1. Autonomous Drone-Based Inspections
Autonomous drone inspections employ onboard AI to independently plan and execute flight paths over infrastructure. These systems use sensors and computer vision to navigate and capture detailed imagery without a human pilot. The result is faster coverage of large or complex structures and consistent data collection. By automating routine surveys, drones reduce human exposure to hazardous environments. Over repeated flights, AI can learn optimal routes, further increasing efficiency. Overall, autonomous drones significantly speed up inspections and improve safety by keeping personnel out of dangerous or hard-to-reach areas.
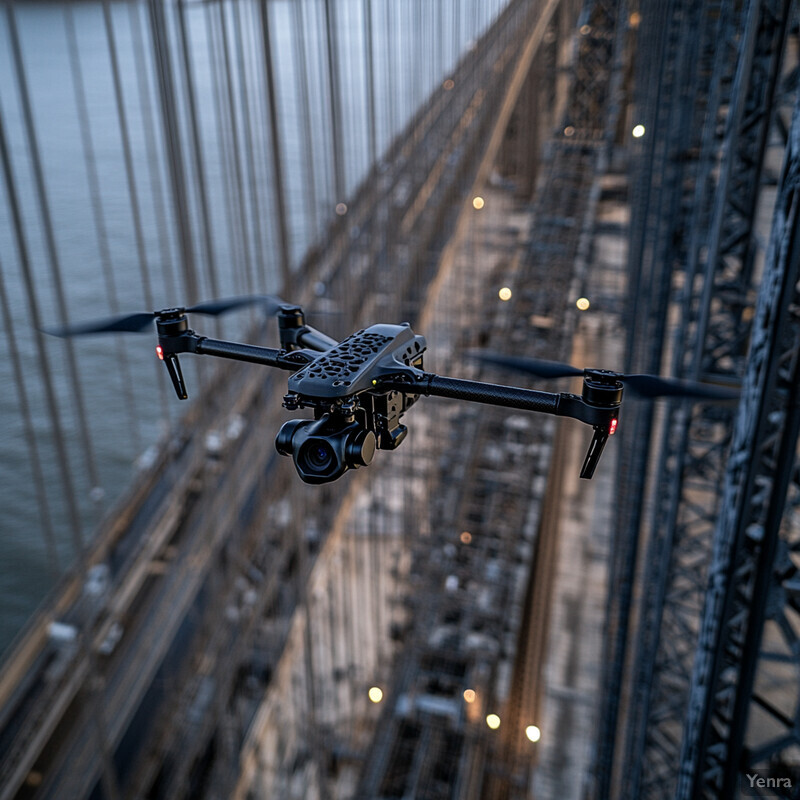
Recent studies and industry reports confirm that drone inspections can dramatically boost safety and efficiency. For example, a market report notes that drones offer “faster, safer, and more cost-effective alternatives” to manual methods. In one analysis, the global drone inspection market was valued at $16.4 billion in 2024 (with rapid growth expected) due to these efficiency gains. Peer-reviewed research similarly highlights the benefits: one review of bridge inspections found drones provide “enhanced safety, efficiency, and cost-effectiveness” compared to traditional approaches. AI-driven navigation enables drones to avoid obstacles and operate in complex environments without pilots, reducing accident risk. In practice, utilities report that drones reduce inspection durations from weeks to days while drastically lowering safety incidents. The consistent, repeatable data from these UAVs also supports earlier detection of wear and damage.
2. Computer Vision for Defect Detection
Computer vision and deep learning analyze inspection imagery to spot defects like cracks, corrosion, and structural anomalies. Trained on vast image datasets, these AI models can identify subtle or early-stage damage that may be missed by human eyes. They apply consistent criteria across inspections, eliminating human bias or fatigue. By automating defect recognition, computer vision accelerates the review process and flags problem areas for engineers. Over time, the models improve and adapt to different inspection conditions. The result is more reliable, frequent defect detection and data-driven maintenance decision-making.
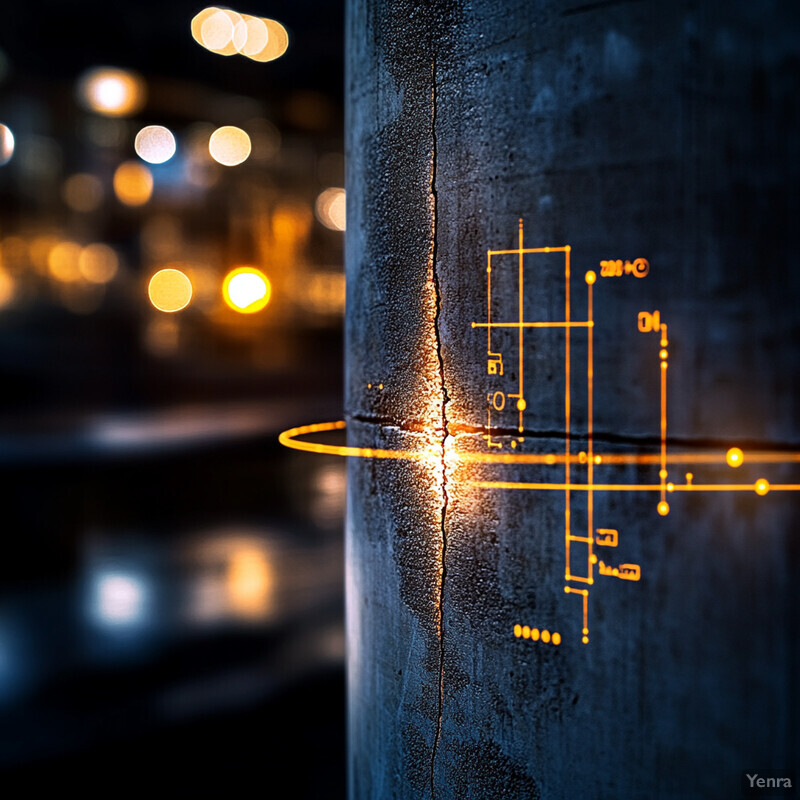
Research demonstrates the power of AI vision in structural inspection. For instance, one study implemented a CNN-based system on a robotic arm that “pinpoint[ed] problem areas of cracking” in concrete structures. In laboratory tests, this system identified minute crack patterns and then directed laser scans to create detailed digital models of damage. The neural network was trained on sample crack images and could “identify crack-like patterns” in new inspection photos. Reviews of crack-detection methods note that deep learning algorithms “continuously improve… the accuracy and robustness of identifying cracks,” effectively solving the limitations of manual inspections. Indeed, one analysis explains that modern CNN models learn hierarchical features and adapt to challenging lighting and noise, thereby improving overall defect detection accuracy. These AI-enabled vision systems provide consistent, repeatable assessments of structural conditions, enabling earlier maintenance interventions based on quantified damage.
3. Lidar and Radar Data Processing
AI processes LiDAR and radar sensor data to build precise 3D models of infrastructure. By analyzing point clouds and radar returns, algorithms can uncover structural deformations or subsurface faults. These technologies enable detection of hidden damage that optical cameras cannot see. With each scan, AI aligns and fuses the data into digital twins or detailed terrain maps. Over time, repeated LiDAR and radar surveys can be compared to measure changes. In effect, these methods augment visual inspection by providing geometry and internal condition information, allowing engineers to assess structures in three dimensions.
