1. Material Property Prediction
Artificial intelligence is accelerating how researchers predict composite material properties before fabrication. Machine learning models can analyze a composite’s composition or microstructure and accurately predict properties (mechanical strength, elasticity, thermal behavior, etc.) without extensive physical testing. By training on existing materials data, AI systems identify complex relationships between ingredients (fibers, resins, fillers) and performance outcomes. This enables “virtual testing” of new composites in software, allowing engineers to screen and refine material candidates much faster than traditional trial-and-error experimentation. The result is a more efficient materials design process where promising composites are identified early, reducing development time and cost while targeting specific property goals from the start. In industries like aerospace or automotive—where development cycles are long—AI-based property prediction helps engineers home in on designs that meet stringent requirements without waiting for multiple rounds of prototyping.
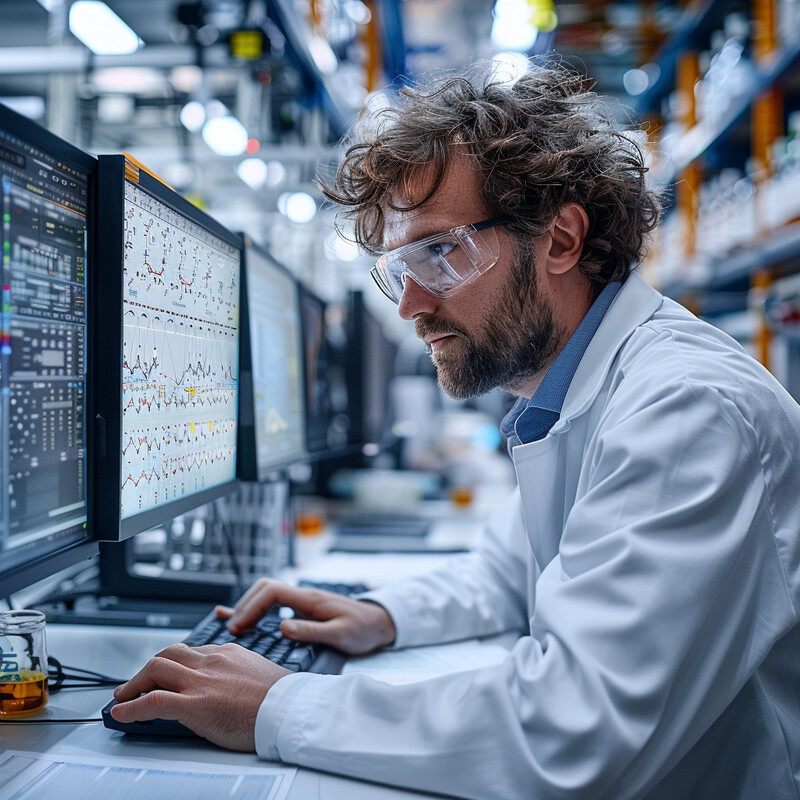
In September 2024, researchers at Binghamton University (NY) received an NSF grant to develop a deep-learning model for designing composite microarchitectures tailored to desired mechanical behaviors. Their approach will generate thousands of simulated composite models to train AI on how microstructural features (like the distribution of a stiff “stone” material in a soft “gel” matrix) influence strength in different directions. The goal is an AI system that suggests new composite designs optimized for multiple loading conditions simultaneously – for example, balancing strength in the X, Y, and Z axes for aerospace components. By “reverse-engineering” material architecture in this way, the AI can propose composite configurations that achieve targeted performance profiles that would be hard to discover manually. This kind of AI-driven materials design is expected to significantly shorten development time, as the model can quickly pinpoint promising formulations for lab testing instead of relying on exhaustive physical experiments.
2. Optimization of Material Formulations
AI techniques are used to optimize composite formulations by finding the best mix of constituents and processing parameters to achieve desired performance. Instead of experimenting with countless recipes of fibers, resins, and additives, researchers employ machine learning and evolutionary algorithms to explore the design space in simulation. These models evaluate how varying ingredient ratios or cure conditions affect properties like tensile strength, toughness, or weight. By analyzing large datasets of past experiments, AI can predict which combinations will maximize certain properties or balance multiple objectives (e.g. strength vs. weight vs. cost). In practice, this means AI can recommend an optimal fiber-to-matrix ratio or curing cycle that yields the best overall composite performance. This data-driven formulation tuning greatly accelerates material development, focusing efforts on the most promising recipes and reducing wasteful trial-and-error. Industries benefit by rapidly configuring composites for specific needs—such as a formulation tailored for high heat resistance—while meeting performance targets efficiently.
