Video: Aerodynamic Optimization
Song: Aerodynamic Optimization (Lyrics)
1. Automated Shape Optimization
AI-driven shape optimization automates the process of refining aerodynamic geometries (e.g. wings, airfoils) to improve performance metrics like lift-to-drag ratio. Techniques include neural networks, genetic algorithms, and reinforcement learning, which iteratively adjust shape parameters guided by performance objectives. These methods greatly reduce manual trial-and-error and explore broader design spaces. For example, a deep reinforcement learning (RL) agent can autonomously modify an airfoil to maximize lift-to-drag nature.com . Hybrid approaches, such as neural-network surrogates combined with genetic algorithms, have shown the ability to find novel high-performance shapes efficiently. Automating shape optimization via AI accelerates design cycles and often discovers configurations that outperform manually-tuned ones.
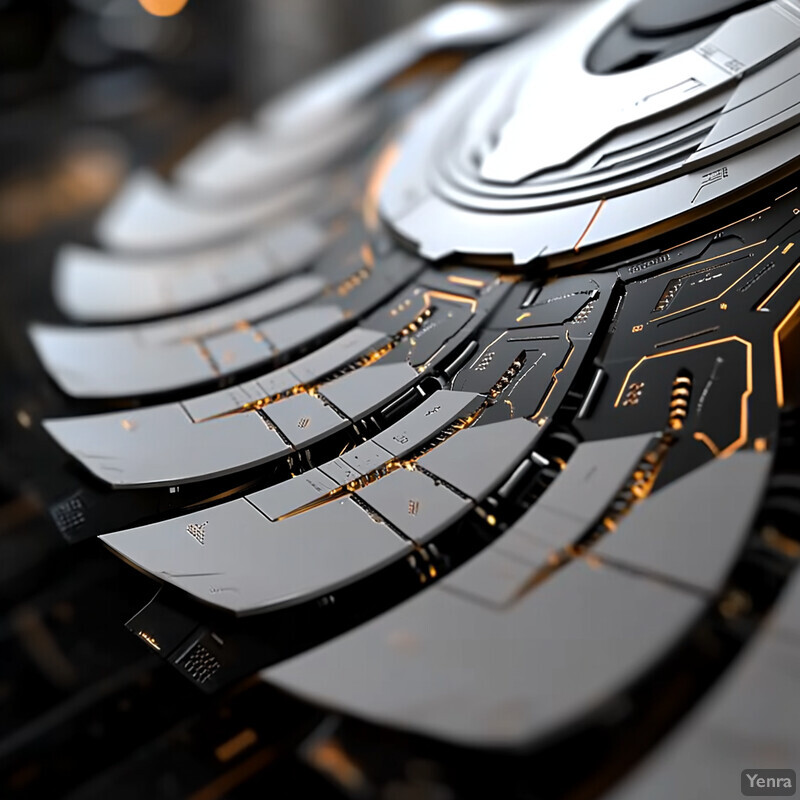
Recent studies demonstrate concrete gains from AI-driven shape optimization. Dussauge et al. (2023) applied deep RL to airfoil design and found that the agent rapidly learned to generate high-L/D shapes; the learned shapes closely resembled known optimal profiles nature.com . Khan et al. (2025) used a hybrid neural-network–genetic algorithm to optimize UAV airfoils, reporting that the optimized NACA 4415 airfoil achieved a maximum lift-to-drag ratio of ~25.22 (at Re≈7.7×10^5, AoA≈11.2°), outperforming NACA 2412 (L/D≈23.93) nature.com . These results underscore that AI-based optimization can yield measurable improvements in aerodynamic efficiency over traditional designs.
2. Surrogate Modeling for CFD
Surrogate models use machine learning (often neural networks or Gaussian processes) to approximate expensive CFD simulations. By learning the relationship between shape parameters and aerodynamic outputs, they predict results orders of magnitude faster than running full CFD each time. This enables rapid design space exploration: AI surrogates provide near-instant estimates of pressure fields or drag, greatly reducing the computational burden in optimization loops. Modern surrogates include physics-informed neural nets and operator networks that automatically differentiate flow solutions researchgate.net . As training data accumulates, these models become more accurate, allowing designers to iterate quickly. The trade-off is that surrogates must be carefully validated, but they unlock real-time performance prediction and more extensive parametric studies.
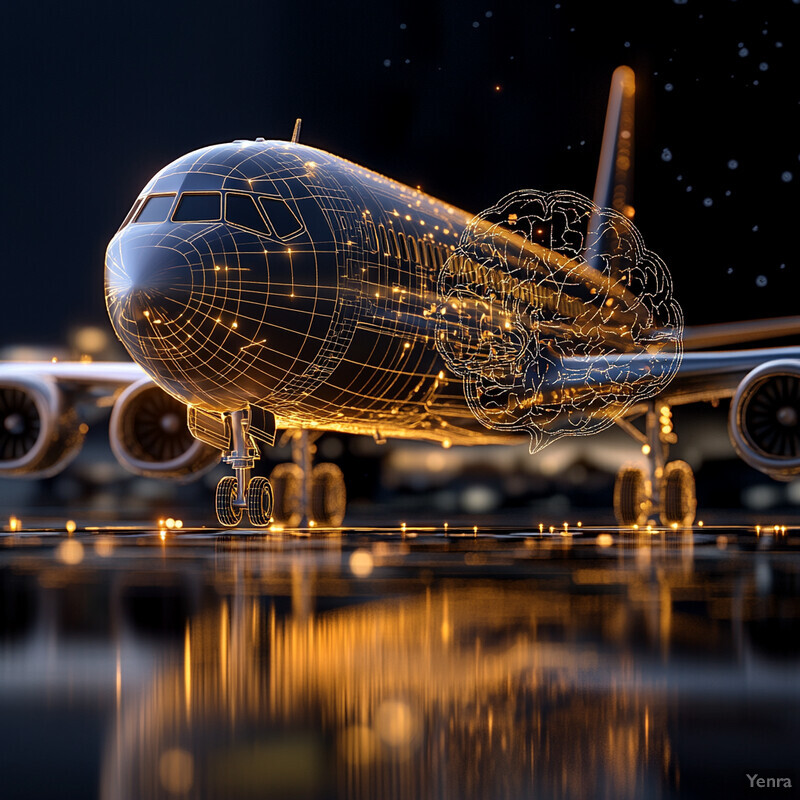
High-fidelity studies quantify the speed and accuracy of AI surrogates. Catalani et al. (2024) developed a neural "field" model of aircraft aerodynamics, achieving five orders of magnitude faster predictions than traditional CFD while maintaining low error nature.com . Their surrogate ran thousands of times faster yet still captured flow details accurately. Other research shows ML surrogates can achieve low mean squared error (MSE) across a range of conditions nature.com . With such performance, surrogates enable near-instant predictions of lift, drag, and pressure distributions, making design iterations and uncertainty studies feasible in real time.
3. Reduced-Order Flow Modeling
Reduced-order models (ROMs) distill complex flowfields into a small number of modes or states to allow faster computation or analysis. AI accelerates this by learning those modes from data, using techniques like autoencoders or ensemble networks. The idea is to project full CFD results into a low-dimensional latent space (for example via proper orthogonal decomposition or neural networks) and then evolve these latent variables with simple equations (e.g. LSTMs). This yields a surrogate that captures unsteady flow dynamics cheaply. Such ROMs enable tasks like rapid parametric studies, control, and long-time predictions. By reducing degrees of freedom, AI-based ROMs make simulating turbulent or unsteady flows much faster, albeit with some loss in detail.
