1. Enhanced Precision and Accuracy
AI significantly boosts the precision and accuracy of industrial robots. By processing sensor data and learning from past performance, AI algorithms enable robots to execute tasks with finer tolerances and greater consistency than traditional programming alone. This leads to fewer errors in processes like assembly, welding, and machining. Enhanced accuracy not only improves product quality but also reduces waste and rework. In sensitive applications (such as electronics or medical device manufacturing), AI’s ability to adjust a robot’s movements in real time helps meet extremely tight specifications reliably. Overall, integrating AI allows industrial robots to perform intricate tasks with repeatable exactness, improving yield and productivity in manufacturing environments.
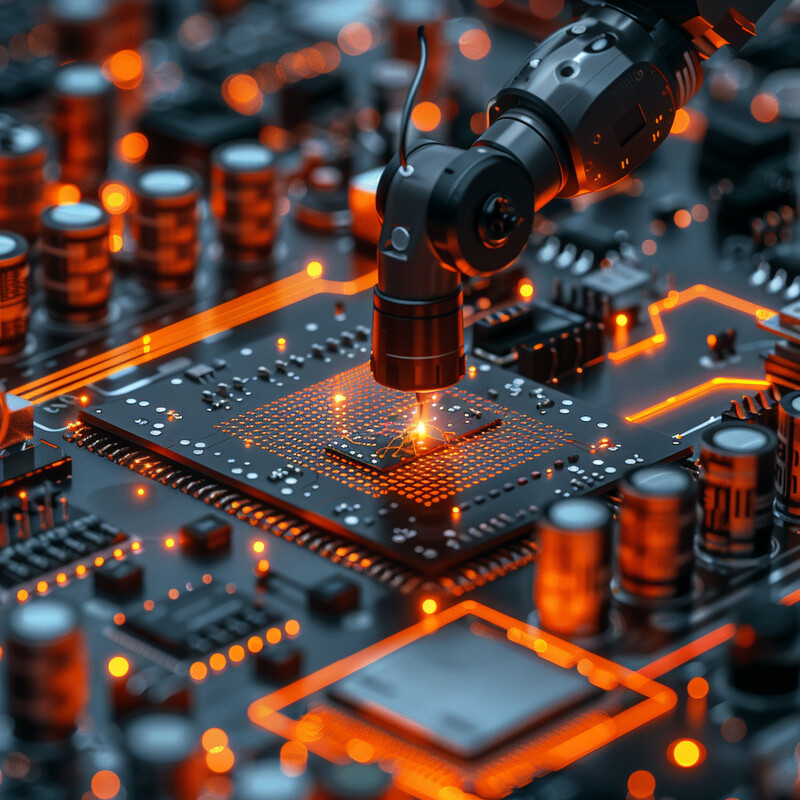
AI-driven robotic systems have achieved remarkable levels of accuracy in real-world deployments. For example, an AI-powered warehouse sorting robot system improved its sortation precision to 99.6% accuracy in 2024, dramatically reducing mis-sorted items. This high accuracy was attained by using machine learning models to optimize the robot’s motions and error-checking in real time. Such precision marks a significant improvement over earlier generations of robots and manual processes. In practical terms, reaching 99%+ accuracy means far fewer defects or mistakes per thousand operations, translating to cost savings and higher throughput. This case demonstrates how AI allows robots to handle tasks—like identifying and placing a wide variety of items—with near-perfect accuracy, showcasing the potential for AI to elevate industrial processes to unprecedented quality levels.
2. Adaptive Learning
AI enables industrial robots to learn and adapt, rather than just repeat preset routines. Through machine learning techniques (including reinforcement learning and neural networks), robots can improve their performance over time by analyzing data from each task execution. This adaptive learning means robots can handle variability in parts or processes – for instance, adjusting to new product designs or changes in the environment – without extensive reprogramming. By generalizing from prior experiences, AI-powered robots can tackle multiple different tasks and even transfer skills from one job to another. This flexibility leads to faster integration of robots into new workflows and continuous improvement in how they operate. In essence, AI gives robots a form of “experience,” allowing them to refine their actions and decision-making much like a human worker gaining expertise, which is invaluable in dynamic manufacturing settings.

A striking example of adaptive learning in robotics is DeepMind’s RoboCat AI model unveiled in 2023, which learned to solve a wide range of tasks across different robotic arms. Unlike traditional robots that require manual reprogramming for each new task, RoboCat uses a general learning approach to master new skills. In testing, a single AI model was able to learn over 250 distinct manipulation tasks – from picking up novel objects to stacking blocks – and could adapt to new tasks with as few as 100 demonstrations. Its task success rates ranged up to 99% on certain challenges after sufficient training. This means the robot quickly improved at tasks by iteratively learning, and it could even teach itself further by generating additional training data. Such results illustrate how AI’s adaptive learning capability allows robots to handle diverse operations and improve rapidly, reducing the need for human engineers to intervene for every new product or scenario.
