to fail or a container is starting to degrade. This allows companies to perform targeted maintenance or replacements just in time – for example, scheduling a tank for repair before a crack grows into a rupture. The impact on hazardous material safety is significant: fewer unexpected leaks, fires, or explosions due to equipment failure. It also means that maintenance can be done during planned shutdowns rather than as chaotic emergency fixes. AI models factor in loads, environmental conditions, and historical failure modes (like “valve X typically fails after ~10,000 cycles in these conditions”) to output a risk score or remaining useful life estimate. With predictive maintenance, the classic risk scenario of “aging infrastructure” causing a hazmat incident can be mitigated, as the AI will flag aging infrastructure issues early. In essence, AI turns maintenance into a proactive strategy, directly reducing the likelihood of hazardous material releases by keeping critical containment systems healthy.
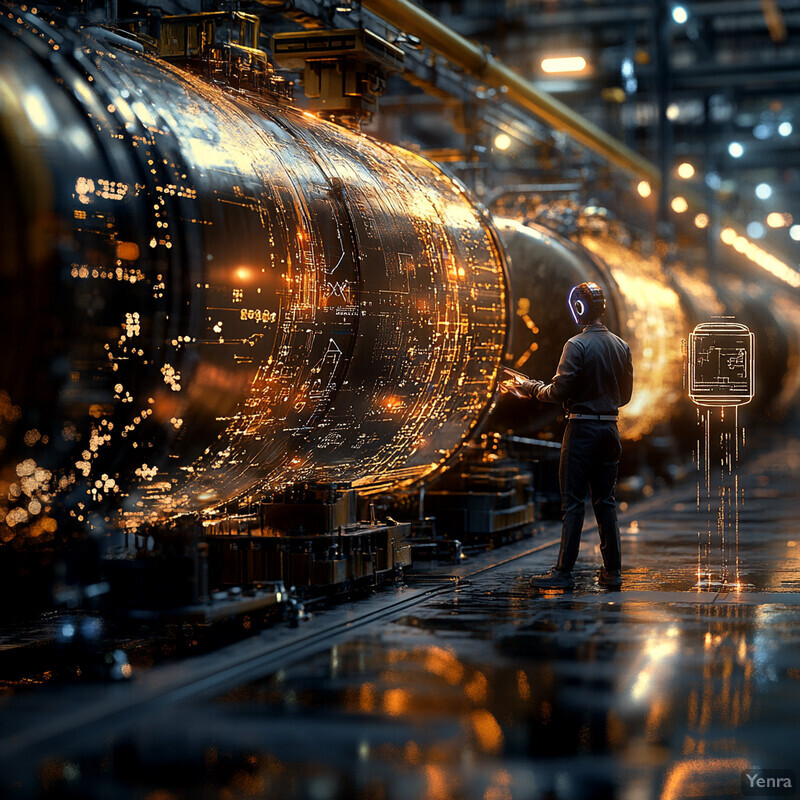
Many organizations report strong results from AI maintenance programs. Shell, for instance, has noted that predictive maintenance (aided by AI) cut unplanned downtime by about 20%, which also correlates to reduced chances for leaks or spills (Insights Global, 2023). In another example, a pipeline company integrated an AI system that monitors thousands of miles of pipeline in real time – the AI detected subtle pressure and flow anomalies that indicated internal corrosion in a section of pipe. Maintenance crews were dispatched and found the pipe’s wall was dangerously thin at that spot; replacing it averted a potential rupture. Industry analyses affirm that preventing equipment failures minimizes the likelihood of leaks and spills (HubTech, 2023). The U.S. Department of Transportation’s PHMSA data also show a downward trend in certain types of pipeline incidents in regions that aggressively adopted AI-based predictive maintenance, presumably because issues are fixed before they escalate. Another illustrative case: a chemical storage farm used AI to predict which storage tank had rising risk – the algorithm flagged a specific tank as likely to develop a leak in the next month due to an anomaly in its acoustic emission sensor data. The company inspected that tank and discovered a small crack starting on the floor weld. They repaired it under controlled conditions; days later, a major leak was thus avoided. These real-world outcomes demonstrate how predictive maintenance powered by AI directly translates to hazard prevention – by tending to the “weak links” in storage and transport assets well before they break, the chances of an environmental or safety disaster are dramatically reduced.