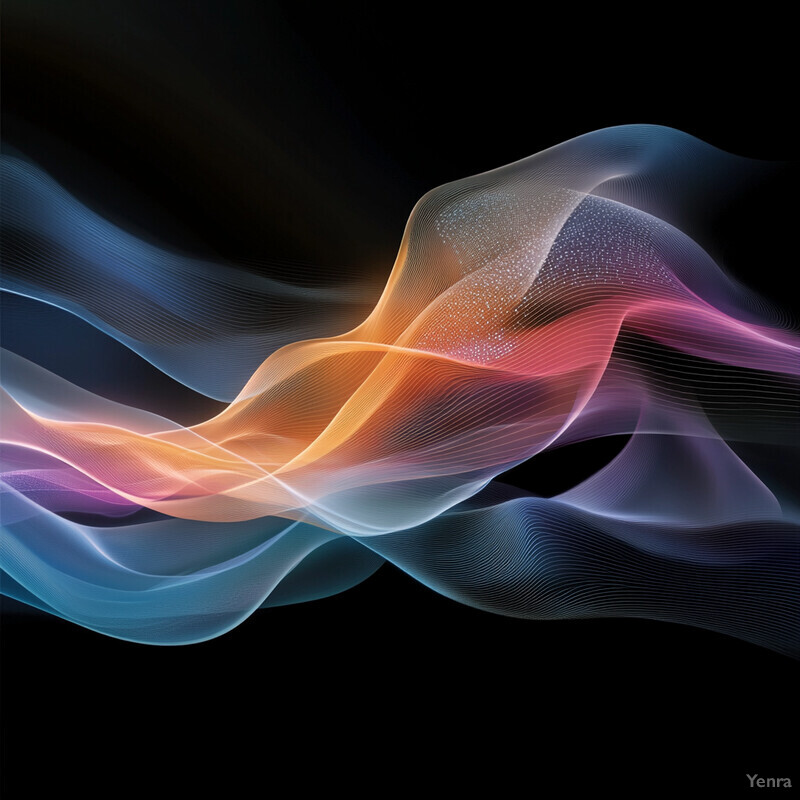
Neural-network ROMs have shown strong predictive capability on unsteady flows. Halder et al. (2024) created a ROM combining a convolutional autoencoder with an ensemble of LSTM networks. They demonstrated that this model significantly reduces error growth in time-evolving predictions of flows not seen in training arxiv.org . In their cases, the ensemble-LSTM approach maintained accurate forecasting of latent flow variables far into the future. This indicates that data-driven ROMs can reliably capture dominant flow features, enabling efficient simulation of unsteady aerodynamics that would otherwise require many costly CFD runs.
4. Turbulence Modeling
AI is increasingly used to improve turbulence modeling by learning closures and corrections from data. Traditional RANS and LES models use fixed formulae for turbulent stresses, but ML can infer these from high-fidelity data. For example, neural networks (including physics-informed nets) can predict Reynolds stresses or wall shear stresses under varying flow conditions. Such data-driven models can adapt to non-equilibrium flows or complex physics that conventional models struggle with. The result is often more accurate predictions of separation or heat transfer. By embedding known physics (like symmetries or conservation laws), AI turbulence models can generalize better. Overall, ML turbulence models aim to reduce the error of RANS/LES and provide uncertainty estimates where needed.
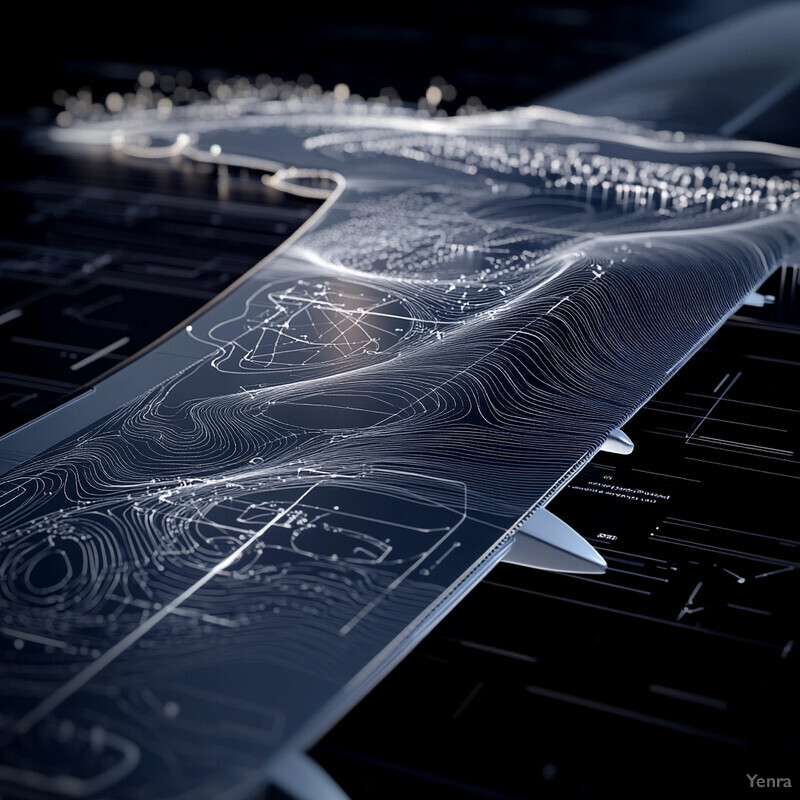
Recent reviews and studies highlight the power of AI turbulence closures. Zhang et al. (2023) note that physics-informed neural networks (PINNs) have been trained to predict wall-shear and velocity profiles across different Reynolds numbers. In one example, a PINN predicted turbulent boundary-layer wall shear stress patterns at arbitrary Reynolds numbers and outperformed traditional equilibrium models in non-equilibrium flows mdpi.com . This shows that a trained network can capture boundary-layer behavior more flexibly than a fixed algebraic model. Such data-driven closures have successfully modeled laminar-to-turbulent transition and flow separation in complex aerodynamics, demonstrating the promise of ML in turbulence modeling.
5. Inverse Design Techniques
Inverse design flips the usual problem around: instead of optimizing a design to meet objectives, we specify target performance and ask AI to generate a shape. Machine learning excels at this by using generative models. For instance, conditional variational autoencoders (VAEs) or GANs can be trained so that, given desired aerodynamic features (like lift and drag), they output a shape (airfoil or wing) expected to meet them. This approach transforms design into a prediction task: sample shapes from a learned distribution. It accelerates early design phases by providing starting points that satisfy requirements, reducing the need for long optimization loops. The challenge is ensuring those shapes are smooth and physically realizable, often addressed by custom loss functions or architecture designs.
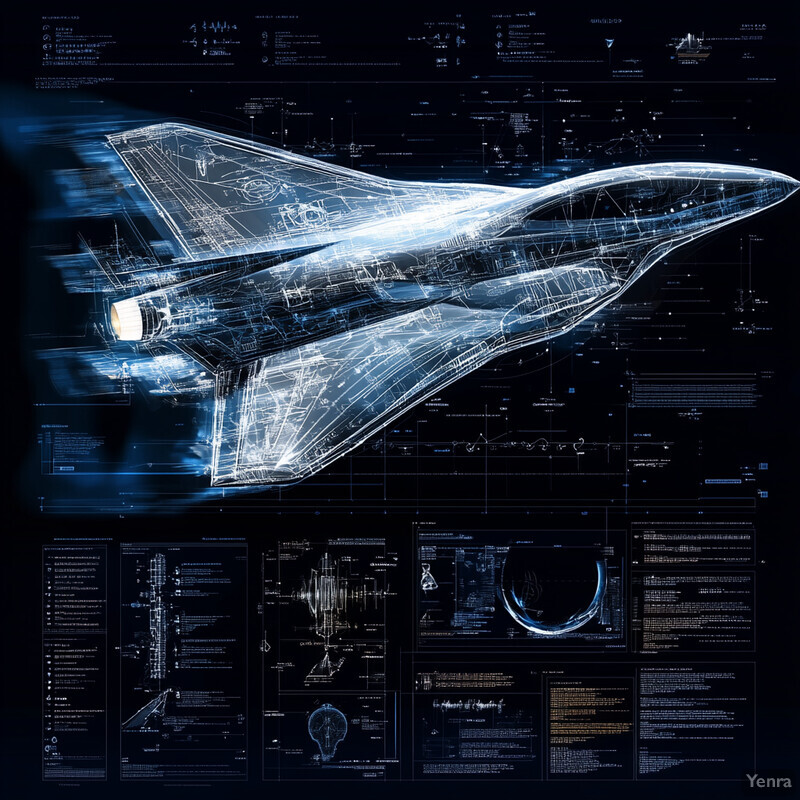
Recent work demonstrates successful inverse aerodynamic design via deep generative models. Yonekura (2023) proposed a hybrid CVAE–WGAN approach for airfoil generation. The model takes a target lift coefficient and generates smooth airfoil coordinates. In tests, the combined VAE-WGAN model produced high-quality shapes: pure VAE gave the most accurate lift-to-drag but lower variability, GAN gave more diversity but rougher shapes, and the hybrid achieved a good balance arxiv.org . These generative networks showed they could produce valid airfoil geometries meeting specified aerodynamic criteria, highlighting AI’s capability in inverse design tasks.