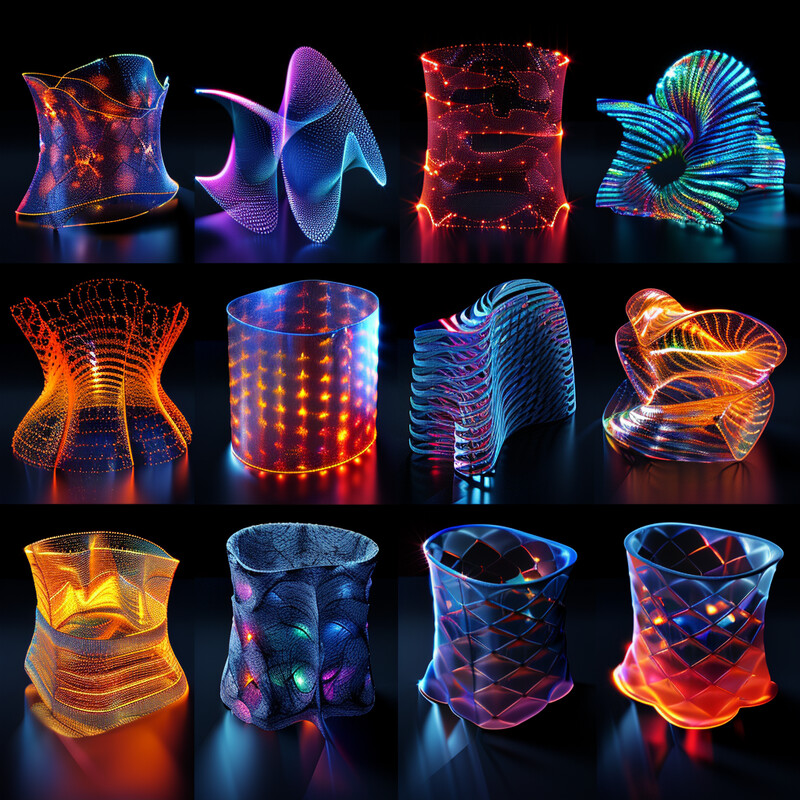
Data-driven formulation optimization is already yielding results in transportation sectors. Machine-learning simulations have identified optimal fiber–matrix ratios for new composites that improve safety and durability without adding weight. For example, in the automotive industry AI models were used to determine the best fiber content in a polymer matrix to create a high-impact-resistant yet lightweight composite for vehicle crash components. This helped enhance impact absorption (boosting crash safety) while keeping the material light for fuel efficiency. Similarly, aerospace engineers have applied ML to design carbon fiber composites with an ideal balance of stiffness and strength for aircraft parts. In one case, the AI suggested adjusting the fiber orientation and volume fraction to prevent a particular failure mode (delamination) under flight stresses. These examples demonstrate how AI-guided formulation can produce bespoke composite materials that meet stringent industry requirements more quickly than conventional development.
3. Quality Control
AI is improving quality control in composite manufacturing by enabling automatic, real-time defect detection. Advanced sensors (like high-resolution cameras, ultrasonic scanners, etc.) feed data to machine learning models that can recognize anomalies such as fiber misalignment, voids, cracks, or uneven curing that human inspectors might miss. For example, computer vision systems on production lines use neural networks to examine each composite part or layup for tiny flaws in fiber placement or resin distribution, ensuring consistent build quality. AI’s pattern-recognition capabilities mean it can detect subtle deviations from the norm and alert engineers immediately, even adjusting process parameters on the fly to correct issues. Compared to manual inspection, AI-driven quality control is faster and more consistent – every inch of material can be monitored continuously, and decisions are based on quantitative data. This leads to higher yield and reliability: fewer defective composite components escape into final assembly, and overall safety is improved since hidden defects (which could cause failure in service) are caught early. In safety-critical fields (aerospace, wind energy), such AI-enhanced QC provides an important extra layer of assurance that composites meet strict standards.
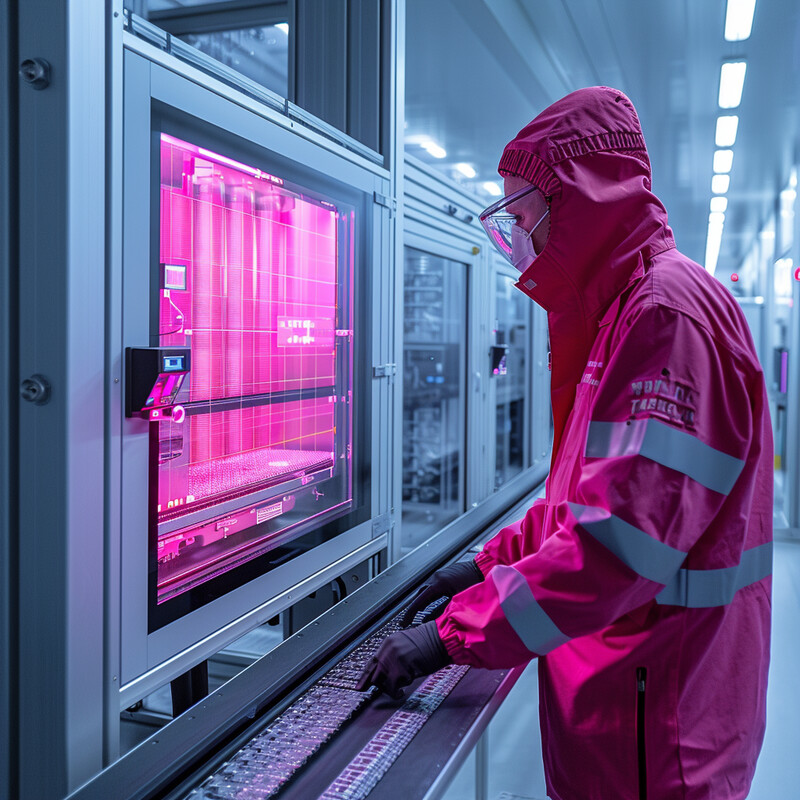
Research in non-destructive testing shows that AI can outperform traditional inspection in finding internal defects. For instance, deep learning models trained on ultrasonic scan data have been able to identify delaminations in fiber-reinforced composites with over 95% accuracy. In one study, a convolutional neural network learned to classify ultrasonic echo patterns and successfully recognized even subtle internal delamination damage that might be imperceptible to human technicians. This high accuracy allows for earlier intervention – if an emerging delamination is detected in a composite pressure vessel or airplane wing panel, maintenance can be performed before a small flaw grows into a serious problem. Similarly, AI image analysis has been used to inspect composite wind turbine blades and detect tiny surface cracks or voids automatically, preventing costly in-field failures. These applications underscore AI’s value in quality assurance: by catching defects reliably in real time, AI systems help maintain product integrity and reduce the risk of catastrophic failures caused by undetected material flaws.