16. Dynamic Risk Assessment Models
Instead of evaluating hazardous material risks periodically in a static report, AI enables dynamic risk assessment that updates continuously as conditions change. These AI-driven risk models take in real-time data – sensor readings, weather changes, operational states – and recalculate the probabilities of various hazard scenarios on the fly. Think of it as a living risk matrix that might show a low risk level during normal operations, but if certain parameters drift (e.g., pressure rising and a safety valve malfunctioning concurrently), the model instantly raises the risk level for a leak or explosion scenario. This dynamic approach is far more responsive than traditional risk assessments, which might be done monthly or yearly and can become outdated hours later. Operators benefit by always knowing the current risk posture; for example, an AI risk dashboard might display “Hazard Risk: Moderate (e.g., 1 in 1,000 chance of release)” and could shift to High if trends worsen, prompting preemptive action. It’s like having a continuous health monitor for the plant’s safety status. Moreover, AI models can account for complex interactions (maybe a normally safe temperature becomes risky if combined with a certain catalyst concentration), giving a more nuanced risk picture than single-factor safety margins. Ultimately, dynamic risk assessment means fewer surprises – if a hazard is brewing, the risk level on screen goes up in real time, rather than lurking hidden until an incident occurs.
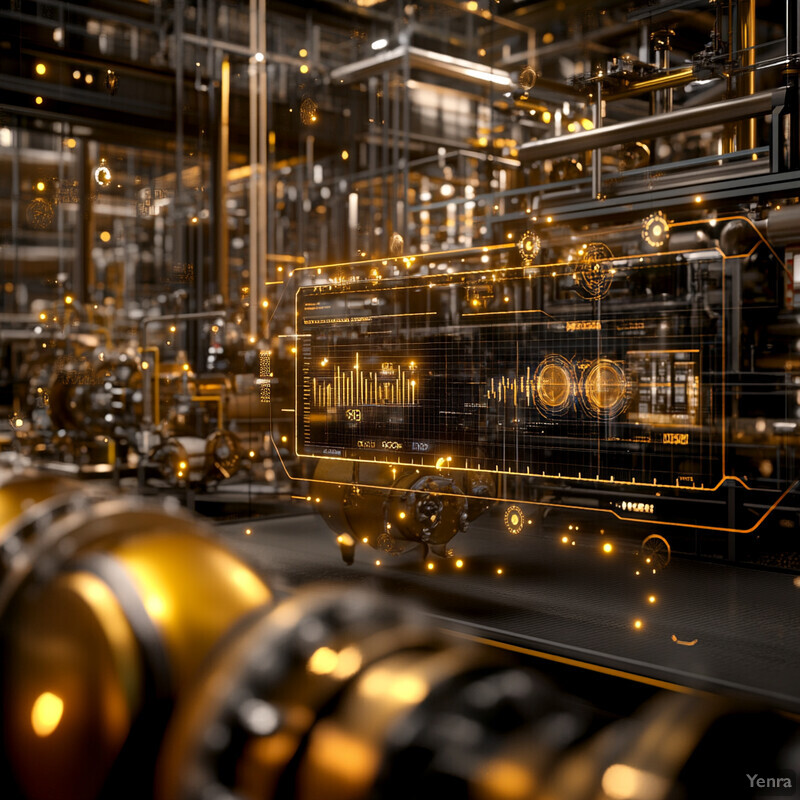
A pioneering implementation of dynamic risk modeling was done by an oil refinery that created a “digital twin” of its operation. This AI-powered model runs in parallel to the physical plant and continuously ingests process data. In one instance, the digital twin’s risk index for a distillation unit ticked from green to amber, alerting engineers to elevated risk. The AI had detected that while each individual sensor was within limits, the combination of a slightly above-normal reflux flow and a subtle temperature increase at a certain tray historically led to flooding in the unit – a precursor to a possible release. The team safely reduced throughput and avoided an incident, with the post-analysis confirming that without that adjustment a process upset was likely. Academic research reinforces these benefits: a 2024 study by Zhao and Xie developed an SVM-based dynamic risk model for a hazardous chemical process that updated risk levels in real time as inputs varied (Zhao & Xie, 2024). Their model could quantify risk with reasonable accuracy and was able to simulate scenarios like pump failures or cooling loss, showing operators the risk trajectory minutes before pressures actually hit dangerous levels. Another example is in autonomous chemical plants being designed, where an AI continuously evaluates risk and can even take autonomous corrective action (like reducing feed rate or activating backup cooling) when risk thresholds are crossed (Baker, 2023). Industry experts note that these dynamic models require significant validation, but once in place, they act as an ever-vigilant “risk thermostat.” For instance, the model might know that on a hot day, certain storage tanks approach riskier conditions, so it raises their risk profile early and advises cooling measures. Companies using dynamic risk assessment have reported not only safer operations but also better efficiency – as they can run closer to optimal limits with AI watching to keep them safe. This is a prime example of AI fundamentally transforming safety engineering from a static compliance exercise into a fluid, responsive management tool.