3. Predictive Maintenance
AI is revolutionizing maintenance of industrial robots and machinery by predicting issues before they cause downtime. In traditional factories, equipment failures can halt production unexpectedly, leading to costly downtime and repairs. AI-driven predictive maintenance uses sensor data, machine learning, and analytics to continuously monitor the health of robots and other machines. By recognizing patterns and anomalies (for example, a motor vibration or temperature trend that deviates from normal), AI systems can forecast when a component is likely to fail or require service. Maintenance can then be performed proactively at a convenient time, rather than reactively after a breakdown. This approach minimizes unplanned downtime, extends the lifespan of equipment, and optimizes the use of spare parts and labor. Ultimately, AI-powered predictive maintenance improves reliability and reduces the overall cost of ownership for industrial robotic systems by addressing problems before they escalate.
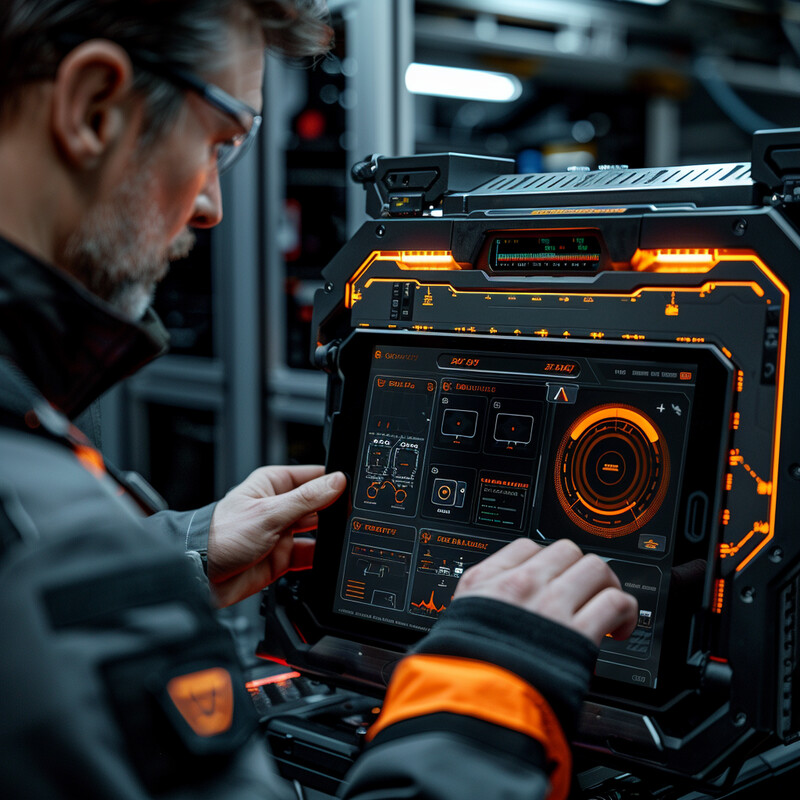
Studies show that AI-driven predictive maintenance yields substantial efficiency gains in industry. According to a report by McKinsey & Company, employing AI and IoT for predictive maintenance can reduce unplanned maintenance costs by 10–40% and cut unplanned downtime by up to 50%, while also extending the working life of machines by 20–40%. For example, sensors on a robotic arm might detect slight increases in motor current and alert an AI system, which then predicts a bearing wear issue days or weeks before failure. The maintenance team can replace the bearing during scheduled downtime, avoiding a sudden line stoppage. The automotive sector illustrates the high stakes: an hour of unexpected downtime in an auto parts factory is estimated to cost about $1.3 million in losses, underscoring the value of preventing breakdowns. By leveraging AI to anticipate such problems, manufacturers save tremendous costs and keep production on schedule. These statistics highlight how predictive maintenance powered by AI is a game-changer for industrial operations, significantly improving uptime and efficiency.