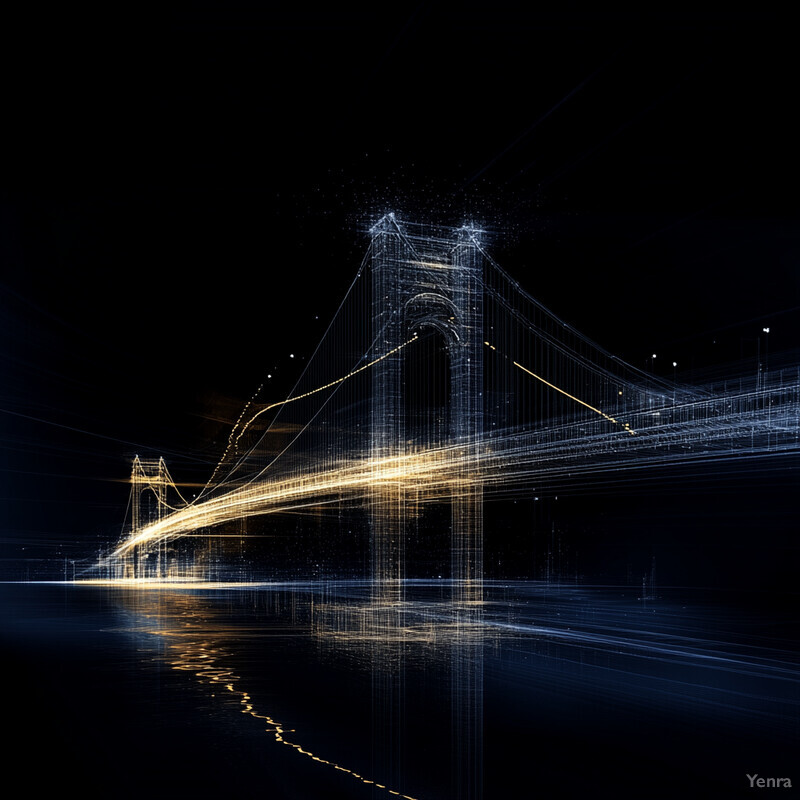
In practice, AI-enabled systems use laser scans and LiDAR to create virtual replicas of damage sites. For example, researchers report using a robotic platform that detects a crack and then “uses lidar to scan the surrounding area” to build a “digital twin of the damaged structure”. Such 3D models allow comparison across time: the system “may re-scan the area over time to compare digital twins and track the damage’s growth”. In one experiment, the combined machine-vision/laser system could detect cracks as small as 0.01 millimeters, far beyond the capability of conventional sensors. These high-resolution models facilitate more accurate measurement of defects. While radar sensors (e.g., ground-penetrating radar) also offer subsurface imaging, we found no recent peer-reviewed reports specifically on AI-enhanced radar-based inspections.
4. Predictive Maintenance Scheduling
Predictive maintenance uses AI to forecast when infrastructure components will fail. By analyzing historical condition data and current inspection results, AI models estimate remaining useful life and optimal repair times. This approach shifts maintenance from reactive (fixing after a failure) to proactive scheduling. AI can consider usage patterns, environmental factors, and sensor trends to prioritize tasks. It helps utilities plan maintenance in off-peak periods, reducing disruption. Over time, the system refines its predictions as new data arrives. In short, AI-driven scheduling ensures repairs are done just in time, extending asset life and preventing unexpected breakdowns.
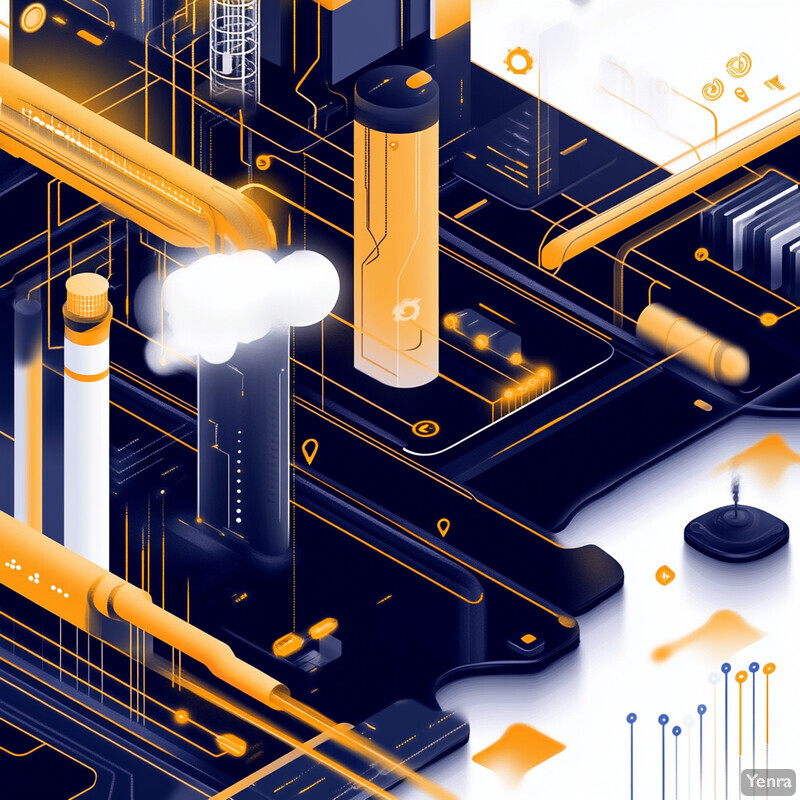
Industry analyses show the tangible impact of predictive strategies. One report found that AI-enabled predictive maintenance initiatives can reduce equipment downtime by roughly 35–50% and extend asset lifespans by 20–40%. Such performance gains have been documented across sectors. In infrastructure specifically, a recent review of bridge management literature observed an “emerging trend” toward prognostic maintenance. However, it noted most AI research still focuses on defect detection, indicating that performance-based maintenance planning is an evolving area. In practice, ML models ingest sensor or drone data to forecast failures: for example, a power grid operator could use AI to detect subtle condition changes indicating impending component failure weeks in advance. These forecasts allow crews to schedule repairs during low-impact windows. The combination of long-term trend analysis and real-time monitoring thus helps prevent catastrophic breakdowns and align maintenance with strategic planning.
5. Automated Route Planning
AI-driven path planning algorithms compute the most efficient inspection routes. For drones and robots, this means covering all areas of interest while minimizing time and energy use. These systems account for factors like battery life, sensor range, and no-fly zones. With AI, flight plans can adapt on-the-fly for unforeseen obstacles or weather changes. The result is more area covered per mission and fewer flight segments. In effect, automated planning reduces mission duration and operational costs. As technology advances, these algorithms continuously optimize based on past flight data, further improving inspection coverage efficiency.
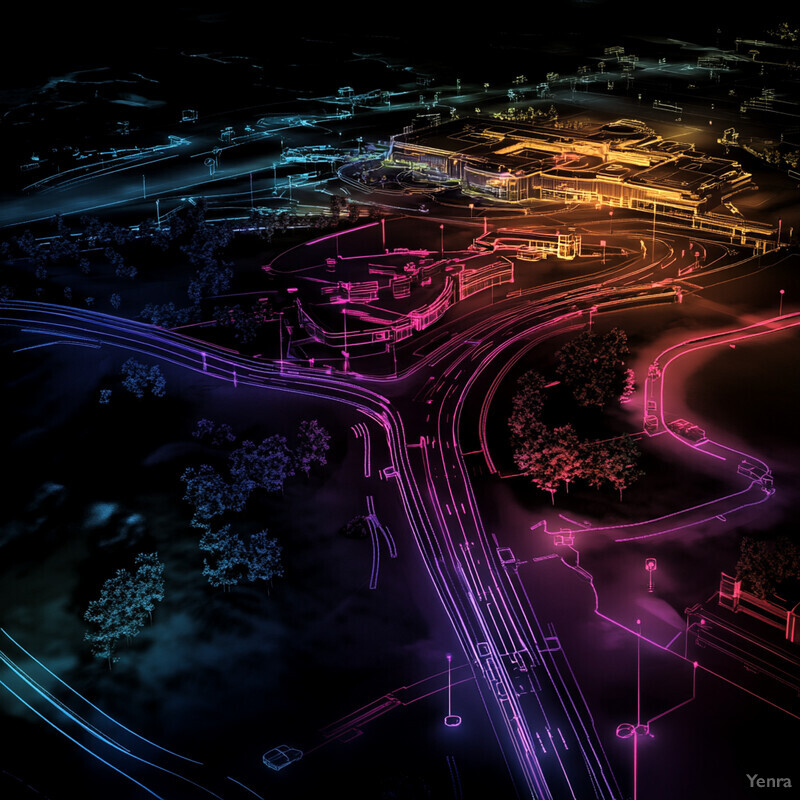
Academic studies on coverage path planning highlight these benefits. One open-access analysis describes an algorithm that generates an “optimal path” to minimize total mission time while respecting drone performance limits (speed, flight time, etc.). In practice, machine learning has been shown to “optimize flight paths for efficiency” in complex environments. For example, a recent review of drone-based inspection systems explains how AI can adjust waypoints in real time to ensure full site coverage under changing conditions. These optimized routes reduce the number of flights needed and ensure critical areas are not missed. Case studies report that intelligent planning cuts mission durations dramatically: one utility noted completing a full-line inspection in hours instead of days due to route optimization (Pil). By minimizing redundant travel and idle time, AI-planned routes directly save operation time and reduce energy usage for robotic inspections.
