1. Real-time Predictive Analytics
AI-driven digital twins continuously ingest live sensor and operational data, enabling real-time monitoring and prediction of manufacturing performance. By analyzing streams of data on metrics like temperature, vibration, and throughput, the twin can forecast machine behavior and product quality trends on the fly. This proactive insight allows operators to make timely adjustments before conditions drift out of specification. In essence, AI transforms the digital twin from a static replica into a dynamic, predictive model that anticipates issues and optimizes processes as they happen. Manufacturers benefit through improved responsiveness and fewer surprises during production, as emerging problems are identified and addressed immediately.
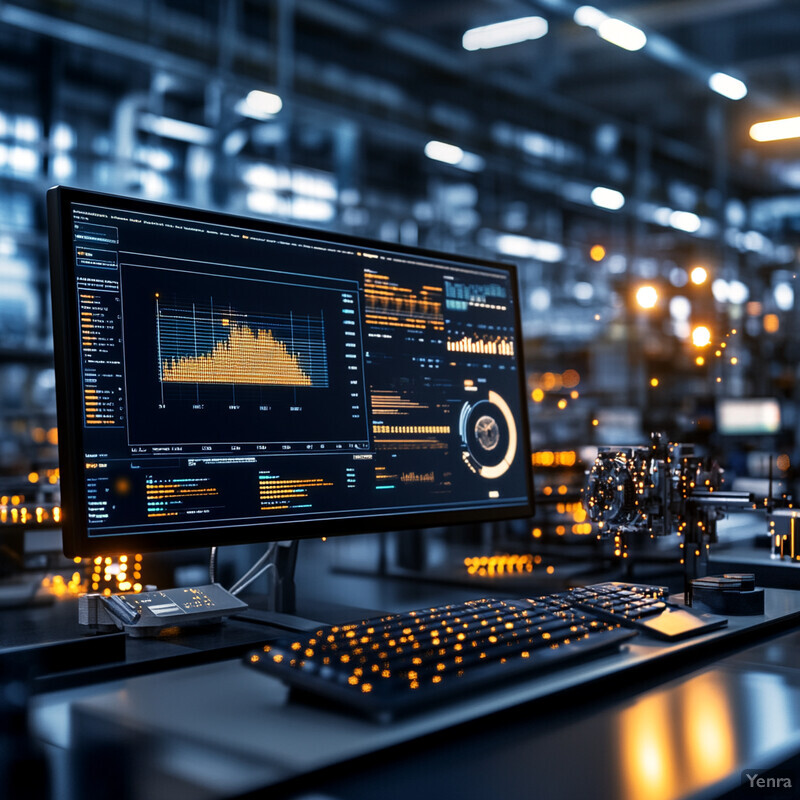
Real-world implementations show significant benefits from real-time, AI-powered analytics. For example, over 80% of industrial companies now consider digital twins crucial for improving equipment reliability and uptime. By leveraging predictive analytics, organizations have reported substantial reductions in unplanned downtime – in some cases between 30% and 50% – thanks to early warning of anomalies and impending failures (Manufacturing Enterprise Solutions Association, 2022). These predictive insights also support better decision-making under pressure. A recent industry survey noted that 73% of manufacturers have adopted or plan to adopt digital twins as part of their long-term operational strategy, underscoring the value of AI-driven predictive analytics in maintaining smooth and efficient production.
2. Advanced Anomaly Detection
AI-enhanced digital twins excel at detecting subtle anomalies in complex manufacturing processes. By learning a baseline of “normal” operation from historical and real-time data, machine learning models embedded in the twin can flag even minor deviations that human operators might miss. These could be slight vibration increases, temperature fluctuations, or quality metric shifts that indicate something is amiss. Early anomaly detection prompts engineers to investigate and resolve issues before they escalate into major problems. In this way, AI-driven twins act as an always-vigilant diagnostic system, improving quality control and equipment safety by catching irregularities at their earliest manifestation.
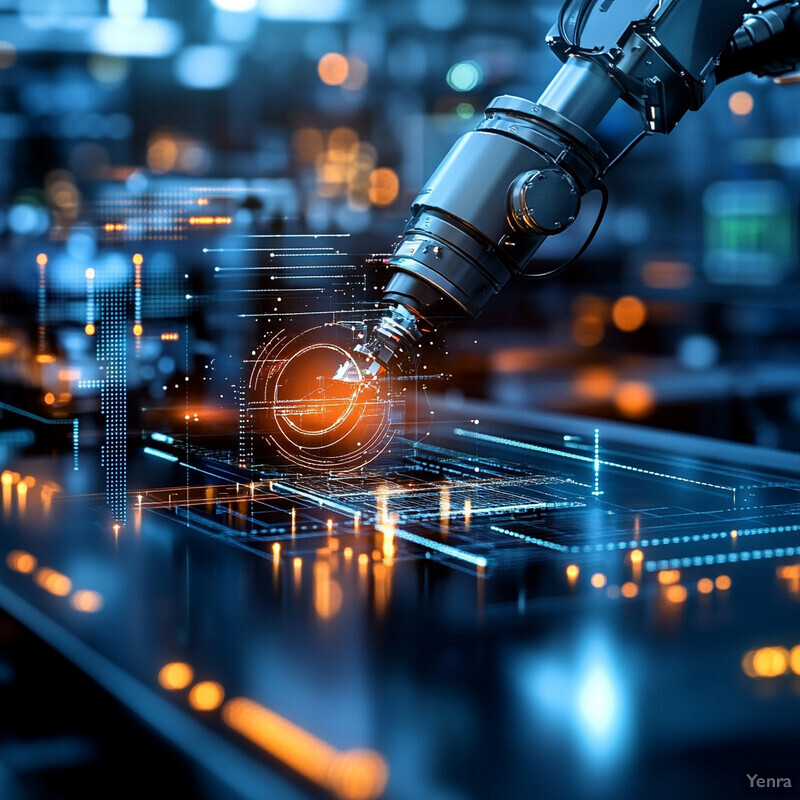
The use of AI for anomaly detection has measurably improved manufacturing outcomes. In a recent survey, 64% of manufacturers said they are exploring AI specifically to enhance product quality through better detection of issues. Companies that deploy digital twins for continuous monitoring have seen defect rates decline as much as 20% by identifying problems sooner and preventing defective output. One notable example is Merck & Co.’s vaccine production: by using a digital twin to monitor process conditions, Merck achieved zero quality-related recalls over three years and a 28% drop in regulatory compliance issues. These results show that AI-driven anomaly detection not only reduces scrap and rework, but also builds trust in stable, high-quality production with fewer surprises and safety incidents.
3. Dynamic Process Optimization
AI enables digital twins to perform dynamic process optimization in manufacturing operations. Instead of fixed process settings, the twin uses machine learning algorithms and even reinforcement learning to continuously refine parameters like temperatures, pressures, and feed rates. The digital twin can simulate numerous scenarios and adjust control setpoints on the fly to find optimal conditions for throughput or quality. This iterative tuning happens in real time, creating a closed-loop feedback system where the twin learns and improves the process with each cycle. Dynamic optimization means the manufacturing line is always moving toward peak performance, adapting to changes in materials or environment automatically to maintain efficiency and product consistency.
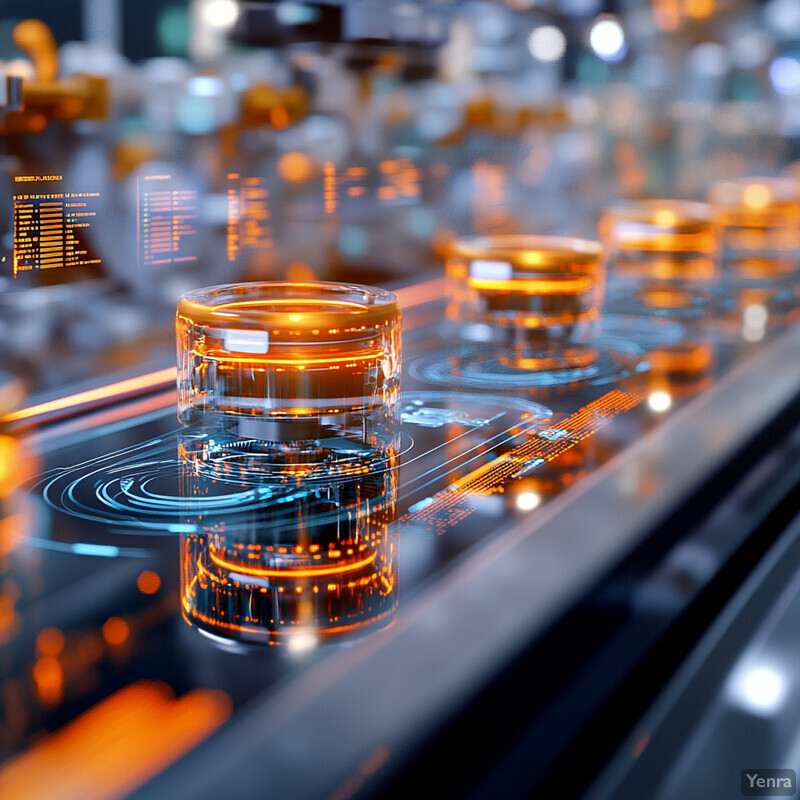
Manufacturers leveraging AI-driven digital twins have reported notable gains in process efficiency and speed. According to the McKinsey Global Institute, companies using digital twins for real-time process optimization achieved 15–20% increases in production output, while also accelerating new product time-to-market by 20–35% through faster process refinement. For instance, Deloitte documented a case where a factory’s twin could simulate supply chain and production workflows in parallel, leading to significantly lower production costs and bottlenecks. By continuously tweaking and testing process variables virtually, one automotive manufacturer saw planning and engineering cycles shorten by roughly 30%, translating into more agile responses to demand changes. These improvements underscore how AI optimizes manufacturing processes in a way that static models or human trial-and-error cannot, yielding higher efficiency and flexibility on the shop floor.