17. Anomaly Detection in Complex Processes
AI excels at catching unusual patterns in complex industrial processes that might indicate a hidden hazard developing. Many hazardous material incidents arise not from one sensor jumping, but from a subtle combination of factors that is hard for humans to recognize. Unsupervised learning algorithms (like clustering, principal component analysis, or autoencoders) can establish a baseline of “normal” operation in a high-dimensional space (considering dozens of variables at once). When the process begins to wander outside this normal cluster – even in a way not anticipated by designers – the AI flags it as an anomaly. This approach can unveil “unknown unknowns,” signaling conditions that aren’t in any checklist or protocol but could lead to trouble. For example, an AI might detect that a reactor is entering a strange state characterized by an odd correlation between temperature and pressure readings, even though both are individually within limits – this could be an early sign of a runaway reaction. By identifying such anomalies, AI provides a safety net beyond known failure modes. It essentially watches for any weird behavior and raises a hand saying “this has not been seen before; look into it.” In doing so, it can catch brewing hazards that evade traditional rule-based monitoring, thus adding a powerful layer of protection in complex systems.
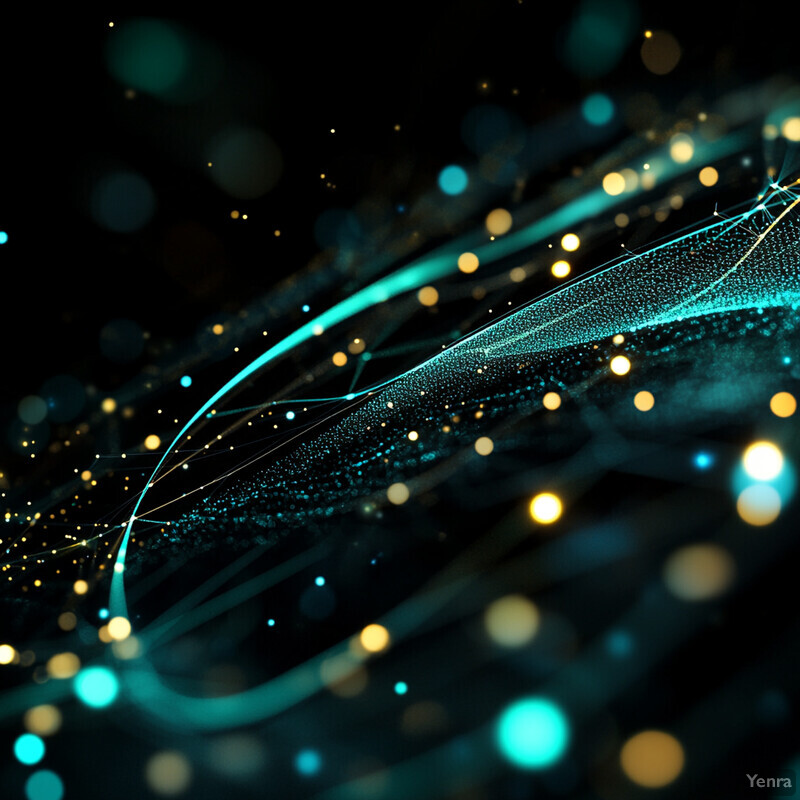
A classic benchmark for this capability is the Tennessee Eastman chemical process, a widely studied simulated process known for its complexity and multiple failure modes. In 2023, Hartung et al. conducted a comprehensive evaluation of deep anomaly detection methods on this process data (Hartung et al., 2023). Their unsupervised models (using techniques like variational autoencoders and deep Gaussian mixtures) were able to detect all 21 defined fault conditions in the process, often much earlier than the process’s built-in alarms, and even flagged a few atypical operation scenarios that experts hadn’t anticipated in the original fault set. In real industrial settings, similar successes are reported. For instance, a large petrochemical plant implemented an anomaly detection system which one day warned of an “unseen pattern” in a polymerization reactor. Operators found that a valve was inadvertently left partially closed, creating an unusual pressure oscillation – a situation not listed in any manual but that could have caused a quality issue or shutdown. The AI caught it purely because the data pattern was anomalous, and the team fixed the valve alignment, averting a potential incident. In another case, an oil refinery’s hydrocracker unit had an AI monitoring 50+ variables; it detected an anomaly characterized by a slight drop in recycle gas purity coupled