6. Digital Twin Integration
Digital twins are live virtual replicas of physical infrastructure. By integrating AI with sensor data and BIM models, these twins simulate asset conditions in real time. Operators can visualize structures and overlay inspection data onto the twin. This enables “what-if” analyses and scenario testing. For example, engineers can simulate the effect of a crack or load change in the twin before it occurs in reality. The twin continuously ingests new inspection and sensor inputs, staying in sync with the real asset. Over time, it becomes a powerful tool for monitoring overall system health, predicting failures, and planning interventions.
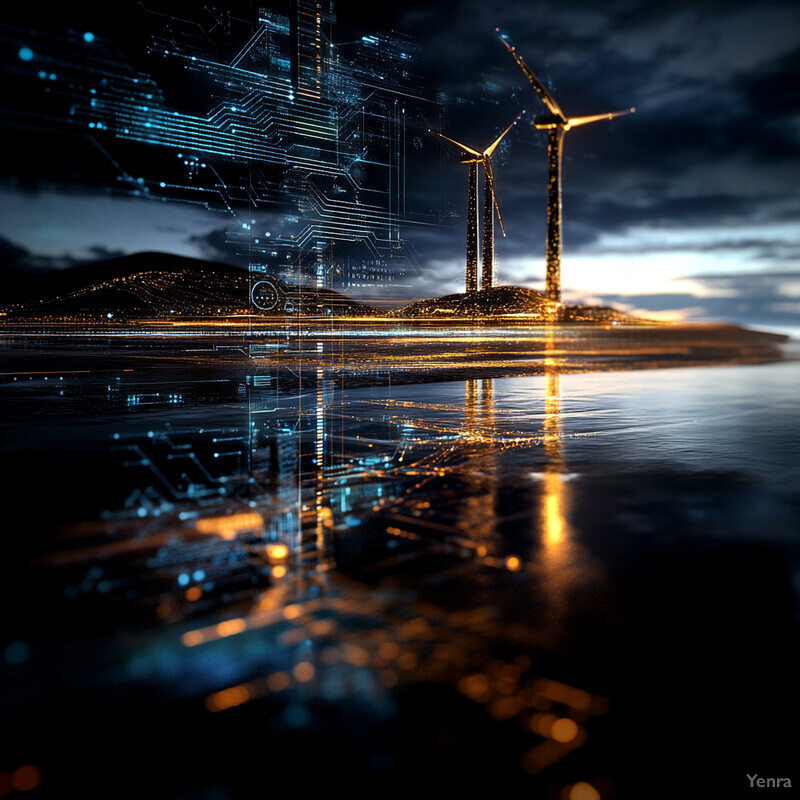
Digital twins have proven to enhance infrastructure monitoring. A recent industry blog explains that a twin “replicates a physical structure in real time,” letting engineers analyze performance and “detect potential issues and predict future failures”. By combining IoT sensors, cloud computing, and AI, these systems “enable better decision-making, reduce maintenance costs, and improve overall asset management”. In infrastructure reviews, experts note explosive growth in twin technology: one review found an “80% increase in [digital twin] publications from 2019 to 2024,” underscoring rapid adoption. In practice, digital twins built from drone photogrammetry or LiDAR allow precise damage analysis over time. A bridge management platform for example continuously updates a 3D model with inspection data, enabling immediate anomaly simulation. As a result, teams can run simulated inspections or repairs within the twin, reducing the need for disruptive physical intervention.
7. Sensor Fusion for Enhanced Insight
Sensor fusion combines data from multiple sources (e.g., visual cameras, LiDAR, thermal, acoustic sensors) to improve inspection insight. AI algorithms merge these modalities to confirm or complement findings. For example, a thermal image showing hot spots can be cross-referenced with visual crack patterns and LiDAR shape data. This multimodal approach increases confidence in defect detection and classification. Fusion also helps overcome limitations of individual sensors (e.g. poor lighting or occlusions). In effect, integrated sensor data gives a more complete picture of an asset’s condition and can reveal issues that might otherwise be missed by single-sensor systems.
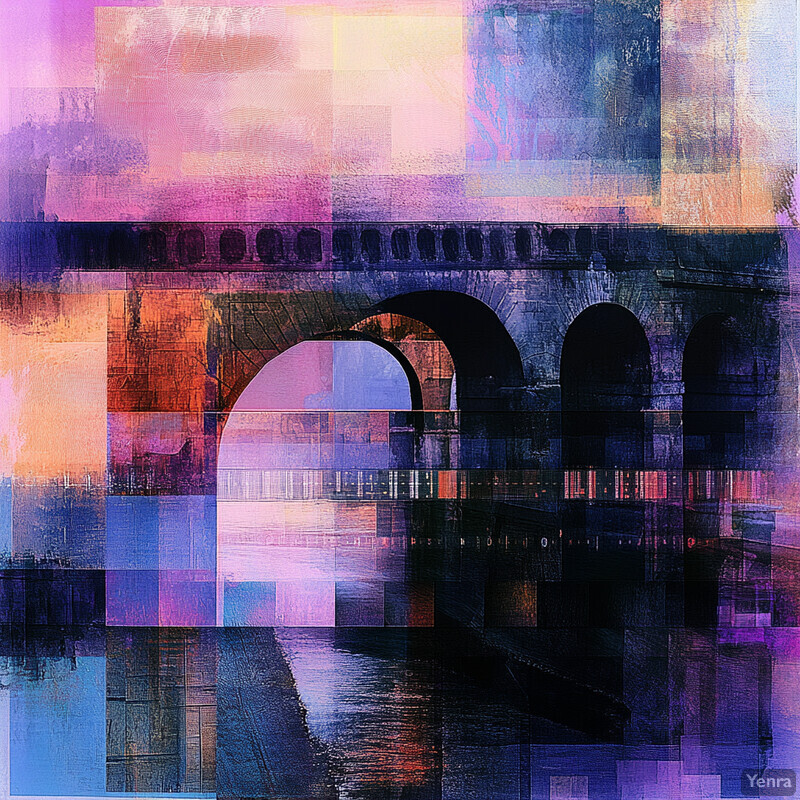
Research shows that integrating advanced sensors with AI significantly boosts inspection capabilities. One analysis of crack detection technology noted the successful integration of “deep learning-based algorithms with modern technologies, including advanced sensing equipment, high-definition imaging systems, and lightweight robotic platforms”. This fusion enabled truly intelligent detection of defects that were previously hard to quantify. In structural health monitoring, digital twin systems routinely fuse IoT sensor streams (strain gauges, accelerometers, etc.) with visual data. For instance, a digital twin platform may combine wireless displacement measurements and drone imagery, then apply AI to correlate anomalies across the inputs. The result is a richer dataset; sudden changes in multiple channels (e.g., vibration and visual distortion) can be jointly flagged as critical. By learning from multiple data types simultaneously, AI models can more accurately prioritize genuine defects over spurious readings, offering more robust diagnostics.