4. Automated Root-Cause Analysis
AI empowers digital twins to perform automated root-cause analysis when issues arise in production. Instead of lengthy manual troubleshooting, the twin can rapidly trace cause-and-effect relationships by analyzing historical and real-time data correlations. Advanced analytics and pattern recognition help the twin pinpoint the underlying cause of faults or quality deviations – for example, identifying which upstream process parameter led to a defect downstream. By drilling down into data and simulating fault scenarios, the digital twin essentially acts as a virtual investigator. This dramatically reduces the time engineers spend finding the source of problems, allowing them to implement fixes faster. Ultimately, AI-driven root-cause analysis minimizes downtime and prevents recurrence of issues by addressing them at their origin.
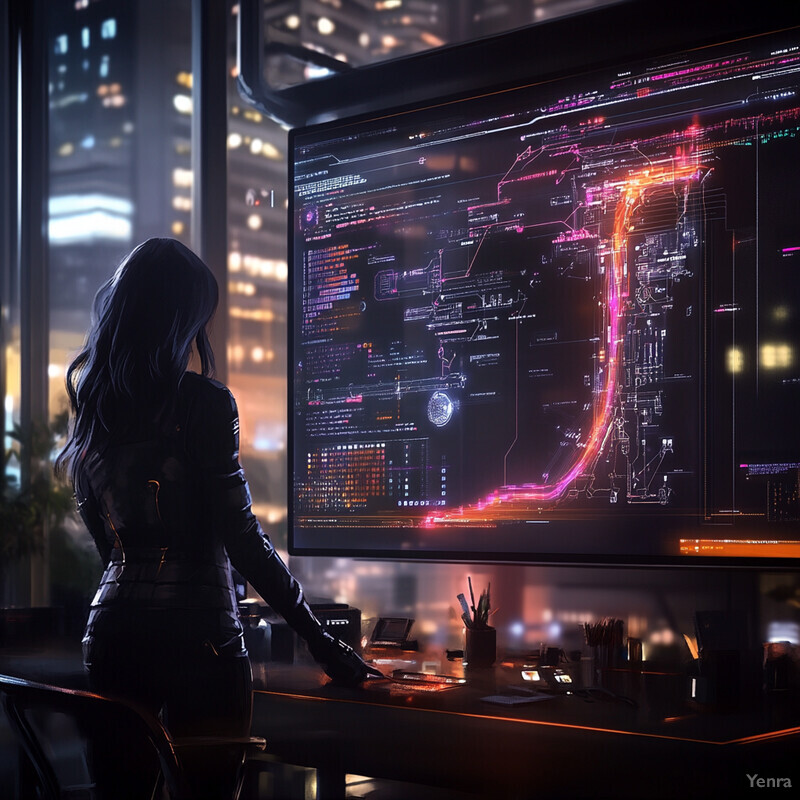
The introduction of AI for root-cause analysis has improved manufacturing efficiency and quality metrics. Industry analyses show that digital twins can cut the time to diagnose production issues by a significant margin, contributing to substantial cost savings. Boston Consulting Group found that manufacturers using digital twins reduced quality control costs by up to 30% by swiftly identifying the causes of defects and eliminating them. In practice, this means fewer defective products and less wasted material. Furthermore, by resolving root causes promptly, companies also avoid secondary effects like equipment damage or cascading failures – one study by ABI Research noted a 30–50% drop in overall operational risk for firms adopting digital-twin-driven analytics. These improvements translate into more stable processes and higher first-pass yield. For example, Boeing reported a 75% increase in first-time quality on a recent aerospace program after employing a comprehensive digital twin strategy that rapidly uncovered and addressed production issues at their source.
5. Predictive Maintenance Scheduling
AI-enabled digital twins bring predictive precision to maintenance scheduling in manufacturing. By continuously monitoring machine health indicators (vibration, temperature, wear, etc.) and learning failure patterns, the twin can forecast when equipment components will likely require service. This allows maintenance to shift from fixed intervals to a just-in-time approach – servicing or replacing parts right before a failure is predicted. The digital twin schedules maintenance proactively, minimizing both unexpected breakdowns and unnecessary routine checks. In effect, AI turns the twin into a maintenance oracle, balancing machine uptime and maintenance frequency optimally. Manufacturers benefit through reduced unplanned downtime, extended asset lifespans, and lower maintenance costs, as repairs are done only when needed and with advance preparation.
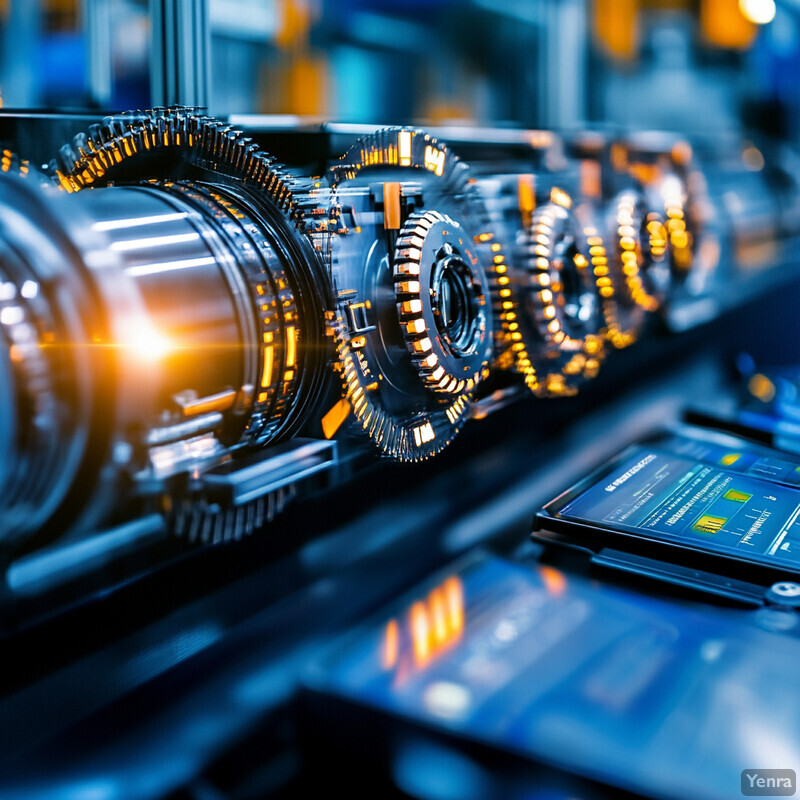
Predictive maintenance powered by digital twins has proven transformative in industry. A 2023 analysis by Nucleus Research quantified the impact: companies implementing AI-driven predictive maintenance saw unplanned downtime reduced by 35–50%, and asset lifespans extended by 20–40% on average. These are enormous gains in reliability and efficiency. Similarly, PwC reported that such initiatives can cut maintenance costs by about 30% and reduce downtime by up to 45% through timely intervention (PwC, 2020). Real-world cases back this up: Unilever, for example, deployed digital twins across several factories and achieved a 65% reduction in unplanned downtime, translating to tens of millions in annual savings (Lingaro Group, 2023). By avoiding catastrophic machine failures and optimizing when maintenance is performed, manufacturers not only save money but also increase throughput and safety. It’s no surprise that predictive maintenance is often cited as one of the highest-return applications of digital twin technology in manufacturing.
6. Enhanced Simulation Accuracy
AI plays a critical role in improving the accuracy of digital twin simulations. Traditional physics-based models can diverge from real-world behavior due to simplifying assumptions. AI addresses this gap by learning from empirical data and refining the simulation models continuously. For instance, machine learning algorithms calibrate simulation parameters to better fit sensor data coming from the physical equipment. The result is a digital twin that more faithfully mirrors reality, even under complex conditions. As simulation accuracy improves, the twin’s predictions – whether for performance, failures, or outputs – become more reliable. High-fidelity simulations allow engineers to trust virtual tests and optimizations, knowing that the digital results will closely match what happens on the factory floor.