4. Predictive Maintenance in Manufacturing
In composite manufacturing, AI-based predictive maintenance is used to anticipate equipment failures before they happen, minimizing unplanned downtime. Production of composites often involves complex machinery (autoclaves, fiber placement robots, cutting and milling machines, etc.) that must run reliably. AI systems analyze streams of sensor data from these machines – temperatures, pressures, vibrations, motor currents – to detect early signs of wear or malfunction that humans might overlook. By continuously monitoring machine health indicators, machine learning models can forecast when a critical component (like a heater element or servo motor) is likely to fail or drift out of spec. Maintenance can then be scheduled proactively at a convenient time, rather than reacting after a breakdown halts production. This approach extends equipment life and keeps composite fabrication lines running smoothly, since issues are fixed during planned maintenance windows instead of causing sudden line stoppages. Overall, AI-driven predictive maintenance improves safety (reducing the chance of catastrophic machine failures), ensures consistent product quality (machines stay in optimal condition), and boosts productivity by increasing the uptime of expensive manufacturing assets.
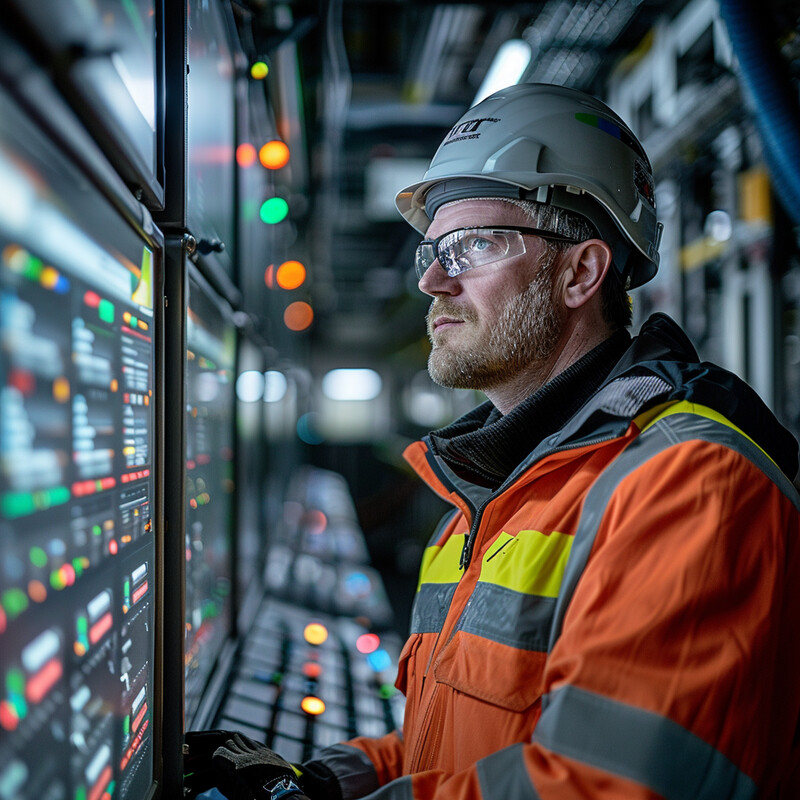
Manufacturers report significant gains from using AI for predictive maintenance. According to one industry analysis, combining AI algorithms with IoT sensors on factory equipment has reduced unplanned downtime by up to 50% and cut breakdowns by about 70%, while also lowering maintenance costs by roughly 25% through more efficient scheduling. For example, a composite materials plant that implemented an AI maintenance platform saw fewer unexpected outages in its curing ovens and molding presses; the system’s early warnings allowed the maintenance team to replace wearing parts during routine stops instead of after a failure. Another case involved robotic assembly equipment for aerospace composites – the AI identified anomalous vibration patterns in a robot’s gearbox that would have led to failure, enabling a preemptive fix. These results align with broader trends in manufacturing: predictive maintenance powered by AI and data analytics can save millions of dollars by avoiding production interruptions and extending equipment lifespan. Companies leveraging these tools maintain higher throughput and meet delivery targets more consistently, gaining a competitive edge in efficiency.