6. Multidisciplinary Optimization
Multidisciplinary optimization (MDO) integrates aerodynamics with other domains (structures, controls, propulsion) to optimize an entire system. AI assists MDO by coupling or surrogate-modeling different physics. For example, neural networks or multi-fidelity surrogates can approximate both aerodynamic loads and structural stresses simultaneously. Reinforcement learning and evolutionary methods can handle the larger parameter space of MDO. By learning complex cross-domain relationships, AI enables co-optimization, for instance trading off wing shape against weight or stiffness. The result is designs that are globally optimal across disciplines. AI-driven MDO thus yields more efficient airplanes by considering aero-structural trade-offs early in the design.
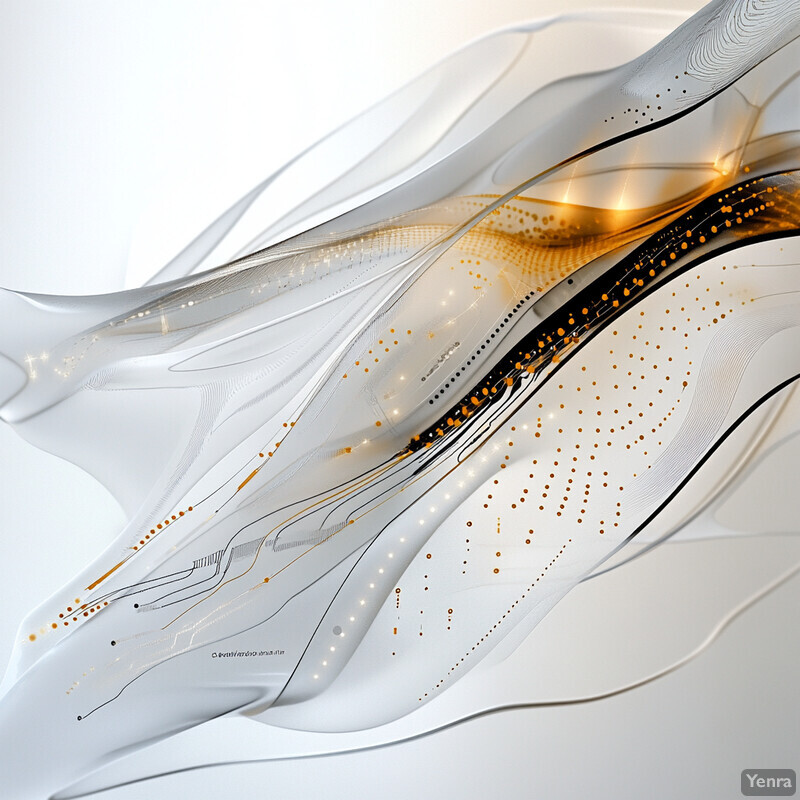
Data-driven MDO frameworks have shown promising results. Ramos et al. (2025) built a deep RL framework that simultaneously optimizes lift-to-drag ratio and structural thickness of an airfoil. They compared against Particle Swarm Optimization (PSO) and found the RL agent outperformed PSO on efficiency. With transfer learning, their agent achieved comparable performance with much less computation arxiv.org . Specifically, the RL solution maintained high L/D while preserving minimum thickness, demonstrating that AI can effectively navigate aero-structural trade-offs. This showcases how learning-based MDO can yield high-performance designs across disciplines.
7. Reinforcement Learning for Control Surfaces
Reinforcement learning (RL) is applied to control surface actuation (flaps, ailerons, thrusters) to improve real-time aerodynamic performance. In this context, an RL agent learns a control policy that adjusts surfaces in response to flow states to maximize objectives (e.g. lift) or minimize drag. Unlike classical PID control, RL can handle complex, time-dependent flow interactions. Typical setups use computational fluid dynamics in the loop to train the agent. Successful RL control laws can stabilize separated flow, adapt to disturbances, or optimize cruise efficiency by continuous surface adjustments. This line of work extends AI from design to active control, enabling “smart” wings that adapt shape on-the-fly.
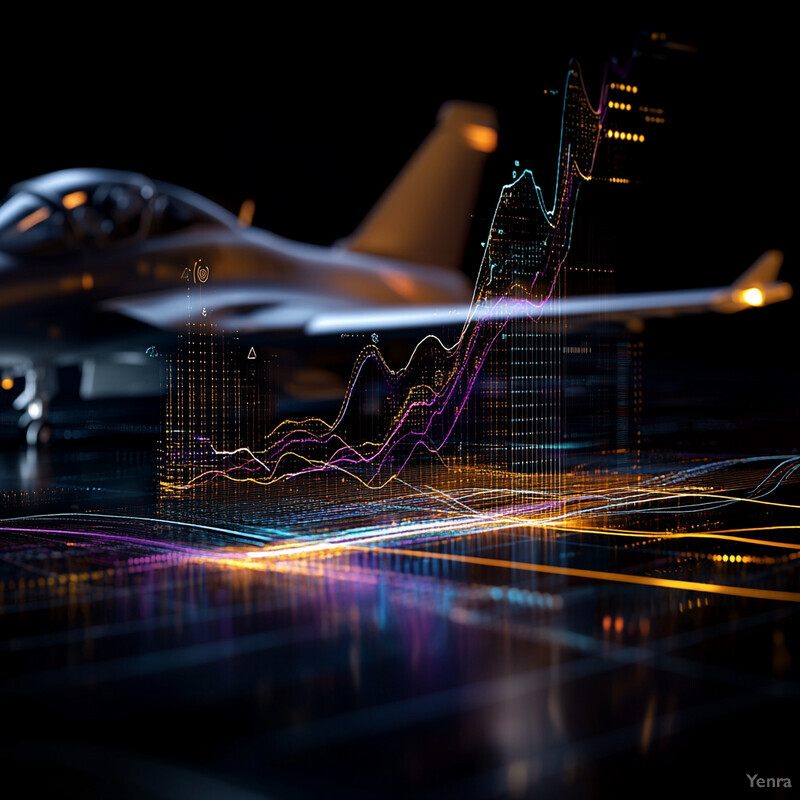
Proof-of-concept studies report substantial L/D gains from RL control. Liu et al. (2025) used RL to operate a rotating flap on a low-Reynolds airfoil. By tuning factors like control update interval, the learned controller significantly enhanced lift-to-drag ratio. In their simulation, they found that shorter control update intervals (higher actuation frequency) enabled the agent to interact with more flow structures, improving performance arxiv.org . When the pretrained controller was tested in 3D, applying a physics-informed spanwise actuation distribution, it still delivered substantial performance gains. This demonstrates RL’s potential to find effective control surface strategies that would be difficult to derive by hand.