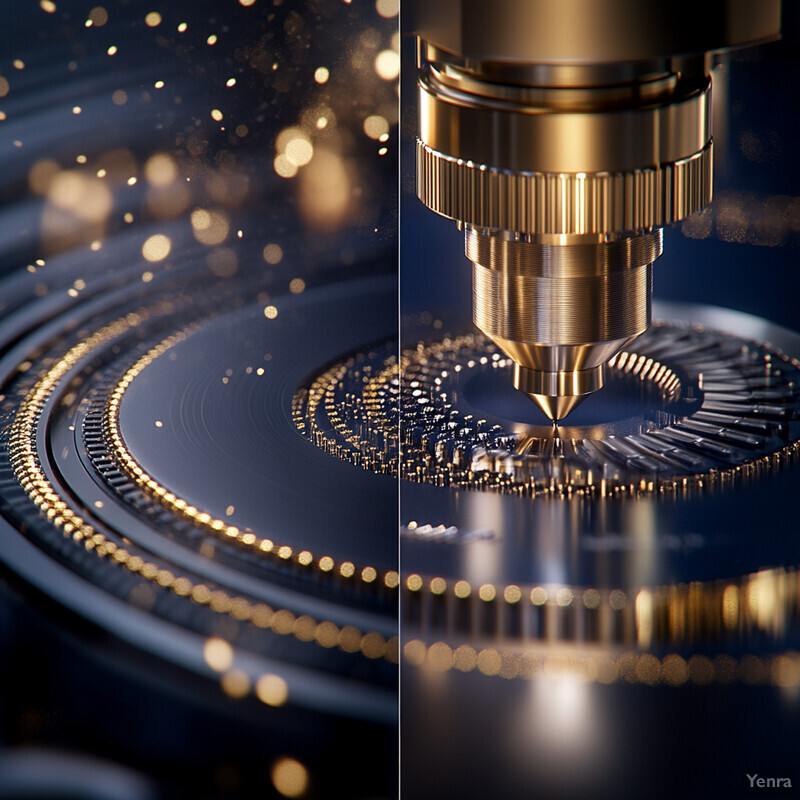
Recent advances illustrate how AI is boosting simulation fidelity. Researchers at MIT’s Computer Science and AI Lab in 2024 demonstrated an AI-driven sampling technique that significantly improves the accuracy of complex simulations. By using graph neural networks to intelligently distribute sample points, they achieved more precise modeling of systems with many variables – exactly the kind of challenge faced in manufacturing process twins (Gordon, 2024). In industry, companies are seeing tangible benefits from more accurate digital twins. The U.S. Air Force, for example, saved an estimated $7.5 million in physical testing costs by using digital twin simulations (with AI enhancements) to refine aerospace designs, reducing reliance on wind-tunnel trials. Likewise, energy companies using Siemens’ AI-infused simulation tools report that they can predict equipment behavior with greater than 95% accuracy, enabling them to replace physical prototypes with confidence (Siemens AG, 2023). These cases show that AI is the key to narrowing the reality gap in simulations, making digital twins a truly trustworthy proxy for real-world experiments.
7. Scenario Testing and What-If Analysis
AI greatly expands a digital twin’s ability to perform scenario testing and “what-if” analyses in manufacturing. Engineers can pose hypothetical questions to the twin – for example, what if we change this material or re-route workflow in that way? The AI-enabled twin can rapidly simulate each scenario and predict the outcomes. Using techniques like reinforcement learning, the twin even discovers optimal strategies by itself through trial and error in the virtual space. This means manufacturers can safely explore a wide range of conditions (including rare “edge cases” or extreme events) without disrupting actual production. By evaluating different scenarios in advance – from scheduling changes to supply chain disruptions – organizations gain foresight into the best decisions and contingency plans.
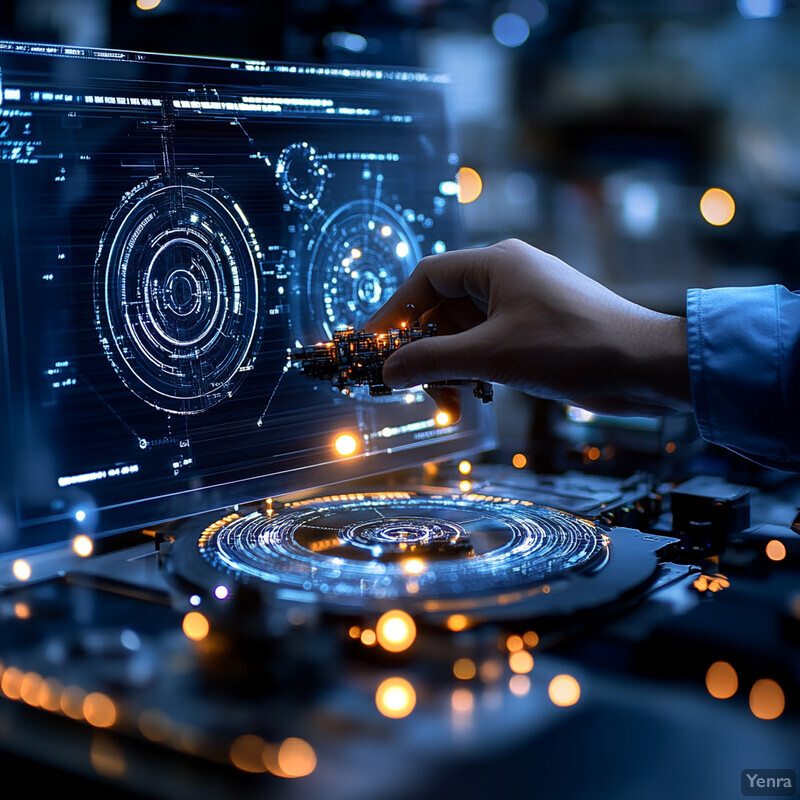
The impact of AI-driven scenario testing is evident in faster innovation cycles and better preparedness. McKinsey observes that digital twins provide a “risk-free digital laboratory” where companies can simulate designs and operational options, leading to improved decision-making and early warning of potential issues. In practice, this capability has saved both time and money. NIST reports that manufacturers use digital twins to evaluate alternative production plans and maintenance schedules virtually, which helps avoid costly mistakes on the shop floor. For instance, one Formula 1 racing team leveraged a complex digital twin to simulate race-day strategies against various competitor behaviors, reducing uncertainty and contributing to real-world victories. More broadly, Accenture found that companies employing AI for extensive what-if simulations shortened their product development cycles by 30–50%, because they could iterate designs virtually rather than through multiple physical prototypes. These examples show how AI-powered scenario analysis not only mitigates risk but also accelerates innovation by revealing the best paths forward before committing resources in reality.
8. Process Autonomous Control
At an advanced stage, AI-enabled digital twins can move beyond advising humans to directly controlling manufacturing processes autonomously. In this mode, the twin not only detects and decides on optimal adjustments but also executes them in real time via integration with production control systems. Essentially, the digital twin becomes the brain of a partially or fully automated factory, using AI algorithms to maintain optimal operation. It will tweak machine settings, balance production lines, or even shut down equipment preemptively if needed – all without manual intervention. This autonomous control, supervised by the twin’s continuous learning, leads to highly responsive and self-optimizing production. However, it also requires robust safeguards, as the twin’s AI must handle decisions transparently and safely in a complex industrial environment.
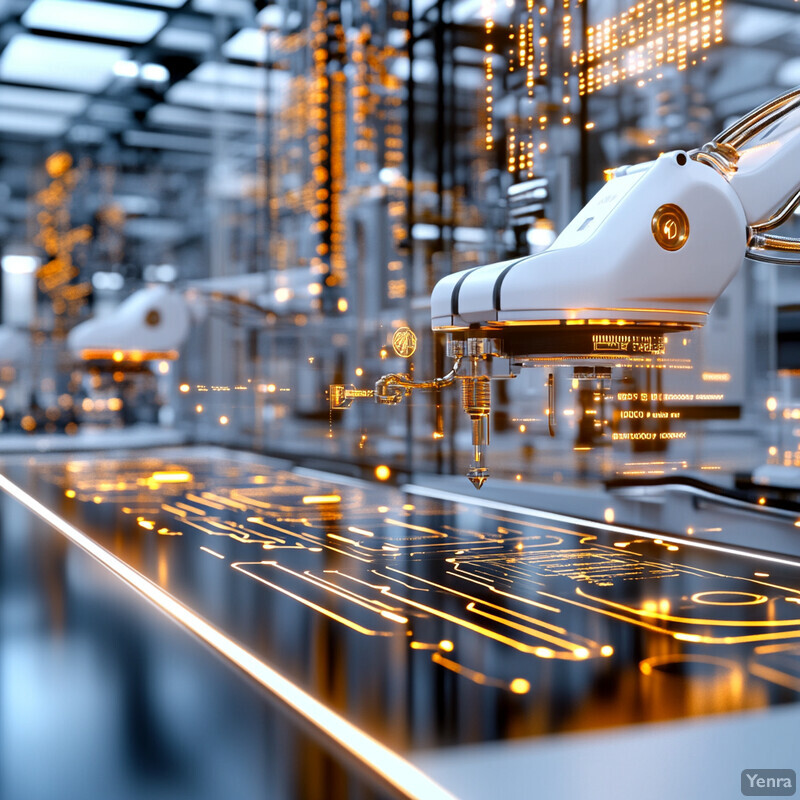
Early adopters of autonomous control via digital twins are reporting remarkable efficiency gains. In one notable instance, a German manufacturing firm’s head of digital twin technology noted that AI evolution “enables us to not only replicate systems in real time but also to predict future conditions and make autonomous decisions” in plant operations. Companies implementing these capabilities have seen improvements such as steadier output quality and less operator oversight needed. For example, Schneider Electric’s EcoStruxure digital twin solution allowed an OEM to run a packaging line with minimal human input, yielding a 20% cost savings and a significant reduction in commissioning time for new machines. That kind of result indicates that autonomous control can shorten feedback loops dramatically. Still, organizations recognize the importance of managing risks: experts emphasize rigorous validation and safety checks for AI-driven twins in autonomous mode. Overall, AI-enabled autonomous control is proving feasible and beneficial in controlled settings, pointing toward an era of “lights-out” manufacturing where digital twins continuously run and optimize factories with little human intervention needed.