4. Autonomous Decision-Making
AI enables industrial robots to make autonomous decisions in real time, increasing their independence and usefulness in complex situations. Traditional robots follow predefined instructions and can struggle when conditions change or when they encounter something unexpected. In contrast, AI-equipped robots can interpret sensor inputs on the fly – such as camera images or force feedback – and decide how to adjust their actions without human intervention. This capability is crucial for tasks like autonomous navigation in a warehouse, dynamic assembly adjustments, or real-time quality control. For instance, an AI-powered robot can reroute itself if an obstacle appears, or change the force it applies to tighten a bolt if it detects resistance. Autonomous decision-making reduces the need for constant human oversight, allowing robots to handle variability and uncertainty in their environment. This leads to “smarter” factories where robots coordinate with each other and respond to production changes instantly, improving overall agility and productivity. AI-driven autonomy is a key stepping stone toward fully “lights-out” manufacturing facilities that can run 24/7 with minimal human supervision.
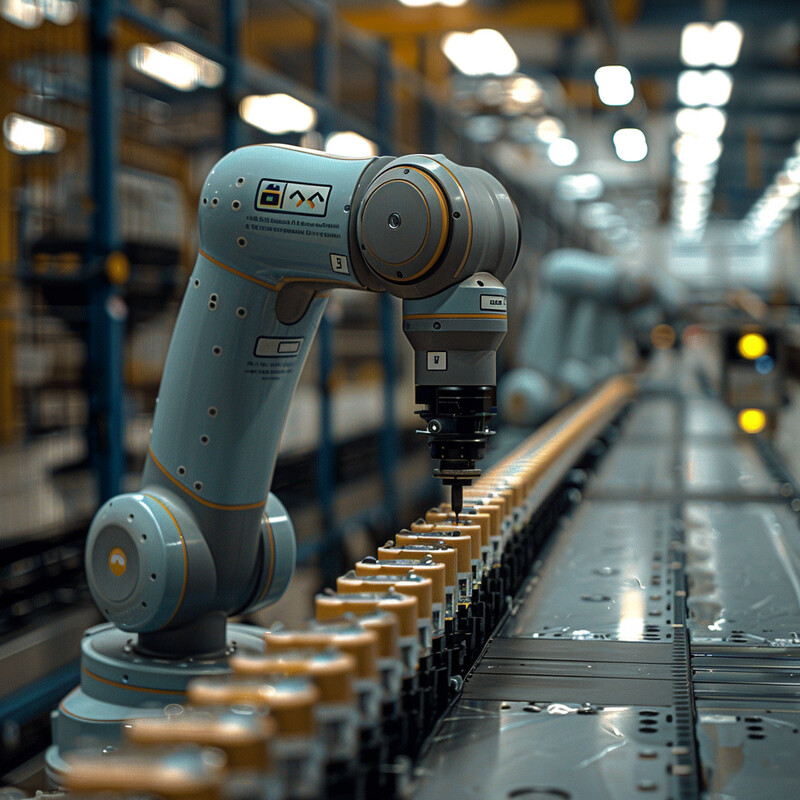
The industrial sector is rapidly embracing AI for robotic autonomy, underscoring its importance. North America’s market for AI-powered industrial robotics is projected to grow at over 25% annually from 2024 to 2030, driven by demand for smart factories and automation that can adapt in real time. This high growth rate reflects manufacturers’ eagerness for robots that don’t just blindly follow code, but can make intelligent decisions on the shop floor. Concrete examples include the deployment of autonomous mobile robots (AMRs) in warehouses: these AI-guided robots independently navigate and distribute materials, with the global installed base expected to exceed 500,000 units by 2030 as adoption expands. Major companies are already operating large autonomous robot fleets – for instance, Amazon now uses more than 750,000 robots in its fulfillment centers to sort and move goods, coordinating their actions via AI software. The rapid market growth and deployment scale show that autonomous decision-making by robots is becoming mainstream, enabling faster workflows and more resilient operations.
5. Collaborative Robotics (Cobots)
Collaborative robots, or cobots, are a class of industrial robots designed to safely work alongside humans, and AI is enhancing their capabilities. Cobots are typically smaller, have force-limited joints, and are equipped with sensors to detect and avoid collisions, allowing them to share workspaces with people. AI plays a role by enabling cobots to be more responsive and intuitive – for example, using computer vision to recognize human co-workers or objects, and machine learning to improve how they assist in tasks. In manufacturing settings, cobots handle repetitive or ergonomically challenging jobs (like precise assembly, machine tending, or packaging) while humans perform more complex decision-making tasks, resulting in a human-robot team that is more productive than either alone. AI helps cobots learn from demonstration (so an operator can show a cobot a new task) and adjust to variability in real time. The outcome is increased flexibility on the factory floor, improved worker safety and ergonomics, and higher overall throughput. Rather than replacing workers, AI-powered cobots augment the human workforce, taking over mundane tasks and allowing people to focus on skilled work.