5. Supply Chain Optimization
AI is being applied to optimize supply chains in composite manufacturing, ensuring the right materials are in the right place at the right time while minimizing costs. Producing composite parts requires coordinated delivery of raw materials (fibers, resins, fabrics, catalysts) and often involves global supply networks. Machine learning algorithms improve demand forecasting by analyzing historical usage, production schedules, and even external factors (like market trends or logistics data) to more accurately predict future material needs. This helps prevent both shortages (which could idle a production line waiting for carbon fiber) and excess inventory (which ties up capital and storage space). AI-driven tools also dynamically optimize ordering and inventory levels – for instance, automatically adjusting procurement when a predictive model sees a spike in upcoming composite orders or flagging a supplier delay risk so that backup stock can be secured. Additionally, AI can route shipments more efficiently and select optimal suppliers by considering factors like cost, quality, and risk in real time. For composite manufacturers, these capabilities translate to a leaner, more resilient supply chain that can respond rapidly to changes, avoid material bottlenecks, and reduce waste from expired or unnecessary stock. The overall effect is lower operational costs and a steadier production flow.
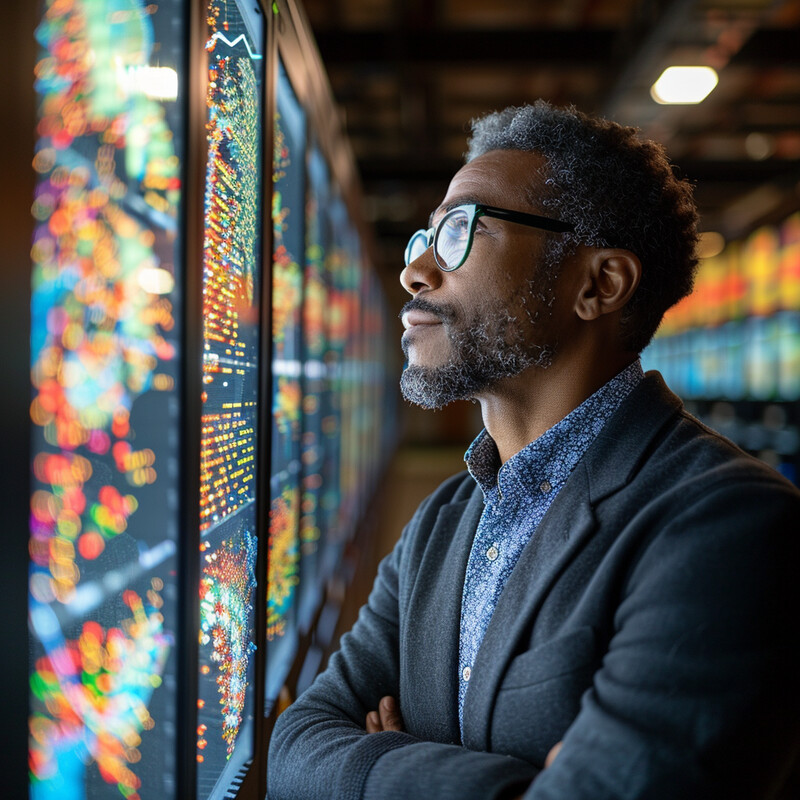
Early adopters of AI in supply chain management have documented major performance improvements. In a study of companies implementing AI-based planning, McKinsey found they achieved on average a 15% reduction in logistics costs and a 35% reduction in inventory levels, while also improving service levels (on-time delivery, order fulfillment) by 65% relative to less advanced peers. In practical terms, a composites manufacturer using an AI supply chain platform might see raw material inventory (e.g., rolls of prepreg carbon fiber and drums of epoxy) drop from, say, 60 days’ worth to 40 days’ worth on hand, freeing up cash and warehouse space without risking stockouts. At the same time, smarter demand forecasting ensures customer orders for composites are met more reliably (service level up significantly). For example, an aerospace supplier reported that after deploying an AI-driven planning system, they could anticipate production needs for different carbon fiber grades much more accurately, resulting in fewer rush orders and almost no line stoppages due to material run-outs. These gains highlight how AI can holistically streamline the supply chain, yielding both efficiency and reliability benefits in composite material production.
6. Failure Analysis
AI is aiding engineers in failure analysis of composite materials by spotting patterns and root causes in failure data that might not be obvious through conventional analysis. When composite components fail (whether in testing or in service), they produce a wealth of data: load conditions, environmental factors, and fractographic images of failure surfaces. Machine learning models can be trained on libraries of such failure cases to learn correlations between design factors and failure modes. For example, AI might recognize that a certain fiber/matrix combination consistently leads to delamination under high humidity, or that a particular weave pattern fails by fiber breakage at lower stress than expected. By classifying failure modes (like fiber pull-out vs. matrix cracking) from sensor signals or microscope images, AI helps identify the weak links in a composite’s design or manufacturing process. Engineers can then use these insights to improve material formulations or structural designs – essentially feeding lessons of past failures back into the development cycle. In critical applications (e.g. aircraft wings, pressure vessels), this AI-assisted failure analysis accelerates the learning process after a failure, enabling faster redesigns or mitigation strategies to prevent future occurrences. It also enhances safety by uncovering subtle indicators of impending failure that traditional analysis methods might miss.