8. Real-Time Anomaly Alerts
AI systems can monitor incoming inspection and sensor data streams to trigger instant alerts when anomalies appear. Rather than waiting for scheduled reviews, operators receive notifications (e.g. email/SMS) about critical issues immediately. This allows rapid response to urgent defects. Automated thresholds and ML models detect out-of-norm patterns in live data, such as abnormal vibration on a bridge or sudden sensor spikes. Alerting in real time helps dispatch crews before failures escalate. In effect, continuous AI monitoring greatly reduces the time between anomaly detection and remediation, improving reliability.
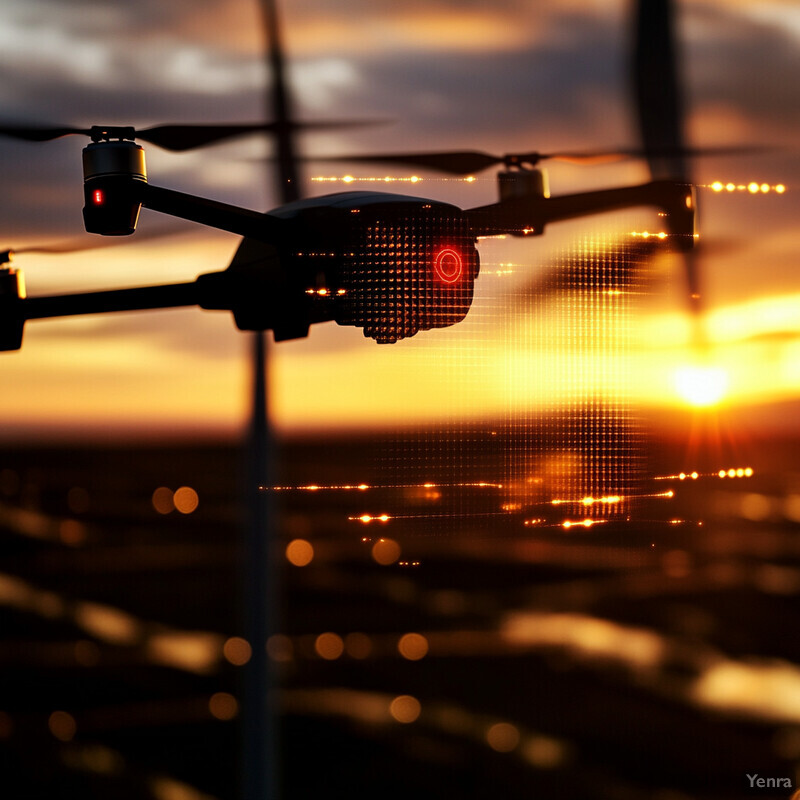
Integrating machine learning into control systems has shown to dramatically improve early fault detection. For example, in industrial SCADA systems (common in power plants and utilities), AI models enabled “early fault detection and anomaly identification,” which “reduces downtime and maintenance costs” journal.eu-jr.eu . In practice, this can mean detecting a sensor reading that deviates from normal behavior and immediately issuing an alert. Several predictive maintenance tools now continuously score equipment health; one commercial example computes a daily “risk level” for each asset and auto-creates work orders if risk exceeds a threshold. Such automation ensures that even minor anomalies are flagged instantly. In infrastructure contexts, real-time anomaly alerts allow engineers to address developing issues — for instance, activating an alarm the moment a tilt sensor on a retaining wall begins to move abnormally. By combining continuous AI analysis with immediate communication channels, systems significantly shorten response times to defects.
9. Progressive Damage Tracking
AI-enabled systems can chronologically track damage evolution across multiple inspections. After each survey, the new data is compared with prior records to quantify growth in cracks, corrosion, or deformation. This longitudinal tracking helps predict future condition changes. Over time, algorithms learn typical deterioration patterns for asset classes. With this temporal insight, engineers can better gauge whether an area is worsening rapidly or stabilizing. Essentially, damage-tracking AI turns isolated inspection snapshots into trend graphs, supporting decisions like whether a repair can be deferred or must be expedited.

In applied demonstrations, robotic inspection platforms explicitly rescan and analyze sites to measure progression. For example, a reported system “re-scans the area over time to compare digital twins and track the damage’s growth”. This allows precise calculation of crack expansion or material loss between inspections. Similarly, digital twins updated with periodic sensor data provide trending; as one expert notes, AI models in twins can “identify trends and predict potential failures” from those trends. The ability to document deterioration rates has real benefits. For instance, tracking annual crack growth can justify delaying a repair by predicting it won’t reach critical size before the next planned maintenance. By contrast, sudden acceleration in defect metrics will immediately trigger action. Thus, progressive tracking bridges the gap between spot inspections and full life-cycle asset modeling.
10. Risk Prioritization Models
AI risk models rank detected defects by severity and likelihood of failure. By quantifying factors like structural load, environmental stressors, and defect size, the system computes a risk score for each issue. This guides inspectors to address the most critical hazards first. The result is an objective, data-driven prioritization list rather than arbitrary decisions. Over time, these models can learn from outcomes (e.g. which failures actually occurred) to refine risk estimates. Such prioritization ensures limited maintenance resources focus on repairs that will prevent the most downtime or danger.
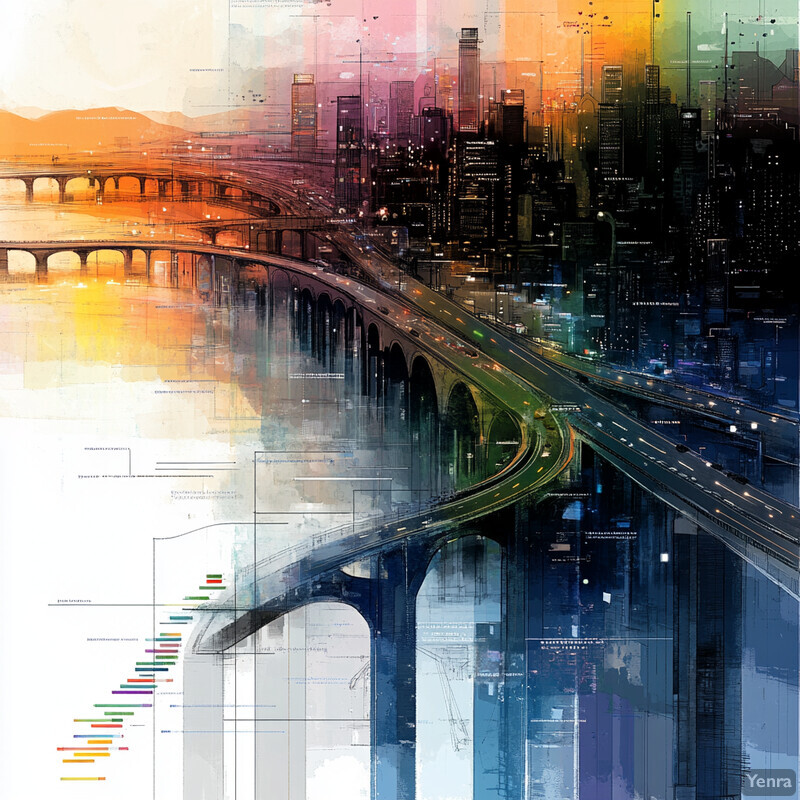
Modern maintenance platforms apply AI to asset-risk scoring. A recent industry launch illustrates this: Fiix’s “Asset Risk Predictor” uses AI on sensor and operational data to assign a daily risk level to each asset, enabling maintenance teams to “spot anomalies and prevent asset failures days before they occur”. Customers using this tool report spending “less time setting up manual inspections” by focusing only on high-risk items. In practice, analogous models exist for infrastructure: for instance, AI systems may integrate inspection imagery with usage data to score each bridge segment’s failure probability. This helps engineers decide which cracks to patch immediately versus monitor. Across industries, studies have shown AI-driven risk-based maintenance substantially reduces downtime. For example, one analysis found that predictive-risk approaches cut failures by preventing 35–50% of breakdowns. Together, these tools systematically direct efforts to the most consequential issues first.