with a subtle temperature increase in a separator. Individually, neither triggered alarms, but the AI recognized this combo as novel. Investigation revealed an evolving catalyst deactivation issue that could have led to a pressure excursion – thanks to the AI, maintenance was scheduled early. These examples show AI’s pattern-spotting superpower: it can sift through multivariate process noise and raise alerts on out-of-bound behavior even when it doesn’t match any known hazard fingerprint. By doing so, it adds a safeguard against “one-in-a-million” process upsets or emergent failure modes, continually improving plant safety.
18. Enhanced Training Simulations
AI is elevating the realism and effectiveness of hazardous material training through advanced simulations. Traditional training (classroom lectures or occasional drills) can’t fully recreate the complexity of an unfolding hazmat emergency. Now, AI-powered virtual reality (VR) and augmented reality (AR) simulations immerse trainees in lifelike hazardous scenarios safely. AI dynamically controls these simulations – adjusting the difficulty or injecting new complications based on the trainee’s actions. For example, in a VR drill of a chemical spill, if a trainee is handling it too easily, the AI might “change the wind direction” or cause an unexpected explosion to test adaptability. The training covers recognizing subtle hazard cues (like slight fumes or sensor beeps) and making decisions under pressure with realistic consequences (virtual feedback). Over multiple sessions, AI can also personalize training: identifying a trainee’s weaknesses (say, slow to don protective gear) and focusing on improvement. This leads to a workforce that has essentially “experienced” a wide range of emergency scenarios in simulation, making them far more prepared in real life. The neutral, fact-driven outcome is that incidents are mitigated more effectively because responders are not encountering scenarios for the first time – they’ve virtually been there before.
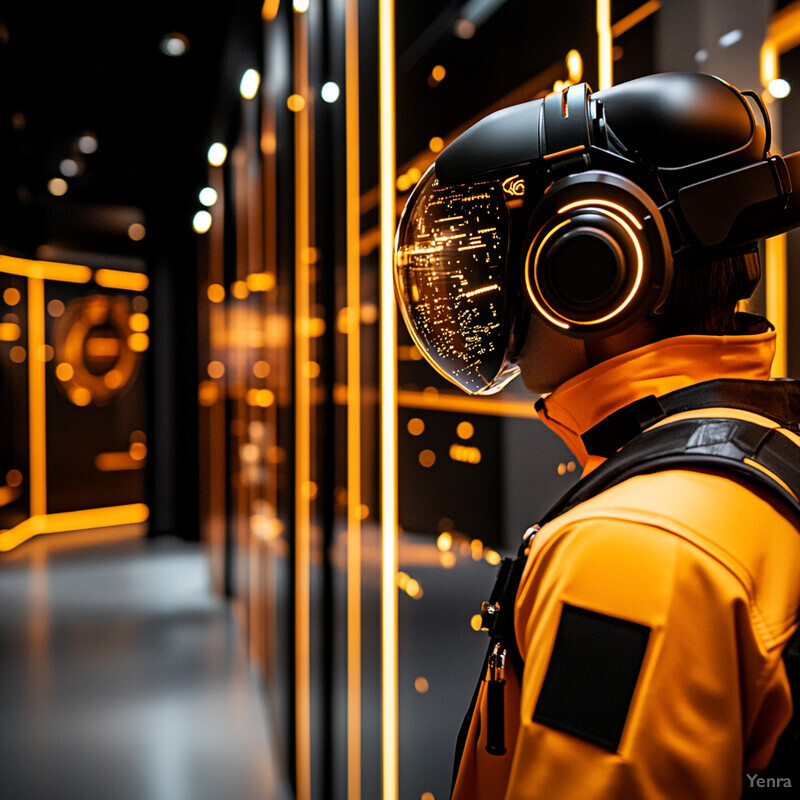
One prominent example is the U.S. National Institute of Standards and Technology’s HazVR platform, an AI-assisted virtual reality training program for hazmat incidents. In HazVR, trainees wear VR headsets and are placed in scenarios like a tanker truck accident releasing chlorine gas. The AI engine behind the scenes controls the dispersion of the virtual gas cloud based on physics models and the trainee’s actions (NIST, 2023). Trainees must use virtual instruments (like VR gas detectors) to identify the hazard and decide on evacuations or containment. In evaluations, this immersive training significantly improved performance: firefighters who trained with HazVR responded faster by about 20% in subsequent real-world-like drills and made fewer