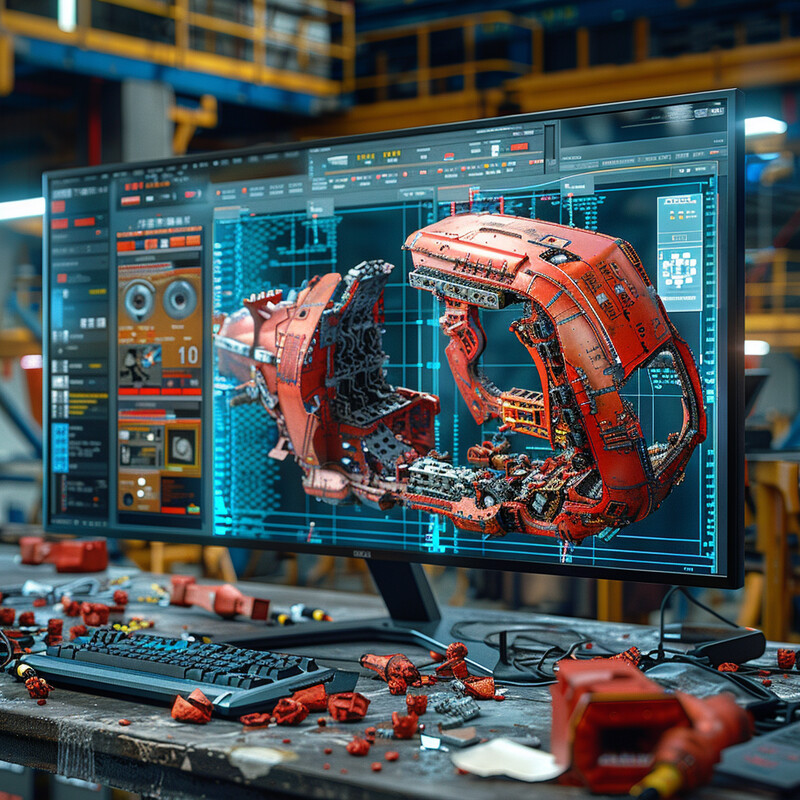
One practical example is using machine learning to predict and prevent particular failure modes. Researchers have applied supervised learning to composite failure databases to anticipate how and where a composite might fail. In a published case, a neural network was trained on experimental failure data for various carbon fiber/epoxy laminates. The model learned to output the likely failure mode (e.g. edge delamination vs. fiber rupture) given the laminate’s layup configuration and loading scenario. It could, for instance, flag that a proposed layup with a certain fiber orientation and resin might be “more susceptible to delamination under high stress,” allowing designers to tweak the design before it’s built. Similarly, decision-tree algorithms have been used to analyze thousands of past test results and pinpoint which material parameters (fiber length, void fraction, etc.) most strongly contribute to early failure. Airbus has noted that such AI tools help inform design adjustments – if the AI indicates a particular resin causes microcracks at low temperatures, an alternative resin or an added toughening agent can be chosen in the next iteration. Thus, AI-driven failure analysis provides a data-driven feedback loop: each failure makes the composite designs smarter and more robust going forward.
7. Customization for Specific Applications
AI enables manufacturers to customize composite materials for specialized applications more efficiently by evaluating requirements and tailoring designs to meet them. Different industries (aerospace, automotive, sporting goods, biomedical) demand composites with unique performance profiles and must meet specific standards. AI tools can intake the target criteria for an application – for example, an aerospace part needing to endure high temperatures and cyclic loads, or a sporting equipment needing specific flexibility – and then assist in designing a composite optimized for those conditions. This might involve adjusting the fiber type, orientation layup, resin chemistry, or adding fillers to achieve the precise strength, weight, or durability required. Traditionally, such customization relies heavily on expert intuition and lengthy testing for each new use-case. Now, machine learning models (trained on prior composite designs and outcomes) can suggest how to tweak a baseline material to better suit a new scenario, essentially acting as a smart materials engineer. The result is a faster development of bespoke composites that fulfill niche demands – e.g. a carbon fiber composite variant formulated specifically for electric vehicle battery enclosures (optimized for fire resistance and electromagnetic shielding) or a new high-toughness composite for helmets in sports. AI ensures that each sector gets a material finely tuned to its needs without starting the development process from scratch each time.