-3.jpg)
The adoption of collaborative robots in industry has been accelerating in recent years. In fact, over 1 in 10 new industrial robots installed worldwide in 2023 was a collaborative robot. According to the International Federation of Robotics, cobots accounted for 10.5% of the 541,000+ industrial robots deployed in 2023, up from virtually negligible levels a decade prior. This percentage represents tens of thousands of cobots integrated into factories in just that year, and the share is expected to continue growing. The rapid rise is driven by improvements in AI and sensor technology that make cobots safer and easier to program. For example, many cobots now feature hand-guiding teaching modes and intelligent force control (thanks to AI algorithms), which lower the programming barrier and let smaller manufacturers automate tasks without specialized engineers. Industries from automotive to electronics are increasingly using cobots on assembly lines and packaging stations, often to work in tandem with humans. The 2023 data underlines that collaborative robots are no longer a niche concept but a significant and growing portion of automation investments, enabled by AI to be reliable partners for human workers.
6. Vision Systems
Vision systems augmented by AI have become critical to modern industrial robotics, giving machines the ability to “see” and interpret visual data. Traditional machine vision could detect simple features or differences based on hard-coded criteria, but AI (especially deep learning) has dramatically improved a robot’s visual recognition capabilities. Now, robots equipped with AI vision can identify objects, defects, or patterns with human-like (or better) accuracy. This is used in quality inspection (spotting tiny defects or assembly errors), guiding robotic arms (by locating parts and determining their orientation), and allowing robots to sort or pick varied items. AI vision systems can also adapt to changes – for instance, recognizing a new product type on the conveyor after being trained on images. The result is a more flexible and reliable automation: manufacturing lines achieve higher quality control, warehouses can have robots that handle a wide mix of products, and operations like welding or painting can be adjusted on the fly by “looking” at the workpiece. Overall, AI-powered vision gives robots a rich understanding of their environment, enabling smarter and more autonomous decision-making in industrial processes.
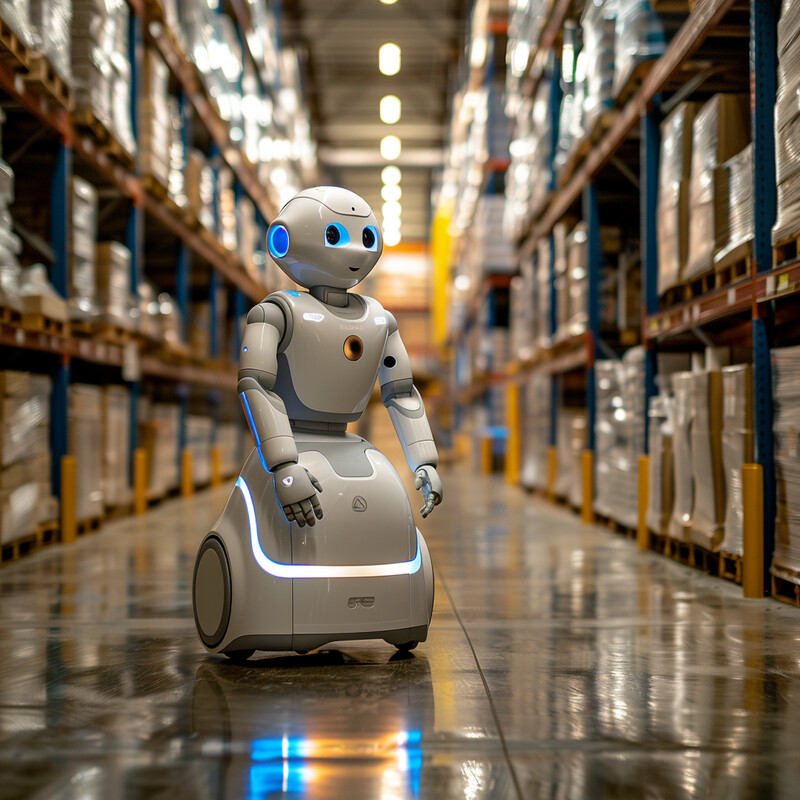
AI vision technology has greatly improved both the effectiveness and efficiency of industrial quality control. For example, one semiconductor manufacturer that implemented an AI-based visual inspection system saw an 80% reduction in labor costs for inspection tasks. Previously, this company required 12 human inspectors working in shifts around the clock to examine product images for defects. After deploying an AI vision solution, the automated system could detect and classify defects with consistent accuracy, drastically cutting the need for manual review. This not only saved labor expenses but also increased inspection speed and consistency. More broadly, the market data reflects how pervasive vision systems have become in automation: over half of all 2D machine vision applications (around 52%) in 2022 were for quality checks and inspections, by far the largest use-case segment. This shows that manufacturers are heavily investing in AI-driven vision for error detection and quality assurance. The combination of high precision (catching subtle flaws that humans might miss) and high throughput (examining products faster than people) makes AI vision indispensable. These statistics underscore how integrating AI into robotic vision yields major improvements in manufacturing quality and efficiency.