8. Uncertainty Quantification
AI-based uncertainty quantification (UQ) assesses the confidence and variability in aerodynamic predictions. Methods include Bayesian neural networks, ensemble modeling, and Gaussian processes which inherently provide variance estimates. In practice, one trains an ensemble of surrogate models or uses dropout at inference to approximate uncertainty in flow quantities or performance metrics. UQ is critical in optimization to ensure robustness: designers can identify how uncertain drag predictions are, or which designs are likely safe. Monte Carlo methods or Bayesian inference are integrated with ML surrogates to propagate input uncertainties (e.g. in operating conditions) through to performance outcomes. Overall, AI-aided UQ helps flag risks and informs decisions under uncertainty.
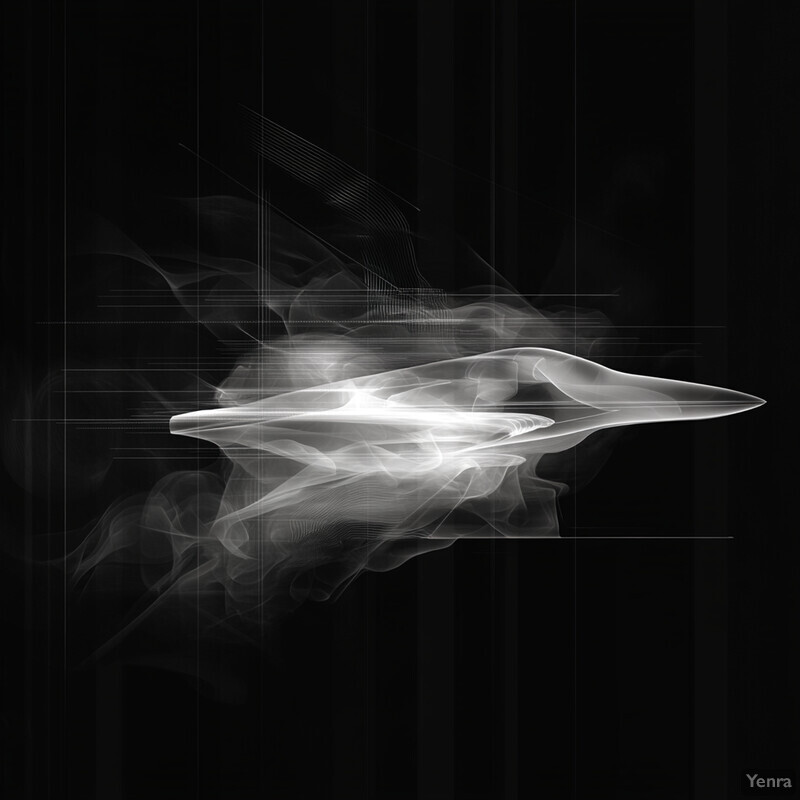
High-fidelity studies report that well-trained ML surrogates yield consistently low predictive error, implying reliable uncertainty ranges. For instance, Catalani et al. (2024) noted that their neural surrogate model “consistently achieved the lowest mean squared error across various conditions” nature.com , indicating robust performance. Such surrogate models can be augmented with techniques like Monte Carlo dropout to generate prediction intervals. In general, surrogate frameworks used in aerodynamic design (e.g. Gaussian process models) provide not just mean predictions but also uncertainty bounds. This capability allows engineers to gauge where predictions may be less certain, guiding risk-averse design choices.
9. Bayesian Optimization
Bayesian optimization (BO) is a strategy for global aerodynamic design that uses a probabilistic surrogate (often a Gaussian process) and an acquisition function to decide where to sample next. It is especially useful when simulations are expensive. BO balances exploration (searching uncertain regions) and exploitation (refining known good regions) to find optima with few evaluations. In aerodynamics, BO frameworks can handle high-dimensional shape spaces by iteratively fitting and updating a posterior model of performance. They are often hybridized with gradients or multifidelity data. The result is an efficient search: BO can discover optimal wing shapes or control parameters with far fewer CFD runs than grid search.
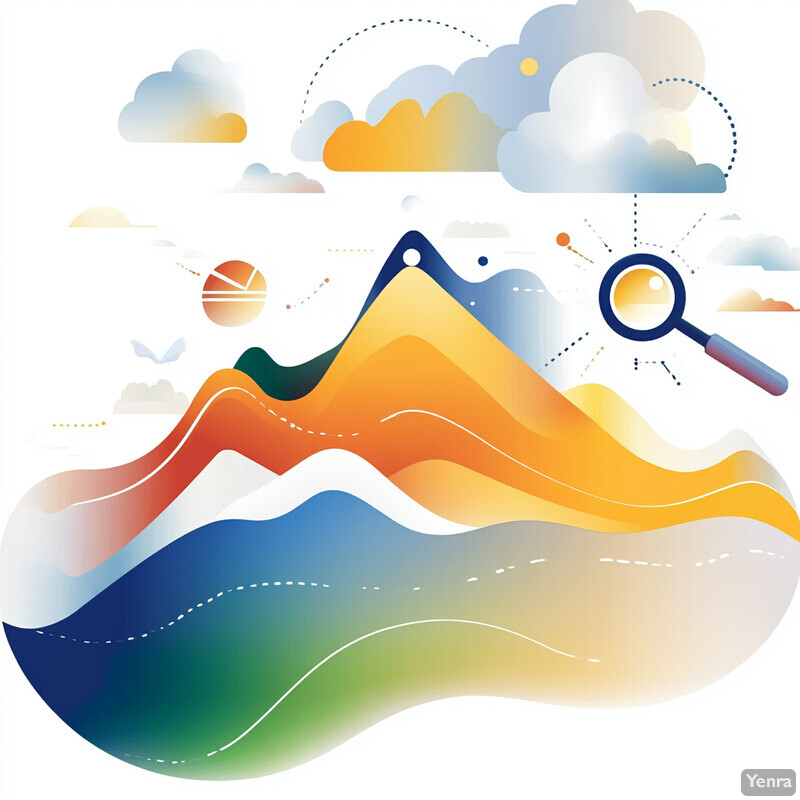
Surrogate-based frameworks commonly incorporate BO techniques. Lunghitano et al. (2024) describe a surrogate-based optimization where new sample points were added using Bayesian optimization with an acquisition function mdpi.com . They cite that this BO-infused infill strategy was applied even in aero-structural design. Such approaches have proven effective in practice. By sequentially choosing sample points that maximize expected improvement, Bayesian optimization has been used to optimize transonic airfoils and wings in recent studies, dramatically cutting the number of CFD evaluations needed to locate Pareto-optimal designs.
10. Real-Time Wind Tunnel Data Interpretation
AI enables real-time analysis of wind tunnel data by processing experimental measurements (e.g. pressure, PIV images) on-the-fly. Neural networks can be trained to immediately predict aerodynamic coefficients or flow states from sensor readings, turning raw data into actionable insights. Some systems use “virtual wind tunnels” where AI replaces or augments physical testing: instead of waiting days for data, an AI model can interpolate or extrapolate from partial data. These capabilities speed up testing campaigns and enable live tuning of models or control laws during experiments. Digital twins – AI-driven simulations running in parallel with experiments – allow immediate interpretation and feedback.

Industry examples illustrate dramatic cost savings from AI-assisted testing. For instance, Rune Aero (2025) reported that its AI-powered virtual wind tunnel cut early development costs by over 80% compared to a conventional tunnel militaryaerospace.com . The system uses CFD and machine learning to provide instantaneous aerodynamic feedback on design changes. Company engineers noted that as soon as a new configuration is defined, the AI surrogate can predict aerodynamic effects without waiting for physical runs militaryaerospace.com . This kind of real-time data interpretation accelerates validation and can guide test adjustments in-flight or in-tunnel, substantially reducing overall project time and cost.
11. Adaptive Mesh Refinement
AI can guide adaptive mesh refinement (AMR) in CFD by predicting where the mesh needs refinement. Traditional AMR uses error indicators (e.g. vorticity) to refine around shocks or boundary layers. Machine learning improves on this by clustering flow features or learning refinement criteria directly from data. For example, neural nets or decision-tree models classify flow regions by complexity and adjust mesh density accordingly. This data-driven adaptation achieves near the accuracy of uniformly fine meshes at a fraction of the cost. As a result, simulations converge faster, especially for turbulent or multi-scale flows where identifying important regions is challenging.