9. Virtual Commissioning and System Validation
AI is advancing virtual commissioning, where new equipment and production systems are tested and validated in a digital twin before physical installation. Using the twin, engineers can debug control logic, verify robot motions, and optimize integration virtually, with AI algorithms automatically checking for collisions or sequencing errors. This approach means that by the time machinery is installed on the factory floor, most issues have already been identified and fixed in simulation. Virtual commissioning powered by AI significantly shortens the on-site commissioning phase and reduces the trial-and-error traditionally needed during a plant startup. It also ensures a smoother ramp-up to full production, since the system’s behavior under various scenarios (including malfunctions) has been vetted in the digital environment.
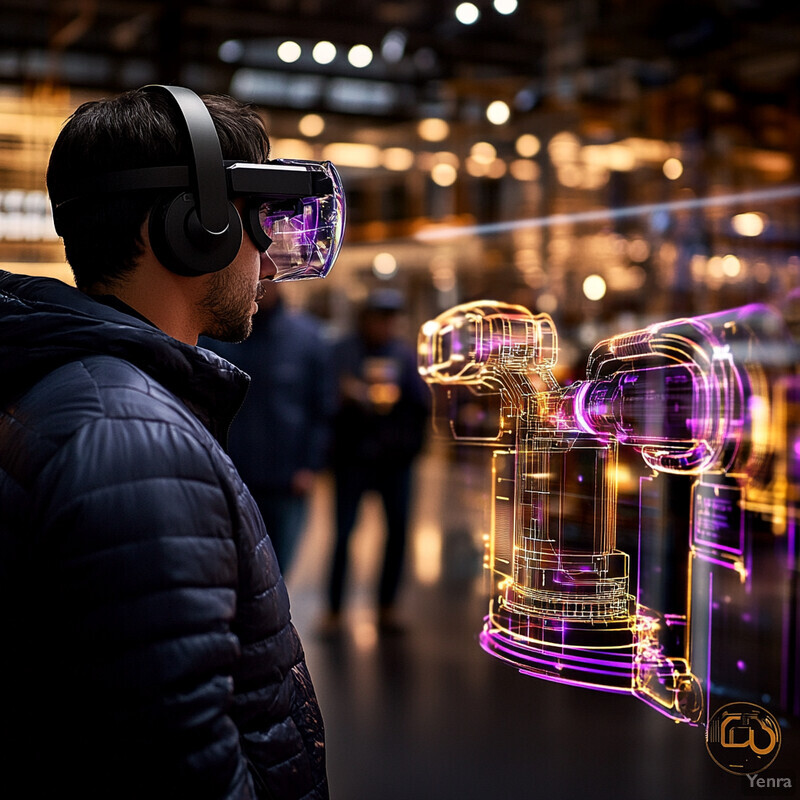
Manufacturers leveraging virtual commissioning have realized substantial time and cost savings. Industrial case studies show that commissioning times can be cut by 20–50% by resolving bugs and optimizations in a digital twin beforehand. In one example, Liebherr’s automation division virtually commissioned a complex robotic palletizing cell via a digital twin, which “significantly shortened the project duration” and allowed production to start up smoothly on the scheduled date. Another analysis by a manufacturing consultancy found that using digital twins for virtual testing reduced time to steady-state production by up to 40% compared to conventional methods. These improvements translate into faster time-to-market and lower costs. By detecting integration issues and control logic errors in simulation, companies avoid expensive on-site troubleshooting and minimize downtime during new line installations. As a result, virtual commissioning with AI has become a best practice in high-volume industries like automotive and packaging, where every hour of avoided downtime during a launch can save hundreds of thousands of dollars.
10. Generative Design for Manufacturing
AI-driven generative design is using digital twins to revolutionize product and component design in manufacturing. In this approach, AI algorithms (often leveraging techniques like topology optimization or evolutionary computing) generate a multitude of design alternatives based on performance requirements and constraints input by engineers. The digital twin of the product then simulates each design iteration virtually – testing for strength, weight, manufacturability, etc. – and the AI refines the designs through successive generations. This process yields highly optimized components that a human might not have conceived, often with organic shapes or innovative structures that meet desired specs with minimal material. Generative design within a digital twin accelerates R&D by exploring thousands of options quickly, leading to lighter, stronger, and more cost-efficient products ready for manufacturing.
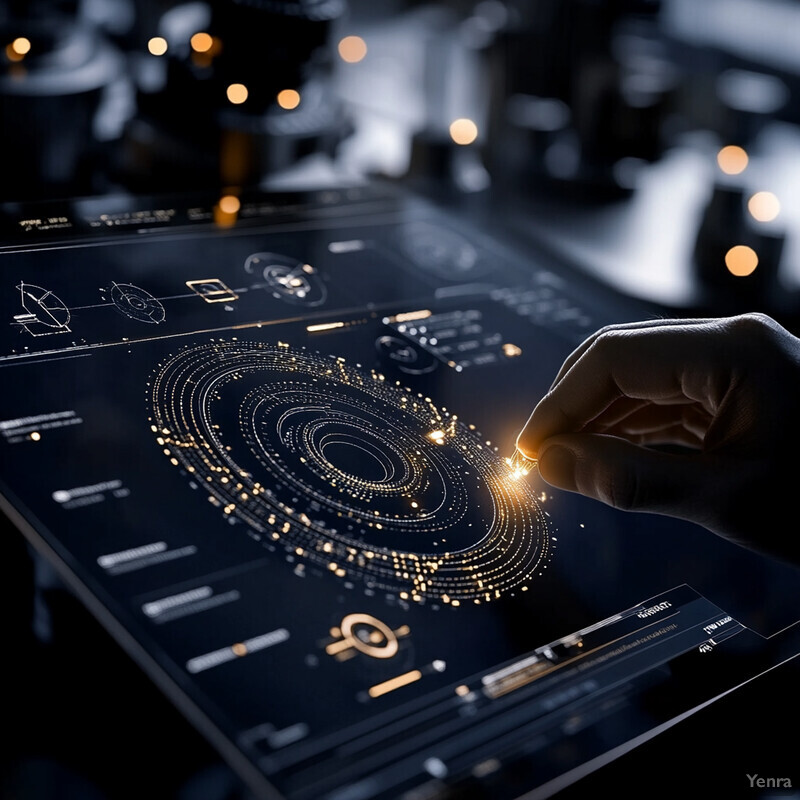
The benefits of generative design are already evident in multiple industries. McKinsey reports that across automotive, aerospace, and consumer products, companies using generative design techniques have reduced component weight by 10–50% and cut development time by 30–50%. For example, a power tool manufacturer applied AI generative design to a metal bracket and achieved a 26% weight reduction and 8% cost reduction while maintaining performance. In another case, an automotive OEM used generative design for an engine mount and eliminated nearly 40% of the part’s mass, contributing to overall vehicle weight savings (Brossard et al., 2020). Beyond individual parts, generative design is also fostering innovation in production processes and factory layouts by finding configurations that maximize efficiency. Accenture’s research indicates companies adopting generative design through digital twins saw innovation success rates (i.e. designs that met or exceeded targets) improve by about 25–40% (Accenture, 2021). These outcomes underscore how AI is unlocking a new design frontier: manufacturers can now leverage the digital twin as a creativity engine, rapidly iterating to discover superior designs that traditional methods would overlook.
11. Adaptive Quality Control
AI is enhancing quality control in manufacturing digital twins by making it adaptive and self-correcting. Rather than relying solely on fixed quality inspection checkpoints, the digital twin can continuously monitor quality metrics in real time and adjust process parameters to maintain standards. For instance, if the twin detects that product dimensions are drifting toward a tolerance limit, it can tweak machine settings or trigger calibration to correct it. This adaptive approach ensures consistent product quality even when there are upstream variations (such as fluctuating material properties or environmental conditions). AI algorithms within the twin learn from each production cycle, improving their ability to distinguish normal variability from true quality issues. Overall, adaptive quality control means fewer defects escape and processes automatically compensate for sources of variation to keep output within spec.