7. Increased Flexibility
AI is greatly increasing the flexibility of industrial robotics, allowing production lines to handle a wider variety of products and rapid changeovers. In the past, robots were typically hard-programmed for a specific task – any change in product design or process could lead to lengthy reprogramming and downtime. Now, AI-driven approaches (like intuitive programming interfaces, machine learning, and simulation/digital twins) enable robots to be reconfigured quickly. Robots can learn new tasks from data or demonstration, meaning a single robotic cell can perform multiple functions or switch between different product models on the fly. This flexibility is crucial for modern manufacturing trends such as mass customization and shorter product life cycles, where production needs can shift frequently. With AI, a factory can introduce a new variant of a product and update the robot’s instructions in hours instead of weeks, often using simulation software to fine-tune changes virtually. Additionally, AI helps robots adapt to variability in parts (for example, slight differences in position or shape) without stopping production. All of this leads to more agile factories that can respond to market demands swiftly, using the same robotic equipment for many purposes. Flexible automation reduces the need for specialized machinery for each product, maximizing the utilization of robots and investment.
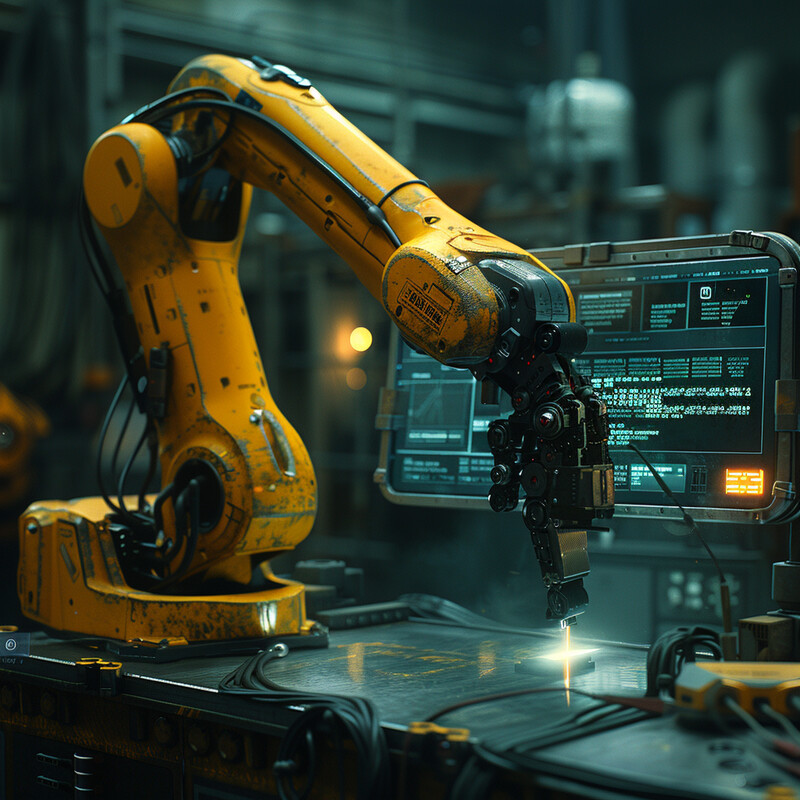
Industry leaders consider flexibility enabled by AI and robotics to be a strategic priority for the coming years. In a 2025 global survey of automotive manufacturers – a sector known for rapid model changes – 84% of respondents said that fully flexible, AI-driven manufacturing will be a significant factor within the next five years. Automakers anticipate needing to build electric, hybrid, and traditional vehicles on the same production lines, and they view advanced robotics and AI as the solution to manage this complexity. This reflects a broader trend across manufacturing: nearly all manufacturers (92% in a 2024 Deloitte study) believe smart factory initiatives (which include AI and flexible automation) are key to competitiveness in the next 3–5 years. Real-world examples of increased flexibility are already evident. Some factories use AI to enable production of dozens of product variants with minimal human intervention – robots can automatically adjust to different dimensions or assembly sequences as needed. Companies like ABB have introduced “lead-through teaching” and AI-assisted programming for cobots, so even small firms can quickly repurpose a robot for new tasks. The strong consensus in surveys and the emergence of such technologies underscore that AI-fueled flexibility is transforming manufacturing, making production lines more adaptable than ever before.