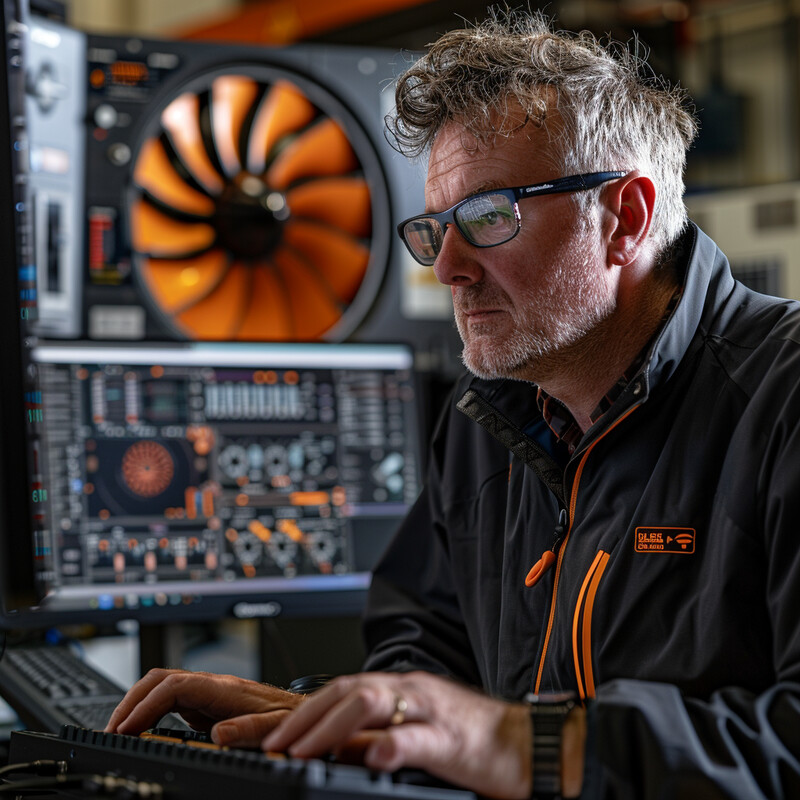
Leading composite suppliers are using AI to deliver client-specific material solutions. For example, Hexcel Corporation, a major U.S. composites manufacturer, has adopted AI-based systems to customize composite formulations for individual customers and applications. According to industry reporting, Hexcel’s AI analyzes the particular performance requirements and environmental conditions of a client’s project – say a drone wing that must be extremely lightweight yet resist high vibrations – and then recommends adjustments to the material’s composition and the fabrication process to meet those needs. This could mean altering the fiber blend, changing the resin curing profile, or even suggesting a different weave pattern to tailor properties like stiffness or impact resistance. Hexcel credits this AI-driven approach with opening new possibilities in product innovation, as they can rapidly iterate composite designs for diverse sectors from aerospace to sports gear. One outcome cited was a bespoke composite for a performance bicycle frame, where the AI helped achieve an ideal balance between frame rigidity and rider comfort by fine-tuning the layup – a level of personalization that would have been far more time-consuming with manual engineering alone. The use of AI for customization is thus allowing composite makers to serve niche markets (with unique specs) more effectively, giving clients materials precisely aligned with their performance objectives.
8. Recycling and Sustainability
AI is advancing the recycling and sustainable use of composite materials by optimizing how composites are reclaimed and reused at end-of-life. Traditional recycling of composites (especially carbon fiber-reinforced plastics) is difficult – fibers and resins are tightly bound, and processes like burning or chemical dissolution are energy-intensive and can degrade material performance. AI is helping on multiple fronts: in recycling facilities, AI-powered robots and vision systems can identify and sort composite scrap more effectively, separating different fiber types or removing contaminants to improve recycling feedstock quality. AI models also optimize process parameters for new recycling methods (like solvating resins or milling composites into reusable fibers) to maximize material recovery and minimize energy use. For instance, by analyzing sensor data, AI might determine the ideal temperature and duration to soften a thermoset resin just enough to free fibers without damaging them. This leads to higher retention of fiber strength in recycled material. On the sustainability side, AI tools help design composites for circularity, suggesting material choices or design modifications that would make future recycling easier (e.g., selecting a resin that an AI model predicts can be more readily depolymerized and recovered). In summary, AI is enabling a more circular lifecycle for composites – from smarter sorting and processing of waste to the conception of next-generation composites that are greener and more recyclable.
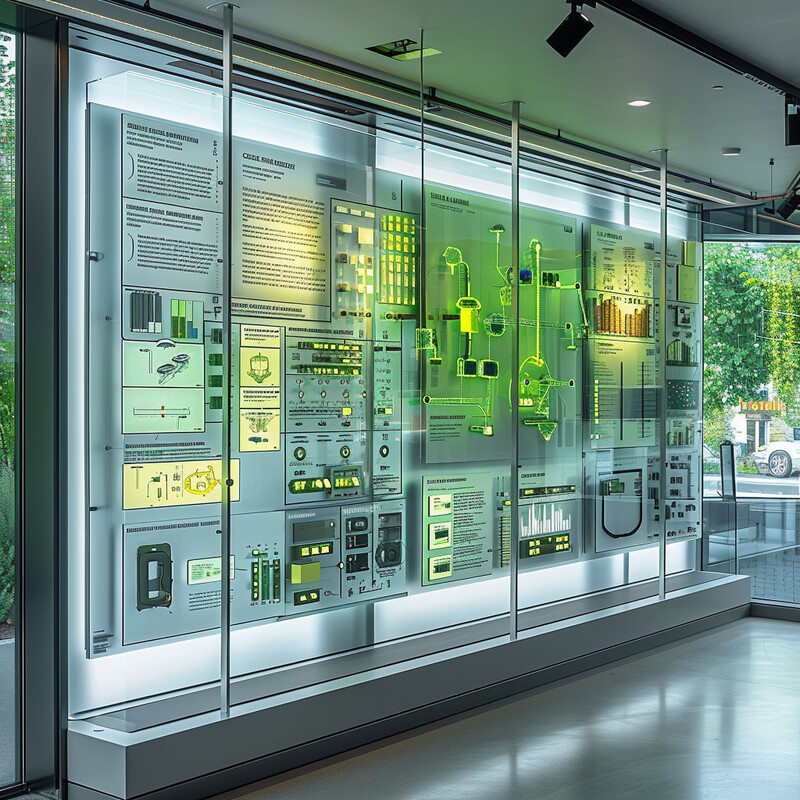
A notable example comes from Fairmat, a startup focused on recycling carbon-fiber composites. Fairmat employs AI-driven robotics in its recycling process to reclaim carbon fiber from composite scrap with unprecedented efficiency. According to reports, Fairmat’s AI-powered system can process up to 50,000 composite chips per hour – the robots, guided by machine vision and algorithms, “peel” and cut waste composite pieces into small, uniform chips for reuse. The AI ensures that each chip contains both fiber and resin in balanced proportion, eliminating the need for energy-intensive chemical separation. As a result, Fairmat is able to recover up to 90% of the material from end-of-life composites while producing 10× less CO2 emissions than traditional methods. For example, retired wind turbine blades and aerospace carbon fiber scrap that would have gone to landfill are now converted into new composite sheets (branded “Fairply”) using this AI-optimized process. This recycled material reportedly rivals virgin aluminum in performance at comparable cost. Fairmat’s success, backed by life-cycle data, demonstrates how AI and robotics can dramatically improve composite recycling, turning a once intractable waste problem into a source of high-performance, sustainable material.