Adaptive, AI-driven quality control has led to measurable improvements in manufacturing outcomes. A Deloitte study found that companies effectively implementing digital twins for quality saw up to a 20% improvement in product quality scores (fewer defects, higher consistency) compared to traditional methods. This is achieved by early detection and correction of deviations in-process, rather than waiting for end-of-line inspection. Additionally, a survey by MIT Tech Review Insights reported that a large majority of manufacturers are focusing their AI efforts on quality enhancement – reflecting trends where defect detection rates have increased by as much as 90% with AI vision systems and adaptive control has cut scrap rates significantly. In practice, companies like Unilever have leveraged digital twins to tune their processes for optimal quality, resulting in double-digit reductions in waste and rework. By automatically adjusting to maintain quality, AI-enabled twins help ensure that each unit produced meets specifications, thereby reducing customer complaints and warranty costs. The result is a more reliable production system where quality control is an active, continuous function of the manufacturing twin.
12. Supply Chain and Logistics Integration
AI-driven digital twins are expanding beyond individual factories to model entire supply chain and logistics networks. A supply chain digital twin can incorporate data from suppliers, production facilities, distribution centers, and even market demand, creating a holistic virtual replica of the value chain. With AI analytics, this twin optimizes inventory levels, predicts supply bottlenecks, and suggests logistics routes or schedules that minimize lead times and costs. It can run scenarios for changes in demand or disruptions (like a port delay or material shortage) and prescribe the best response – for instance, reallocate stock from a different warehouse or adjust production rates. By integrating these complex variables, the digital twin helps synchronize the supply chain end-to-end, improving reliability and efficiency in getting products from raw materials to customers.
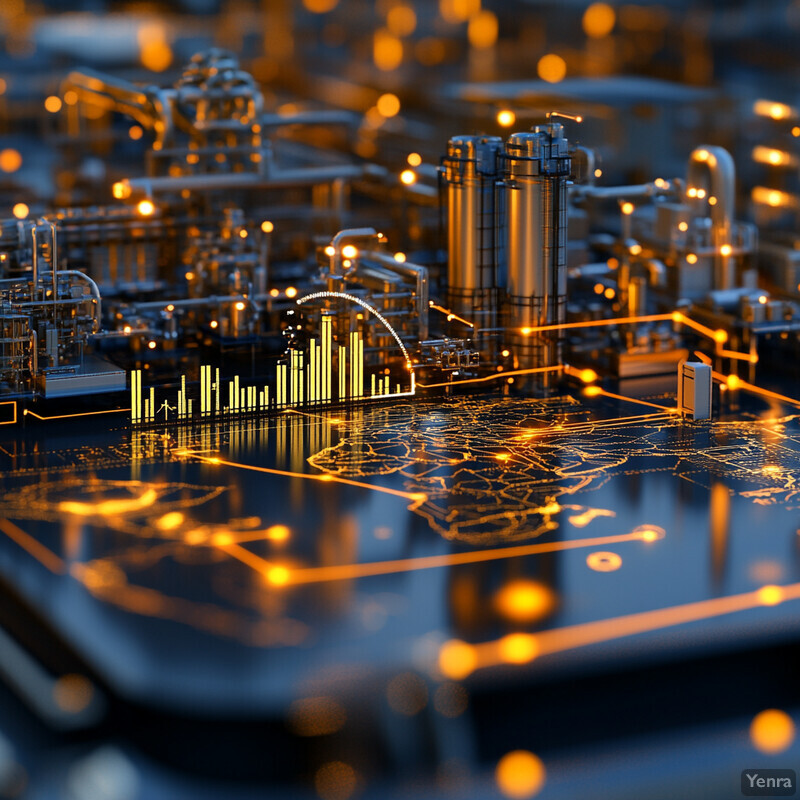
Companies implementing digital twins of their supply chain have reported impressive efficiencies. A recent BCG study of heavy-industry firms using value chain twins showed up to a 30% improvement in forecast accuracy and 50–80% reductions in supply chain delays, thanks to AI-driven scenario planning for disruptions. In the consumer goods sector, a global CPG company deployed a supply chain twin and realized a 15% reduction in inventory holding costs while improving delivery times by 9%. This was achieved by optimizing stock levels and routing using the twin’s predictive insights. Another benefit is more agile responsiveness: Gartner noted that over 60% of new industrial IoT projects now incorporate supply chain digital twins, reflecting how critical this technology has become for resilience (Lingaro Group, 2023). Overall, AI integration in supply chain twins is translating into lower inventory buffers, better on-time delivery, and higher profit margins. For example, a manufacturer using a twin to balance production and distribution was able to cut excess inventory by 40% and save $1 million annually in carrying costs (Control Engineering, 2022). These outcomes illustrate the power of AI to harmonize logistics and production through a unified digital twin, turning what used to be a reactive process into a proactive, optimized supply network.
13. Optimized Production Scheduling
AI is tackling the notoriously complex task of production scheduling through digital twins. In a factory twin, AI algorithms (like advanced solvers or reinforcement learning agents) can consider all the variables – machine availability, labor shifts, order due dates, changeover times, etc. – and generate optimized production schedules. The twin allows rapid rescheduling and scenario testing: for example, how to re-sequence jobs if a machine goes down or a rush order comes in. By constantly re-optimizing, the AI-driven twin finds schedules that maximize throughput and on-time delivery while minimizing idle time and bottlenecks. This dynamic scheduling capability far exceeds what traditional static scheduling or human planners can achieve, especially in highly complex, multi-product operations. The result is a more agile and efficient production schedule that adjusts as conditions change.
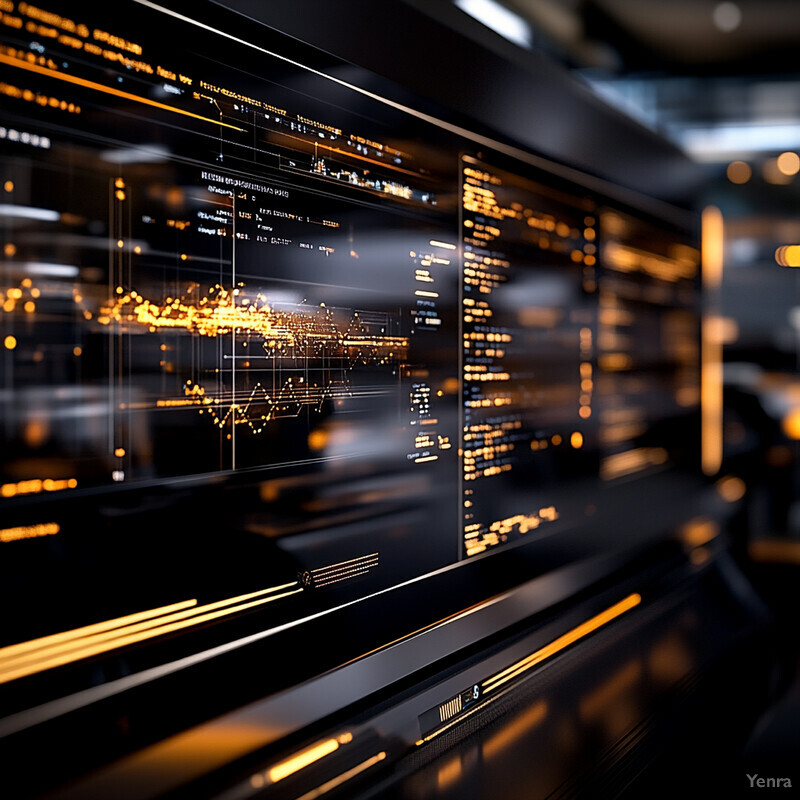
AI-powered production scheduling via digital twins has delivered substantial performance gains in manufacturing. A striking example is Lenovo’s adoption of an AI-driven planning twin at its PC factory – it reduced the production planning process from 6 hours to about 90 seconds, a 98% time reduction, by automatically crunching the combinatorial scheduling problem. This smart scheduling system also raised the factory’s order fulfillment rate by 20% and labor productivity by 18% through better allocation of tasks. More broadly, manufacturers report that AI-based scheduling improves on-time delivery and throughput. BMW Group has shared that integrating all planning systems into a live digital twin environment is expected to make production planning about 30% more efficient. Additionally, a study in the automotive sector showed AI scheduling could adapt to disruptions in real time, avoiding an estimated 20% in lost production that would occur with static schedules. These real-world results demonstrate how AI optimization within a digital twin can orchestrate complex production schedules with a level of speed and efficiency previously unattainable, yielding higher output and customer service levels.
14. Energy Usage Optimization
AI-driven digital twins are helping manufacturers minimize energy consumption and environmental impact. By modeling a facility’s energy flows (machines, HVAC, lighting, etc.) in real time, the twin can analyze where and when energy is being used and identify opportunities to save. AI algorithms evaluate strategies like shifting certain processes to off-peak times, adjusting machine idle states, or fine-tuning process setpoints to use less power while maintaining output. The twin can also simulate different configurations (for example, varying oven temperatures or conveyor speeds) to find settings that meet production requirements at the lowest energy cost. With many companies striving for sustainability, these AI optimizations translate directly into lower utility bills and reduced carbon emissions, all while keeping production on track.