8. Integration with IoT
The integration of Industrial Internet of Things (IIoT) with AI and robotics is unlocking new levels of connectivity and smart automation in factories. IIoT refers to networks of sensors, devices, and machines (including robots) that are connected to share data and insights. When industrial robots are integrated with IoT infrastructure, they become part of a connected ecosystem – machines can communicate their status, receive remote instructions, and coordinate with other equipment in real time. AI plays a central role by analyzing the large streams of data collected from these connected devices to optimize operations. For example, data from multiple robots and sensors on a production line can be aggregated and analyzed by an AI system to find bottlenecks or inefficiencies, which then can be corrected by adjusting robot workflows. Integration with IoT also enables remote monitoring and control: engineers can track robot performance via dashboards and deploy AI algorithms from the cloud to improve motion planning or energy usage. Essentially, IoT connectivity turns isolated robots into smart nodes in a larger intelligent factory. This leads to benefits like adaptive scheduling (robots adjusting their tasks based on supply chain data), real-time quality control across the line, and easier scalability of automation solutions. As more factories adopt IIoT and AI, we see the emergence of truly “smart factories” where every robotic system and sensor works in concert, guided by AI-driven analytics for continuous improvement.
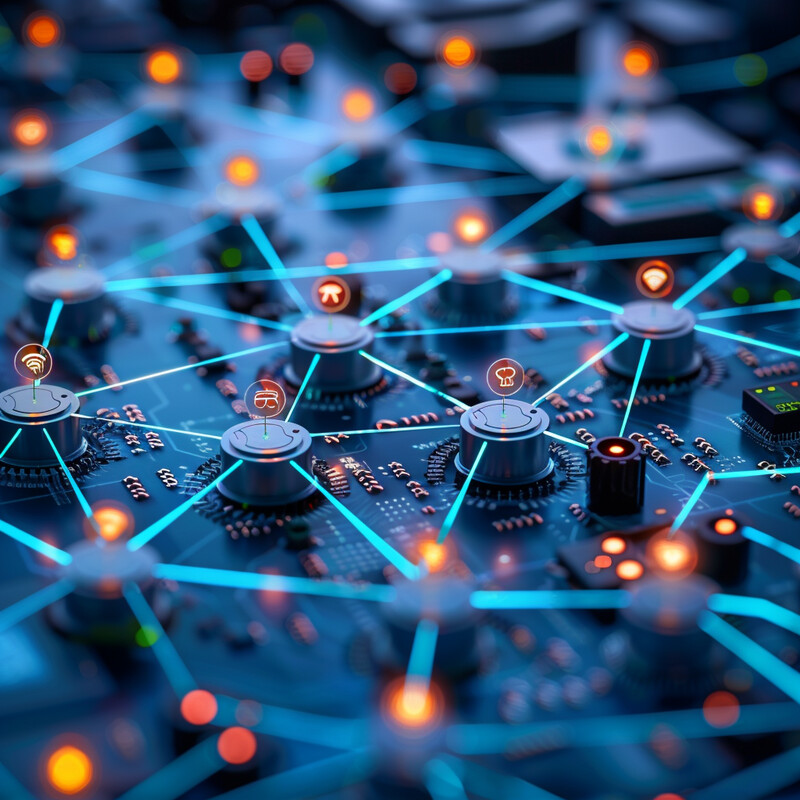
Recent industry surveys highlight a strong momentum toward IoT-connected, AI-enhanced manufacturing. As of 2024, 74% of industrial companies have deployed or are developing an IIoT (Industrial Internet of Things) strategy, reflecting widespread commitment to connected operations. Importantly, almost half of these firms are integrating AI and machine learning into their IIoT systems to enable intelligent automation and data-driven decision-making. This convergence means that many manufacturers are not just collecting data from machines, but also applying AI analytics to that data in real time. For instance, a network of IoT sensors might monitor temperature and speed of dozens of robots on a production floor; AI algorithms analyze this data to dynamically adjust each robot’s operating parameters for optimal throughput. In practical applications, one large consumer goods manufacturer reported that combining IoT data from its production lines with AI analysis improved its Overall Equipment Effectiveness (OEE) by identifying previously unseen causes of micro-downtime. Additionally, integration with IoT allows easier predictive maintenance across an entire factory: AI can sift through data from hundreds of connected machines to predict issues (as discussed earlier), scheduling maintenance across the facility efficiently. The high adoption rates indicated by the survey show that companies recognize the value of marrying IoT infrastructure with AI – creating smart, interconnected production environments that elevate performance and responsiveness.