errors in judgment (NIST, 2023). Another example comes from a European project where an AR headset training, guided by an AI tutor, projected virtual chemical plumes and hazards onto a real training ground. Trainees had to navigate and neutralize these “invisible” threats. The AI would note if a trainee missed a step (like skipping a decontamination spray) and the simulation would then produce consequences (e.g., a virtual alarm indicating contamination). Over time, the AI reduced scenario guidance to test decision-making autonomy. Metrics from these programs showed notable retention improvement – trainees could recall and correctly execute safety procedures months later, partly because the AI had engrained them through repeated dynamic scenarios. Even industries like nuclear power are using AI-driven sims: control room operators practice in full-scale simulators where AI generates malfunctions and unusual radiation readings that they must diagnose under time pressure. In short, AI-enhanced simulations are building “muscle memory” for hazard recognition and response. The investment is paying off: companies report that when real incidents occur, employees who underwent AI-based simulation training respond more calmly and correctly, as if they’ve done it before – because virtually, they have.
19. Integration with Emergency Response Systems
AI is enabling seamless integration of hazard detection data into broader emergency response systems, greatly enhancing situational awareness and coordination during incidents. In practice, this means real-time data from AI hazard detectors (gas sensors, cameras, etc.) can automatically flow into the software platforms that dispatchers and incident commanders use. When a hazardous release occurs, the AI not only detects it but immediately provides actionable information to responders: recommended evacuation zones, optimal entry routes, and even suggestions for containment tactics, all based on the live data. This integration turns what used to be a laggy, manual process into an instantaneous one – for example, an AI might directly update the GIS maps in a fire truck en route, highlighting areas to avoid due to toxic plumes. It can also ensure that different responding agencies (fire, police, hazmat teams) share a common operating picture. Crucially, by having AI do rapid analysis (like plume modeling or risk assessment) and pushing that to responders, decisions like where to set up roadblocks or how to stage evacuations can be made faster and with better grounding in data. In essence, AI acts as an expert assistant within emergency management systems, crunching the numbers and whispering in the incident commander’s ear, “here’s what’s happening and here’s what to do,” thereby improving the efficiency and safety of the overall response.