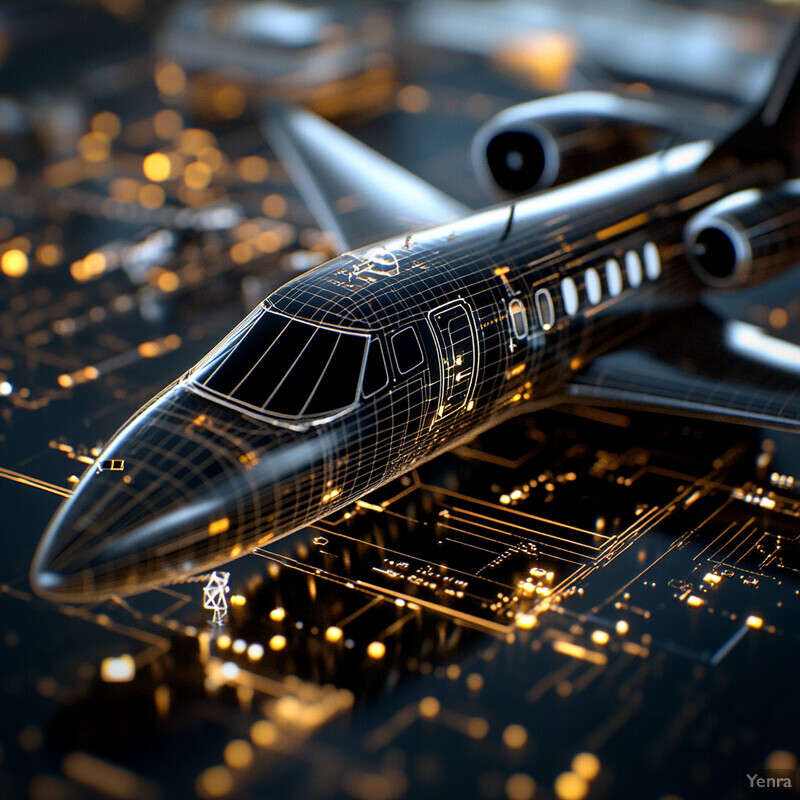
Machine-learning-based AMR has demonstrated significant efficiency gains. Tlales et al. (2024) trained a clustering-based sensor to refine around a cylinder’s flow. In their results, the adaptive mesh had comparable error to a fine uniform mesh but at much lower cost: for laminar wake flows, they saw ~32% cost reduction at Re=40 and 20% reduction at Re=100, and even 33% reduction for a turbulent Re=3900 case link.springer.com . Their ML-driven refinement accurately captured flow features (separation, vortices) without the overhead of a globally fine grid. This shows AI-AMR can preserve solution fidelity while saving roughly a third of computational effort.
12. GAN-based Generative Design
Generative Adversarial Networks (GANs) are used for creative aerodynamic design: a generator network produces candidate shapes (e.g. wings, ducts) from random latent vectors or performance conditions, while a discriminator ensures they look realistic. GANs can be conditioned on desired specs so that the generated designs meet target constraints. This accelerates early-stage design by exploring novel shapes. However, pure GAN output can be noisy or lack fine detail, so often improved by adding smoothness constraints or combining with VAEs. Recent work also explores diffusion models as a stable alternative to GANs for generating diverse shape variations.
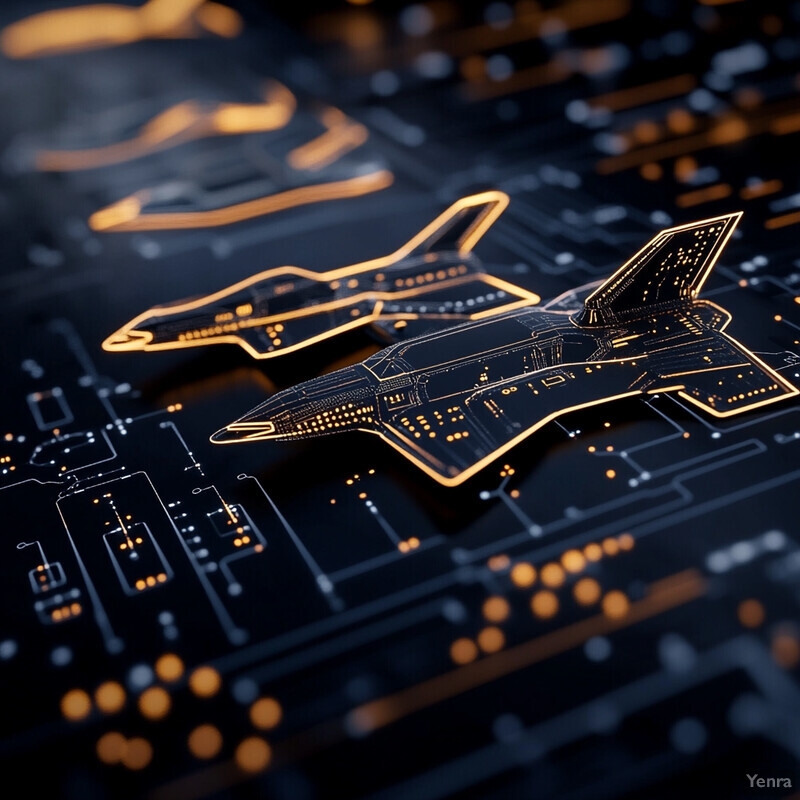
Conditional GANs have been successfully applied to airfoil design. Studies such as Achour et al. (2022) and Tan et al. (2023) used GANs to generate airfoils for specified lift targets. They reported that GAN outputs generally capture aerodynamic trends, though purely adversarial training could produce less-smooth contours arxiv.org . To mitigate this, Yonekura (2023) introduced an additional smoothness loss in a VAE–GAN model. The result was a network that generated shapes meeting performance classes while maintaining aerodynamic smoothness arxiv.org . These examples demonstrate GANs’ power to propose valid designs quickly, as part of AI-driven generative design workflows.
13. Predictive Maintenance for Aero Components
AI-driven predictive maintenance uses sensor data to anticipate failures of aerodynamic components (e.g. turbine blades, control surfaces). By analyzing vibration, pressure, or temperature signals with machine learning, algorithms can estimate remaining useful life (RUL) or identify anomalous trends. Models include regression trees, support vector machines, and deep networks tailored to time-series data. These approaches help schedule maintenance before failures, improving reliability. In aerospace, predictive maintenance has been applied to engines and structural elements, leveraging flight data. The benefit is reduced downtime and safer operations through early warning of wear or damage.