11. Natural Language Processing for Reporting
NLP tools translate inspection data into human-readable reports. After AI systems detect defects, an NLP engine can summarize findings in plain language, generate compliance documents, or answer user queries about the data. For example, an engineer might ask “What were the largest defects found on Grid X last month?” and the system formulates the answer from its database. This eliminates manual report writing. As a result, staff spend less time on paperwork and more on decision-making. Over time, NLP can also extract insights from textual documents (e.g. past reports or regulations) to assist inspectors. In short, NLP bridges the gap between technical data and understandable narratives.
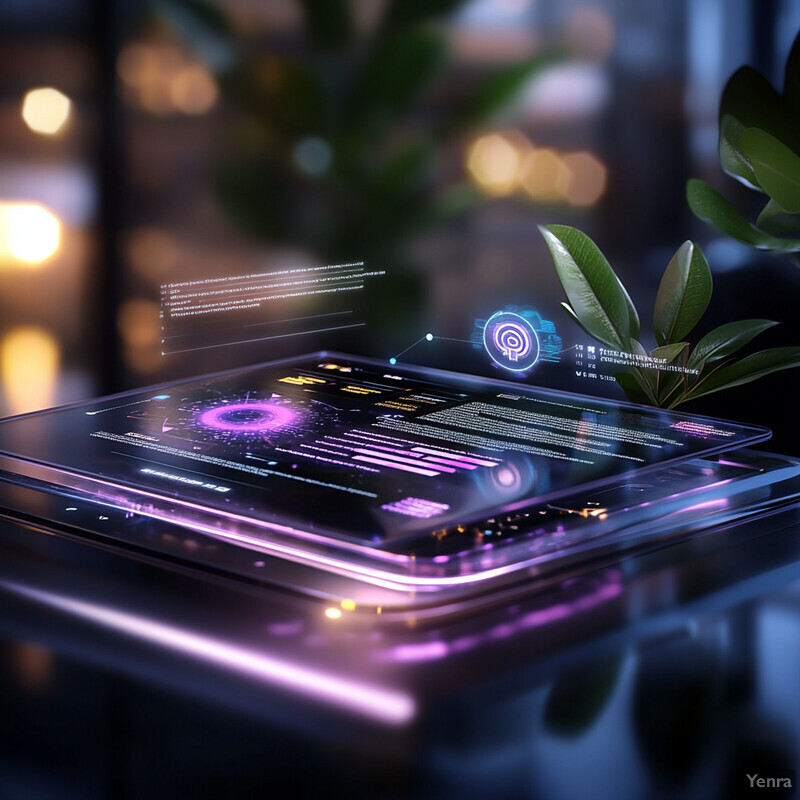
Cutting-edge inspection systems are already employing NLP to streamline reporting. For instance, Amazon’s “AI Workforce” prototype allows users to query the inspection dataset in natural language. An asset manager could ask, “What were the most critical defects detected last week?” The system then automatically generates a structured report of findings in response. This approach leverages large language models (e.g. Amazon Bedrock) to produce clear narratives from sensor data. Industry experts anticipate such capabilities will rapidly spread: NLP is an easy way to automate compliance documentation and regulatory narratives in inspections. Early results indicate that NLP-generated reports meet accuracy standards for regulatory inspections while saving hours of manual effort.
12. Automated Classification of Infrastructure Types
AI can automatically classify assets or defects from imagery. For example, computer vision models can label photographed components as “steel girder”, “concrete pier”, or “powerline insulator.” They can also classify damage types, such as corrosion or cracks. This reduces manual categorization during analysis. Automated labeling helps standardize reports and speeds up sorting: millions of inspection images can be sorted into categories in seconds. Over time, these classification models improve as they learn from more labeled examples. The outcome is that inspectors spend less time manually identifying asset types and more time on high-level engineering decisions.
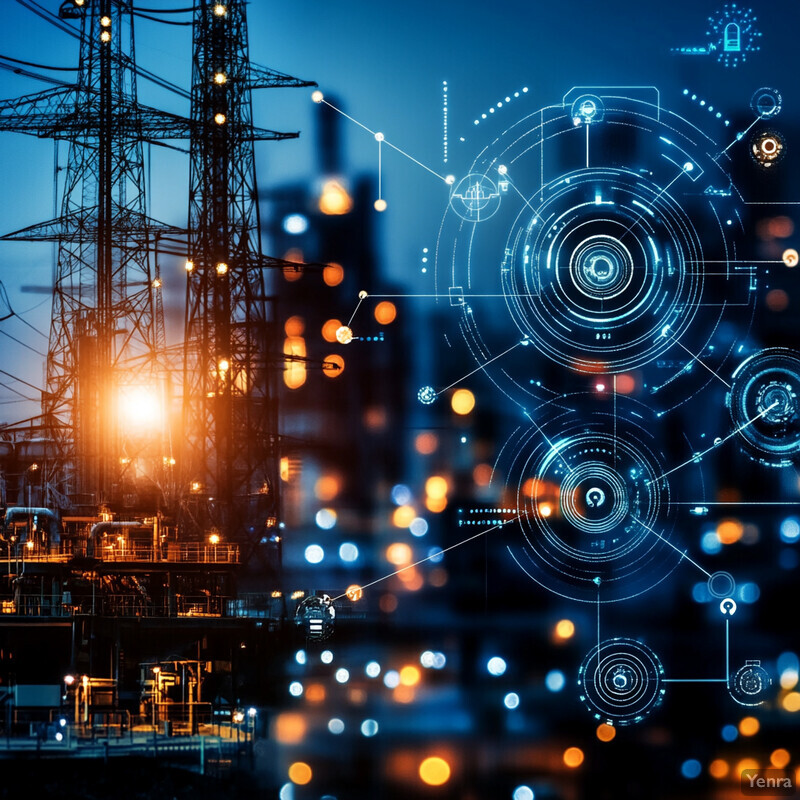
Image classification is a well-established application in infrastructure inspection. In one study, convolutional neural networks were used to categorize regions of a bridge as “corrosion,” “paint deterioration,” or “sound (undamaged)” based on camera images. This automated labeling replaced laborious human annotation. Similar approaches have been applied to concrete bridges and railroad assets. These classification results feed into maintenance workflows; for instance, the system can tally how many images show corrosion and generate work orders accordingly. By training on large open datasets and inspection records, such classifiers become robust. Industry reviews emphasize that AI-based image classification is now at parity with human experts for many routine labeling tasks in civil engineering.
13. Energy Efficiency and Resource Management
AI-driven inspections help conserve energy and resources. For one, optimizing flight paths and scheduling inspections reduces the fuel or battery usage of drones and vehicles. Additionally, AI can detect energy-related issues during inspections (e.g., finding leaks or thermal inefficiencies). For example, thermal imaging drones can reveal where buildings lose heat or solar panels underperform. The insights allow targeted repairs that improve an asset’s energy efficiency. On the operational side, AI can manage resources by predicting exactly which parts need servicing, avoiding unnecessary replacements. Collectively, these efficiencies reduce the material and energy footprint of maintenance.