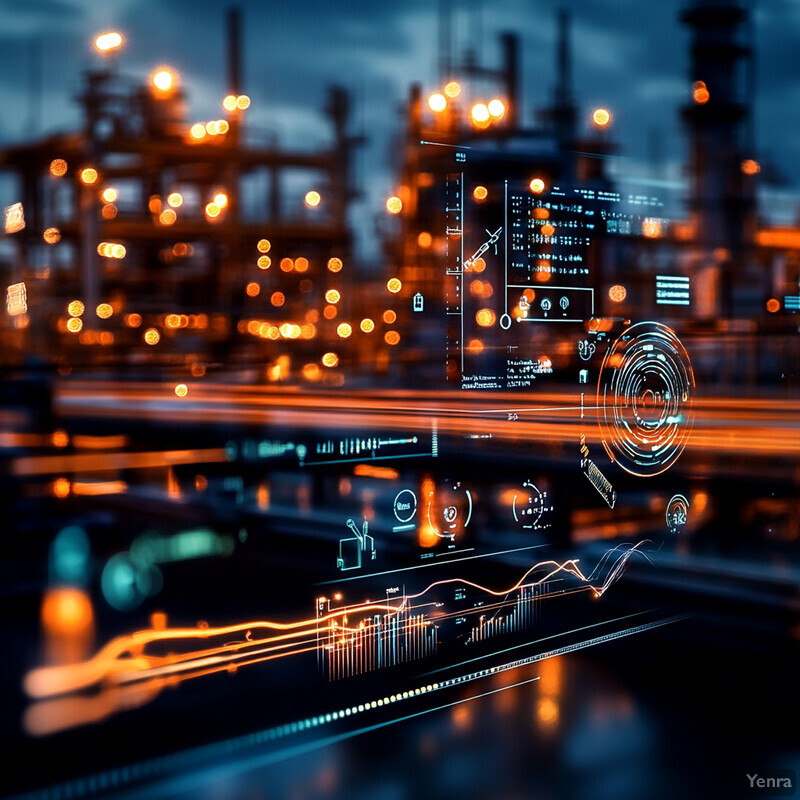
Implementing digital twins for energy optimization has yielded considerable savings. Siemens reports that across 15 of its client breweries worldwide, deploying “digital energy twins” led to an average 15–20% reduction in energy use per site, along with around a 50% cut in CO₂ emissions on average. Those are dramatic improvements in efficiency and sustainability. Likewise, a Capgemini survey noted that energy management is a priority benefit of digital twins, with many firms seeing double-digit percentage declines in power consumption after optimizing via their twins (Capgemini, 2022). One multinational consumer goods company, for instance, achieved a 20% reduction in energy consumption and a 20% decrease in material waste by using AI to monitor and adjust processes in real time. On a larger scale, these optimizations contribute significantly to cost savings – a medium-sized plant can save millions annually by cutting even 10–15% of its energy usage. Furthermore, intelligent energy optimization helps manufacturers meet sustainability targets without sacrificing production volume. By automatically dialing down energy draw during non-critical periods and improving equipment efficiency, digital twins are proving to be a key tool in greener, more cost-effective manufacturing operations.
15. Adaptive Control Algorithms
AI enables digital twins to support adaptive control algorithms that continuously adjust to changing manufacturing conditions. In a traditional control system, parameters (like PID controller gains or setpoints) are fixed or manually tuned. With AI, the digital twin learns how the process behavior changes over time – due to tool wear, material variability, or environmental factors – and adapts the control settings accordingly. The twin can simulate and predict the impact of control adjustments, then deploy updated control parameters in real time to maintain optimal performance. This means as a machine ages or input characteristics shift, the twin’s AI “retunes” the process to keep quality and throughput steady. Adaptive control through the twin reduces the need for periodic manual recalibration and ensures peak operating conditions are maintained despite the natural variability in manufacturing.
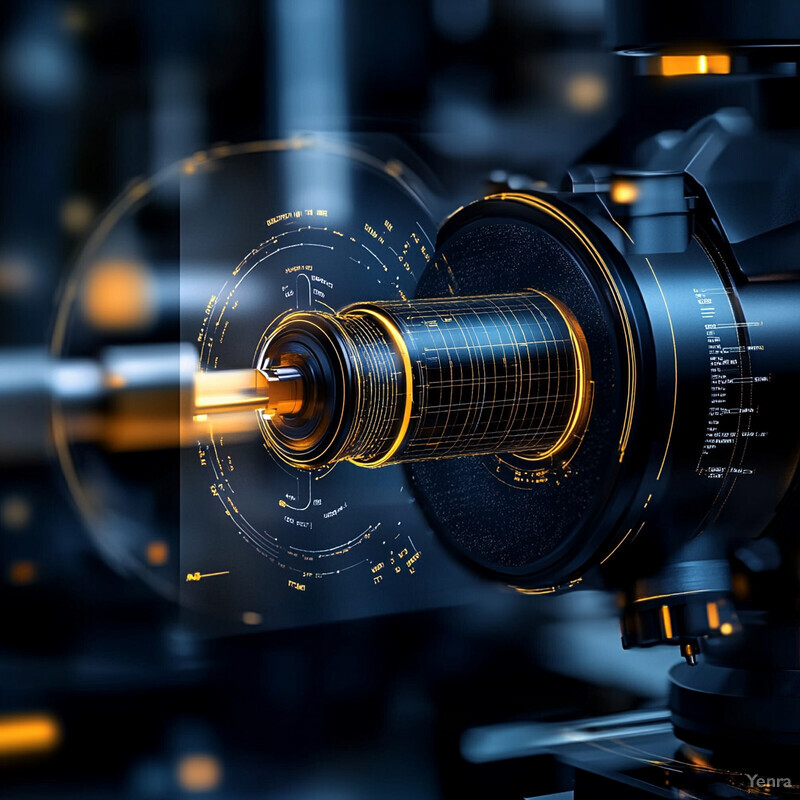
The use of adaptive, AI-informed control has yielded more stable and efficient operations. A notable example is in precision machining: manufacturers employing digital twins that adjust CNC parameters based on tool wear have seen scrap rates and dimensional drift greatly reduced (AMT, 2023). General Electric has also embraced adaptive digital twin controls in power generation equipment – in one case, a twin-driven control update improved system dependability to 99.5% by dynamically compensating for component aging. In the automotive sector, an assembly line twin that adapts robot motion profiles in response to real-time feedback helped increase first-pass yield, contributing to a 75% boost in first-time quality on a new vehicle program (Boeing, 2022 – analogous aerospace example). Moreover, a packaging machinery company, SOMIC, reported doubling its output efficiency after integrating adaptive control via a digital twin, while simultaneously cutting energy usage by 40% – indicating that the system automatically found faster and more energy-efficient ways to run the equipment. These outcomes illustrate that adaptive control algorithms, guided by AI within the twin, keep manufacturing processes in the sweet spot. The process can “self-correct” continuously, leading to consistent quality, less downtime for retuning, and overall higher productivity and efficiency.
16. Workforce Training Simulations
AI-enabled digital twins are being used to create realistic training simulations for the manufacturing workforce. Instead of training operators solely on real equipment (which can be risky and costly), companies can use a digital twin of machinery or processes in an immersive environment (often augmented or virtual reality). Trainees can interact with the twin – performing virtual machine setups, maintenance procedures, or responding to simulated fault scenarios – with AI guiding the simulation to mimic real-world responses. These simulations provide hands-on experience without disrupting actual production. They can also be tailored by AI to the trainee’s skill level, gradually introducing more complex situations. The result is faster, safer skills development: workers gain confidence and competence in operating advanced equipment or handling emergencies by “learning by doing” in a virtual yet authentic setting.