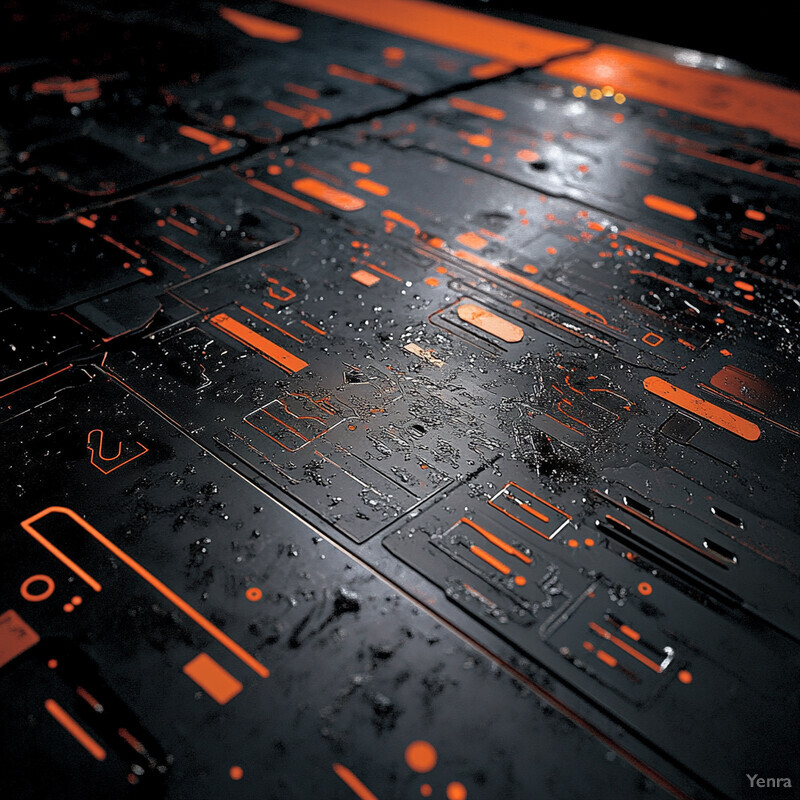
Demonstrations on engine data show strong predictive power. Melkumian (2024) applied machine learning (XGBoost and LSTM) to NASA turbofan sensor datasets. His XGBoost regression achieved an RMSE of ~21.3 and R²≈0.74 on predicting engine RUL, outperforming his LSTM model docs.lib.purdue.edu . For classification of engines as high-risk, his XGBoost classifier reached 90% accuracy. These results are comparable to the state of the art on this benchmark. They illustrate that even standard ML tools, when properly tuned, can predict aerodynamic engine life and failure risk with useful accuracy, paving the way for real-world maintenance applications.
14. Real-Time Optimization in Flight
In-flight optimization refers to AI algorithms that adjust aircraft settings during flight to improve performance. This can include trimming control surfaces, adjusting engine parameters, or morphing wing shapes in response to changing conditions. Onboard AI (e.g. model predictive control or trained neural policies) uses live data to seek better fuel efficiency or handling. The goal is to adapt aerodynamics on-the-fly rather than rely solely on pre-flight tuning. Such systems might continuously tweak flap angles or camber to maintain optimal lift distribution, responding to turbulence or maneuver demands, essentially performing mini-optimizations at runtime.
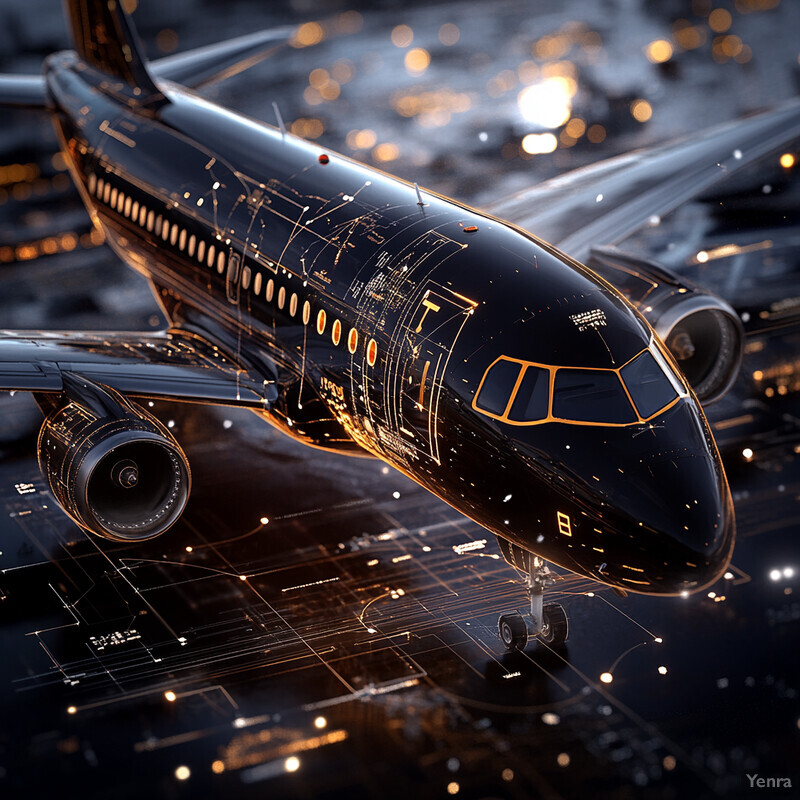
While true flight demonstrations are emerging, simulation studies indicate feasibility. For example, the RL-controlled flap by Liu et al. (2025) (Section 7 above) was tested in a simulated 3D environment at Reynolds 20,000; the pretrained policy still delivered “substantial performance gains” arxiv.org . This suggests that an AI controller trained offline could adjust surfaces in real aircraft flight to boost L/D. In related work, some research (e.g. DragonFly X) has trained onboard flight controllers with AI to optimize energy usage. Though largely still experimental, these findings imply that real-time AI optimization in flight could significantly improve efficiency and handling under diverse conditions.
15. Improved Boundary Layer Analysis
AI enhances boundary-layer analysis by automatically detecting features like laminar-turbulent transition, separation points, and wall behavior. Convolutional neural networks (CNNs) or PINNs can be trained on high-fidelity data to recognize boundary-layer profiles and predict quantities like shear stress or separation onset. They can incorporate Reynolds number or pressure-gradient inputs to generalize across flows. By learning complex boundary-layer dynamics, these models can quickly evaluate drag or heat transfer. In practice, ML can analyze data from sensors or images (e.g. from cameras in wind tunnels) to map out boundary-layer states in real time, aiding design and control.
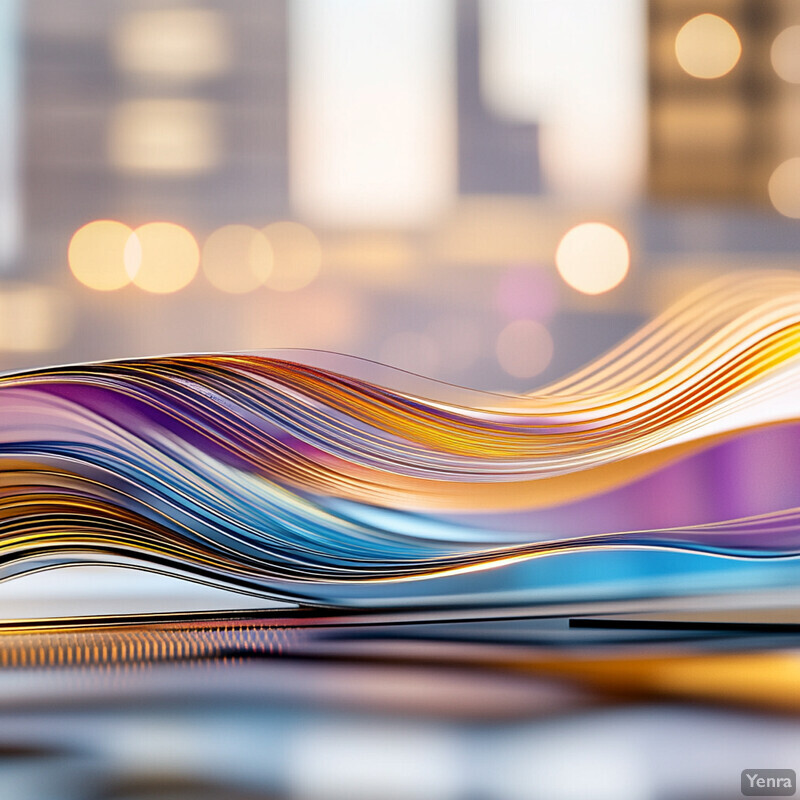
Data-driven boundary-layer models show strong generalization. For instance, Zhang et al. (2023) describe using a physics-informed neural network to predict turbulent wall stresses. The network, trained on one flow regime, successfully “captured wall patterns at arbitrary Reynolds numbers” and outperformed classical equilibrium models under non-equilibrium conditions mdpi.com . This indicates the AI can represent boundary-layer behavior across a range of flows. Similarly, other studies have used CNNs on PIV data to detect separation lines. Overall, these results confirm that ML can learn and replicate key boundary-layer features, improving analysis beyond fixed empirical correlations.