9. Energy Efficiency
AI is helping industrial robotics become more energy-efficient, which is increasingly crucial as manufacturers seek to cut costs and meet sustainability goals. Robots and automated systems consume energy through their motors, controllers, and auxiliary systems; traditionally they were operated at full power even when not actively working. AI introduces smarter energy management by optimizing robot motions and idle times. For example, AI algorithms can plan the most efficient path for a robot arm that minimizes unnecessary movement, thus reducing energy use per task. AI-driven control systems can also put robots into automatic “sleep” or low-power modes when they detect no work is present, and wake them as needed. Furthermore, AI can coordinate multiple robots and processes to smooth out power demand, avoiding spikes in energy consumption. Some advanced robot controllers now even regenerate energy (like braking energy) and AI decides how to reuse or store it. In essence, AI enables a more nuanced control over robot operations, ensuring they consume just the necessary amount of electricity and not more. The benefits are twofold: companies save on energy costs, and the overall carbon footprint of manufacturing is reduced. Especially in large-scale facilities with hundreds of robots, these savings add up significantly. As energy prices rise and regulations on emissions tighten, AI-based energy efficiency measures in robotics are becoming an important aspect of modern industrial automation.
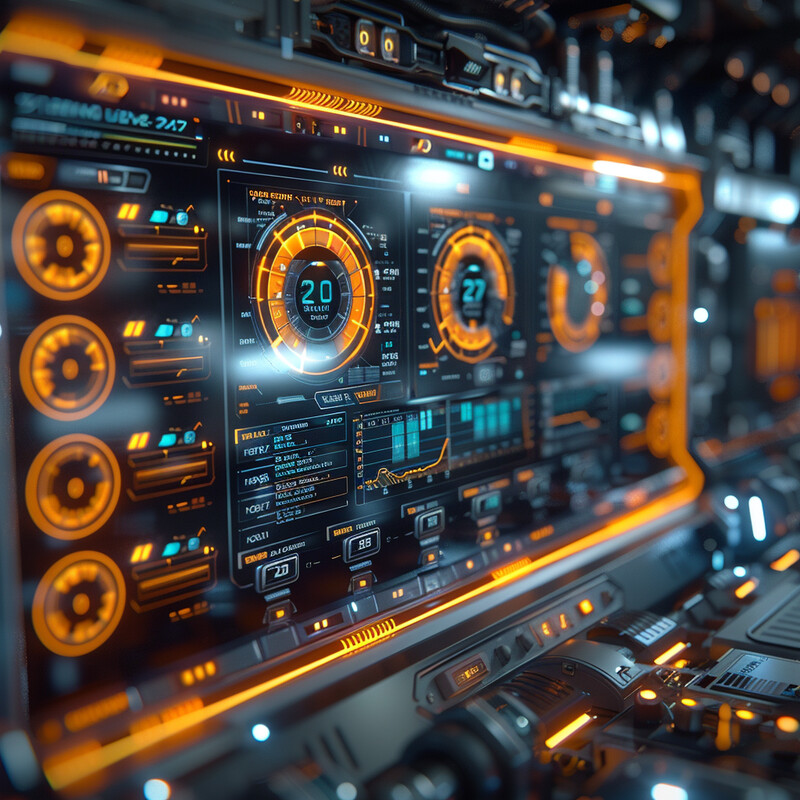
Manufacturers are seeing tangible energy savings by applying AI and analytics to their robotic systems. A recent program by a leading robotics provider found that optimizing robot performance with AI-based analysis can cut energy consumption by up to 30% for those robots. For instance, ABB Robotics reported in 2024 that its new Energy Efficiency service—using data insights to fine-tune robot operations—helped clients identify nearly one-third reduction in power usage without sacrificing output. These savings come from measures like automatic standby modes and smoother motion profiles determined by AI. The drive for energy efficiency is widespread: in a global survey, 93% of industrial companies indicated they plan to invest in energy efficiency improvements for their facilities in the next three years, and a majority specifically cite reducing energy costs as key to remaining competitive. This has led to innovations such as AI-controlled “smart grids” within factories, where robotic workcells draw power in a balanced way to avoid peaks, and intelligent scheduling where energy-intensive tasks are done at off-peak utility hours. Additionally, AI helps in maintenance that keeps equipment running at optimal efficiency (e.g., ensuring motors aren’t working harder due to wear). The up to 30% energy reduction figure demonstrates that significant efficiency gains are achievable. With near-universal corporate focus on this issue, we can expect AI to continue playing a pivotal role in trimming the energy footprint of industrial robots and automation systems.