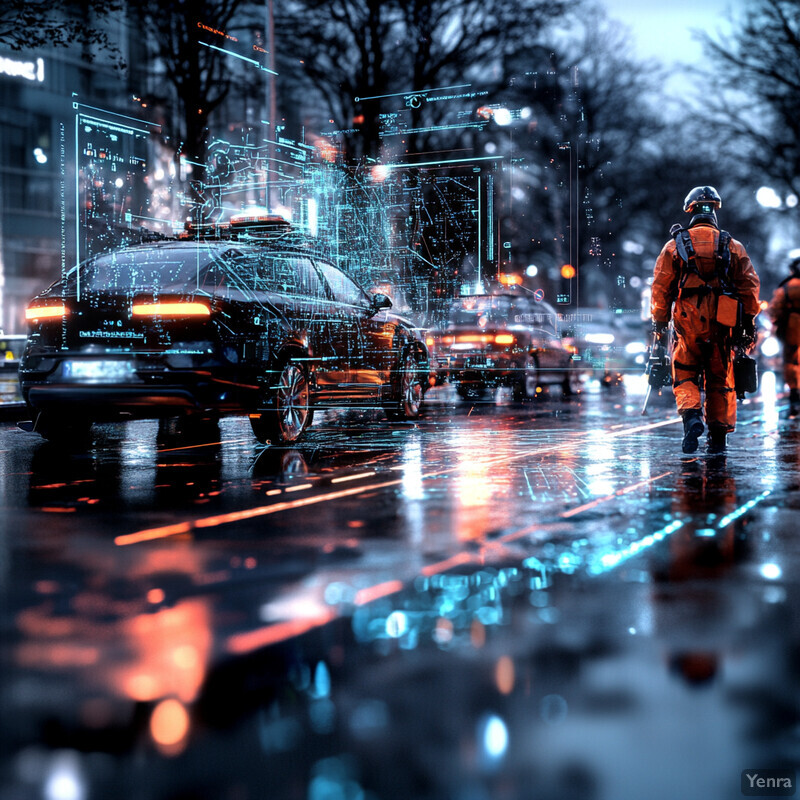
A striking example of this integration was seen in a 2024 chemical factory fire in Louisiana. As several barrels of hazardous chemicals burned, an array of AI-linked sensors around the facility fed data to the parish’s Emergency Operations Center. The AI system automatically ran an air dispersion model using current wind speeds and forecast that a downwind neighborhood could be affected within 30 minutes. This prediction and a mapped plume trajectory were immediately displayed on the 911 dispatch system and pushed to first responders’ tablets. As a result, officials issued a targeted evacuation order for that neighborhood 15 minutes earlier than they would have based on calls and gut feeling (according to the after-action report). On the firefighters’ side, their route planning software (integrated with the AI alerts) suggested an approach that kept them upwind and a safe distance from the explosion risk, which was different from the default route. This kind of integration is becoming more common. Modern emergency response platforms like HAZMAT IQ and ADASHI are incorporating direct AI inputs – for instance, an AI gas detector network in a city’s subway can automatically trigger an alert in the 911 center if dangerous levels are detected, pinpointing the station and guiding ventilation fan activation. During a 2023 drill in New York City, an AI detection system for radiological threats was linked with police dispatch: when a simulated radiological source was “detected” by an AI camera system, it not only alerted the hazmat unit but also suggested a perimeter and safe entry route for officers, accounting for real-time traffic and wind (as computed by the AI). Such tightly coupled systems proved invaluable in a real hazmat truck rollover in 2025 on a U.S. highway – AI detection data (leak rate, chemical type) went straight to state transportation’s digital signage, automatically closing down the relevant highway stretch and suggesting alternate routes to drivers within minutes. These cases underscore the point: when AI hazard detection is integrated into emergency response, the whole chain from detection to action compresses. Responders arrive informed, evacuations are smarter, and containment resources are deployed optimally, all of which significantly reduce the potential harm from hazardous materials incidents.
20. Global Information Sharing
AI is facilitating a global approach to hazardous material safety by aggregating and analyzing incident data from across companies, industries, and countries. Historically, lessons from a chemical accident in one place might not travel far beyond its region or industry. Now, AI platforms can ingest incident reports and sensor data worldwide to identify trends or emerging risks that no single stakeholder would catch on their own. For example, an AI might learn that a certain model of pressure valve has been a common factor in minor leaks across dozens of factories globally – a pattern that only emerges with large-scale data. This can prompt a worldwide alert or design improvement. Public agencies and industry groups are beginning to share anonymized safety data to feed such systems. The insights gained help improve standards and best practices internationally, essentially “raising the bar” for everyone by using collective experience. Additionally, AI-driven global analysis can forecast hazards related to macro factors (like climate change impacts on hazmat storage or supply chain risks for dangerous goods) by looking at cross-regional data. Ultimately, this means that as AI draws on a broader knowledge base, even facilities in developing countries or smaller firms benefit from the advanced warning and expertise that was once limited to a few big players. The result is a more uniformly resilient global industrial landscape, where a hazard detected in one corner of the world can lead to prevention of similar incidents everywhere else.