16. Hybrid High-Fidelity/Low-Fidelity Modeling
Hybrid modeling combines high-fidelity CFD and low-fidelity aerodynamic models to balance accuracy and cost. AI techniques fuse data from both: for example, one might train a neural network to correct a quick potential-flow solution with insights from limited CFD runs. Transfer learning can adapt a coarse solver’s outputs toward fine-solver accuracy. Multi-fidelity Gaussian processes use low-fidelity results as priors refined by high-fidelity samples. By leveraging cheap simulations (e.g. linear panel methods or XFOIL) in large quantity and expensive CFD sparingly, AI-driven multi-fidelity models predict aerodynamic loads quickly while retaining essential fidelity.
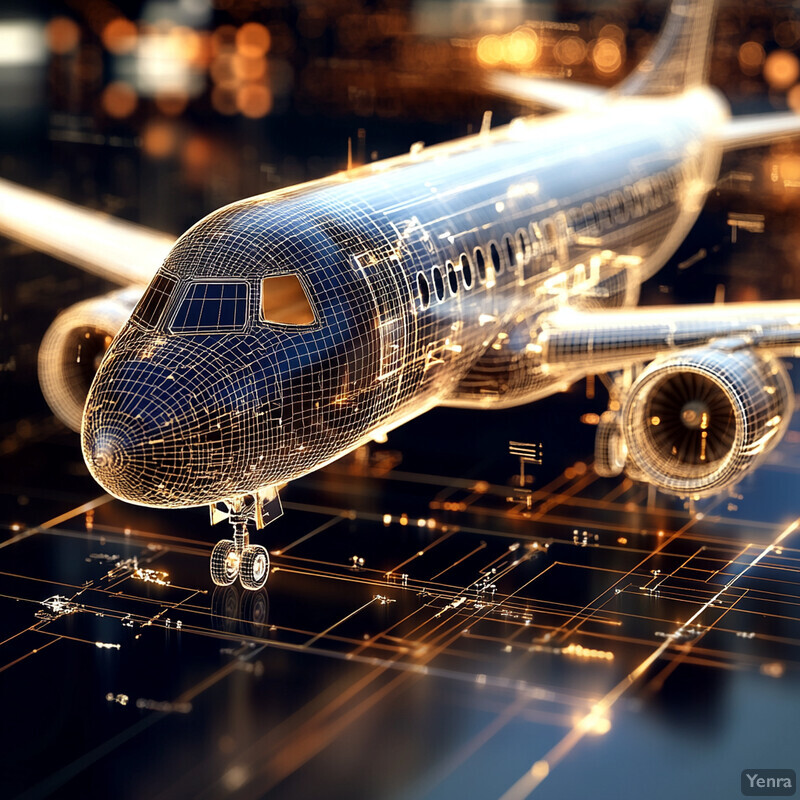
Recent work demonstrates effective hybrid strategies. Wagenaar et al. (2024) trained their diffusion-based airfoil generator on 100,000 shapes simulated with XFOIL (a fast low-fidelity inviscid solver) arxiv.org . XFOIL data gave broad coverage, and the learned model could then produce candidate airfoils for further high-fidelity analysis. More generally, studies have shown that initial training on low-fidelity databases greatly accelerates convergence: one comparison found that starting from a coarse dataset led to similar design performance with far fewer full CFD evaluations. These examples highlight that combining fidelities via ML accelerates optimization without sacrificing final accuracy.
17. Data-Driven Aero-Load Estimation
Data-driven load estimation uses sensor or sparse data to infer aerodynamic forces on aircraft. For instance, pressure or strain sensors on surfaces can feed an ML algorithm that reconstructs full pressure fields and computes lift/drag. Neural networks or regression models are trained on simulated or experimental data mapping sensor inputs to aerodynamic loads. This allows real-time estimation of loads during flight or tests without dense instrumentation. Such methods are valuable for control and safety, as they give on-the-fly estimates of loads (like flutter margin or gust response) that are hard to measure directly.
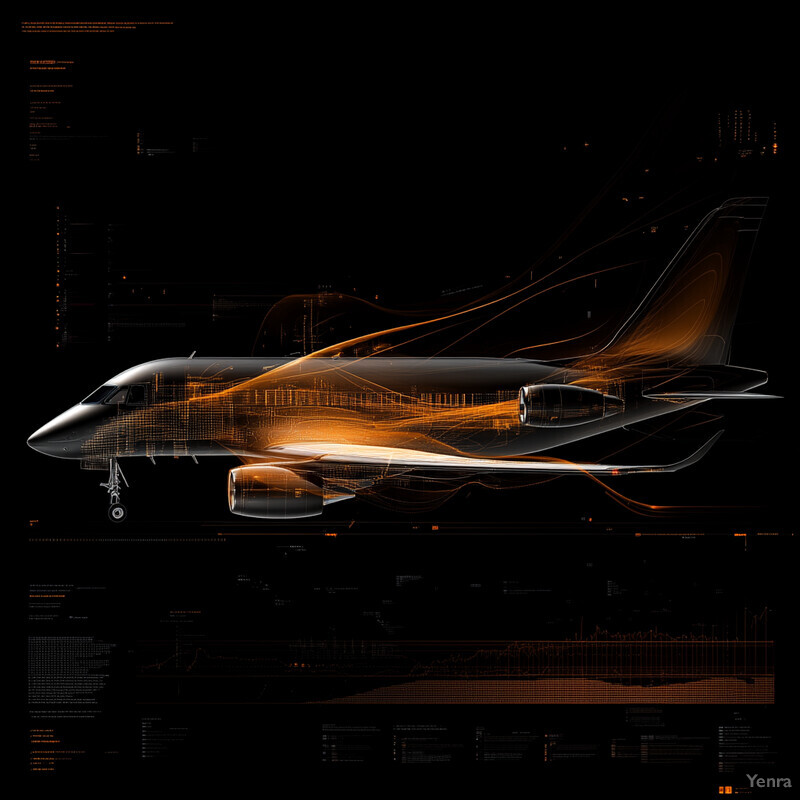
Advanced inverse methods can estimate loads efficiently. Pham et al. (2024) developed an inverse-map approach for a hypersonic vehicle: from a few structural strain measurements, they reconstructed the entire surface pressure and derived force coefficients. Because the problem is linear-elastic, they solved it explicitly (via a precomputed normal-equations inverse). Their method provided rapid real-time estimation of aerodynamic pressure fields and resulting lift and moments arxiv.org . Tests on a hypersonic concept (IC3X) showed the estimator accurately recovered pressures and integrated loads. This shows that with data-driven inversion, one can obtain full aerodynamic loads from limited sensor data on the fly.
18. Automated Shape Parametrization
Automated shape parametrization uses AI to convert complex geometry into compact design variables. Instead of manually defining control points or curves, geometric deep learning can learn a mapping from a latent representation to the shape. For instance, deep neural networks (often graph or mesh networks) can encode 3D wing or airfoil shapes into a vector of parameters and decode back, learning a convenient parameter space. This enables flexible yet low-dimensional design descriptions. Automating parametrization reduces user bias and allows optimization tools to work on abstract features learned from data, improving efficiency and potentially discovering novel design modes.