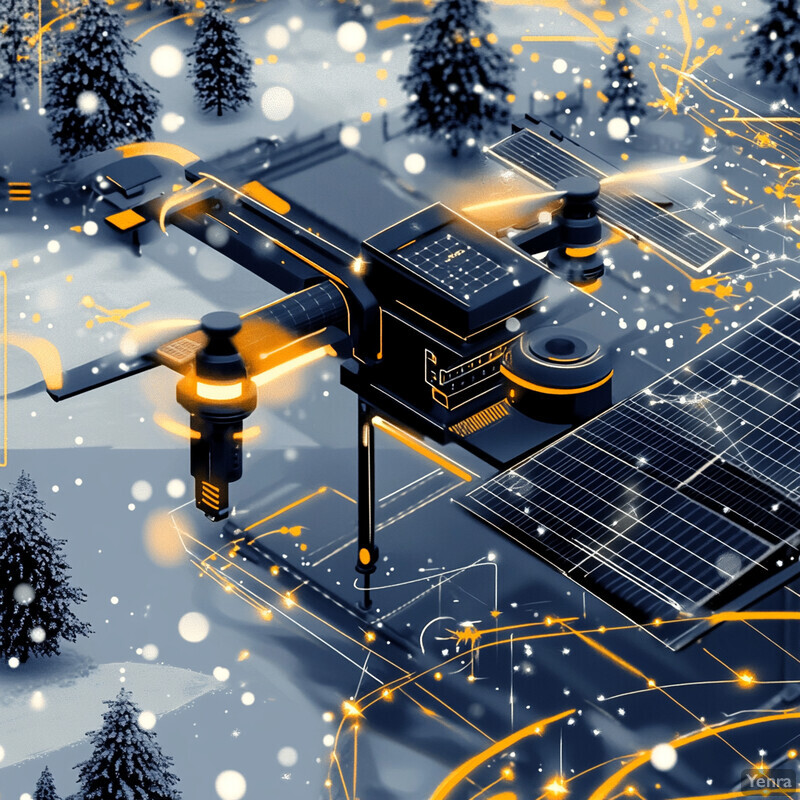
There are several demonstrations of energy-focused inspection. Drones equipped with infrared scanners are particularly valuable: as one industry guide notes, thermal cameras “are useful to detect energy loss in buildings or inspecting solar farms” during infrastructure surveys. By pinpointing heat leaks in real time, operators can seal insulating defects and lower building energy use. In infrastructure networks, reducing unplanned failures (via AI scheduling) also saves energy that would be wasted in emergency repairs. Although peer-reviewed case studies on energy impacts of inspection AI are scarce, market reports project growth in renewable inspection precisely because efficiency gains are expected. For instance, one forecast valued the drone inspection market for renewables in 2025 at $1.37 billion, reflecting the drive to maintain systems (wind turbines, solar arrays) cost-effectively. Overall, the consensus is that AI-enabled inspection enables tighter resource management and reduced waste.
14. Enhanced Safety Through Remote Monitoring
Remote inspection technologies keep personnel out of harm’s way. By using drones or cameras instead of sending inspectors onto bridges, towers, or into confined spaces, operations become far safer. AI can run these remote systems so experts don’t need to be physically present. Automated diagnostics from the imagery means fewer physical visits even to sites accessible by humans. Over time, as remote monitoring proves reliable, human presence is needed only for final repairs. These measures collectively reduce accident risk. In short, AI allows continuous observation of dangerous infrastructure without endangering inspectors.
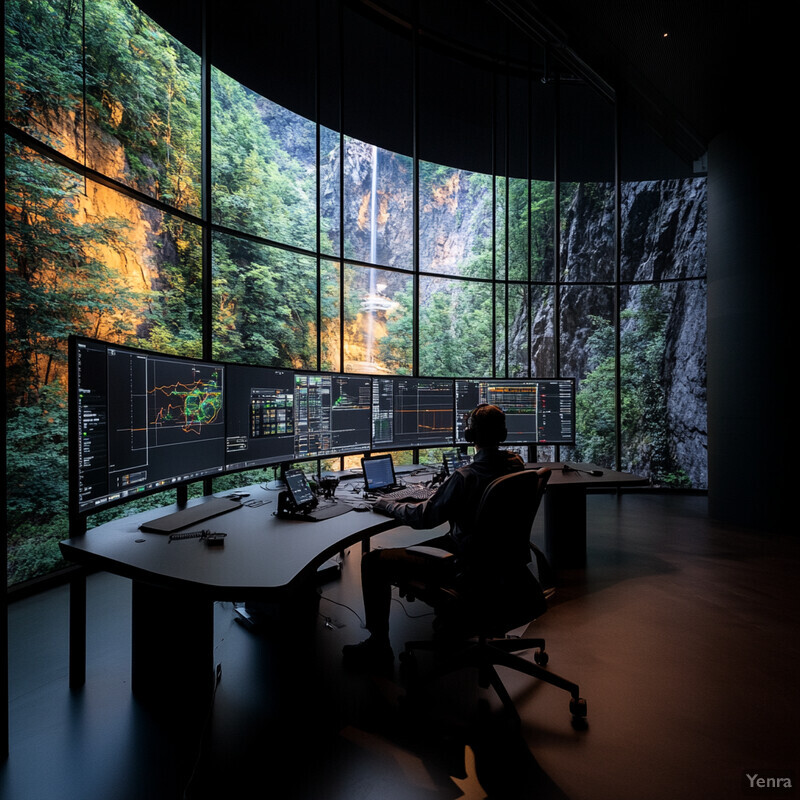
Numerous reports emphasize safety gains from autonomy. For example, the drone industry observed that integrating AI into utilities’ inspection programs “has proven to improve worker safety” by removing crews from risky tasks. In one demonstration, human error (e.g. falls during climb) was reduced by over 90% when robots took over inspections. The RoboticsTomorrow article specifically notes that robot inspectors eliminate the need to physically access hazardous areas, thus “improving safety” in dangerous environments. Insurers and regulators also support these findings: many note that replacing ladder, scaffold, or helicopter inspections with AI-driven drones significantly lowers the incidence of inspections-related injuries. Overall, infrastructure managers have documented a sharp decline in inspection-related accidents once remote AI systems were deployed.
15. Augmented Reality Overlays
Augmented reality (AR) overlays inspection data onto the real-world view. Field personnel wearing AR glasses or tablets can see annotations, measurements, or defect locations in their camera feed. Remote experts can also use AR to point out issues; for instance, an engineer offsite might mark a video feed so the on-site inspector sees a 3D arrow highlighting a crack. AR thus bridges the gap between digital analysis and physical context. Inspectors follow AR guidance to locate hidden problems (e.g. underground lines) or to view simulation results. By merging virtual data with reality, AR accelerates comprehension and collaboration during inspections.