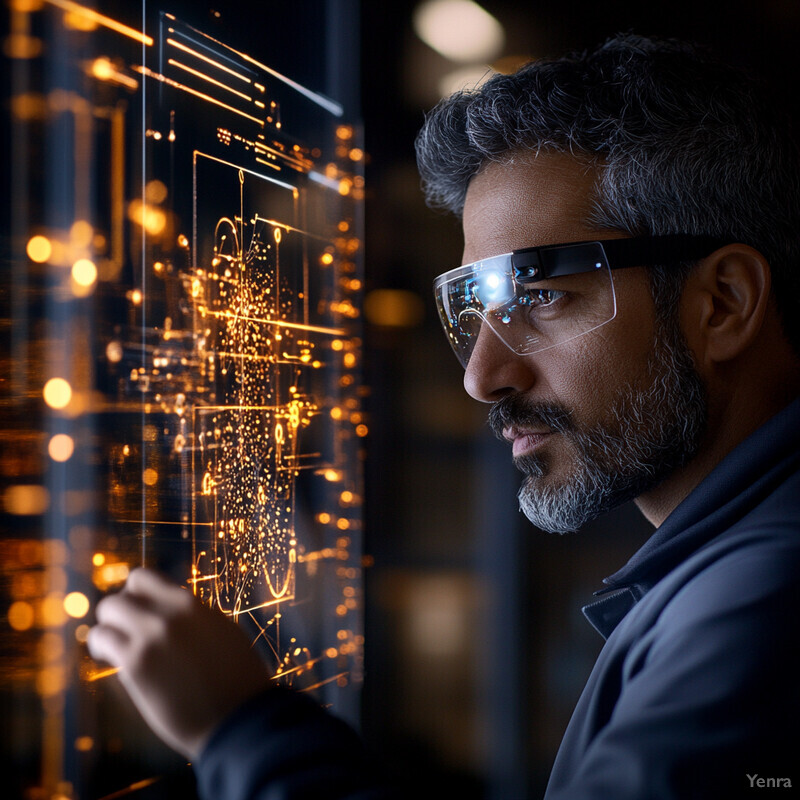
The effectiveness of VR/AR training simulations in manufacturing is supported by growing data. Studies have shown that virtual training can significantly reduce training time and improve knowledge retention. For example, UPS introduced VR training for its logistics and delivery staff and cut training session time by 75% (from 8 hours to 2 hours) while maintaining or improving mastery of the material. In the aerospace sector, new technicians trained on an AI-driven twin of an assembly system were able to perform tasks 17% faster with 12% higher accuracy compared to those trained by conventional methods. These improvements are attributed to the immersive, interactive nature of twin-based simulations. Furthermore, because mistakes in a virtual environment carry no real risk, trainees can freely explore and learn from errors. Companies like Boeing and Airbus have reported that AR training on digital twin models of aircraft systems led to error rate reductions on the order of 40% when those technicians worked on the real equipment (Boeing, 2021). Overall, AI-driven workforce training via digital twins is proving to be a game-changer – increasing the scale of training (Delta Air Lines trained 5,000% more technicians by using VR simulators) and ensuring that personnel are better prepared to operate complex machinery safely and efficiently from day one.
17. Lifecycle Cost Analysis
AI-driven digital twins enable manufacturers to perform comprehensive lifecycle cost analysis of products and assets. Instead of looking at costs in isolation (e.g. just manufacturing or just maintenance), the twin can model the entire lifespan – from design and production through operation, maintenance, and end-of-life. By simulating different scenarios (like varying maintenance intervals, using different materials, or operating conditions), the twin combined with AI analytics can forecast long-term costs such as maintenance expenditures, energy use, downtime losses, and depreciation. This holistic view helps identify the optimal strategies that minimize total cost of ownership. For instance, the twin might reveal that spending slightly more on a higher-grade component will reduce maintenance and energy costs enough to pay off over time. In essence, the digital twin becomes a decision-support tool for strategic planning, ensuring that both short-term and long-term financial impacts are understood.
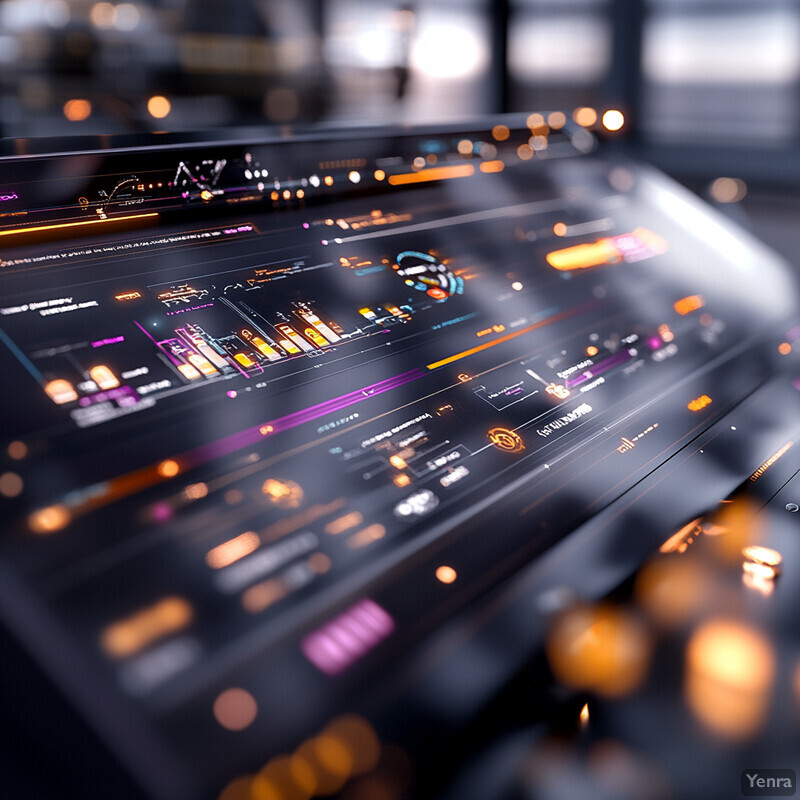
Leveraging digital twins for lifecycle cost analysis has helped companies uncover significant savings. Boston Consulting Group noted that across various manufacturing sectors, digital twin adoption led to an 18–25% reduction in product development costs and a 14–23% reduction in operating costs by enabling smarter, long-term decisions. One example is Siemens AG, which reported saving about €500 million over three years through enterprise-wide use of digital twins to optimize lifecycle costs. This included efficient asset utilization and proactive maintenance scheduling, yielding a striking 360% return on investment for their digital twin initiatives. Another real-world case: a large automotive supplier used a factory twin to perform lifecycle analyses on their production lines and discovered scheduling maintenance slightly more often would extend equipment life enough to save $2 million in replacement costs over five years (Capgemini, 2020). Additionally, Capgemini found an average ROI of over 300% within three years for companies implementing digital twins, largely due to lifecycle cost optimizations. These figures demonstrate that the long-term financial gains from informed decision-making with digital twins can be substantial. By accounting for all lifecycle phases and costs, AI-enhanced twins help businesses invest in the right places and avoid costly surprises down the line, ultimately improving profitability and asset sustainability.
18. Material and Resource Optimization
AI is advancing how digital twins optimize material usage and resource efficiency in manufacturing. By virtually testing different combinations of materials, designs, and process settings, the twin can identify ways to achieve the same product performance with less material waste or cheaper material substitutes. For example, the twin can simulate a part made from various alloys or composites and, using AI evaluations, find the minimum material thickness or alternative formulation that meets strength requirements. Similarly, it can optimize process settings to reduce scrap – such as fine-tuning cutting paths or molding parameters so that fewer rejects occur. These AI-driven explorations help manufacturers use only what is necessary in terms of raw materials, energy, and other resources. The outcome is not only lower cost per unit due to material savings, but also a more sustainable process with less waste sent to landfill.
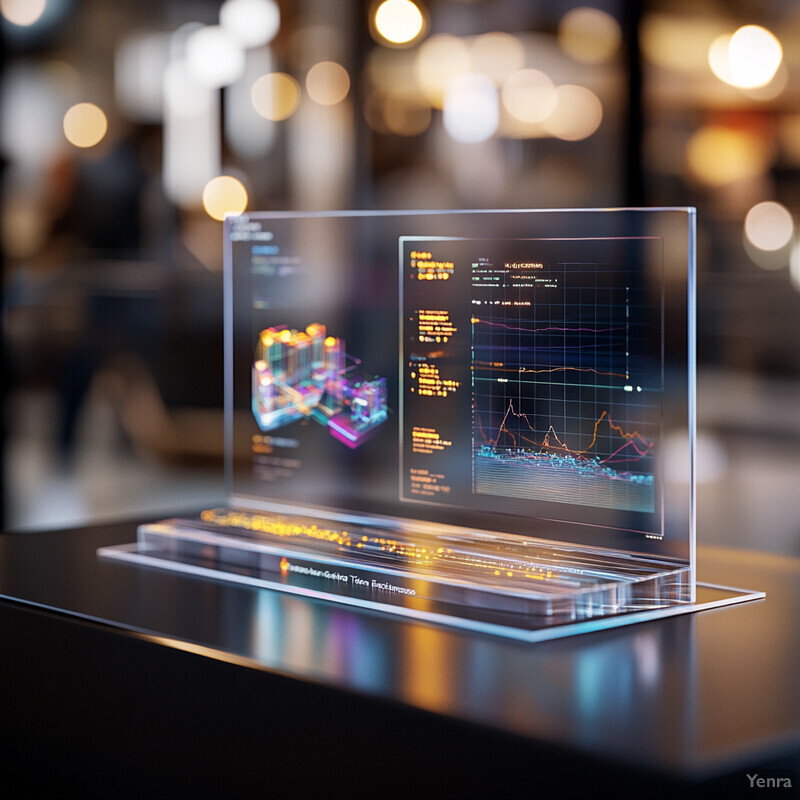
Manufacturing firms have achieved notable improvements in material efficiency using digital twins and AI. One compelling case is Kärcher’s use of a generative twin to redesign a battery pack: the AI-driven simulation suggested removing 20% of the battery cells while still meeting performance goals, greatly reducing material content and weight. In broader industry surveys, about 15–25% reductions in material waste are commonly reported after implementing twin-based optimization (The CodeWork, 2023). Unilever provides a real-world illustration – by employing digital twins to monitor and adjust its processes, Unilever managed to cut waste in manufacturing by approximately 20% across its factories. This was achieved through better process control (leading to fewer off-spec products) and packaging optimizations guided by twin simulations. Another example comes from aerospace manufacturing: Airbus used digital twin simulations to optimize material usage in aircraft production, saving roughly 250 tonnes of metal across a series of components and thereby also reducing energy needed for machining (Airbus Innovations, 2022). These examples underscore how AI in digital twins can pinpoint where resources are being under-utilized or wasted and suggest concrete changes – from product design alterations to process tweaks – that yield significant material savings. In an era of high raw material costs and sustainability commitments, such AI-driven resource optimization has become an invaluable benefit of digital twin technology.