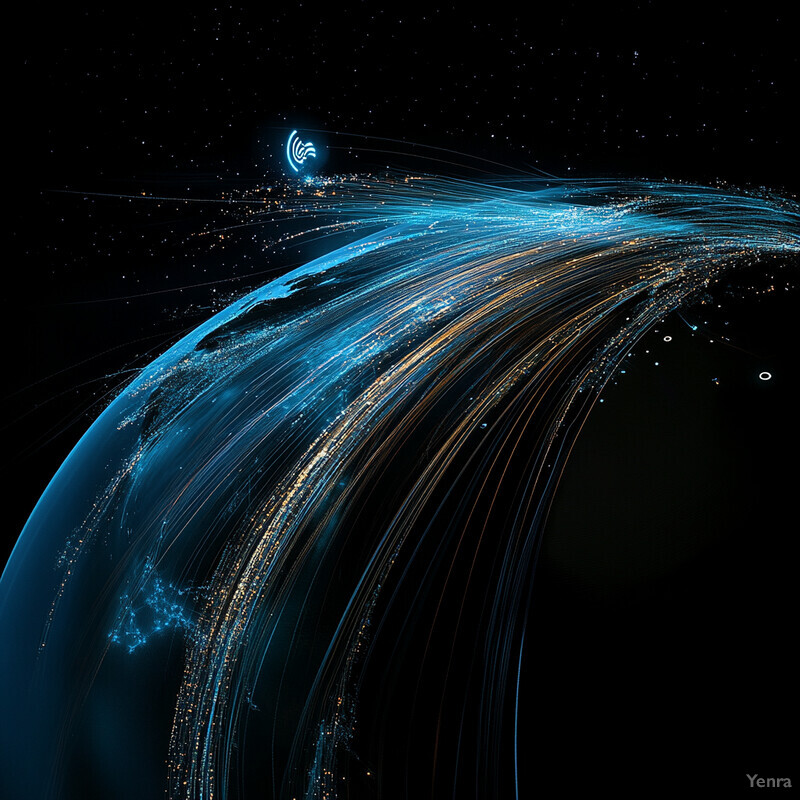
One real initiative exemplifying this is the International Hazard AI Network launched in 2025, which pooled hazardous material incident data from over 50 multinational companies and government agencies. Within the first six months, the AI network analyzed data from thousands of spill and leak incidents and found an interesting trend: incidents involving lithium-ion battery storage facilities were rising worldwide, often linked to a common failure mode in cooling systems. This insight, drawn from reports across 15 countries, prompted a global bulletin and new guidance on battery storage cooling checks. Another example: the European Union’s Major Accident Reporting System (eMARS) partnered with an AI analytics firm to review decades of chemical accident reports from EU countries. The AI flagged that operational errors during transfer of chemicals (e.g. tanker to tank transfers) were a disproportionately frequent root cause in different industries, suggesting systemic issues with training or procedures. As a result, EU regulators issued updated recommendations on transfer procedures across the bloc (and this was shared with the UN to inform global practices). On the flip side, successes are also shared: if an AI system in Japan significantly reduces false alarms in oil refineries, those parameters or algorithms can be shared to refineries in other countries through global industry forums. For instance, an arXiv preprint in 2024 detailed a novel deep-learning approach to gas leak prediction that was quickly downloaded and implemented by researchers in multiple nations (indicating how open sharing via AI research can accelerate improvements globally). The COVID-19 pandemic provided a template too – the way genomic AI data was globally shared to track variants has inspired similar sharing for industrial hazards. Big picture: global information sharing through AI means a hazardous materials scare in one place becomes a lesson everywhere. Over time, this should drive down incident rates internationally, as AI uses the planet as its dataset to continually refine what best safety practice looks like.