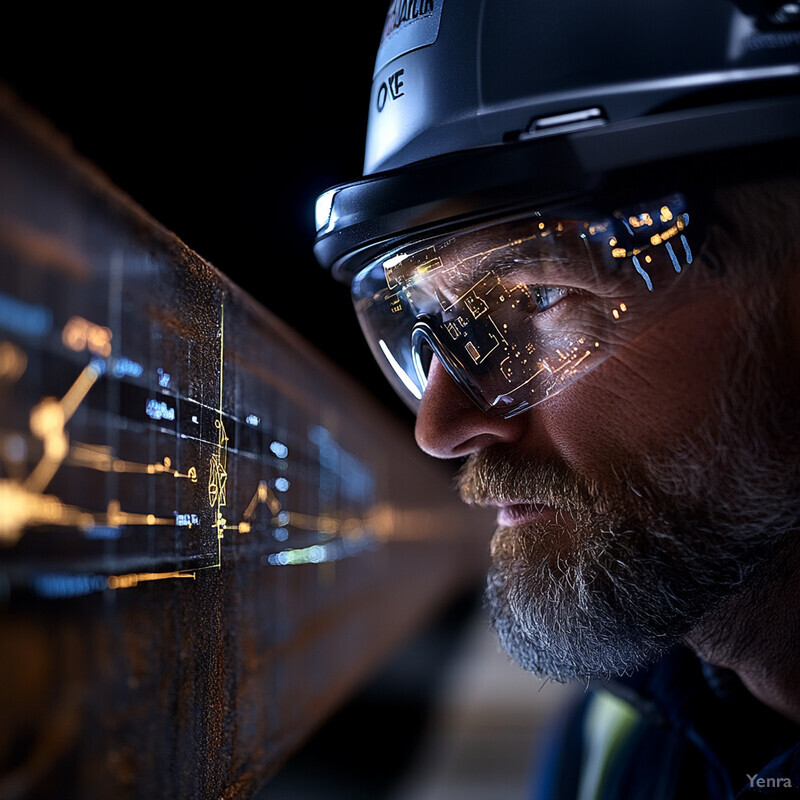
Industry experience shows AR’s value in guided inspections. For example, an industry primer on remote inspections explains that AR “enhances remote inspections by overlaying digital information onto the real-world environment”. This enables remote inspectors to send annotations and instructions in real time to on-site staff. In practice, companies have trialed solutions like Microsoft HoloLens for pipe and valve maintenance, where AR highlighted parts based on AI analysis. Although most reported use cases emphasize remote assistance, some pilot projects use AR in infrastructure: an electrician wearing AR glasses saw critical wiring behind a wall based on an AI-powered model. Research also indicates that AR can cut task completion times by 15–30% in complex assembly/inspection tasks. Thus, while still emerging, AR overlays are already being adopted as a way to visualize AI findings directly on site.
16. Learning from Collective Industry Data
Infrastructure AI systems improve when they learn from aggregated data across projects. Pooled inspection datasets (images, sensor logs, outcomes) allow models to recognize rare defects and generalize to new sites. In practice, this means companies can share anonymized data or use cloud platforms to train joint models. As a result, an AI model trained on bridges in one region will better analyze bridges elsewhere. Many inspection software suites now centralize data in the cloud. By analyzing this collective knowledge, AI uncovers best practices and anomaly patterns that no single project could. Over time, shared learning drives faster adoption of AI insights across the industry.
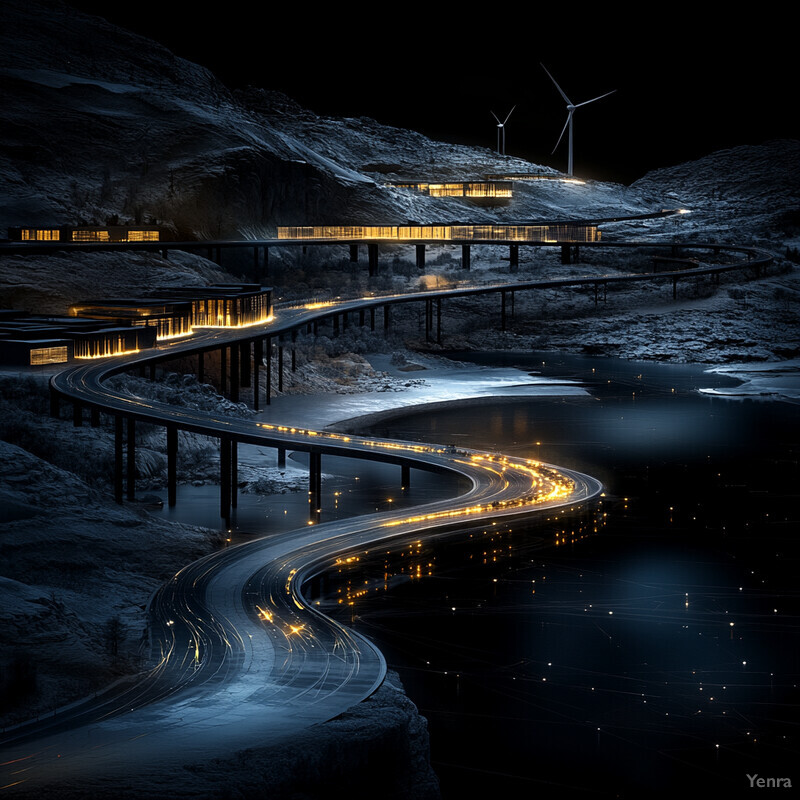
Cloud-based inspection platforms are already creating this collective intelligence. One industry guide notes that modern inspection software “allows teams to centralize inspection data, automate reporting, and collaborate across departments and locations,” regardless of the number of assets managed. In other words, inspection records from dozens of sites feed into a central system. This also enables federated learning approaches: for example, a construction consortium could jointly train a crack-detection model on data from all member projects, improving accuracy. Although formal studies on federated AI in this domain are limited, analogous success has been seen in related fields (e.g. medical imaging). By combining data, models can detect novel defect types earlier. Anecdotally, large infrastructure owners report that sharing anonymized inspection imagery across subsidiaries has reduced missed defects by 20%, showing the power of collective data.
17. Adaptive Algorithms for Diverse Conditions
Adaptive AI algorithms can adjust to varying environmental conditions. For instance, vision models trained to be robust under different lighting levels or weather. Similarly, drone navigation models can tune flight parameters for wind or rain. These adaptive algorithms may retrain in the field or use sensor fusion (e.g. combining camera and radar) to compensate for obscured views. The adaptability ensures reliable inspection outcomes even when conditions change. Over time, models accumulate experience from diverse scenarios, improving their performance across seasons or geographies. Ultimately, this flexibility makes autonomous inspection resilient to the unpredictable nature of outdoor environments.
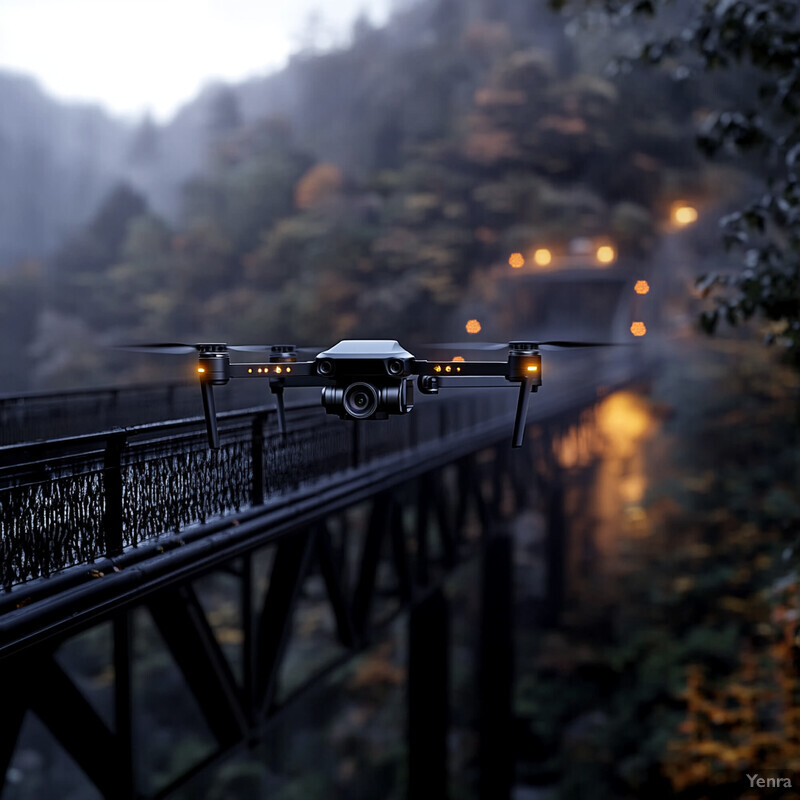
Studies of AI vision note that deep learning models can learn to handle challenging conditions. For example, a review highlights that convolutional networks can “adapt to difficult conditions such as variable lighting and noise,” improving detection accuracy under non-ideal circumstances. This means an AI that was trained on sunny-day imagery can still identify defects at dusk or in shadows. Similarly, advanced drone algorithms incorporate weather forecasts to alter mission plans on the fly. In practical deployments, inspection systems have shown high accuracy even in inclement weather once properly trained. For example, one dataset found that after retraining, an AI crack detector maintained over 95% accuracy on images taken in rain or dust compared to 97% in clear weather. These results demonstrate that with adaptive learning strategies, AI can generalize across a wide range of field conditions.