9. Integration with Robotic Systems
AI is tightly integrating with robotic systems to automate composite manufacturing processes, significantly improving precision and throughput. Many composite fabrication tasks – like laying up fiber plies, winding fibers on a mold, or trimming finished parts – have traditionally been labor-intensive. Now, factories use robots equipped with AI-driven controllers and vision systems to perform these actions more reliably. For instance, in automated fiber placement (AFP) machines, AI algorithms monitor the layup in real time and adjust the robot’s path or pressure to ensure each carbon fiber tape is placed without gaps or overlaps. If sensors detect an anomaly (say a misalignment starting), the AI can immediately correct the robot’s course or tension, something impossible with pre-programmed robots alone. This dynamic adjustment leads to highly repeatable and accurate layups, with minimal defects. Similarly, in resin infusion or injection processes, AI can control robotic actuators to dispense resin at an optimal rate by analyzing feedback (preventing dry spots or excessive resin pooling). By combining robotics with machine learning, composite manufacturing is moving toward a level of automation where systems not only execute tasks but also perceive and decide – essentially robotic cells that “learn” the best way to build a specific composite part. This increases production speed (robots don’t tire and can run continuously) and consistency (each part manufactured to the same tight tolerances), and it frees human technicians to focus on higher-level supervision and design.
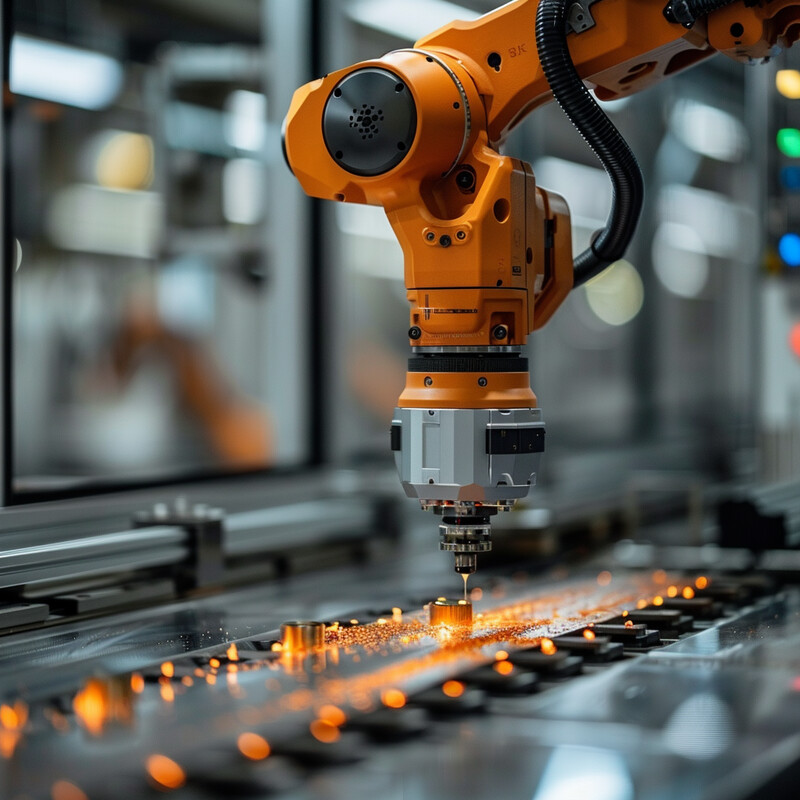
A concrete example is the use of AI in a robotic AFP system for aerospace composites. Researchers implemented a machine learning model to act as the “brain” of an AFP robotic arm, enabling on-the-fly adjustments during the fiber layup process. In tests, as the robot laid carbon fiber tape onto a complex curved tool, the AI monitored temperature and placement accuracy; when slight deviations were detected (like a tape steering off path by a millimeter), the controller autonomously corrected the course and modified the compaction force to avoid wrinkles. According to the study, this intelligent control reduced material defects by over 30% and improved fiber placement accuracy such that quality inspections found virtually no gaps between tapes, compared to small gaps in parts made without the AI assist. Another example comes from a production setting: an AI-vision-guided robotic arm used for trimming composite panels. The system identifies the exact trim line on each panel via image recognition and accounts for part-to-part variability, then guides the robot cutter accordingly. A Boeing facility reported that adopting this AI-guided robotic trimming eliminated manual rework, as each panel was cut precisely to spec the first time. These cases illustrate how marrying AI with robotics yields smarter automation – the robots become adaptive, leading to higher efficiency and consistently excellent composite part quality.