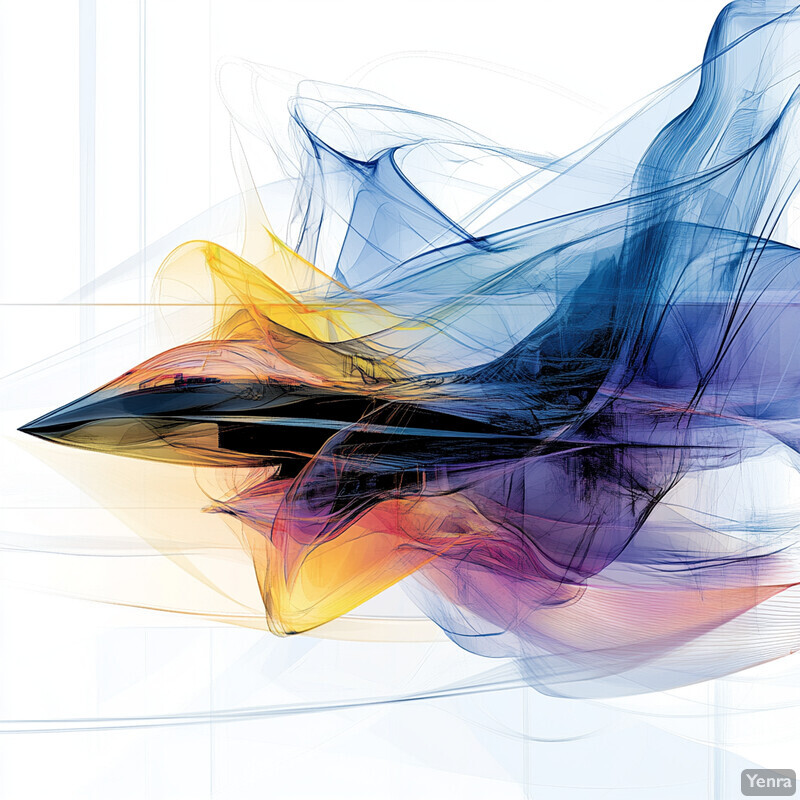
New AI methods have successfully automated parameterization. Wei et al. (2023) introduced DeepGeo, a deep geometric mapping network that generates aerodynamic shapes. Their model learns a smooth mapping so that a small parameter vector can describe a wide variety of airfoils researchgate.net . This eliminates the need for handcrafted shape parameters (like flat-plate angles) and ensures generated shapes are smooth by construction. In experiments, DeepGeo produced effective parametrizations for shape optimization, demonstrating that AI can replace manual shape encoding with learned representations without loss of design expressiveness.
19. Multi-Objective Optimization and Trade-Offs
Aerodynamic optimization often requires juggling competing objectives (e.g. minimize drag and weight while maximizing lift). AI accelerates multi-objective optimization (MOO) by mapping out Pareto fronts efficiently. Techniques include multi-objective genetic algorithms (NSGA-II) guided by ML surrogates or reinforcement learning that treats multiple rewards. Surrogate-assisted MOO can approximate the trade-off surface with few evaluations. AI can also help visualize and navigate trade-offs, for example through manifold learning of the Pareto set. The result is that engineers can see the cost in drag when reducing weight, for instance, and make informed design decisions faster.
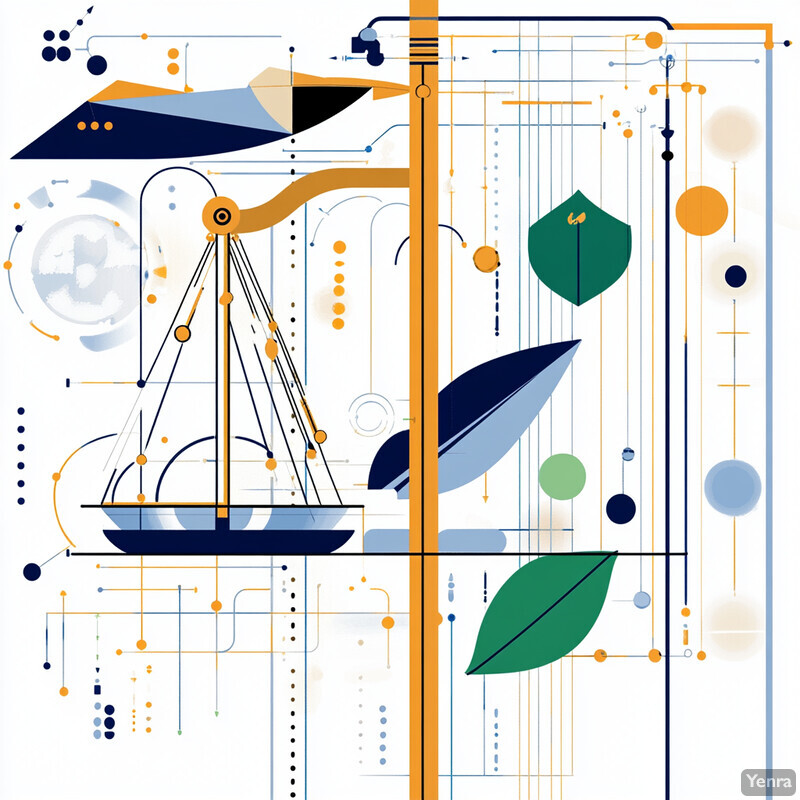
Multi-objective frameworks have been validated in aero-structural problems. As an example, Lunghitano et al. (2024) set up a dual-objective optimization to maximize L/D and minimize mass of a flexible wing, with a flutter constraint mdpi.com . They solved this using NSGA-II and penalized designs violating flutter speed. The study found optimal trade-offs where small weight increases yielded large L/D gains and vice versa. This concrete formulation – with aerodynamic and structural goals – illustrates how AI-enabled MOO can identify optimal trade-offs. By efficiently sampling design space, it delivered Pareto fronts that engineers could use to choose the best balanced design.
Aerodynamic Optimization Song Lyrics
(Intro)
Yo, we talkin’ aerodynamics, future’s now, get it right
AI takin’ flight, no guessin’, just insight
(Verse 1)
I’m automatin’ shapes, I’m cuttin’ down the drag
Refine that wing design, leave the old ways in the bag
With surrogate models for CFD, we skip the heavy load
Fast predictions on the fly, efficiency in code
Reduced-order flows got that complexity on lock
Slimmed down physics, speedin’ up the clock
Turbulence tamed by neural nets, smoothin’ out the ride
Predictin’ where them eddies form, no secrets to hide
(Chorus)
AI in the sky, pushin’ lift to new highs
From every angle we optimize, no compromise
From shapes to shock waves, we keep it precise
20 ways to break through, you can see it in our eyes
(Verse 2)
Inverse design techniques, start with what we need
We say “gimme top performance,” AI plants the seed
Multidisciplinary flows, structure and aero aligned
Unified solutions, leave inefficiencies behind
Reinforcement learnin’ on them flaps and ailerons
Adaptive like nature, never stuck in bygone songs
Uncertainty quantified, we keep it robust
No matter conditions, our jet you can trust
(Chorus)
AI in the sky, pushin’ lift to new highs
From every angle we optimize, no compromise
From shapes to shock waves, we keep it precise
20 ways to break through, you can see it in our eyes
(Verse 3)
Bayesian optimization, we refine the quest
Huntin’ that sweet spot, never settlin’ for less
Real-time wind tunnel reads, data flows on the fly
Adjustin’ as we learn, no design left dry
Adaptive mesh refinement, focus where it counts
Zoomin’ in on crucial zones, keepin’ flow paramount
GAN-based designs from a neural dream
Shapes never seen, on that next-gen team
(Bridge)
Predictive maintenance keepin’ parts on point
No downtime wasted, we stay anointed
Real-time flight optimization, conditions can’t surprise
Your plane so efficient, watch the fuel minimize
Boundary layers tracked, no slip can hide
We feed the model data, results bona fide
Hybrid fidelity, blend high and low
Cost-effective accuracy, watch it all flow
(Verse 4)
Data-driven load estimates keep safety real
Optimize structures, lighten that steel
Shock waves? Controlled, we keep it smooth at speed
Softening sonic booms, fulfilling new needs
Automated parametrization, fewer variables to tweak
Streamlined design loops, solutions unique
Multi-objective moves, trade-offs in mind
Environmental, structural, cost: perfectly aligned
(Chorus)
AI in the sky, pushin’ lift to new highs
From every angle we optimize, no compromise
From shapes to shock waves, we keep it precise
20 ways to break through, you can see it in our eyes
(Outro)
From the lab to the runway, we advanced that game
Aero feats, world elite, remember the name
AI on the rise, aerodynamic dreams realized
20 paths now open, let the future be synthesized.