10. Data Analytics for Process Improvement
AI-driven data analytics is being harnessed in industrial robotics to continuously improve manufacturing processes. Modern production generates a wealth of data – from sensor readings on machines, production throughput numbers, quality inspection results, to supply chain logs. By applying advanced analytics and machine learning to this big data, companies can uncover patterns and insights that were previously hidden. For robots on the line, this means AI can tune their operation for optimal performance: for example, finding the ideal speed that maximizes output without causing more errors, or discovering that a slight adjustment in tool angle improves quality. Analytics can also reveal inefficiencies – maybe a certain robot is frequently idling waiting for parts, indicating a need to rebalance the line. With AI, multiple variables can be analyzed simultaneously to perform complex optimizations that humans struggle with. Additionally, AI models can run simulations (digital twins) of the process to test improvements virtually before applying them. Over time, this data-driven approach leads to processes that are ever more efficient, with higher yield, lower cycle times, and improved product quality. It transforms manufacturing into a continuously learning operation, where each day’s production data informs the next day’s slight adjustments. AI-based analytics thus serves as the brain of the smart factory, driving iterative enhancements and innovation in processes that keep companies competitive.
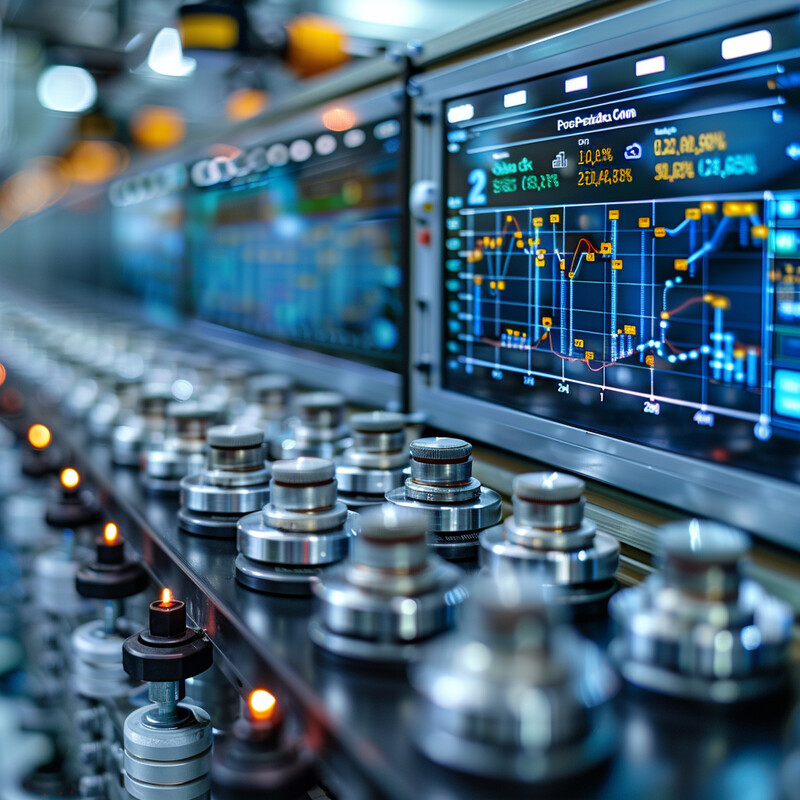
The impact of AI analytics on process improvement is evidenced by significant gains reported at advanced manufacturing sites. For example, Beko (a global appliance manufacturer) implemented AI-driven controls at one of its “lighthouse” factories and achieved remarkable results: a machine learning system for sheet metal forming reduced scrap material waste, yielding a 12.5% reduction in material costs, and an AI model for assembly eliminated certain errors, cutting defect rates by 66%. In another process at the same site, a computer-vision and AI feedback loop in plastic molding optimized the cycle time, improving throughput by 18%. These improvements were realized by analyzing thousands of data points collected during production and letting the AI find the best settings and adjustments continuously. Many such examples exist across industries – for instance, a pharmaceutical plant in the World Economic Forum’s Lighthouse Network used AI to optimize cleaning and changeover procedures, reducing the time needed by nearly 50%. These case studies underline how data analytics with AI can pinpoint inefficiencies and recommend solutions far beyond what traditional monitoring could do. By iteratively fine-tuning processes (reducing waste, speeding up steps, improving yields), AI analytics delivers substantial productivity and cost benefits. The quantitative results – double-digit percentage improvements in key metrics – illustrate the power of data-driven process optimization in modern factories.