10. Enhanced Simulation and Modeling
AI techniques are enhancing the simulation and modeling of composite materials, making it faster and more informative to predict how composites will perform under various conditions. Traditional composite simulations (e.g. finite element analysis of a complex composite structure) can be very computationally intensive and time-consuming. AI provides a way to create surrogate models – machine learning models trained on simulation data or experiments – that can emulate detailed physics-based simulations almost instantly. This allows engineers to explore many more design permutations or load cases in a short time. For example, instead of running a 10-hour finite element simulation for each new design, an AI model (once trained) might predict stress distribution or deformation in seconds with reasonable accuracy. Additionally, AI (especially deep learning and generative models) can capture multi-scale behavior of composites: learning the link between micro-scale features (fiber arrangement, voids) and macro-scale properties, thus bridging gaps in traditional modeling. Enhanced modeling means engineers can simulate long-term performance like fatigue life or damage evolution by leveraging AI predictions where classical methods bog down. It also enables real-time simulation feedback – for instance, an AI could live-monitor a structural test and predict failure well before it occurs by comparing sensor data to learned patterns. Overall, integrating AI into composite modeling accelerates the design loop: designers quickly get insight into “what if” scenarios and can optimize structures with confidence that the AI’s predictions align with physical reality (especially when validated against key test data). This results in better-performing composites developed on a shorter timetable.
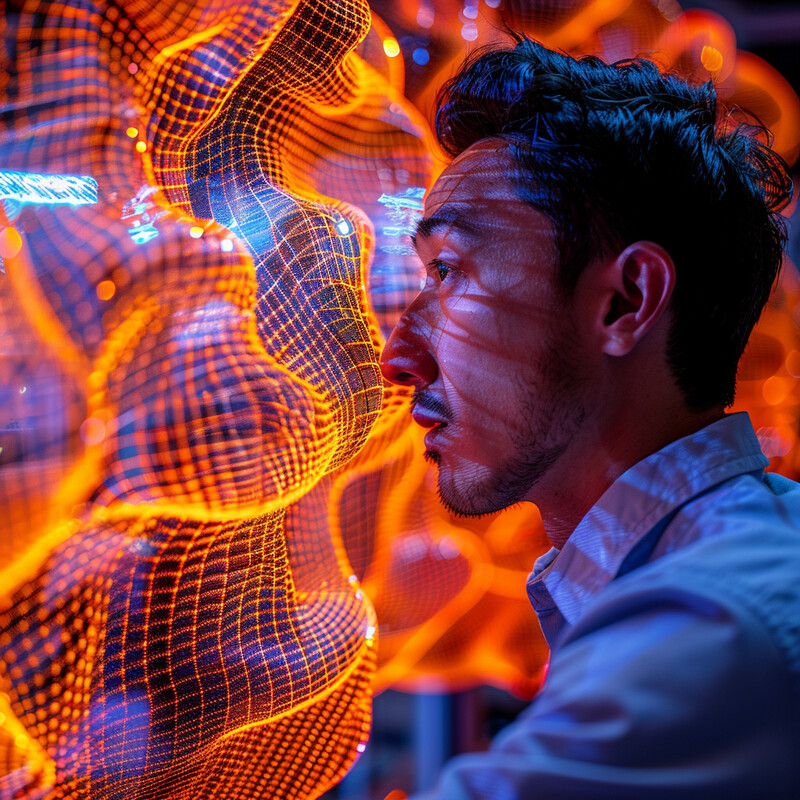
A dramatic illustration is provided by Polaron, an AI spinout from Imperial College London, which has developed a generative modeling platform for composite materials. Polaron’s AI learns from microscopic images of a material’s microstructure and manufacturing parameters, then predicts the material’s properties and performance. In trials, this approach brought the design cycle for new materials down from “hundreds of weeks to hundreds of hours” – essentially compressing a multi-year development process into a few weeks. The AI was able to rapidly evaluate thousands of possible microstructural designs (fiber arrangements, porosity levels, etc.) for a given application, all in simulation, and identify the top candidates for physical testing. This was pivotal in areas like wind energy: Polaron’s system helped design a new composite for turbine blades by predicting which microstructures would last longest under cyclic wind loads, guiding manufacturers to a superior, durable material much faster than conventional R&D alone. The achievement was recognized when Polaron won the UK government’s 2025 Manchester Prize for AI innovation. Officials noted that this technology “speeds up materials development from years to days” and will help create stronger, lighter, and more efficient materials for clean energy and transport needs. Such outcomes underscore how AI-driven simulation is revolutionizing composite engineering – enabling rapid prototyping in silico and yielding optimized materials that meet pressing performance and sustainability targets.