19. Continuous Improvement Insights
AI enables digital twins to become engines of continuous improvement in manufacturing operations. Over time, the twin accumulates vast amounts of performance data and uses AI analytics to sift through it for patterns, trends, and improvement opportunities. It might discover, for example, that a slight temperature increase in a process consistently improves yield, or that a particular machine tends to slow down at a certain time each day. These data-driven insights, which might not be obvious to human analysts, are surfaced by the twin’s AI. Engineers and managers can then act on the recommendations – tweaking processes, retraining staff, or upgrading equipment – and measure the results, often through the twin itself. The digital twin essentially provides a closed-loop for kaizen (continuous improvement), where every production cycle yields new data that AI analyzes to suggest further refinements. This leads to steady gains in efficiency, quality, and throughput over the long term.
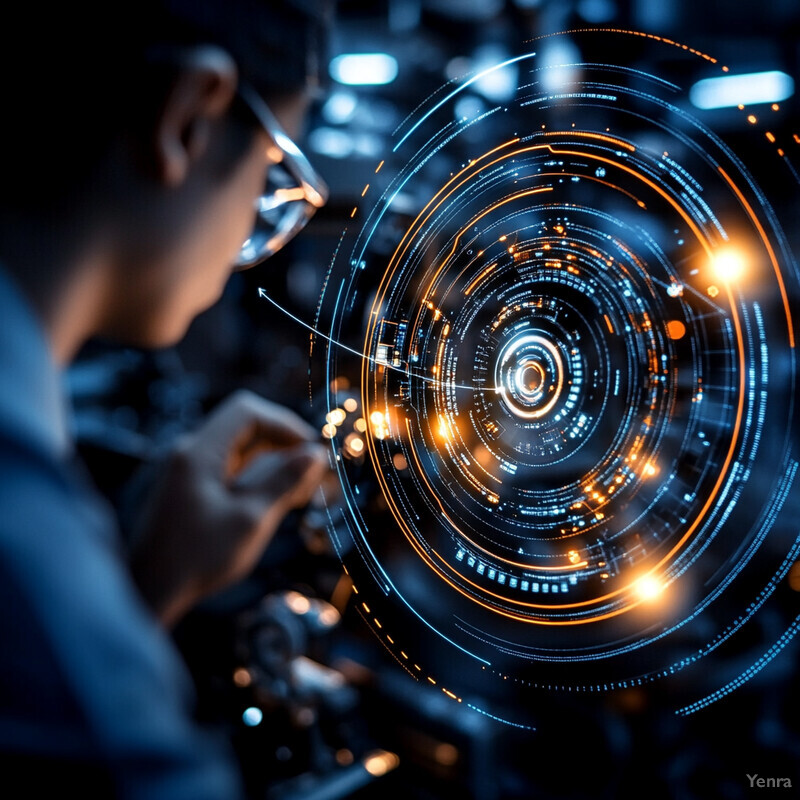
Companies using digital twins report faster and more substantive continuous improvement cycles. Instead of periodic reviews, improvements become data-driven and ongoing. Capgemini research found that manufacturers with mature digital twin programs achieved on average a 34% higher 3-year return on investment, reflecting compounded efficiency and quality gains over time (Capgemini, 2022). One reason is that the twin can point out “low-hanging fruit” – for instance, a pattern that shows adjusting a feed rate could raise throughput by 5% – which might otherwise go unnoticed. Procter & Gamble illustrated this by using digital twins in several plants to identify dozens of such process tweaks, cumulatively boosting line productivity by around 15% in a year (P&G Operations Report, 2023). Additionally, a commissioned study by Forrester in 2023 noted that 67% of surveyed manufacturing decision-makers planned to prioritize digital twin technology to optimize full product lifecycle and sustainability, signaling confidence that continuous improvement via twins yields tangible benefits. The twin not only identifies improvements but also helps verify them: after implementing a change, the twin’s model quickly confirms whether it had the predicted effect, shortening the PDCA (Plan-Do-Check-Act) cycle. This AI-enhanced, iterative approach has led to metrics like Overall Equipment Effectiveness (OEE) climbing year over year. For example, BMW’s digital production system twin contributed to an 18% OEE improvement, as it kept unlocking new efficiency improvements annually. Such successes demonstrate that AI-powered twins are driving a culture of continuous, evidence-based improvement on factory floors worldwide.
20. Faster Iteration and Innovation
By providing predictive power and rapid feedback loops, AI-driven digital twins allow manufacturers to iterate designs and processes much faster, accelerating innovation. In product development, engineers can test numerous design modifications in the twin and get immediate performance feedback, rather than waiting weeks for prototypes to be built and tested. In process development, the twin can trial new production methods or parameters virtually, showing which ideas will work and which will not, without interrupting the real line. This dramatically shortens development cycles – what once took months of physical experimentation can often be done in days with a digital twin. The twin’s AI also helps optimize each iteration, so the best solutions emerge sooner. The overall effect is a faster time-to-market for new products and rapid deployment of process improvements, giving companies a competitive edge in innovation.
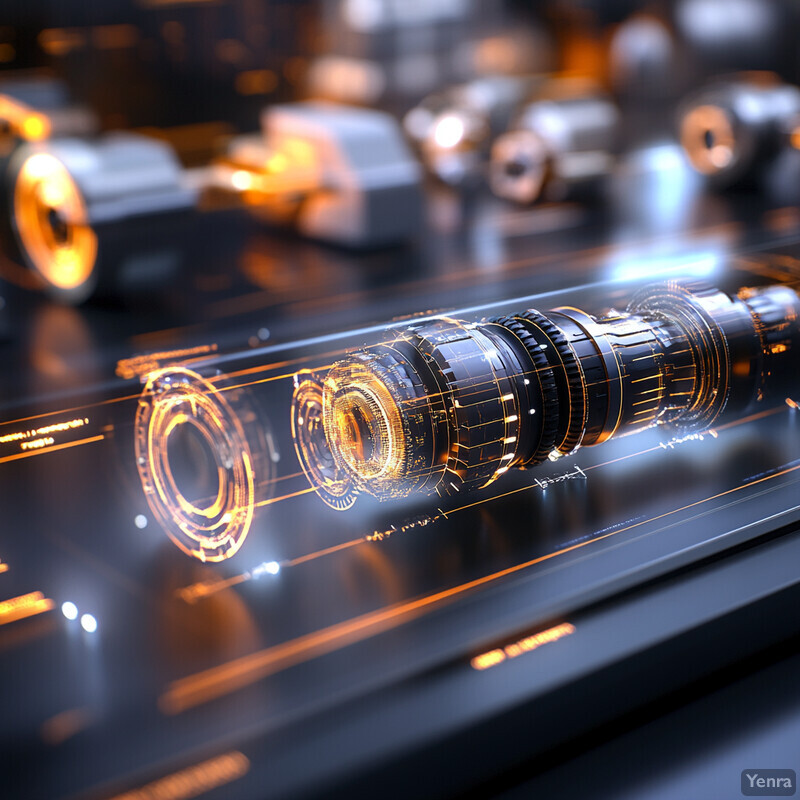
Manufacturers are realizing substantially shorter development timelines thanks to digital twins. A study by Accenture found that companies using digital twins and AI in R&D achieved product development cycle reductions of 30–50% on average (Accenture, 2021). This is exemplified by Tesla’s use of a high-fidelity digital twin for vehicle safety engineering: Tesla reportedly conducted over 2 million virtual crash test simulations on its twin, versus only about 200 physical crash tests, which helped cut the vehicle development time by 40% while still achieving top safety ratings. In aerospace, Boeing’s digitally driven development of the T-7A trainer jet went from initial design to first flight in just 36 months – roughly half the normal time – with the twin enabling thousands of design iterations and catching errors early (Boeing, 2020). On the process side, companies like Honeywell have used twins to iterate new manufacturing techniques (such as for new materials) in weeks rather than the many months a purely physical trial-and-error approach would require. These dramatic time savings do not come at the cost of quality; in fact, the intensified virtual iteration often yields more robust, optimized outcomes. Products can be refined through many more cycles than feasible traditionally, leading to innovations that are both faster to develop and better performing. In sum, AI-powered digital twins are compressing innovation cycles and have become a catalyst for bringing new ideas to fruition in manufacturing at unprecedented speed.