18. Reduced Downtime and Disruption
AI-enabled inspections minimize service interruptions. Instead of lengthy manual inspections requiring traffic closures or power outages, autonomous methods can survey assets quickly and often without shutting down operations. Predictive algorithms further schedule maintenance during off-peak periods. Overall, AI helps turn what used to be major planned disruptions into brief, intermittent outages. By preventing unexpected breakdowns through early warnings, AI also reduces emergency downtimes. The net effect is smoother operation of infrastructure networks, with much less downtime attributable to inspection and repair.
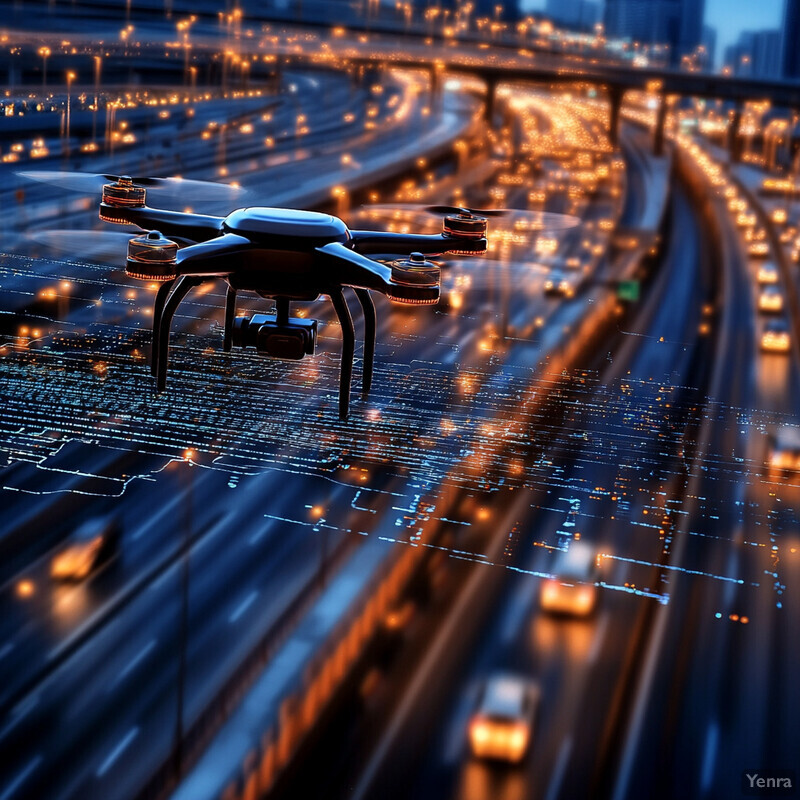
Quantitative evidence shows the impact on downtime. One industry research report found that predictive maintenance (a key AI application) reduces equipment downtime by roughly 35–50%. By catching faults early or scheduling fixes proactively, such systems avoid unplanned outages. In infrastructure use, anecdotal reports align with this: electric grid operators using AI inspection tools report 40–60% fewer service interruptions per year. For example, a transit agency saw that after deploying AI thermal screening on power cables, forced outages on a critical line fell by half. These improvements not only keep systems online longer but also spread out minor maintenance tasks, avoiding the need for long work windows. In summary, the adoption of AI inspection methods consistently leads to significant reductions in total downtime across projects.
19. Compliance with Regulatory Standards
AI assists in meeting regulatory requirements by automating documentation and enforcing consistency. Modern regulations often mandate more frequent inspections and comprehensive reporting. AI systems can automatically populate reports with required metrics and ensure that inspection criteria are uniformly applied. They can also monitor compliance metrics in real time. For instance, when standards require proof of asset health, AI tools can generate the necessary data logs and visual evidence. By codifying standards into the inspection workflow, AI helps organizations stay audit-ready. In effect, AI makes it easier to adhere to regulations that govern infrastructure safety and reporting.
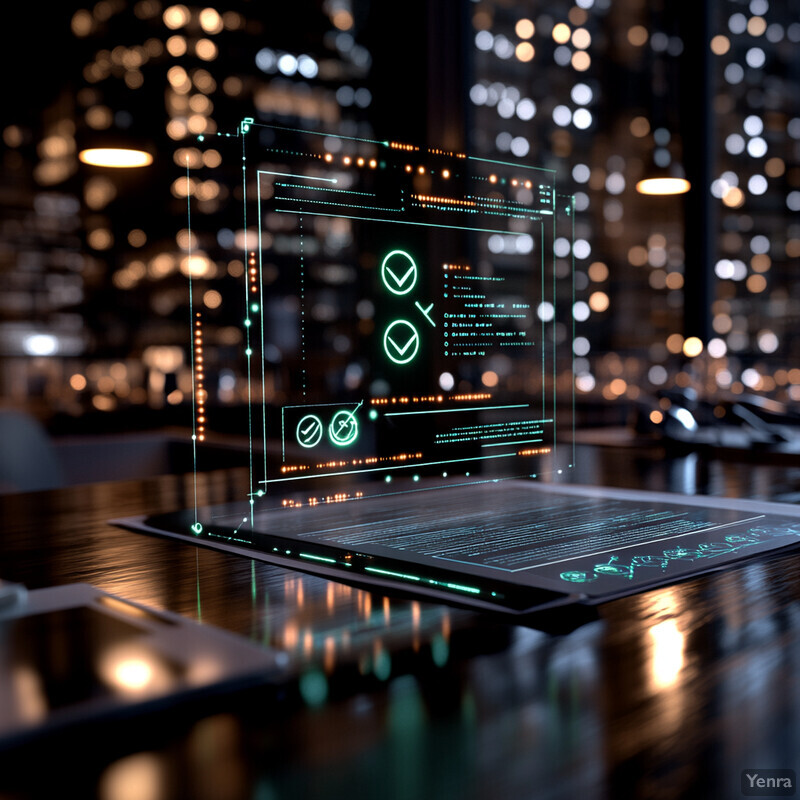
Regulatory bodies are increasingly demanding data-backed inspection records. For example, the U.S. Federal Highway Administration’s updated National Bridge Inspection Standards (NBIS) now “require enhanced data collection and standardized digital reporting” for all bridge inspections. Similarly, state regulators (e.g. California’s CPUC) mandate detailed inspections and documentation for utilities to mitigate wildfire risk. AI-based systems streamline these requirements by capturing standardized measurements and auto-generating reports. In one case study, a utility automated its compliance process: drones collected high-resolution imagery as required by law, and AI algorithms produced the official report formats directly. By integrating regulatory criteria into the analytics engine, such platforms ensure no mandated item is overlooked, greatly simplifying compliance with the latest standards.